CNC Recycling: Sustainable Waste Management in Manufacturing
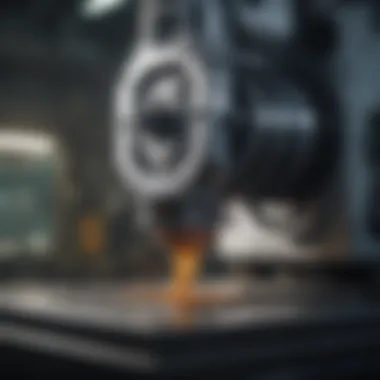
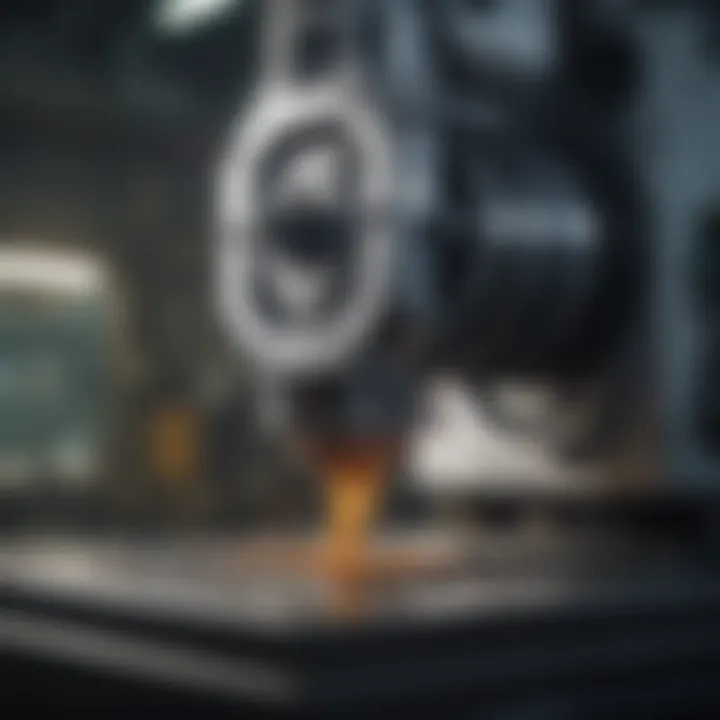
Intro
As the demands of modern manufacturing evolve, sustainability has become a buzzword that rings louder with each passing year. At the crossroads of innovation and environmental responsibility lies CNC recyclingâa process that not only mitigates waste but also enhances operational efficiency and profitability. The manufacturing industry, often stigmatized for its contribution to environmental degradation, is now stepping up, embracing CNC recycling as a vital solution in its journey toward greener practices.
In the world of Computer Numerical Control (CNC) machining, materials like metals and plastics can lead to substantial waste. But instead of simply discarding scrap and remnants, innovative techniques are being employed to recycle these materials, breathing new life into what was once considered useless. The significance of this practice can't be overstated; it encompasses not just the reduction of landfill waste, but also the conservation of resources and a positive impact on the bottom line, marking it as both an environmentally and economically sound approach.
What's notable about CNC recycling is how it dovetails with broader trends in sustainability. With governments and organizations pushing for stringent regulations on waste and emissions, companies are increasingly recognizing the need to adapt. Yet, the journey isn't without its hurdlesâranging from the technical limitations of current recycling technologies to the cultural shifts needed within organizations.
As this article unfolds, we'll explore the key concepts behind CNC recycling, examining the scientific principles that inform the process, the latest research trends in this field, and the substantial benefits of integrating these practices into manufacturing. Case studies will shed light on real-world implementations, challenges faced in pursuit of sustainability, and the potential future outlook for an industry that increasingly prioritizes recycling in its strategic frameworks.
By synthesizing the information throughout, we hope to provide a well-rounded perspective that encourages readers to rethink waste management in manufacturing, seeing it not just as a challenge but as an opportunity for growth and development in a more sustainable direction.
Prelims to CNC Recycling
In todayâs manufacturing landscape, CNC recycling emerges as a beacon of sustainability, illuminating a path towards more responsible waste management practices. As industries continue to grapple with increasing waste generation and environmental regulations, understanding the nuances of CNC recycling becomes not just beneficial but essential. This section aims to unpack the core elements, advantages, and various considerations surrounding the concept of CNC recycling, providing a thorough insight into its role in creating a more sustainable manufacturing ecosystem.
Definition and Overview of CNC Recycling
CNC recycling refers to the systematic process where scrap and waste generated during the Computer Numerical Control (CNC) machining process are reclaimed and repurposed. This involves recovering materials such as metals, plastics, and composites that typically end up in landfills or incinerators. Rather than being mere byproducts, these materials can be cycled back into the supply chain, whether through reprocessing, repurposing, or selling to secondary markets.
The heart of CNC recycling lies in its potential to reduce the environmental impact of manufacturing operations. When waste is effectively managed, it leads to a substantial decrease in the demand for virgin materialsâa crucial step towards preserving natural resources and minimizing ecological footprints.
However, it isn't just about the environment. Employing CNC recycling techniques also brings economic advantages to manufacturers. For instance, reusing materials can significantly lower production costs, contributing to improved profit margins. Additionally, companies that adopt sustainable practices often find themselves more appealing to conscious consumers and potential partners.
Yet, as with any practice, CNC recycling does not come without its own set of challenges. Factors such as the initial investment in recycling technology, the need for specialized training, and the intricacies of compliance with environmental regulations must all be navigated carefully. Manufacturers often need to evaluate if the benefits outweigh these hurdles, making a firm commitment to sustainability a pivotal decision.
Importance of Sustainable Manufacturing
The concept of sustainable manufacturing is now more pertinent than ever, serving as a cornerstone for industries aiming to mitigate their environmental footprint while enhancing productivity. In an age where resources are finite and consumer awareness is soaring, the focus on sustainable methods of production is not just a trendâit's essential for both organizational resilience and ecological preservation. For manufacturers, adopting sustainable practices means recognizing the broader impact their operations have on both society and the planet.
Environmental Impact of Traditional Practices
Traditional manufacturing processes have long been associated with substantial environmental degradation. The sheer volume of waste produced, from scrap materials to harmful emissions, often goes unchecked, leading to devastating consequences. For instance, the production of metals and plastics usually involves energy-intensive processes that emit large quantities of greenhouse gases. These emissions contribute to climate change, resulting in harmful consequences such as global warming and extreme weather patterns.
The disposal of manufacturing waste is another significant concern. Most materials end up in landfills, where they can take years to decompose, leaching toxic substances into the soil and groundwater. Additionally, the extraction of raw materials leads to habitat destruction and biodiversity loss, undermining the natural systems on which life depends. By focusing on sustainability, the manufacturing sector can significantly lower these adverse impacts, promoting both environmental health and regulatory compliance.
Economic Advantages of Recycling
When we delve into the economic advantages of recycling within the manufacturing sector, the benefits become increasingly clear. Firstly, recycling can drastically reduce material costs. Raw materials can be expensive, particularly in volatile markets where prices fluctuate wildly. In contrast, utilizing recycled materials generally incurs lower costs and less market unpredictability. This dynamic can boost profit margins and create a more predictable budgeting framework for companies.
Moreover, businesses that embrace CNC recycling can capture new market opportunities. As consumer demand for sustainable products rises, companies that prioritize recyclable materials position themselves favorably in the market. They can attract a customer base that is environmentally conscious, thereby sustaining sales growth in a competitive landscape.
Another economic advantage is found in resource efficiency. Manufacturing processes that integrate CNC recycling often operate more smoothly with less waste. This effectiveness leads to less downtime and better utilization of machinery, which ultimately enhances productivity. Additionally, lower disposal costs can also mean significant savings, especially for companies dealing with large volumes of waste.
To sum it up, the importance of sustainable manufacturing is multi-faceted. From reducing environmental impact to realizing economic benefits, the shift towards sustainable practices in manufacturing is a positive step for both the industry and the planet. By looking closely at recycling initiatives, companies can pave the way toward a more sustainable and economically viable future.
Processes Involved in CNC Recycling
CNC recycling forms a crucial component in addressing the considerable waste generated in the manufacturing process. Machine operations often produce leftover materials and scraps that, if not managed properly, contribute significantly to environmental degradation. Thus, understanding the processes involved in CNC recycling is essential for the development of more sustainable manufacturing practices.
"Recycling is more than just a strategy; it's an essential path towards sustainable production that aligns economic viability with ecological responsibility."
"Recycling is more than just a strategy; it's an essential path towards sustainable production that aligns economic viability with ecological responsibility."
This section will explore two significant elements of CNC recycling: Machining Waste Collection and Segregation and Material Reprocessing Techniques. Each element contributes to reducing waste while optimizing both environmental and economic outcomes in the manufacturing sector.
Machining Waste Collection and Segregation
The first step in effective CNC recycling involves the collection and segregation of machining waste. As parts are manufactured, excess materials such as metal shavings, plastic offcuts, and other debris accumulate. These by-products can be either recyclable or non-recyclable, depending on their composition.
- Collection: Efficient collection systems help ensure that all types of waste are gathered without contamination. Utilizing dedicated bins for different materials is one way to improve overall efficiency.
- Segregation: Sorting waste at the source is essential. For instance, metals should be separated from plastics and composites. If materials are mixed, they often become difficult or impossible to recycle. Using technology, like sensors to help differentiate types, can streamline this process significantly.
- Importance: Beyond the environmental benefits, proper waste collection and segregation can lead to significant cost savings and improve resource efficiency. Organizations that prioritize these initial steps tend to experience smoother processes in later recycling phases.
Material Reprocessing Techniques
After waste has been collected and sorted, the next phase is reprocessing those materials back into usable forms. Various techniques are applied here, and it's crucial to choose the right method based on the material type and desired end product.
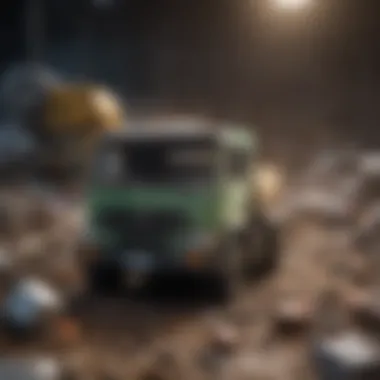
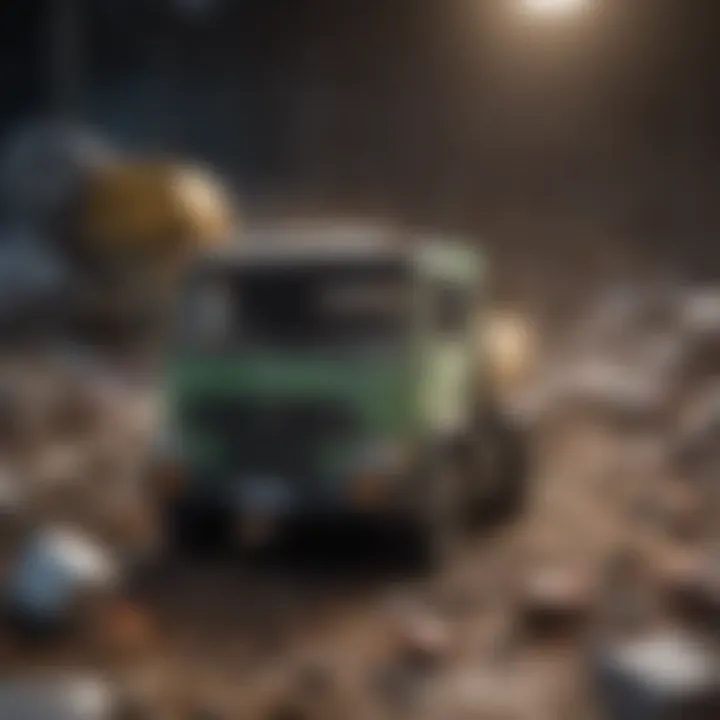
- Shredding: This method is often utilized for plastics and composites. Reducing the size of waste materials makes them easier to remold or repurpose into new products.
- Melting and Extrusion: For metals, melting down the scraps is a common approach. The material is then cast into molds or extruded to form new parts. This process retains the material properties, allowing manufacturers to reuse the same high-quality metal.
- Depolymerization: In cases of polymer waste, a chemical process known as depolymerization can revert materials back to their monomers. This allows for a fresher start for recycling plastic products into new ones.
- Important Considerations: Selecting the right techniques requires understanding the previous history of the materials. Contaminants can affect the end product's quality, so any pre-processing must be thoroughly addressed.
Overall, both the careful collection of waste and the application of innovative material reprocessing techniques stand at the heart of CNC recycling. They are integral in crafting an efficient loop of resource utilization that benefits the environment while simultaneously fostering economic growth. By adopting these processes, manufacturers can significantly elevate their sustainability game.
Types of Materials Suitable for CNC Recycling
Understanding the types of materials appropriate for CNC recycling is crucial within the umbrella of sustainable manufacturing. This knowledge not only facilitates effective waste management but also underpins economic viability in the recycling process. The materials utilized in CNC machiningâranging from metals to plasticsâcarry distinct characteristics that influence how well they can be recycled. By focusing on these materials, manufacturers can make informed decisions that add financial and environmental value to their operations.
Metals: Aluminum, Steel, and Others
Metals represent a significant proportion of the scrap generated in CNC machining. Aluminum is highly prized in recycling circles due to its lightweight nature and resistance to corrosion. When recycled, aluminum can be repurposed repeatedly without loss of quality, making it a sustainable material choice.
Steel, on the other hand, is the go-to choice for a variety of manufacturing applications. Its recyclability is remarkable; it can be melted down and reshaped indefinitely. This aspect not only decreases the immediate need for raw materials but also minimizes energy consumption typically required in new steel production.
Moreover, there are specialty metals, like titanium and nickel alloys, which are also suitable for CNC recycling. Their high strength-to-weight ratio makes them critical in sectors such as aerospace and medical devices.
- Benefits of recycling metals:
- Decreased need for raw material extraction.
- Reduction in landfill contributions.
- Conservation of energy resources.
The process often involves collecting scrap metal from various production operations, then sorting and melting it to produce new products. The key is maintaining high purity levels to ensure quality recycling.
Plastics and Composites
Plastics and composites formed a harder puzzle in CNC recycling. With the sheer diversity of plastics, sorting them accurately is an essential step. Common plastics like Acrylonitrile Butadiene Styrene (ABS) and Polycarbonate (PC) can often be recycled through mechanical processing, in which they are ground into small flakes and reprocessed.
Composites, like carbon-fiber reinforced plastics, present unique recycling challenges. While they are lightweight and strong, traditional recycling methods struggle to separate the materials efficiently.
A few considerations include:
- Type of Plastic: Different plastics have varying recycling processes. Knowledge of these is key.
- Strength and Durability: Composites may offer excellent physical properties, but they often require specialized recycling approaches.
- Market Demand: The economic viability of recycling plastics hinges on market demand for recycled versus virgin materials. More industries are leaning toward sustainable materials, which makes recycling more feasible.
"In a world where resources are finite, choosing the right materials for recycling isnât just about sustainability; itâs about survival."
"In a world where resources are finite, choosing the right materials for recycling isnât just about sustainability; itâs about survival."
Technological Innovations in CNC Recycling
In the evolving landscape of CNC recycling, technological innovations serve as the backbone of progress. They are not just helpful options; they are essential in pushing the boundaries of what's possible in sustainable manufacturing. These advancements contribute to improved efficiencies, better material recovery rates, and significant cost savings. As industries face increasing pressure to minimize waste and pivot towards sustainability, embracing technology becomes a necessity.
Advanced Software and CNC Machines
When we talk about advanced software and CNC machines, we are diving headfirst into a realm where precision meets efficiency. The integration of sophisticated software into CNC machinery allows manufacturers to optimize operations in ways that were previously unimaginable. These software solutions facilitate real-time monitoring of machining processes, pinpointing areas where waste could be reduced.
With features like predictive maintenance, manufacturers can foresee machinery failures before they happen. This proactive approach reduces downtime and ensures smoother recycling processes. Furthermore, simulation software enables manufacturers to visualize the entire lifecycle of a product, from material input to recycling output. In practical terms, this leads to smarter design choices and a sharper focus on sustainability right from the get-go.
It's worth noting that these advanced machines aren't exclusive to big players in the market. Small and medium enterprises (SMEs) can also reap the benefits. With certain software-as-a-service (SaaS) models, even smaller companies can access top-notch tools without the burden of heavy upfront investments. This leveling of the playing field opens doors for wider adoption of CNC recycling practices across the board.
Machine Learning and Optimization in Recycling
Then thereâs machine learning, which has been a game-changer in optimizing CNC recycling efforts. By analyzing vast amounts of data, machine learning algorithms can identify repeat patterns in waste generation and suggest innovative strategies for material reuse. For example, an algorithm can analyze historical machining data to determine which materials generate the most waste during production and suggest alternative methods to reduce this waste.
The takeaway here is that machine learning is not just a tool but a strategic partner in crafting more efficient recycling processes. It empowers manufacturers with actionable insights, allowing them to make data-driven decisions that elevate their recycling initiatives to new heights.
Moreover, machine learning helps streamline supply chains. Patterns are detected that help predict demand for recycled materials, allowing businesses to react more swiftly and efficiently. It paints a clearer picture of how materials move from machine shop to recycling facility, significantly reducing the time and resources spent on reprocessing.
"The embrace of both software advancements and machine learning in CNC recycling represents a crucial leap towards a circular economy, where materials are perpetually reused rather than discarded."
"The embrace of both software advancements and machine learning in CNC recycling represents a crucial leap towards a circular economy, where materials are perpetually reused rather than discarded."
Regulatory Frameworks and Compliance
Regulatory frameworks and compliance are vital points of discussion when it comes to CNC recycling. These guidelines set the stage for how companies manage their waste, urging them to adopt sustainable practices and paving the way for a healthier environment. Understanding and adhering to these regulations is not merely a checkbox exercise; itâs crucial for fostering a culture of responsibility and sustainability in manufacturing.
Understanding Environmental Regulations
Environmental regulations play a key role in shaping the landscape of CNC recycling. They serve as a legal framework that compels manufacturers to be more conscientious about their waste management practices. These laws, which vary by region and country, often include requirements for waste reduction, recycling, and proper disposal of materials. For instance, the Resource Conservation and Recovery Act in the United States outlines how waste should be tracked, managed, and reused.
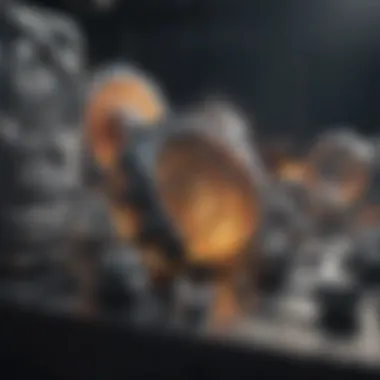
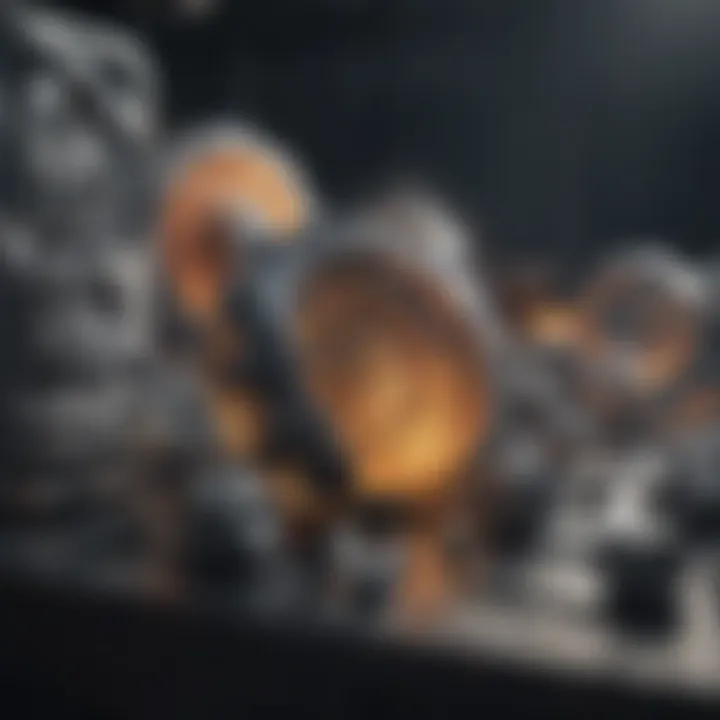
Emphasizing compliance not only mitigates the risk of fines and penalties but also enhances a companyâs reputation. Here are some critical aspects:
- Local and Global Compliance: Companies need to be aware of both local laws and international standards, such as those set by the ISO (International Organization for Standardization).
- Documentation and Reporting: Regulations often require extensive record-keeping related to waste management. This ensures accountability and allows regulatory authorities to oversee compliance.
- Environmental Impact Assessments: These assessments help companies identify potential environmental damage caused by their operations, guiding them towards better waste management practices.
In the eyes of consumers and stakeholders, adherence to regulations signals a commitment to sustainability, potentially leading to increased customer loyalty and better market positioning.
Standards for Recycled Materials
In addition to understanding environmental laws, knowing the standards for recycled materials is equally essential for success in CNC recycling. Standards dictate how materials should be processed and what requirements they must meet to be deemed safe for reuse.
Having established standards helps companies ensure that the materials they are using are of high quality, promoting confidence not only in their own processes but also among consumers and partners. Hereâs a closer look at some key elements:
- Quality Control: Standards often mandate specific testing procedures for recycled materials, ensuring they meet certain safety and performance criteria.
- Industry Certifications: Many industries offer certifications for recycled materials. For example, ASTM International provides guidelines that can help producers of recycled materials claim compliance to potential buyers.
- Traceability and Transparency: Adhering to standards promotes the ability to trace materials back to their sources, which can bolster trust among manufacturers and consumers alike.
Compliance with standards for recycled materials not only ensures legality but also elevates market trustâessential in todayâs environmentally-conscious world.
Compliance with standards for recycled materials not only ensures legality but also elevates market trustâessential in todayâs environmentally-conscious world.
Challenges and Barriers to CNC Recycling
Addressing the challenges and barriers to CNC recycling is crucial for understanding the broader scope of sustainable practices in manufacturing. Various factors can hinder the effective implementation of recycling initiatives, especially within small enterprises. By examining these issues, stakeholders can devise strategies that not only promote recycling but also ensure it becomes a standard practice rather than a mere afterthought.
Economic Limitations for Small Enterprises
When it comes to CNC recycling, the financial aspect can't be overlooked. Small enterprises often face tight budgets and limited resources that make it difficult to invest in recycling programs. The initial cost of implementing such systems can be daunting. This includes expenses for specialized equipment, training staff on new processes, and even ongoing maintenance and operational costs.
As a direct result, many small businesses might consider recycling initiatives low-priority. They might opt for traditional disposal methods that seem less expensive in the short term. However, this approach can lead to increased waste over time, potentially incurring higher costs associated with waste disposal fees and environmental penalties.
The irony lies in the fact that failing to invest in CNC recycling could lead these enterprises to miss out on long-term savings through waste reduction.
The irony lies in the fact that failing to invest in CNC recycling could lead these enterprises to miss out on long-term savings through waste reduction.
Furthermore, many small manufacturers might lack access to resources that larger companies often take for granted. This creates an uneven playing field where small players feel overwhelmed and inadequately supported when trying to adopt sustainable practices in CNC recycling.
Technical Limitations and Requirements
On the technical side, the challenges are just as significant. CNC machinery can be complex and not all machines are compatible with recycling processes. Outdated machines may lack the capability to efficiently segregate materials or properly process them for recycling. This limitation can result in increased downtime and efficiency losses, putting additional strain on small businesses already fighting to remain competitive.
Moreover, skilled labor is essential for effective CNC recycling, yet hiring or training employees with the necessary expertise can prove to be a hefty task. Many companies may not have the training programs in place to upskill their existing workforce to handle new recycling technologies or processes.
Itâs also worth noting that regulations governing recycling can vary widely, leading to confusion or compliance issues, especially for companies that lack robust legal departments. Falling short of these expectations can result in legal ramifications and crippling fines, further discouraging investment in recycling initiatives.
Case Studies in CNC Recycling
Case studies play an invaluable role in understanding the practicalities of CNC recycling within the manufacturing sector. They offer a window into real-world applications, showcasing how companies have embraced or struggled with recycling initiatives. This section aims to not only highlight these implementations but also to reflect on the lessons learned from them, turning successes and failures into learning opportunities for the industry at large.
Successful Implementations in Industry
The journey of CNC recycling has seen various companies spearhead initiatives that not only cut costs but also reduce environmental footprint. For example, a prominent aerospace manufacturer adopted CNC recycling practices for their aluminum waste. By implementing a closed-loop system, they were able to reclaim scraps from their machining process and recycle them back into production. This shift not only saved hundreds of thousands of dollars annually but also led to a significant reduction in raw material usage.
Furthermore, a notable automotive company established a partnership with local recycling facilities, transforming their plastic waste into reusable materials for manufacturing new parts. This initiative drastically reduced the need for virgin materials and bolstered their sustainability credentials in the eyes of both consumers and regulators.
Successful implementations like these offer insightful snapshots into best practices that can inspire others in the field. Together, they underscore the importance of innovation and collaboration in pursuing sustainability goals.
Key Benefits of Successful Implementations:
- Cost Savings: Many companies reported lower raw material costs due to recycling efforts.
- Improved Brand Reputation: Sustainable practices tend to resonate positively with modern consumers.
- Enhancement of Regulatory Compliance: Complying with environmental regulations becomes easier with established recycling protocols.
Lessons Learned from Failed Initiatives
While some companies have thrived through effective recycling initiatives, others faced hurdles that led to less favorable outcomes. One common pitfall observed in various failed initiatives is the underestimation of the complexity involved in recycling operations. A furniture manufacturing firm, for instance, attempted to recycle their wood waste but quickly found that the collection and processing systems were inadequate for their needs. This shortfall not only resulted in increased costs but also contributed to waste being sent to landfills instead of being recycled.
Another case involved a tech company that tried to implement CNC recycling for electronic components without proper training or equipment for employees. This led to operational disruptions and resistance among workers, demonstrating that technology can only be as effective as the human element behind it. Investors and stakeholders lost confidence, leading to a complete reconsideration of the recycling initiative.
Lessons from Failures:
- Importance of Comprehensive Planning: It's crucial to plan all stages of the recycling process, from waste collection to processing.
- Employee Training & Engagement: Workers must be well-informed and engaged for recycling efforts to be successful.
- Continuous Evaluation: Ongoing assessment allows companies to correct course before facing large-scale failures.
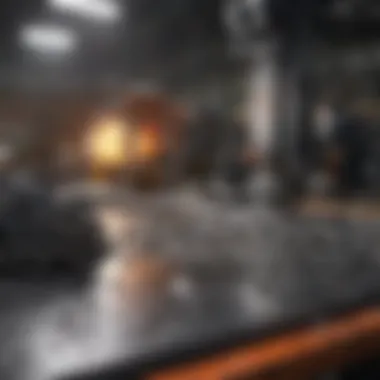
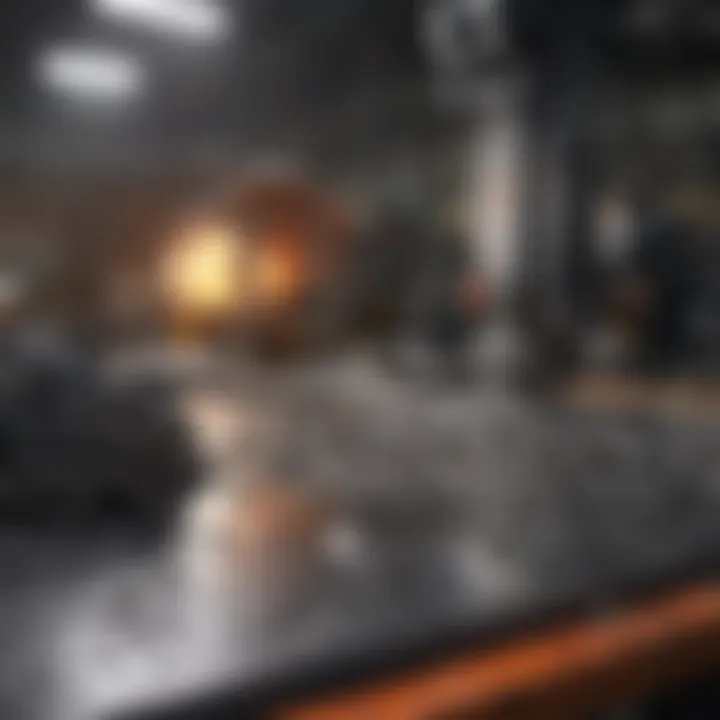
By reflecting on both successes and failures in CNC recycling, manufacturers can glean vital insights that could guide their strategies for implementing sustainable practices effectively. This ongoing learning process fosters an adaptive and resilient approach to CNC recycling, which is essential for the ever-evolving landscape of manufacturing.
Economic Models Supporting CNC Recycling
The rise of CNC recycling isnât merely a trend; itâs a cornerstone in sustainable manufacturing finance. By delving into economic models that bolster CNC recycling, companies can recognize the benefits and considerations that these frameworks present. Understanding financial implications helps create an environment where recycling isnât viewed as an additional expense but rather as an investment with promising returns. This switch in mindset can be essential for companies striving for both environmental responsibility and economic viability.
Cost-Benefit Analysis of Recycling Programs
When assessing the viability of CNC recycling initiatives, conducting a thorough cost-benefit analysis becomes indispensable. This analysis goes beyond mere dollars and cents; it examines the overall economic character of recycling programs, looking at both tangible and intangible benefits.
- Direct Savings: Companies often save money through reduced material costs since recycled materials can be cheaper than purchasing new raw materials. This includes recycling metals like aluminum and steel, which have significant aftermarket values.
- Operational Efficiency: Implementing recycling processes often leads to increased efficiency, as manufacturers can repurpose waste on-site instead of outsourcing disposal. This efficiency translates into less downtime and higher productivity.
- Regulatory Compliance: Adhering to environmental regulations, though it can seem burdensome, often leads to financial incentives or grants that help offset recycling program costs.
- Brand Value: Companies engaging in sustainable practices may enhance their reputations, attracting environmentally conscious consumers which can lead to increased sales.
One key takeaway from this analysis is to shift the focus from immediate costs to long-term financial health. As one expert aptly put it:
"Investing in sustainability isnât just about saving the planet; itâs about savings on the balance sheet, too."
"Investing in sustainability isnât just about saving the planet; itâs about savings on the balance sheet, too."
Market Trends and Opportunities
With the increasing global emphasis on sustainability, the market for CNC recycling is evolving. There are several opportunities that businesses can explore in this space:
- Innovative Materials: As new composites and materials join the market, their recycling potential is often untapped. This scenario offers a chance for companies to pioneer recycling methods for newer materials. It could become a significant niche market as industries look to dispose of wastes smartly and sustainably.
- Collaborative Efforts: Businesses can form alliances to share resources in recycling efforts. Collectively investing in recycling infrastructure can reduce costs significantly and make processes more streamlined.
- Technological Integration: As technology advances, tools that support recyclingâsuch as AI-driven sorting systemsâare becoming more affordable. Companies investing in these technologies stand to gain significantly in terms of efficiency and reduced waste.
- Corporate Responsibility Initiatives: Not only do companies face pressure from consumers to adopt better practices, but also share-holder scrutiny is increasing. Companies can capitalize on this trend by developing robust recycling programs that will appeal to responsible investors.
The Future of CNC Recycling
As we steer into a world that increasingly values sustainability, CNC recycling presents a unique opportunity in the manufacturing industry. This part of the discourse is about eyes on the horizonâwhat's next for this budding field? Understanding The Future of CNC Recycling isn't merely an academic exercise; it holds significant implications for environmental stewardship, economic viability, and technological enhancement. As manufacturers continue to grapple with waste management challenges, CNC recycling offers a pathway to better efficiency while minimizing the ecological footprint.
Predictions for Technological Advancements
With technology evolving at a rapid pace, the future of CNC recycling is likely to be shaped by innovations that facilitate better recycling processes and enhance the quality of recycled materials. Here are a few expected advancements:
- Automation: The integration of robotics in waste segregation processes can streamline efficiency, minimizing human error and labor costs. Automated mechanisms can rapidly identify and sort waste materials, ensuring that recyclables are processed more effectively.
- Enhanced Material Recovery: New technologies, such as advanced sensors and imaging techniques, can improve the detection of recyclable materials during manufacturingâpotentially leading to recovery rates reaching new heights.
- AI and Machine Learning: Predictive analytics can optimize recycling pathways by forecasting trends in material use, allowing for better planning and allocation of resources.
- Smart Recycling Machines: Equipment equipped with machine learning could analyze incoming materials and adapt processing methods dynamically, optimizing output consistency and quality.
These advancements not only promise to elevate the operational standards of recycling but also ensure that they align with the broader goals of sustainable manufacturing.
Emerging Practices in Sustainable Manufacturing
The landscape of sustainable manufacturing is ever-changing, with various emerging practices reshaping how materials are sourced, used, and reprocessed. A glimpse into what lies ahead reveals exciting potential:
- Circular Economy Models: Moving towards a model where products are designed not only for functionality but also for end-of-life recycling creates a circular approach. Manufacturers can work in tandem with designers to ensure that each component is easily disassembled and recycled.
- Collaboration Across Industries: Partnerships between manufacturers, recyclers, and materials scientists can foster innovation. Sharing knowledge and practices can lead to new recycling methodologies that achieve higher levels of material purity and reuse.
- Lifecycle Assessment: More manufacturers are adopting lifecycle assessments to evaluate the environmental impact of products from inception to disposal. This approach encourages responsibility at every stage of a product's life, advancing the push for sustainable practices.
- Consumer Awareness: Educated consumers demand greater sustainability from manufacturers. Companies that respond by offering clear recycling information and sustainability guarantees are likely to position themselves favorably in a competitive market.
As the industry evolves, the focus on sustainability may lead to new standards that redefine efficiency and profitability.
As the industry evolves, the focus on sustainability may lead to new standards that redefine efficiency and profitability.
To marvel at what lies ahead in CNC recycling is to recognize that adaptability and innovation will be the main drivers. As technological advancements emerge and sustainable practices grow, CNC recycling will become not just an operational choice but a crucial element integrating into the broader narrative of responsible manufacturing.
Ending
In closing, it's clear that CNC recycling stands as a pillar for sustainable waste management within the manufacturing landscape. By recycling CNC machining waste, companies not only uphold eco-friendly practices but also reap economic and operational advantages. Weâve seen how traditional waste disposal methods lead to significant environmental damage, pushing businesses to rethink their strategies. The intersection where technology meets sustainability opens plenty of avenues for cost savings. Here are crucial elements to consider:
- Environmental Benefits: CNC recycling effectively diminishes harmful waste that would otherwise pile up in landfills, ensuring cleaner surroundings.
- Cost Reduction: Businesses that implement recycling strategies often cut costs associated with raw material procurement and waste management. Itâs a pocket saver.
- Regulatory Compliance: Following environmental standards isnât just about legal adherenceâit fosters better corporate relationships and enhances brand reputation.
Rather than merely focusing on immediate financial implications, organizations should see the wide-angle view. These practices lay groundwork for a circular economy where waste is transformed into valuable resources.
Summarizing Key Insights
Several insights crystallize as this article comes to a close:
- The importance of proactive waste management in CNC machining cannot be overstated. Itâs not just about responsibility; it's about foresight.
- Innovations in technology are a game-changer. Advanced sorting machines and software algorithms refine the recycling process, improving efficiency.
- Case studies reflected varied success rates, emphasizing that a one-size-fits-all attitude will not work. Tailoring solutions to specific environments and materials is essential.
"Effective recycling in CNC machining isnât just a best practice; it is an imperative for future-focused manufacturers."
"Effective recycling in CNC machining isnât just a best practice; it is an imperative for future-focused manufacturers."
Call to Action for the Industry
So, what does it mean for you, a part of this vast manufacturing ecosystem? The call to action is clear:
- Adopt Sustainable Practices: Evaluate your current processes. Are you taking advantage of CNC recycling? If not, itâs high time.
- Invest in Technology: New machines and software can significantly streamline your recycling efforts. Think beyond the initial costs; consider long-term savings and benefits.
- Educate Your Workforce: Spread the word. Employees play a crucial role, and their understanding of CNC recyclingâs importance can fortify your organizationâs sustainability initiatives.
- Collaborate with Experts: Engage with environmental consultants to ensure compliance and effectiveness in your recycling methods.
The journey of sustainability in manufacturing isn't easy, but itâs a path worth treading. Embrace this call to action, and together, we can foster a more sustainable manufacturing future.