A Comprehensive Guide to Learning Metallurgy
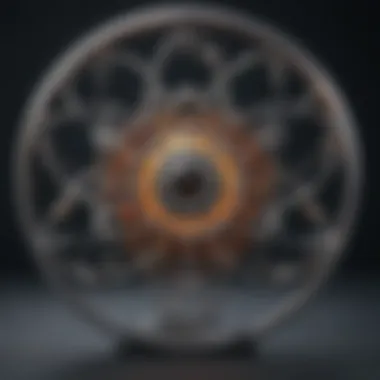

Intro
Metallurgy is a vast field that merges science, engineering, and art. This guide presents an in-depth look into metallurgy, exploring its theories, materials, and current trends. Understanding metallurgy is essential for various industries such as aerospace, automotive, and construction. Each section aims to provide clarity on complex issues and encourage further research and application.
Key Concepts
Definition of the Main Idea
Metallurgy refers to the study of metals and their behaviors. It includes the processes of extraction, refining, and alloying, as well as the physical and chemical properties of metals. Knowledge of metallurgy is crucial for developing new materials and products that meets modern demands.
Overview of Scientific Principles
Several scientific principles underpin metallurgy. Topics such as crystallography, phase diagrams, and thermodynamics are foundational. For example, crystallography examines the arrangement of atoms in metals, influencing their strength and ductility. Phase diagrams illustrate how different alloys behave under varying temperature and pressure conditions, which is pivotal for process optimization.
Current Research Trends
Recent Studies and Findings
Recent research in metallurgy focuses on lightweight materials and those with enhanced properties. Innovative alloys, such as titanium aluminides, are gaining attention due to their exceptional strength-to-weight ratios. Other studies explore nanostructured materials, which exhibit remarkable mechanical properties at reduced weights.
Significant Breakthroughs in the Field
Breakthroughs in metallurgy often arise from interdisciplinary collaborations. For instance, the integration of artificial intelligence in materials design is an exciting trend. By analyzing vast datasets, AI can predict how changes in composition affect material properties, leading to faster development cycles.
Continuous advancements in metallurgy shape the way we construct and utilize materials in various applications, impacting industries on a global scale.
Continuous advancements in metallurgy shape the way we construct and utilize materials in various applications, impacting industries on a global scale.
This guide will further elaborate on relevant materials, processes, and future directions in metallurgy.
Intro to Metallurgy
Metallurgy is a significant field that bridges science and technology. Understanding its foundations can lead to improved methods of material production, shaping various industries. By exploring metallurgy, professionals and students gain insights into properties and behaviors of metals, which are fundamental to engineering and manufacturing processes.
Definition and Scope of Metallurgy
Metallurgy is defined as the science and technology of metals, encompassing the extraction, processing, and applications of metallic materials. This includes understanding how metals are combined with non-metals to form alloys, and how they assist in the development of advanced materials. There are several branches within metallurgy, including physical metallurgy, which studies the physical properties and structure of metals, and extractive metallurgy, focused on the extraction of metals from their ores.
The scope of metallurgy extends to various sectors such as aerospace, automotive, and construction industries. It contributes to innovations like lighter and stronger materials that enhance fuel efficiency in vehicles. As sustainability becomes essential, metallurgy also plays a role in recycling processes, ensuring that metal waste is reduced and reused efficiently.
Historical Development of Metallurgy
The historical development of metallurgy dates back thousands of years, marking the evolution of human civilization. Early man discovered metals like copper and gold, which were used for tools and ornaments. Over time, metallurgy advanced with the mastery of smelting techniques, allowing for the extraction of metals from their ores.
In ancient civilizations, metallurgy was essential for producing weapons, tools, and structures. The Bronze Age represented a significant leap forward, as people began to create alloys of copper and tin to produce bronze, which was tougher and more durable than its raw components. The subsequent Iron Age saw further evolution, with iron becoming the dominant metal due to its abundance and superior strength.
Today, the narrative continues as new techniques in metallurgy emerge, focusing on nanotechnology and biomaterials, illustrating how the past informs current practices.
"Understanding the history of metallurgy provides a context for current innovations and helps predict future trends in the field."
"Understanding the history of metallurgy provides a context for current innovations and helps predict future trends in the field."
Exploring the roots of metallurgy enhances our grasp of modern applications and challenges. By linking historical significance to contemporary practices, students and professionals can better appreciate the profound impact metallurgy has on society.
Fundamental Concepts in Metallurgy
Understanding the fundamental concepts in metallurgy lays the groundwork for comprehending how metals behave and are utilized. These basic principles form the essential building blocks for advanced study and practical applications within the field. Knowledge of atomic structure, bonding, and phase diagrams is critical for students, researchers, educators, and professionals alike.
Metallurgy is fundamentally rooted in the behavior of metals at the atomic level. Grasping these initial concepts allows one to appreciate how materials can be tailored for specific use cases. When experts understand how atoms interact and bond, they can better predict and enhance material properties. In essence, metallurgy combines science and technology to develop materials that meet precise specifications, which is why these core principles are essential.
Atomic Structure and Bonding
Atomic structure and bonding are vital to understanding how metals function. Metals are primarily composed of atoms that possess unique arrangements and properties. The arrangement of electrons in these atoms determines the types of bonding that can occur.
- Types of Bonding: The two main types of bonding observed in metals are metallic bonding and covalent bonding. Metallic bonding involves the sharing of free electrons among a lattice of positively charged ions, contributing to properties like conductivity and malleability. On the other hand, covalent bonding is observed in alloys where metal atoms share electrons more tightly, often resulting in different characteristics.
- Importance of Electron Configuration: The outer electron configuration significantly influences a metal’s properties. Metals tend to have few electrons in their outer shell, allowing for effective bonding and contributing to their conductivity. Therefore, understanding electron configuration is paramount for metallurgists.
Comprehending atomic structure and the associated bonding types enables metallurgists to manipulate metals to achieve desired properties, making it a foundational aspect of metallurgy.
Phase Diagrams and Alloys
Phase diagrams provide critical insights into the phases present in a material under varying conditions of temperature and pressure. They illustrate how different alloys behave when mixed and processed, and this understanding is crucial in metallurgy.
- Understanding Phase Diagrams: A phase diagram is a graphical representation that maps the relationships between temperature, pressure, and composition. These diagrams help predict how a mixture of metals will behave when heated or cooled, making them indispensable tools in material design. The shape of the curves and lines in these diagrams allows metallurgists to determine at which temperature specific phases or mixtures can be achieved.
- The Significance of Alloys: Alloys are mixtures of two or more elements, where at least one is a metal. They are designed to enhance particular properties like strength, corrosion resistance, or malleability. Understanding the phase relationships in these alloys is essential for tailoring materials for specific industries, such as aerospace or automotive, where unique property combinations are often required.
In summary, knowledge of phase diagrams enables metallurgists to select the right alloy compositions, ensuring that the materials perform reliably under expected conditions. By mastering the fundamental concepts surrounding atomic structure and phase diagrams, potential metallurgists place themselves on solid ground for advanced studies and applications in metallurgy.
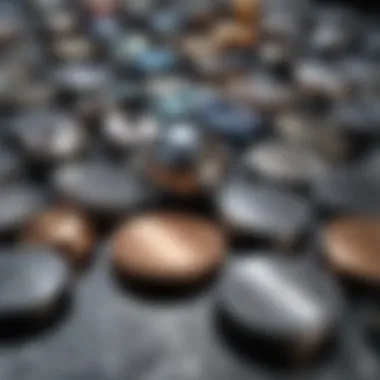
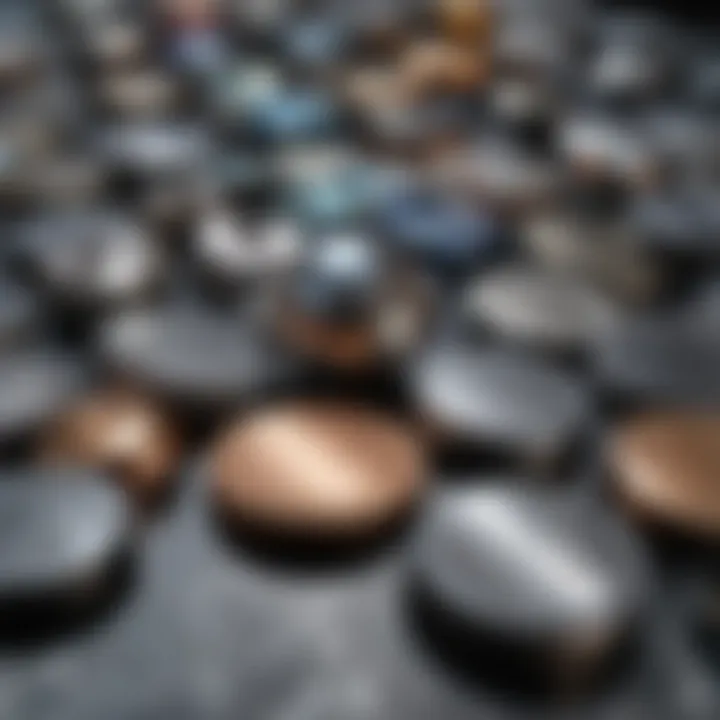
Metal Processing Techniques
Metal processing techniques form an integral part of metallurgy. They involve various methods that transform raw metal into usable forms, each tailored to achieve specific characteristics and qualities. Understanding these techniques is crucial not only for students and researchers but also for professionals working in diverse industries like aerospace, automotive, and construction. This section delves into the three main techniques: casting, welding and joining, and forming methods.
Casting Processes
Casting is one of the oldest methods of metal processing. It involves pouring molten metal into a prepared mold where it solidifies to form a specific shape. This technique offers numerous advantages, making it popular in various industries.
- Versatility: Casting can produce complex shapes that may be difficult to achieve through other methods.
- Material Efficiency: The process generally results in minimal waste, as virtually all the poured material solidifies into the final product.
- Scalability: It allows for the production of both small components and large industrial parts in bulk, ensuring both small and large scale production efficiency.
Common casting processes include sand casting, investment casting, and die casting. Each method varies in its requirements and applications. For example, investment casting is often preferred for creating parts with very fine detail, while sand casting is the most commonly used due to its low cost and versatility.
Welding and Joining Techniques
Welding and joining techniques are pivotal in assembling metal components together. These techniques are essential when creating structures, machines, and vehicles that require strong and reliable bonds between different parts.
- Weld Types: There are several welding processes including arc welding, MIG (Metal Inert Gas) welding, and TIG (Tungsten Inert Gas) welding. Each method has its unique applications and benefits. For instance, MIG welding is noted for its speed and ease, making it ideal for high-volume production.
- Joining vs. Welding: While welding joins metals through melting and solidifying the metal, other joining techniques, such as riveting or using adhesive, may not involve melting. Understanding the right technique based on the material and application is vital.
- Strength and Integrity: Proper welding ensures structural integrity, which is essential in applications that endure high stresses, such as in aerospace and automotive manufacturing.
"The weld's quality directly affects the finished product's overall performance and lifespan."
"The weld's quality directly affects the finished product's overall performance and lifespan."
Forming and Manufacturing Methods
Forming methods manipulate metal into desired shapes through mechanical processes without changing the material's mass. These techniques are critical in manufacturing various parts for different applications.
- Process Overview: Common forming techniques include rolling, forging, and stamping. Each of these methods have unique advantages. For instance, forging can enhance the mechanical properties of metal through controlled deformation, making it suitable for high-stress applications.
- Key Considerations: Tolerance and precision are crucial in forming. The choice of method often depends on the desired specifications for the end product.
- Integration with Technology: Modern manufacturing increasingly integrates technologies such as CNC (Computer Numerical Control) machining and robotics, improving precision and reducing production time.
These metal processing techniques are foundational in metallurgy. Knowledge of these methods equips learners and professionals with the critical skills necessary for advancing in this field. The evolution and optimization of these processes continue to shape the future of manufacturing across industries.
Further exploration of these topics can help deepen understanding and inspire innovations in metal processing.
Mechanical Properties of Metals
Understanding the mechanical properties of metals is crucial in metallurgy. These properties determine how materials perform under various conditions. Mechanical properties influence decisions in engineering, design, and production. Knowing these characteristics helps predict how metals will behave when subjected to stress, temperature changes, or corrosion.
Mechanically, metals exhibit distinct behaviors. Stress and strain are fundamental concepts. Stress refers to the force exerted on a material, while strain is the deformation produced. Together, they form a relationship that helps characterize metal performance.
Here are some specific mechanical properties examined in metallurgy:
- Elasticity: This property defines how a material returns to its original shape after deformation. Metals exhibit elastic behavior up to a certain limit.
- Plasticity: This is the ability of metals to undergo permanent deformation without breaking. Plasticity is essential for processes like molding and shaping.
- Strength: Metals have different strength levels, such as tensile strength, which measures resistance to being pulled apart.
- Ductility: The ability to stretch without breaking. This property is important for forming processes and is often desired in materials for pipes and wires.
- Toughness: A measure of a material's ability to absorb energy before fracturing, crucial in applications where impact resistance is needed.
Assessing these properties allows professionals to select appropriate materials for specific applications. It ensures safety, reliability, and functionality in various structures and devices.
Stress-Strain Relationships
The stress-strain relationship of metals is a key element in understanding their mechanical properties. Stress is the applied force divided by the area over which the force is distributed. Strain is the deformation that results from this applied stress. When plotted on a graph, this relationship creates a curve, often referred to as the stress-strain curve.
This curve can be broken down into several segments:
- Elastic Region: Here, stress and strain are proportional. Metals return to their original shape once the stress is removed.
- Yield Point: The point at which a material begins to deform plastically. Beyond this point, permanent deformation occurs.
- Plastic Region: In this region, strain increases with little or no increase in stress. The material will not return to its original shape after the removal of load.
- Ultimate Tensile Strength: The maximum stress that a material can withstand. It signifies the point before fracture occurs.
- Fracture Point: This represents the end of the curve where the material ultimately fails.
Understanding this relationship is crucial for engineers and researchers. It helps in designing components that can withstand expected stresses without failure. For instance, in aerospace applications, the mechanical integrity of the materials used is paramount to ensure safety and performance.
Hardness, Toughness, and Ductility
Hardness, toughness, and ductility are interrelated properties that provide insight into a metal's overall performance in various situations. Each property serves a unique purpose in material selection and processing.
- Hardness: This measures a metal's resistance to localized deformation. Hardness tests are often used in industry to assess wear resistance. Common methods include the Rockwell and Brinell tests. A harder material is usually more resistant to scratching and indentation, which is vital in applications that require durability, such as in cutting tools.
- Toughness: Toughness is the ability of a metal to absorb energy and plastically deform without fracturing. It is particularly important in structural applications where heavy loads and impacts are expected. Metals with high toughness are less likely to fracture under stress, a quality necessary for critical components in bridges and buildings.
- Ductility: Ductile metals can be drawn into wire or shaped without breaking. This property is crucial in manufacturing processes like extrusion and forging. Ductility allows metals to deform under stress before failing. This can be advantageous in applications where stretching or bending occurs.
Culmination
The exploration of mechanical properties, particularly stress-strain relationships, hardness, toughness, and ductility, is vital in metallurgy. These properties drive decisions in material selection and application across various industries, ensuring safety and performance.
Metallurgical Testing and Evaluation
Metallurgical testing and evaluation are crucial components in understanding and ensuring the integrity of materials used across various industries. The primary aim of such testing is to assess the properties of metals and alloys, ensuring they meet the required standards for specific applications. This section will explore the various methodologies used in metallurgical testing, highlighting both destructive and non-destructive techniques. Understanding these testing methods contributes significantly to material selection, quality control, and failure analysis.
Destructive Testing Methods
Destructive testing methods are used to determine the mechanical properties of materials where the test itself results in the failure of the specimen. These tests provide critical information about how a material will perform under stress and include techniques such as:
- Tensile Testing: This involves pulling a material until it fractures, measuring its tensile strength, elongation, and yield strength. The results help in understanding the material's ductility and toughness.
- Impact Testing: Evaluates a material's toughness by striking it with a pendulum. The amount of energy absorbed before failure indicates how well it can resist impact.
- Fatigue Testing: Repeatedly applies loads to a specimen to simulate long-term use. This test determines how many cycles a material can withstand before failing.
Although destructive tests provide valuable insights, one significant downside is that they require the specimen to be damaged or destroyed, limiting the number of evaluations that can be performed on a single specimen.

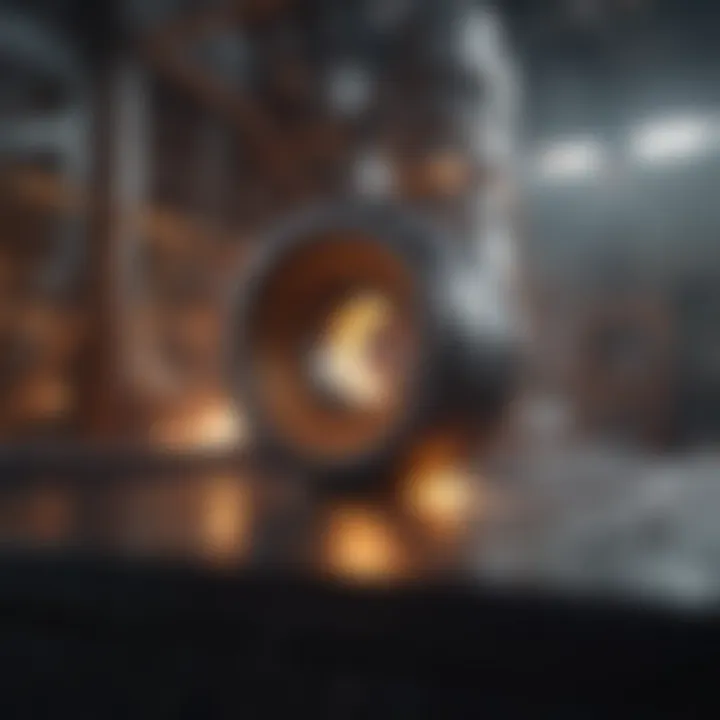
Non-Destructive Testing Techniques
Non-destructive testing techniques (NDT) are essential as they allow for the evaluation of material properties without causing any harm. These methods are ideal for assessing the integrity of materials in service or during manufacturing. Common NDT techniques include:
- Ultrasonic Testing: Uses high-frequency sound waves to detect internal flaws. When sound waves encounter a defect, they are reflected back, which can be analyzed.
- Radiographic Testing: Involves using X-rays or gamma rays to create images of the internal structure of materials. It reveals internal defects such as cracks or voids.
- Magnetic Particle Testing: This method relies on magnetic fields to detect surface and near-surface defects in ferromagnetic materials. It is especially useful in inspecting welds and castings.
Non-destructive testing methods minimize risk of damage and enable thorough evaluation of materials, making them an essential part of quality control in metallurgy.
Non-destructive testing methods minimize risk of damage and enable thorough evaluation of materials, making them an essential part of quality control in metallurgy.
In summary, metallurgical testing and evaluation are paramount for ensuring that materials meet safety and performance standards. The combination of destructive and non-destructive testing methods enables engineers and material scientists to collect detailed information about material properties, directly influencing design, manufacturing, and maintenance practices in various industries.
Applications of Metallurgy in Industry
Metallurgy plays an essential role in shaping modern industry. Its applications extend across various sectors, influencing the design, production, and performance of numerous materials used in everyday life. Comprehending these applications is crucial for both professionals and students in metallurgy. This section will explore specific elements of metallurgy in major industries, highlighting its benefits and significance.
Metallurgy in Aerospace Engineering
Aerospace engineering heavily relies on metallurgy due to the unique demands of aircraft and spacecraft materials. The aerospace sector requires materials that can withstand extreme conditions, including high temperatures and significant pressure variations. Advanced alloys, such as titanium-aluminum and nickel-based superalloys, are commonly utilized in this field. These materials are not only lightweight but also demonstrate exceptional strength-to-weight ratios.
Furthermore, the use of composites is gaining traction in aerospace design. For instance, carbon fiber reinforced polymers offer remarkable durability while significantly reducing weight. This directly contributes to fuel efficiency and performance enhancement for aircraft.
The followings are key points about metallurgy's impact in aerospace engineering:
- Lightweight materials reduce fuel consumption.
- Alloys provide necessary strength and durability.
- Innovative composites improve design flexibility.
Role in the Automotive Sector
The automotive sector also draws greatly from metallurgy, influencing both vehicle performance and safety standards. Steel remains the backbone of automotive construction, given its cost-effectiveness, strength, and versatility. However, automotive manufacturers are shifting toward using high-strength steel and aluminum alloys to improve fuel efficiency without compromising safety.
In recent years, advancements such as the development of advanced high-strength steel (AHSS) have enhanced the ability to produce lighter vehicles that meet stringent safety regulations. This shift not only aligns with environmental goals by reducing emissions but also aids in better fuel economy.
Critical points regarding metallurgical applications in automotive include:
- High-strength materials enhance safety.
- Lightweighting efforts contribute to lower emissions.
- Sustainable practices are emerging in material usage.
Construction Materials and Metallurgy
Metallurgy's influence extends into construction, where it is foundational for the development and application of structural materials. Steel is widely recognized for its structural integrity and high tensile strength; it is an indispensable component in building infrastructure. Furthermore, concrete reinforcements often rely on steel bars (rebar) to enhance tensile strength, ensuring durability in structures.
Recent trends showcase the use of innovative alloys and treated metals that resist corrosion and wear in construction environments. Corrosion-resistant materials are particularly critical in scenarios with exposure to harsh weather conditions, ensuring longevity and reducing maintenance costs.
Take note of the following aspects of metallurgy in construction:
- Steel provides strength for structural applications.
- Innovative materials improve lifespan of structures.
- Corrosion resistance minimizes maintenance needs.
In summary, metallurgy significantly influences various industries, ranging from aerospace to automotive and construction. Understanding these applications highlights the importance of metallurgy in creating safer, more efficient, and durable products. These insights also pave the way for future developments as industries continue to innovate.
Emerging Trends in Metallurgical Research
Research in metallurgy continuously evolves, responding to the demands of technology and society. Emerging trends in this field play a critical role in addressing challenges related to material properties, sustainability, and innovation. Understanding these trends is essential for students, researchers, educators, and professionals alike.
Advancements in Alloy Design
Alloy design is undergoing significant transformation with modern computational techniques and advanced modeling software. These tools allow researchers to simulate how different elements interact at the atomic level. By tailoring the composition of alloys, it is now possible to achieve specific mechanical properties.
Key advancements in this area include:
- Data-Driven Design: Utilizing large databases to analyze existing alloys and predict potential new compositions. Researchers can now identify trends and relationships that were previously difficult to comprehend.
- Machine Learning Applications: Algorithms can help optimize alloy properties by analyzing various inputs, such as thermal conductivity or tensile strength. This reduces the trial-and-error process in developing new materials.
- High-Throughput Methodologies: These allow the rapid synthesis and testing of numerous alloy combinations, accelerating the development cycle.
The advent of these technologies not only improves performance but also reduces costs and time in alloy production, thereby enhancing the competitiveness of industries relying on advanced materials.
Sustainable Metallurgical Practices
Environmental consciousness is becoming increasingly vital in metallurgy. Sustainable practices are essential to mitigate the ecological impact of metallurgical processes. New trends focus on minimizing waste and increasing the efficiency of resource usage.
Key aspects of sustainable metallurgical practices include:
- Recycling and Reusability: Metals like aluminum and copper are highly recyclable. Efforts in metallurgy now aim to improve the recycling processes, ensuring these metals can be reused effectively without significant loss in quality.
- Green Chemistry Initiatives: Research is targeting the reduction or elimination of hazardous substances in metallurgical processes. This can involve using water-based solvents or reducing energy consumption.
- Life Cycle Assessment: This practice evaluates the environmental impact of a product from extraction through production to disposal. Aligning practices with such assessments promotes more sustainable decision-making in metallurgy.
"As the world faces resource scarcity, the integration of sustainability into metallurgy is no longer optional; it is a fundamental requirement."
"As the world faces resource scarcity, the integration of sustainability into metallurgy is no longer optional; it is a fundamental requirement."
Through these advancements, the field of metallurgy is aligning itself with broader societal needs, ultimately contributing to a more sustainable future. Engaging in such practices not only aids environmental conservation but also fosters innovation that meets market demands in a responsible way.
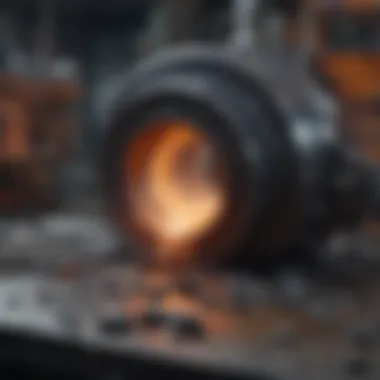
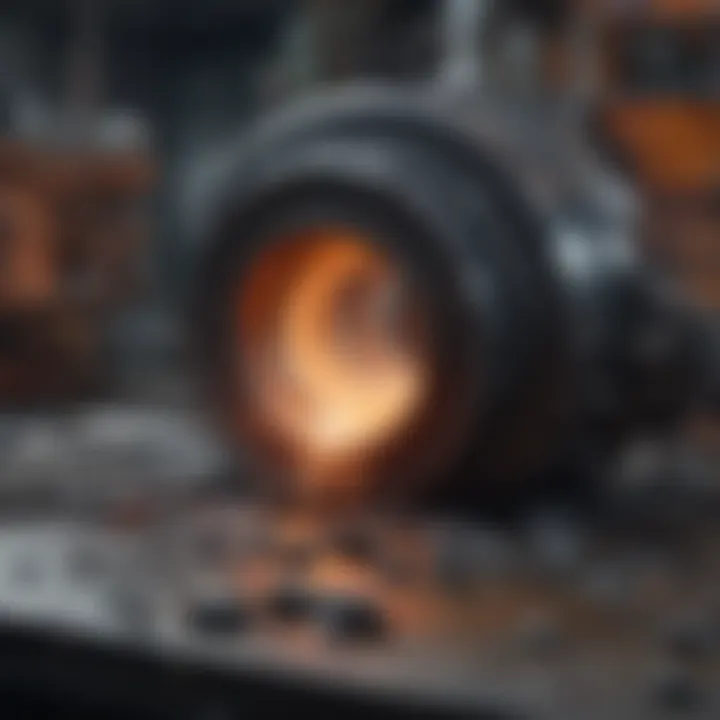
Metallurgy and Environmental Considerations
Metallurgy is a critical field that intersects with environmental issues in various ways. As the demand for metal products grows globally, it is essential to understand how metallurgical processes impact the environment. This relationship involves factors such as emissions, waste generation, energy consumption, and the depletion of natural resources. Addressing these environmental concerns requires a significant shift in how materials are processed and reused.
Impact of Metallurgical Processes on the Environment
Metallurgical processes can cause substantial environmental harm. The extraction of metals from ores usually involves mining operations that disrupt ecosystems, generate dust, and produce pollutants. For example, smelting operations emit greenhouse gases and other harmful substances, contributing to air and water pollution. Additionally, waste materials from metallurgical processes, such as slag and tailings, pose disposal challenges and can leach toxins into the soil and waterways.
To mitigate these impacts, metallurgists are encouraged to adopt cleaner technologies and practices. Innovations such as hydrometallurgy and biotechnological methods are emerging, offering alternatives that are less harmful to the environment. These processes aim to minimize waste and reduce energy consumption, which are critical aspects of environmental conservation.
Recycling and Reusability of Metals
Recycling metals is a key strategy to mitigate the environmental footprint of metallurgy. The process involves collecting and processing used metals to create new products. This not only reduces the need for raw material extraction but also conserves energy. For example, recycling aluminum saves approximately 90% of the energy needed to produce new aluminum from ore.
The reusability of metals is another important concept in sustainable metallurgy. Many metals, such as steel and copper, can be recycled multiple times without losing their properties. This attribute makes them valuable in promoting circular economy practices.
Incorporating recycling and reusability into metallurgical practices contributes significantly to reducing waste and pollution. It aligns with global sustainability goals and offers economic benefits by lowering production costs and resource dependency.
By focusing on recycling and sustainable practices, the metallurgy industry can play a pivotal role in environmental stewardship.
By focusing on recycling and sustainable practices, the metallurgy industry can play a pivotal role in environmental stewardship.
Summary
The interplay between metallurgy and environmental considerations is complex but crucial. Recognizing the adverse impacts of metallurgical processes on the environment drives the need for innovation and sustainable practices. Fostering recycling and reusability of metals stands as an essential strategy to reduce waste and improve efficiency. As the industry progresses, adopting these sustainable practices will be vital for the health of our planet.
Educational Pathways in Metallurgy
Educational pathways in metallurgy are vital for anyone looking to build a successful career in this field. This area of study not only lays a foundation for theoretical knowledge but also equips students with vital practical skills necessary in various industries. As metallurgy is at the intersection of science and engineering, having formal training is often essential for understanding complex processes, materials, and applications.
Participation in degree programs leads to an understanding of various metal properties, their interactions, and advanced processing techniques. These programs often cover a wide range of subjects which are relevant in today’s industrial landscape.
Moreover, prospective students must also consider the certifications available in metallurgy. Certifications enhance one's qualifications and can differentiate candidates in the job market. Accredited courses or certifications from recognized institutions provide credibility and indicate proficiency in specific areas within metallurgy.
"Understanding metallurgy is not just about learning theories; it's about applying them in real-world situations."
"Understanding metallurgy is not just about learning theories; it's about applying them in real-world situations."
Thus, finding the right educational pathway is crucial. It will influence the skill set developed and the career opportunities available. When students select programs that align well with their career ambitions, they build a strong base not just in learning but in practical applications as well.
Degree Programs and Certifications
Various degree programs are available in metallurgy, including Bachelor’s, Master’s, and PhD levels. A Bachelor's degree in Metallurgical Engineering or Materials Science will introduce students to the fundamental principles that govern metal processing and material properties.
Many universities offer specialized tracks focusing on areas such as:
- Extractive Metallurgy
- Physical Metallurgy
- Mechanical Metallurgy
Postgraduate degrees such as a Master’s or PhD can further enhance one’s expertise and open doors to more advanced research or positions in academia or industry. Certifications like those from the American Society for Metals or other recognized organizations provide additional validation of one’s skills and knowledge.
Importance of Internships and Research Experience
Internships and research experiences create essential bridges between academic learning and practical application. They allow students to apply theoretical concepts in real-world settings, enhancing understanding and reinforcing learning. Participating in internships provides exposure to industry standards, teamwork, and technology used in metallurgy.
Research experience can play a significant role as well. Engaging in projects can strengthen analytical abilities and critical thinking. It also helps build a professional network, which is beneficial for future job prospects.
The skills acquired during these experiences are invaluable. An internship can sometimes lead to permanent positions, giving students direct entry into the workforce with relevant experience and contacts.
In summary, pursuing educational pathways in metallurgy offers varied routes that are rich with opportunity. A combination of degrees, certifications, and hands-on experiences will effectively prepare individuals for challenges in the metallurgical field.
Culmination
In this article, we have delved into the substantial field of metallurgy, illustrating its complex theoretical foundations and practical applications. The conclusion is significant as it synthesizes the key points discussed and emphasizes the relevance of metallurgy in various industries. As we reflect, it becomes clear that metallurgy is not merely an academic subject; it is a crucial discipline directly impacting engineering, manufacturing, and sustainable practices.
Summary of Key Aspects of Metallurgy
Several aspects of metallurgy have been highlighted throughout this guide. These include:
- Fundamental Concepts: An understanding of atomic structure and bonding is vital. This underpins how metals behave and interact with each other in various conditions.
- Metal Processing Techniques: The methods used to mold metals into required shapes, such as casting, welding, and forming, are essential for practical application in real-world scenarios.
- Mechanical Properties: The discussion on stress-strain relationships, hardness, toughness, and ductility provide insights into how metals respond to forces and conditions, impacting their selection for different applications.
- Metallurgical Testing: Evaluation methods, both destructive and non-destructive, ensure materials meet quality and safety standards before use in critical applications.
- Emerging Trends: Advancements in alloy design and sustainable practices demonstrate ongoing innovation within the field, addressing both performance needs and environmental concerns.
Metallurgy also plays an undeniable role in sectors like aerospace, automotive, and construction, showcasing its versatility and importance.
Future Directions in the Field
Looking ahead, the field of metallurgy is expected to evolve significantly. Some key directions may include:
- Advanced Materials: Research into high-performance alloys and composites continues to grow, aiming to create lighter, stronger, and more corrosion-resistant materials.
- Sustainability Practices: With increasing awareness of environmental issues, sustainable metallurgical processes that minimize waste and energy consumption are gaining traction.
- Nanotechnology: The integration of nanomaterials in metallurgy could lead to revolutionary changes in material properties, opening new applications.
- Digital Fabrication: Advancements in technologies like additive manufacturing may transform how metals are shaped and used, allowing for more complex designs and reduced material usage.
- Interdisciplinary Approaches: Future metallurgists will likely collaborate across various fields, integrating insights from materials science, engineering, and environmental science.
The synthesis of these aspects can significantly reshape the future of metallurgy and influence various industries, making it a vibrant and continuously evolving field.
The synthesis of these aspects can significantly reshape the future of metallurgy and influence various industries, making it a vibrant and continuously evolving field.