Crafting Electric Vehicle Batteries: An In-Depth Guide
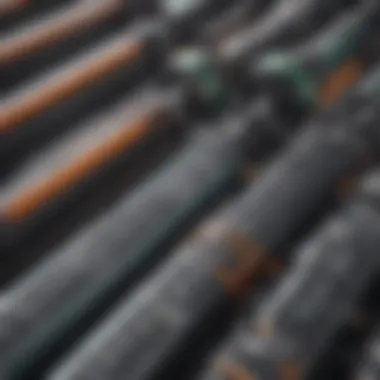
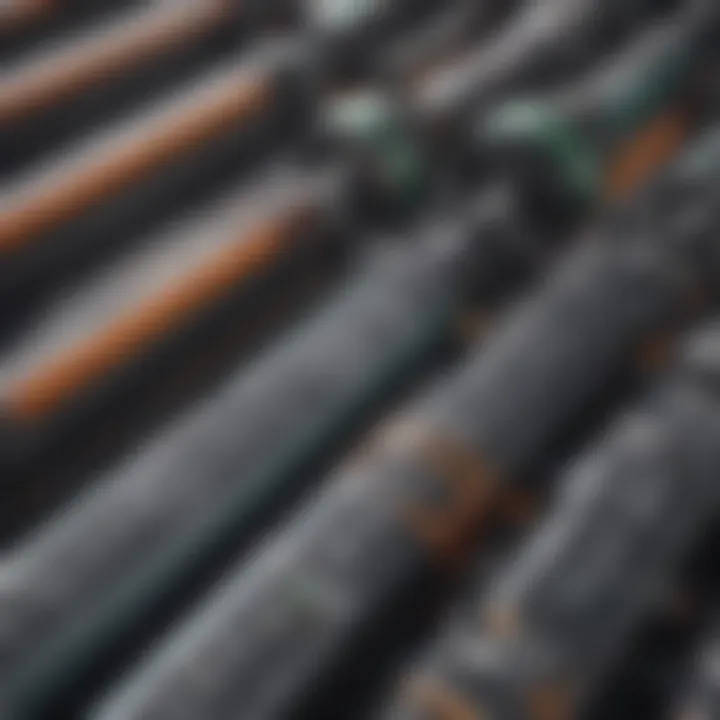
Intro
Electric vehicles (EVs) are really shifting gears in the automotive industry, and at the heart of this transformation lies the battery. You can think of an EV battery as the lifeblood of the vehicle, powering everything from the engine to the air conditioner. This process of creating these batteries isn't just cutting-edge; it's a blend of chemistry, engineering, and environmental science that has evolved tremendously over recent years. With each innovation, we not only enhance performance but also tackle larger concerns about sustainability and safety.
As we dive into what makes these batteries tick, it’s crucial to start with the Key Concepts that underpin their design and manufacturing.
Understanding Electric Vehicle Batteries
Understanding electric vehicle batteries is fundamental for grasping the broader landscape of EV technology. As we delve into crafting these batteries, we discover that the very essence of an electric vehicle lies within its battery system. The battery not only powers the vehicle but serves as a keystone in the transition toward more sustainable transport solutions.
When one thinks of EV batteries, it's clear they aren’t merely components; they’re a technological embodiment of advancement and innovation. We will uncover various aspects that propel electric vehicles forward, including why certain batteries are chosen over others, the specific roles they play, and how they impact performance and longevity.
Definition and Purpose
Electric vehicle batteries act as a reservoir for electrical energy, designed to power the electric motor. Their primary purpose is straightforward: store and deliver electric energy efficiently. From everyday commuting vehicles to high-performance electric cars, the ability to provide energy on demand is what defines the experience of driving an EV.
In a more technical sense, these batteries convert stored chemical energy into electrical energy using electrochemical reactions. Each of these batteries has its own definition and operational parameters that shape user experience, charging times, and overall efficiency.
Types of EV Batteries
Electric vehicles typically utilize several types of batteries, each bringing unique advantages and disadvantages to the table. Understanding these types becomes crucial for choosing the right battery for specific applications within the electric vehicle sector.
Lithium-ion Batteries
Lithium-ion batteries have become synonymous with modern EVs, known for their high energy density and long life span. This type of battery can store a substantial amount of energy in a relatively compact space, making it a popular choice for manufacturers aiming to create lightweight vehicles with extended ranges.
One standout feature of lithium-ion batteries is their relatively efficient charging process. Unlike traditional batteries that struggle with memory effects, lithium-ion batteries perform well when partially discharged and recharged. However, they do present challenges, such as vulnerability to thermal runaway under certain conditions—an aspect that manufacturers are continuously addressing through safety measures and innovations.
Nickel-Metal Hydride Batteries
While nickel-metal hydride batteries aren't as common in newer electric vehicles, they still play a significant role, especially in hybrid cars. Their key characteristic lies in their durability and ability to endure numerous charge cycles without significant degradation. This aspect makes them an attractive option for certain applications where battery longevity is pivotal.
These batteries are generally heavier and bulkier compared to lithium-ion options, presenting a trade-off between energy capacity and weight. A unique feature is their capacity to maintain performance in lower temperatures, which can be a decisive factor in regions with harsh climates. However, they lag behind in energy density, which has led to a gradual shift towards lithium-ion technologies for fully electric vehicles.
Solid-State Batteries
Solid-state batteries represent a cutting-edge advancement in battery technology, promising higher energy densities while enhancing safety. Unlike traditional batteries that use liquid electrolytes, solid-state batteries utilize a solid electrolyte, significantly reducing the risks of leaks and fires associated with liquid variants. This move could potentially lead to safer and longer-lasting batteries in the near future.
The unique feature of solid-state systems is their ability to pack energy more densely, which means they could power vehicles over longer distances on a single charge. Challenges remain, including manufacturing complexities and high costs that limit widespread adoption for now. Yet, their potential to revolutionize the industry makes them a focal point of ongoing research.
Core Components of EV Batteries
Understanding the core components of electric vehicle (EV) batteries is crucial for grasping how these batteries operate and contribute to the overall performance of electric vehicles. It’s like knowing the engine inside a car; without this knowledge, one only sees the surface. Each part plays a distinct role, ensuring efficiency, cellular stability, and longevity.
Anode Materials
Graphite
Graphite is widely recognized as the main player in the world of anode materials. Its ability to adequately store lithium ions makes it a favored choice. One might say, graphite is the bread and butter of battery production.
In terms of performance, graphite offers a solid cycling stability and decent conductivity. This helps in maintaining efficiency during multiple discharge and charge cycles. What sets graphite apart is its ready availability and lower cost compared to other materials.
However, there are drawbacks. While graphite is reliable, it has limitations on maximum energy density. As EV technology pushes toward higher capacities, the old faithful might struggle to keep up. Still, for now, its benefits outweigh its limitations, making it indispensable in battery design.
Silicon-Based Compounds
Silicon-based compounds are coming into play as alternative anode materials, slinging seasoned graphite to the sidelines. Silicon has an enormous capacity for lithium ions, which is like striking gold when it comes to energy retention.
The standout feature of silicon is its high theoretical capacity, which is significantly higher than that of graphite, about ten times more. This makes silicon a powerhouse choice in next-gen battery designs. However, this unique feature comes with a catch. Silicon tends to expand and contract significantly with cycling, leading to structural breakdown over time.
Thus, while silicon holds promise, research is focused on stabilizing it for it to be a practical alternative to graphite in mainstream production.
Cathode Materials
Lithium Cobalt Oxide
Lithium cobalt oxide is a renowned cathode material, contributing significantly to many commercial lithium-ion batteries. Its fame is primarily due to its high energy density, which suits applications requiring light weight and powerful output. In simple terms, it’s like the a-list actor of battery chemistry, often stealing the spotlight.
The notable advantage of lithium cobalt oxide is its stability at higher voltages, which supports longer-lasting battery life. Yet, cobalt comes with its issues, such as limited supply and ethical concerns related to mining practices. Thus, while lithium cobalt oxide is popular, the conversation surrounding sustainable sourcing is gaining momentum.
Lithium Iron Phosphate
Another contender in the cathode material arena is lithium iron phosphate. It’s known for being robust and thermally stable, which is essential for safety in electric vehicles. This characteristic allows it to operate well in a broader range of temperatures.
Why is it gaining traction? Well, its cycle life is often longer than that of lithium cobalt oxide, leading to sustainability in long-term usage. However, it has a lower energy density, which may not suit applications demanding high power output. In a sense, it's a trade-off; while you get reliability, some potential energy output can be sacrificed.
Electrolyte Options
Liquid Electrolytes
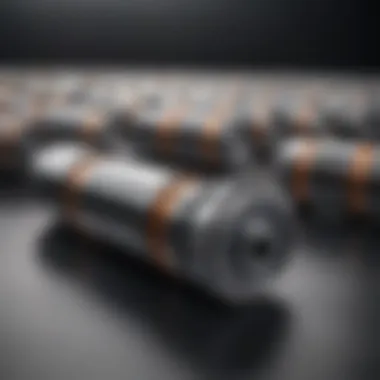
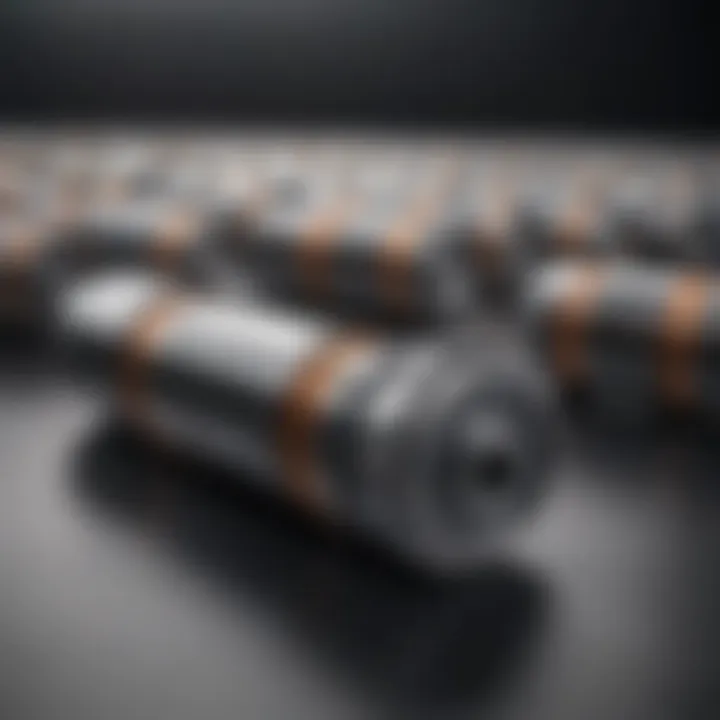
Liquid electrolytes bring fluidity to the field of EV battery design. They play a key role in facilitating the movement of lithium ions between the anode and cathode. Most conventional battery chemistries utilize this approach, and it’s proven effective over time.
The primary appeal of liquid electrolytes is their high ionic conductivity, allowing for efficient energy transfer. Yet, they are prone to leakage and might pose safety concerns under specific conditions, such as high temperatures. Therefore, while liquid electrolytes work well, manufacturers are continually exploring alternatives to overcome safety hazards.
Gel and Polymer Electrolytes
Gel and polymer electrolytes are stepping into the limelight as solid alternatives to traditional liquid electrolytes. They offer enhanced safety by reducing risks of leakage and flammability. Think of them as protective barriers in the battery world.
This type of electrolyte often has lower conductivity compared to their liquid counterparts but compensates for it with stability and flexibility. It can adjust to different shapes without compromising safety. The main downside is their relatively higher manufacturing cost, which might deter manufacturers from large-scale adoption immediately.
"As the demand for electric vehicles continues to grow, understanding these core components becomes ever more relevant, shaping the future of transportation and technology."
"As the demand for electric vehicles continues to grow, understanding these core components becomes ever more relevant, shaping the future of transportation and technology."
In summary, the core components of EV batteries—anode and cathode materials, as well as electrolytes—play significant roles in determining battery performance and safety. Each material possesses unique attributes that influence energy density, charge cycles, and overall sustainability. As innovations cease to halt, the future of these essential elements will continue to evolve.
Materials Selection Process
The materials selection process is a critical piece of the puzzle when it comes to electric vehicle battery manufacturing. Choosing the right materials not only influences the performance and safety of the batteries but also plays a significant role in cost management and sustainability. In a fast-evolving industry like electric vehicles, every decision in this phase can lead to ripple effects that impact overall production efficiency and market viability.
Criteria for Choosing Materials
Cost
Cost stands as a significant factor in material selection for EV batteries. Lowering material expenses enhances the overall competitiveness of the manufacturing process which, in a high-stakes market, can be the difference between profit and loss. Many companies opt for cost-effective materials like graphite for anodes or lithium iron phosphate for cathodes due to their reliable performance coupled with relatively low prices.
However, there's a trade-off here. While cheaper materials can reduce upfront costs, they may not always deliver the desired performance or lifespan. If the material doesn't hold up under stress, a manufacturer might find themselves spending more in the long run on replacements and warranty costs. It’s a balancing act, as business folk are always saying: "Penny wise, pound foolish."
Performance
Performance is equally crucial when evaluating materials for EV batteries. The material's ability to deliver energy effectively can greatly influence the end-user experience. Lithium-ion batteries, for instance, are celebrated for their high energy density and efficiency, making them a popular choice. Such capabilities allow an electric vehicle to drive longer distances before needing a recharge.
The key characteristic of performance-focused materials lies in how well they translate energy input to output. High-performance materials can be more costly, creating dilemmas in budget allocation that companies must navigate smartly. As the saying goes, "You get what you pay for," and this applies to materials in battery crafting.
Sustainability
Sustainability considerations are gaining traction in material selection within the EV battery industry. As consumers grow more environmentally conscious, manufacturers are beginning to seek materials that can be responsibly sourced and recycled. For example, efforts to source ethically produced cobalt reflect this trend, showing that companies are thinking long-term about their ecological footprint.
Sustainable materials not only address environmental concerns but also strengthen brand reputation. However, they often come with higher costs and may present additional complexity in sourcing. The trade-off here is clear; greener choices might cost more upfront but can lead to stronger customer loyalty and regulatory compliance over time.
Innovative Material Developments
The landscape of materials used in EV batteries is ever-changing, driven by the need for enhanced performance and sustainability. New advancements are working their way into the mix, including biodegradable composites and alternative lithium sources. The continual evolution in this area means that staying informed is crucial not just for manufacturers but for anyone interested in the future of mobility.
The selection of materials impacts not just performance and cost but the very sustainability of our energy future.
The selection of materials impacts not just performance and cost but the very sustainability of our energy future.
In summary, while selecting materials for EV battery production involves navigating a complex web of cost, performance, and sustainability criteria, it also opens doors to innovations that could redefine the industry. With every step taken during this selection process, manufacturers are effectively writing the next chapter of electric vehicle technology.
Manufacturing Techniques for EV Batteries
The manufacturing process of electric vehicle (EV) batteries plays a crucial role in determining their performance, longevity, and overall reliability. There are myriad factors to consider, such as the choice of materials, precision in production, and adherence to safety standards. It’s a complex dance of science and engineering that requires an intimate understanding of both the materials involved and the technological processes at play. By mastering these techniques, manufacturers can not only increase efficiency but also enhance the performance and sustainability of the batteries they produce.
Cell Production
Cell production is the initial stage of battery manufacturing where individual cells, the smallest unit of an EV battery, are created. Thought of as the heart of the battery, these cells are responsible for storing and releasing energy. The process begins with the assembly of the anode and cathode materials, typically electrodes made from intricate composites like graphite or lithium cobalt oxide. This is often achieved through techniques such as
- Coating: Here, electrodes are coated in the active materials, ensuring even distribution, which is vital to operational efficiency.
- Drying: After coating, the electrodes need to be dried to evaporate solvents, often using high-temperaturs ovens to ensure thorough removal of any moisture.
- Pressing: Once dried, electrodes are compressed to enhance conductivity and energy density, thereby optimizing overall battery performance.
These individual cells then undergo rigorous testing to ensure they meet necessary quality standards before moving to the next phase. Often, a production line that employs automated machinery ensures consistency and minimizes human error, a critical factor given the requirements of modern EVs.
Module Assembly
Following cell production, the next step involves module assembly. This is where the individual cells are grouped into modules, a larger structure that can manage energy flow and enhance safety. The module assembly process is vital as it integrates multiple cells and connects them in series or parallel configurations, which defines how they will operate in tandem.
During this phase, considerations include:
- Thermal Management: Modules are designed with specialized cooling systems to manage heat, which can affect battery performance and lifespan.
- Connectivity: Wires and connectors are installed to ensure efficient energy transfer, boosting the overall performance of the vehicle’s battery.
- Safety Features: Adding protective layers and monitoring systems is crucial here; this prevents potential malfunction or fires, safeguarding both the battery and the vehicle it's part of.
By employing sophisticated methodologies, manufacturers guarantee that these modules can perform reliably under various conditions.
Pack Configuration
Lastly, we come to pack configuration, the process where multiple modules are combined into a single, cohesive battery pack that will ultimately be installed in the electric vehicle. This stage is crucial as it determines how the battery interacts with the vehicle’s energy management systems.
Key elements in this phase include:
- Design Layout: Engineers carefully plan the physical configuration of battery packs, ensuring that all modules fit snugly, which helps to optimize weight distribution and space utilization within the vehicle.
- BMS Integration: Each battery pack incorporates a Battery Management System (BMS) that monitors the health and performance of the battery, ensuring optimal efficiency. This helps prevent overcharging or excessive discharging, prolonging the battery’s lifecycle.
- Final Quality Checks: Before battery packs leave the factory, they undergo a final set of rigorous tests to ensure they meet safety standards and performance specifications. This thorough inspection often includes simulated stress testing to examine how packs perform under extreme conditions.
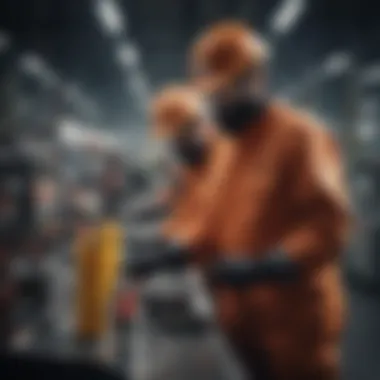
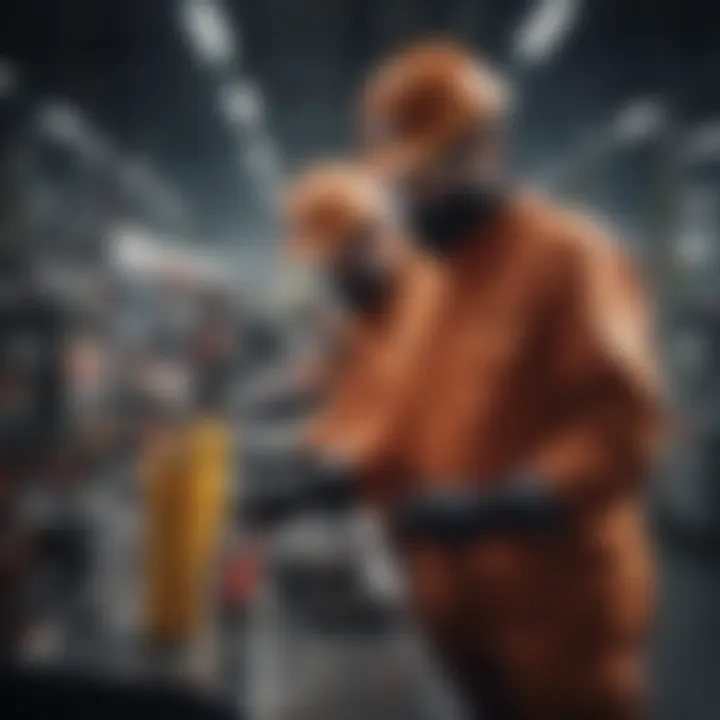
Quality Control Measures
Quality control measures are central to the manufacturing of electric vehicle batteries. They ensure that each component functions correctly and meets the strict specifications for safety and performance. In an industry where the stakes are high, having robust quality control is not just a formality; it’s a necessity that traces every step of battery production, from material selection to the final assembly.
Quality control impacts many facets of battery production: ensuring safety for end-users, extending product lifespan, and providing manufacturers with tangible data to improve future designs. By assessing key characteristics of batteries, including capacity and thermal stability, manufacturers can safeguard against failures that lead to costly defects or dangerous scenarios.
“Quality is never an accident; it is always the result of intelligent effort.”
“Quality is never an accident; it is always the result of intelligent effort.”
Testing Procedures
Capacity Testing
Capacity testing examines how much energy a battery can store and deliver under standard conditions. This assessment is critical for determining the viability of a battery in real-world use, especially in electric vehicles that demand performance. A battery that doesn’t retain its capacity effectively can lead to significant operational issues in an electric vehicle, like shorter driving ranges or unexpected power losses.
One of the key features of capacity testing is its ability to simulate various usage scenarios. This provides manufacturers with valuable insights into how their products will perform across different conditions. However, one notable disadvantage is that this testing can be resource-intensive and time-consuming, potentially delaying product launches.
Cycle Life Testing
Cycle life testing assesses how many charge and discharge cycles a battery can undergo before its capacity falls to an unusable level. This metric is crucial because it directly relates to the longevity of the battery, impacting both the environment and consumers' pocketbooks. An extended cycle life is a hallmark of quality in a battery.
The prime benefit of cycle life testing is that it reveals the durability of the battery over time. This forms a predictive model for consumers considering long-term investments in electric vehicles. Yet, just like capacity testing, cycle life testing can be complicated to perform, as factors influencing results can vary widely, including temperature and humidity.
Thermal Stability Assessments
Thermal stability assessments evaluate how a battery reacts to temperature fluctuations, which is vital for safety. Given the risks associated with overheating, it’s essential to ensure that the materials used in battery construction can withstand a range of operating temperatures. Adverse thermal reactions can lead to battery fires, posing significant hazards.
This type of assessment underscores the importance of material selection and design in mitigating risks. While providing assurance of safety, these tests can also identify materials that may not perform well under stress, thus guiding further research and development in alternative materials. However, the downside often encountered is that thermal tests can require extensive setups and lead to longer testing times, inadvertently increasing costs.
Standards and Certifications
Standards and certifications serve as benchmarks for quality, ensuring products meet industry regulations. They help both manufacturers and consumers trust in the performance and safety of electric vehicle batteries, playing a pivotal role in the marketplace.
ISO Standards
ISO standards set internationally recognized criteria for different aspects of manufacturing processes. They guide manufacturers toward practices that ensure consistency and quality. Following ISO guidelines indicates a commitment to quality and safety, which consumers increasingly value.
The unique aspect of ISO Standards lies in their global applicability. This means that a battery manufacturer adhering to these standards can potentially market products worldwide. However, navigating these regulations can also be complex, sometimes requiring extensive documentation.
SAE International Guidelines
SAE International guidelines focus on specific engineering practices, particularly related to automotive components. These guidelines are pivotal, especially for the safety and performance of electric vehicle batteries. Aligning with these standards can significantly bolster a manufacturer’s credibility in the marketplace.
One of the main benefits of adhering to SAE guidelines is that they represent a convergence of industry expertise, having been developed by professionals in their fields. However, the downside can be the costs associated with compliance testing and delays that might occur as companies work to meet certification requirements.
In summary, quality control measures not only reassure consumers but also act as a crucial framework guiding manufacturers toward producing safer and more efficient electric vehicle batteries. These standards and testing procedures enhance product reliability and ensure consistent performance across the industry.
Environmental Considerations
In the realm of electric vehicle (EV) battery manufacturing, environmental considerations have taken center stage. With the burgeoning emphasis on sustainability, it’s become vital for manufacturers to assess their ecological impact. This section explores the necessity of responsible practices in raw material sourcing and effective strategies for recycling and lifecycle management.
Sourcing Raw Materials Responsibly
The reliance on raw materials significantly shapes the environmental footprint of battery production. Commonly used materials like lithium, cobalt, and nickel, are not just abundant on Earth; they come with a set of challenges. Mining these minerals often leads to ecological degradation, water contamination, and even societal issues, particularly in regions where mining takes place.
To mitigate these adverse effects, companies need to commit to sourcing minerals responsibly. This involves:
- Ethical Mining Practices: Engaging with certified suppliers who follow ethical protocols can reduce the harm to local communities and ecosystems.
- Supply Chain Transparency: Increased traceability of materials aids in ensuring that they aren’t sourced through exploitative means. Blockchain technology can be an asset here, providing real-time tracking of materials from mine to manufacturing.
- Locally Sourced Materials: Whenever feasible, tapping into local resources minimizes transportation emissions, supporting both the economy and the environment.
Adopting these practices not only enhances the sustainability of battery production but also strengthens the overall brand reputation. Companies that prioritize responsible sourcing often find themselves favorably viewed by consumers and investors alike.
Recycling and Lifecycle Management
As the adage goes, "out with the old, in with the new," but when it comes to EV batteries, there's much more to consider. The lifecycle of a battery does not end when it is no longer functioning as intended. Instead, the emphasis should be on effective recycling and management.
Recycling EV batteries presents several benefits:
- Resource Recovery: Many of the materials used in batteries can be extracted and reused, which alleviates the demand for new raw materials.
- Reduced Environmental Impact: By recycling, we lessen the need for mining, which consequently curtails habitat destruction and pollution associated with such activities.
- Energy Conservation: It’s often less energy-intensive to recycle materials than to mine new ones.
Moreover, manufacturers must not only focus on recycling after a battery has outlived its usefulness, but also consider the entire lifecycle of the battery. This involves:
- Design for Disassembly: Creating batteries that can be easily disassembled at their end-of-life promotes effective recycling practices. Designing batteries with recyclable materials in mind can significantly improve recovery rates.
- Second-Life Applications: Batteries that are no longer suitable for vehicle use can still have a role to play, such as in stationary energy storage solutions for homes or commercial applications.
"The future of battery technology lies not only in innovation but also in creating a circular economy that minimizes waste and maximizes resource efficiency."
"The future of battery technology lies not only in innovation but also in creating a circular economy that minimizes waste and maximizes resource efficiency."
It’s clear that addressing environmental considerations isn’t merely an afterthought; it’s a crucial element in the evolution of EV battery manufacturing. In recognizing the ecological impacts from the ground up, manufacturers can pave the way for a more sustainable future.

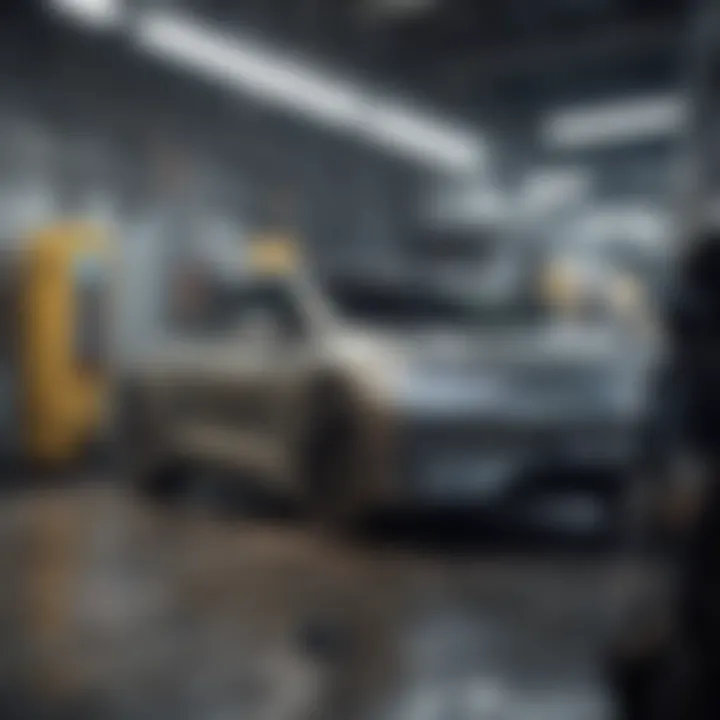
Safety Protocols in Battery Manufacturing
Ensuring the safety of battery manufacturing is essential, both for the protection of workers and the integrity of the products being created. Electric vehicle batteries, while fundamental to the operation of modern vehicles, involve materials and processes that carry various risks. Hence, implementing robust safety protocols is not just advisable but imperative. These protocols encompass a range of measures designed to mitigate hazards and ensure compliance with industry standards.
As the demand for electric vehicles rises, so does the necessity for stringent safety measures in battery production. This section critically examines hazard identification and mitigation strategies, alongside fire safety measures that are vital in the lifecycle of battery manufacturing.
Hazard Identification and Mitigation
In the world of battery manufacturing, recognizing potential hazards is the first step in fostering a safe work environment. Manufacturers must adopt a proactive approach to hazard identification which, ideally, starts before any production begins. With processes that involve chemical reactions, high voltages, and potentially reactive materials, the risks are considerable.
Key considerations for hazard identification include:
- Material Safety Data Sheets (MSDS): Every chemical used in battery production has associated safety data. These documents should be easily accessible and provide crucial information about handling, exposure, and first aid measures.
- Regular Risk Assessments: Conducting frequent risk assessments helps in identifying new threats that may arise as production processes evolve or change.
- Employee Training: Ensuring that workers are thoroughly trained on potential hazards and proper equipment usage is essential. Well-informed employees are better equipped to spot dangerous situations and respond appropriately.
Once hazards have been identified, mitigation strategies must be established and continually refined. An effective strategy may encompass technical and organizational measures, like redesigning processes to minimize risk. Correcting any identified deficiencies quickly can prevent accidents before they even occur.
Fire Safety Measures
Considering that battery manufacturing involves flammable materials and high-energy components, fire safety is of paramount importance. Fires in battery production can escalate rapidly, resulting in extensive damage and loss of life. Therefore, comprehensive fire safety measures must be in place.
Critical fire safety protocols include:
- Fire Suppression Systems: Installation of advanced fire suppression systems, such as sprinkler systems and gas suppression units, can effectively minimize fire spread once initiated.
- Spatial Regulations: Keeping flammable materials away from ignition sources and ensuring that workspaces are not overcrowded can drastically reduce the risk of fires breaking out.
- Regular Drills and Training: Conducting regular fire drills ensures that employees know how to respond in case of a fire. Familiarity with evacuation routes and safety equipment is crucial to prevent panic during an actual emergency.
"A commitment to safety in battery manufacturing not only protects employees but also boosts overall productivity and company reputation."
"A commitment to safety in battery manufacturing not only protects employees but also boosts overall productivity and company reputation."
Current Innovations in EV Battery Technology
In the rapidly evolving field of electric vehicles, technological advancements in battery design and manufacturing have become a vital focus. This section sheds light on current innovations in EV battery technology, underscoring their significance in enhancing battery performance, safety, and sustainability. As automakers increasingly shift towards electric solutions, these innovations play a crucial role in addressing market demands and regulatory pressures for cleaner transportation.
Advancements in Battery Chemistry
High-Energy Density Batteries
High-energy density batteries have captured the spotlight due to their significant contribution to extending the range of electric vehicles. By packing more energy into a smaller, lighter package, these batteries enable EVs to travel longer distances without the need for recharging, which is one of the major consumer concerns. The key characteristic of high-energy density batteries is their ability to maximize energy output per unit mass, making them an excellent choice for both manufacturers and consumers.
One unique feature is the incorporation of advanced cathode materials like nickel-rich compounds, which enhance the energy capacity without increasing the size of the battery. However, they are not without disadvantages; these batteries often come at a higher upfront cost and may require more sophisticated thermal management systems to operate safely at high performance.
Fast-Charging Solutions
Fast-charging solutions have emerged as a game changer in the EV landscape, alleviating the time constraints typically associated with electric vehicle charging. With the ability to charge batteries from empty to about 80% in a mere 30 minutes, these solutions are tailored for the busy modern life. The key characteristic of fast-charging technology is its compatibility with high current supply, which significantly reduces the charging duration.
Unique to this innovation is the development of advanced charging stations integrated with smart technology to optimize charging times and battery health. However, some disadvantages include the need for robust infrastructure and potential thermal challenges that can arise from the rapid energy influx.
Emerging Manufacturing Techniques
3D Printing Techniques
3D printing techniques represent a cutting-edge approach to manufacturing EV batteries, enabling greater customization and efficiency in the production process. This technology allows producers to create intricate battery designs that can better accommodate specific vehicle requirements, enhancing performance and driving range. The key characteristic of 3D printing is its ability to reduce material waste and streamline production time.
A unique feature of this method is the potential to produce battery components with complex geometries that improve thermal pathways and energy distribution. However, the technology is still evolving, and scaling it for mass production poses a significant hurdle that manufacturers need to overcome.
Automated Production Lines
Automated production lines are transforming the way electric vehicle batteries are made by introducing precision and speed into the manufacturing process. The integration of robotics and AI ensures consistent quality, minimizing human error and operational costs. The key characteristic of automated systems is their capacity for rapid, large-scale production.
One distinct advantage of automation is increased safety, as workers are kept away from potentially hazardous tasks. However, relying heavily on automation also brings its own set of challenges, such as job displacement and the need for skilled personnel to maintain and oversee these sophisticated systems.
"Innovation in battery technology is not just about performance; it's also about meeting the demands for sustainability and efficiency in manufacturing."
"Innovation in battery technology is not just about performance; it's also about meeting the demands for sustainability and efficiency in manufacturing."
Economic Implications of EV Battery Production
The production of electric vehicle (EV) batteries does not merely influence the automotive sector; it reverberates throughout the global economy. As the world shifts towards sustainable energy, understanding the economic implications of EV battery production becomes paramount. This sector encompasses job creation, investment opportunities, and the ever-important supply and demand dynamics that shape both local and international markets. With governments and industries striving for carbon neutrality, the pivot to EVs may also unlock avenues for innovation and growth.
Market Trends and Opportunities
In recent years, as electric vehicles have grown in popularity, a wave of market trends has emerged. The burgeoning demand for EVs is generating attractive opportunities across various segments:
- Investors are pouring capital into battery technologies, leading to a surge in startups focused on enhancing battery efficiency, capacity, and reducing costs. This influx contributes to an innovative ecosystem, promoting research and development.
- Supply chain diversification is becoming necessary, as manufacturers look to mitigate risks associated with reliance on specific raw materials, such as lithium and cobalt. Alternative sourcing and recycling of these materials are being explored, potentially leading to new markets and economic subsets.
- Government incentives play a critical role, with many nations offering subsidies and grants to encourage the production and adoption of EVs. These incentives not only boost consumer interest but also fuel investment in manufacturing capacities and technologies.
"As the transition to electric vehicles accelerates, the battery industry is blossoming into a key economic player worldwide."
"As the transition to electric vehicles accelerates, the battery industry is blossoming into a key economic player worldwide."
However, it’s not merely about profits and markets. Sustainability has become a crucial factor, driving public sentiment and consumer behavior. Stakeholders must acknowledge and capitalize on the shift in consciousness towards eco-friendliness, which could result in increased demand for EVs and their batteries.
Challenges Facing the Industry
While the economic prospects for EV battery production are promising, several challenges loom large. Understanding these obstacles is essential for stakeholders wishing to navigate the landscape successfully:
- Resource scarcity poses significant challenges. The demand for critical materials such as lithium, nickel, and cobalt may outpace supply, leading to price volatility. If the supply chain cannot cope with demand, long-term scaling could be adversely affected.
- Technological hurdles are also present. The quest for higher energy densities and faster-charging methods is ongoing. However, significant investments in research are needed to bear fruit, and that requires stable funding and skilled labor.
- Regulatory constraints add another layer of complexity. As regulations evolve to enhance safety protocols and environmental sustainability, manufacturers must stay agile, adapting to increasing compliance costs and operational shifts.
- Market competition is fierce and will only get tougher. With established giants and emerging players vying for dominance, companies must differentiate themselves, possibly through innovation, branding, or operational efficiencies.