Comprehensive Guide to Diamond-Like Carbon Coatings
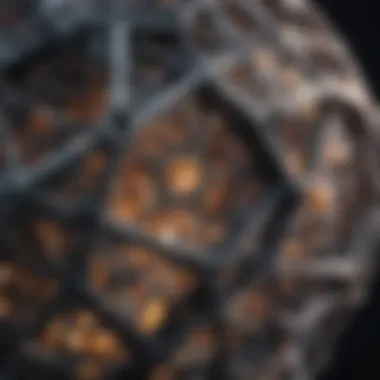
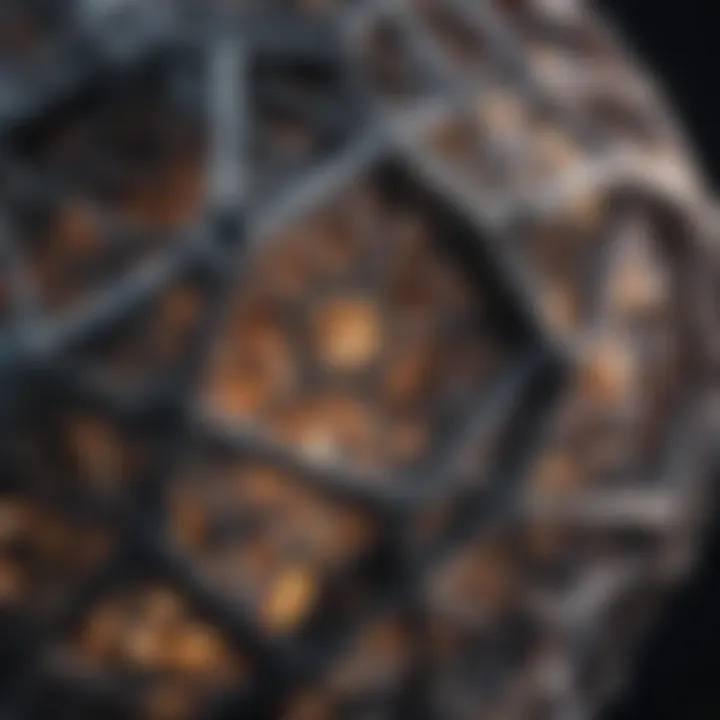
Intro
The diamond-like carbon (DLC) coating process has garnered a significant amount of attention in recent years, not least because of its remarkable properties that can be applied across a multitude of industries. This section looks to set the stage for a deep dive into the complexities associated with the production, application, and future of DLC coatings.
DLC is prized for its superior hardness, low friction, and excellent resistance to wear. What’s more, it has a high degree of biocompatibility, which makes it useful in medical applications. This overview aims to clarify the basic concepts and scientific principles involved in the DLC coating process, as well as the ongoing research trends shaping its evolution.
Key Concepts
Definition of the Main Idea
At its core, diamond-like carbon refers to a class of amorphous carbon material that exhibits properties akin to those of diamonds. This includes a hard surface, thermal stability, and electrical insulating characteristics, making it a versatile choice for various applications. DLC coatings are predominantly applied to enhance durability and performance of components in harsh environments.
Most commonly, DLC is found in automotive, aerospace, and medical industries. The coatings can be applied to a variety of substrates, such as metals, ceramics, and polymers, enabling a wide array of applications from engine components to surgical instruments.
Overview of Scientific Principles
DLC coatings are primarily produced through chemical vapor deposition (CVD) or physical vapor deposition (PVD) methods. Both processes allow for the controlled deposition of carbon atoms onto a substrate, forming a thin film that boasts remarkable properties. Here’s a concise breakdown of the two:
- Chemical Vapor Deposition (CVD): This method involves the chemical transformation of gaseous precursors into solid materials on the substrate surface. It provides superior coating uniformity and can be conducted at low temperatures.
- Physical Vapor Deposition (PVD): Unlike CVD, PVD utilizes physical processes to remove material from a solid source and transport it in vapor form to the substrate. This method leads to excellent adhesion and a variety of coating thicknesses.
The resulting DLC films can be categorized based on their sp2 and sp3 carbon bonding, which ultimately influences their hardness and wear resistance. The intricacies of these carbon bond formations are what give DLC its diamond-like characteristics, aligning perfectly with the need for materials that demand strength without added weight.
Current Research Trends
As technology advances, the quest for improved DLC coatings is ceaseless. Recent studies and breakthroughs are reshaping the understanding of how to enhance the performance and broaden the application scope of DLC components.
Recent Studies and Findings
Recent research has focused on optimizing the deposition processes to enhance the quality of DLC films. Some notable findings include:
- Nanostructured DLC: This approach seeks to improve mechanical properties by controlling the microstructure of the coating.
- Biocompatibility Improvements: Research into enhancing the biocompatibility of DLC coatings for medical applications has gained traction, making it more favorable for use in implants.
Significant Breakthroughs in the Field
Significant breakthroughs are being recorded in the area of multi-layer coatings that combine DLC with other materials to achieve desirable attributes. For instance, layering DLC with titanium nitride can yield a composite that has exceptional toughness while retaining the low friction characteristics of pure DLC.
"Emerging technologies in DLC coating show potential for advancing applications where performance under extreme conditions is paramount."
"Emerging technologies in DLC coating show potential for advancing applications where performance under extreme conditions is paramount."
Such advancements illustrate the adaptability of DLC coatings and drive enthusiasm among researchers and industry professionals alike.
Intro to Diamond-Like Carbon Coating
Understanding diamond-like carbon (DLC) coatings is essential in numerous high-tech industries today. DLC coatings play a crucial role in enhancing the performance and lifespan of various materials by imparting unique properties such as hardness, low friction, and resistance to wear. Their importance cannot be overstated, especially when considering the demands of modern applications where durability and efficiency are paramount.
Some specific elements worth noting include:
- Versatility: DLC coatings can be applied to a range of substrates, including metals, plastics, and ceramics, making them suitable for numerous applications.
- Protection: They offer an effective barrier against environmental factors that can lead to corrosion or degradation of materials.
- Performance Enhancement: Many industries utilize DLC coatings to improve the functioning of critical components, where even a slight enhancement can lead to significant improvements in systems performance.
By diving into the details of DLC coatings, this article explores various aspects including their definition, historical context, applications across different fields, and the methodologies used in their development and application.
The Importance of Coatings
Diamond-like carbon (DLC) coatings play a significant role in various industries due to their unique properties. By forming a thin film that combines the hardness of diamond with the versatility of carbon, these coatings are designed to enhance the performance and longevity of components across multiple applications. The significance of DLC coatings goes beyond surface protection; they offer a range of benefits that can dictate the success of technological advancements and industrial efficiencies.
Applications in Various Industries
Each industry utilizes DLC coatings to address specific challenges and enhance the effectiveness of its products.
Automotive Industry
In the automotive sector, DLC coatings are extensively applied to components such as engine parts, pistons, and gears. The key characteristic of these coatings lies in their robust hardness and wear resistance. As vehicles face increasing demands for fuel efficiency and reduced emissions, the ability to withstand extreme conditions becomes critical.
DLC coatings provide a means to lower friction between moving parts, directly contributing to better fuel economy. Moreover, their lightweight nature means they do not add significant weight to components, an important consideration in automotive design. The downside here can be their cost, as producing high-quality DLC coatings may require sophisticated technology and a corresponding investment.
Aerospace Applications
The aerospace sector relies on DLC coatings for protecting components that operate under harsh conditions, including high temperatures and diverse atmospheric stimuli. The unique feature of DLC in this context involves its ability to minimize wear and tear on critical parts like valves and turbines. Its lightweight properties combined with tenacity mean that rather than letting heavy coatings reduce overall aircraft efficiency, DLC can provide performance while preserving weight limits.
One must note that the rigorous testing and certification processes required in aerospace applications can complicate the adoption of DLC coatings, but their benefits often outweigh these hurdles. This balance between performance and lightweight requirements makes DLC coatings a compelling choice in the industry, often seen as indispensable.
Biomedical Uses
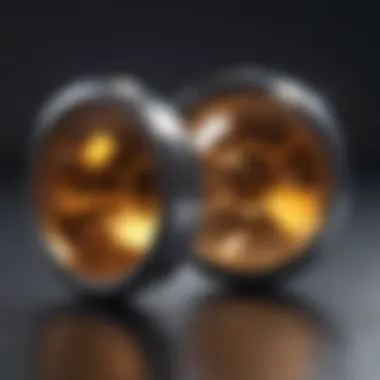
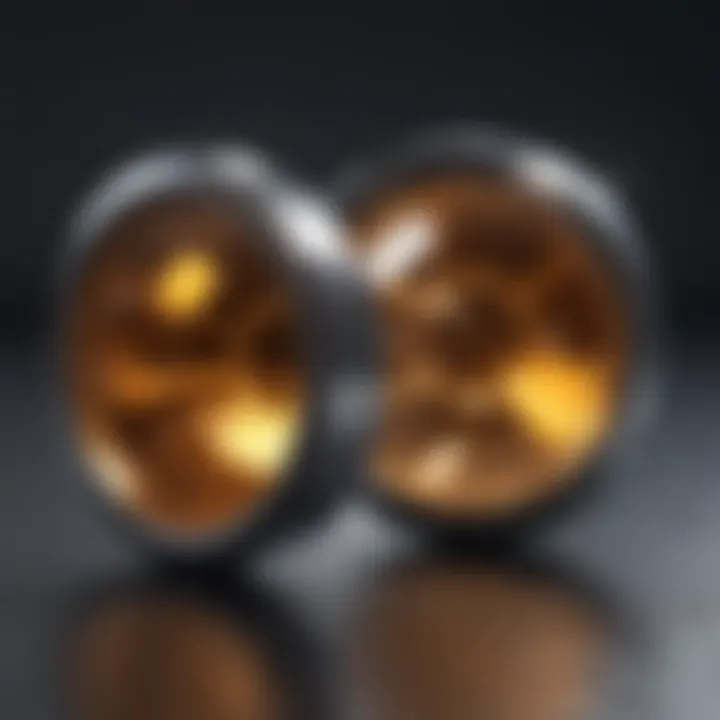
In the biomedical field, the application of DLC coatings has opened new avenues for medical devices and implants. The inherent biocompatibility of DLC is pivotal, as it is less likely to adversely interact with human tissues compared to other coatings. This allows for a broader range of applications, from surgical tools to implants that require rigorous longevity and reliability.
A key characteristic of the biomedical use of DLC is its ability to reduce blood clotting, offering immense advantages for devices in vascular applications. However, achieving the required surface smoothness can be challenging, and this may affect the efficacy of the application. Still, the reduction in friction and bio-fouling presents a strong argument for selecting DLC coatings in medical technologies.
Advantages Over Traditional Coatings
DLC coatings distinguish themselves by offering a myriad of advantages over traditional coatings, making them highly sought after in many applications.
Enhanced Durability
One of the standout features of DLC coatings is their enhanced durability. The significant hardness level means that components can withstand abrasive wear better than those coated with traditional methods. This durability extends the lifecycle of parts, which in turn, reduces costs for end-users in maintenance and replacement.
However, while most would view this as a clear advantage, it is paramount to manage the expectations that come with it. Depending on the base material, the application process can introduce stress points, potentially leading to differences in performance under specific conditions.
Low Friction Properties
DLC coatings exhibit low friction properties, drastically minimizing the wear that typically occurs between moving parts. This low friction characteristic not only improves efficiency but also contributes to thermal management within machinery. By reducing heat generation, DLC coatings help maintain operational stability, a quality highly regarded in high-performance engineering solutions.
Of course, these low friction numbers may come with a trade-off; if not applied properly, the coatings could wear unevenly under certain operational stresses resulting in unexpected service issues.
Corrosion Resistance
Another prominent advantage of DLC coatings is their corrosion resistance. In environments prone to oxidation and other corrosive factors, DLC coatings can shield underlying materials, ensuring longevity and sustainability of components. This property is particularly essential in industries like aerospace and automotive, where components face both chemical and mechanical degradation.
That said, while DLC can offer good protection against many forms of corrosion, it is always advisable to consider the environmental specifics. Not all configurations guarantee absolute resistance, and depending on exposure to chemicals or conditions, diligence in selection and testing is imperative.
The integration of diamond-like carbon coatings across various industries signifies a leap towards more resilient, efficient, and innovative technological solutions.
The integration of diamond-like carbon coatings across various industries signifies a leap towards more resilient, efficient, and innovative technological solutions.
Coating Processes
The processes involved in applying diamond-like carbon (DLC) coatings are pivotal for the performance and durability of various materials. Understanding these processes helps elucidate the techniques used to enhance surface properties, which in turn, allow for broader applications across different industries. By dissecting the main coating methods like Physical Vapor Deposition (PVD), Chemical Vapor Deposition (CVD), and Laser Ablation Techniques, we can appreciate their respective roles and advantages in creating effective DLC coatings.
Physical Vapor Deposition (PVD)
Process Overview
Physical Vapor Deposition is one of the cornerstone processes for applying DLC coatings. This method vaporizes material to allow it to condense on the substrate, forming a thin film. A key characteristic of PVD is its ability to produce a highly pure and dense coating, which is essential given that impurities can drastically alter the properties of the coating. This process is widely regarded as effective due to its straightforward nature and ability to prepare surfaces for added coatings under a controlled vacuum environment. Moreover, PVD is featured by the lack of significant thermal stress on substrates, which is crucial when working with materials that are sensitive to heat.
Advantages and Disadvantages
Focusing on Advantages, one can't overlook the remarkable adhesion that coatings deposited by PVD generally exhibit. This leads to a substantial increase in their durability and wear resistance. Also, PVD works well with high-temperature applications, making it a popular choice in sectors like aerospace and automotive.
Conversely, its Disadvantages cannot be ignored. The initial equipment investment can be substantial, and the process may be less efficient for larger surfaces compared to chemical methods. Additionally, achieving uniform coatings on complex geometries can present complexities.
Chemical Vapor Deposition ()
Types of
Chemical Vapor Deposition involves the chemical reactions in a gaseous phase, bringing the carbon atoms to form a bonded layer on the substrate. There are several types of CVD, including Plasma-Enhanced CVD and Hot-Wall CVD, each tailored for different environments and requirements. The main advantage here is versatility; not only can one deposit a thick film, but tuning the deposition conditions can yield films with varying properties. CVD's unique approach allows for a more uniform coating on intricate parts compared to PVD.
Material Considerations
When we discuss Material Considerations, it is crucial to think about the compatibility of the substrate material with the deposition process. Not every substrate will respond optimally to all types of CVD processes. Some materials may require pre-treatments or specially designed gaseous mixtures to ensure effective coating adherence. Understanding these factors is essential for maximizing the benefits of DLC coatings. Factors such as thermal expansion compatibility and reactivity can dictate whether the process will be successful or lead to defects like delamination.
Laser Ablation Techniques
Laser Ablation Techniques are emerging as a novel approach to DLC coating. This method involves using focused laser beams to either directly deposit DLC or to modify existing coatings. The unique feature of laser ablation is that it allows for spatial control over the deposition process, which can be invaluable for applications requiring precision.
With the increased precision and reduced risk of contaminating the coated material, laser ablation could represent a significant leap forward in DLC technology. This method further affords the flexibility to tune the properties of the coatings through control over the process parameters, making it a promising choice for future developments.
"The evolution of DLC coating processes not only enhances material properties but also expands the application frontiers in advanced technologies."
"The evolution of DLC coating processes not only enhances material properties but also expands the application frontiers in advanced technologies."
Materials Used in Coatings
Understanding the materials used in diamond-like carbon coatings is crucial, as these choices directly influence the coating's performance and applications. The selection of materials is not merely a technical detail; it significantly determines the effectiveness of the coatings in various environments. Let’s dive into this intricate relationship between materials and DLC coatings.
Carbon Sources
Carbon is the backbone of DLC coatings, and the choice of carbon source is paramount. Various sources yield different characteristics in the final coating. Common sources include graphite, hydrocarbons, and even carbon dioxide under specific conditions.

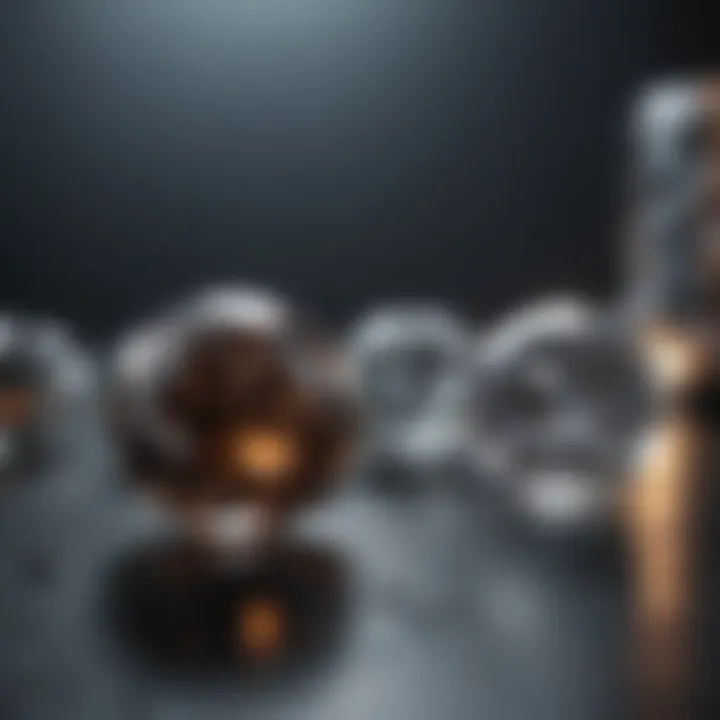
Key Characteristics of Carbon Sources:
- Purity: The quality and purity of carbon sources can impact the resulting coating's hardness.
- Sustainability: The shift towards greener technologies has made bio-derived carbons increasingly popular. Their lower environmental footprint aligns with current sustainability efforts.
Using hydrocarbons, for instance, may lead to coatings with a smoother finish and finer structure compared to other sources. However, one downside is that improper management during the deposition can result in a buildup of stress within the coating, leading it to crack under pressure. Therefore, selecting the right carbon source not only affects performance but also dictates long-term durability.
Substrate Compatibility
Compatibility of the substrate with DLC coatings is essential for achieving optimized performance. A mismatch can lead to poor adhesion and premature coating failure. Various materials such as metals, ceramics, and plastics come into play here; each presents its unique attributes and challenges.
Metals
When it comes to metal substrates, they typically exhibit high thermal and electrical conductivities, which are beneficial in various applications. For instance, steel and aluminum alloys are commonly chosen due to their strength and lightweight nature.
Key Characteristic of Metals:
- Durability: Metals can withstand substantial mechanical stress, complementing the hardness of DLC coatings.
A unique feature of metals is their ability to be machined readily; this ensures that coated parts can maintain their precise shapes. However, during high-temperature applications, such as in aerospace components, metals must undergo additional surface treatments to prevent degradation over time.
Ceramics
Ceramics are gaining traction as substrate materials for DLC coatings due to their excellent thermal stability and wear resistance. Alumina and zirconia are common choices that offer exceptional hardness and are often used in high-performance applications.
Key Characteristic of Ceramics:
- Temperature Resistance: Ceramics can operate efficiently at elevated temperatures, making them ideal for components in harsh environments.
A significant advantage of ceramics is their inherent chemical inertness, which makes them less prone to corrosion. However, they might be relatively brittle under certain conditions, posing a risk of chipping or breaking, especially during mechanical stress.
Plastics
Plastics, though not the first choice for many, are becoming increasingly relevant in DLC coatings. Polycarbonate and nylon substrates are popular due to their lightweight nature and flexibility.
Key Characteristic of Plastics:
- Weight Reduction: Utilizing plastics can significantly lower the overall weight of parts, especially in automotive settings where efficiency matters.
The unique feature here is that plastics can be molded into complex shapes, allowing for innovative designs that wouldn’t be feasible with metals or ceramics. However, they may not offer the same level of hardness or temperature resistance as the more traditional choices, which could limit their use cases.
In summary, selecting the appropriate materials for DLC coatings—carbon sources and substrates alike—factors greatly into the performance and application of the coatings. The right fit can enhance durability, reduce friction, and boost overall effectiveness in various settings. As the industry evolves, keeping abreast of advancements concerning material science will be imperative.
Characterization of Coatings
Characterizing diamond-like carbon (DLC) coatings is key to understanding their performance and application across various industries. Proper characterization ensures that the coatings meet predetermined specifications and behave as expected in their operational environments. The examination of mechanical properties is particularly prominent because these attributes directly correlate with the durability and functionality of DLC coatings. Furthermore, surface profile analysis provides a comprehensive view of the coating's surface morphology, which is vital for optimizing performance in diverse applications.
Mechanical Properties Testing
Mechanical properties testing forms the backbone of DLC coating characterization. This evaluation often includes hardness, elasticity, wear resistance, and other properties that critically influence the performance of coated components. Researchers and engineers rely heavily on these tests to ensure that DLC coatings not only meet industry standards but also excel in real-world conditions.
- Hardness Testing: This is one of the most significant factors determining a coating's ability to withstand wear. Techniques like microhardness tests help gauge the indention resistance of the coating.
- Adhesion Testing: The strength of the bond between the DLC coating and the substrate is essential for longevity and efficacy. Tests such as scratch tests or tape tests reveal a lot about the adhesion qualities.
Surface Profile Analysis Techniques
Understanding the surface topography of DLC coatings is crucial since it directly impacts their behavior in a practical setting. Surface profile analysis techniques help researchers visualize and quantify these critical characteristics.
Atomic Force Microscopy
Atomic Force Microscopy (AFM) is an atomic-scale imaging process that allows for the visualization of the surface topography of DLC coatings with unmatched precision. One standout characteristic of AFM is its ability to provide three-dimensional profiles of surfaces at the nanoscale, which aids in examining roughness and texture intricacies. This technique is extremely beneficial for analyzing DLC coatings, as it reveals the fine details that can influence performance—like porosity or surface roughness.
One unique feature of AFM is its versatility; it can also measure mechanical properties, like stiffness, alongside topographical data. However, a consideration is that AFM can be time-consuming, and its resolution may vary depending on the substrate. Still, for those deep into surface analysis, AFM offers vital insights that are hard to achieve through other means.
Scanning Electron Microscopy
Scanning Electron Microscopy (SEM) serves as another powerful tool, enabling researchers to observe the morphology of DLC coatings on a micro or nanoscale level. One key characteristic of SEM is its ability to generate high-resolution images that reveal the fine structure of the coatings. This provides insight into defects or variations that may affect the coating's overall performance—something particularly significant for industries requiring utmost durability.
A unique aspect of SEM is that it can provide elemental analysis through techniques like Energy Dispersive X-Ray Spectroscopy (EDX), which can further complement the characterization process. Conversely, while SEM is excellent for visualizing surface structures, it does have limitations such as sample preparation requirements and potential for coating damage under high-energy electron beams.
"Through both AFM and SEM, researchers gain essential insights that propel the advancement of diamond-like carbon technology forward, helping refine existing methods and discover new applications."
"Through both AFM and SEM, researchers gain essential insights that propel the advancement of diamond-like carbon technology forward, helping refine existing methods and discover new applications."
Challenges in Coating Technology
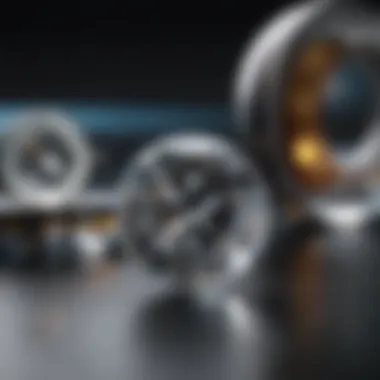
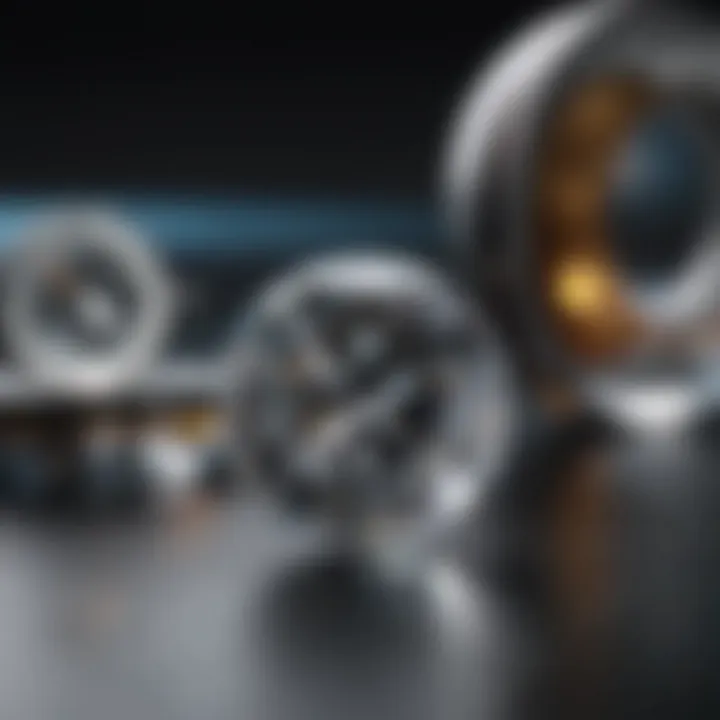
Understanding the challenges in diamond-like carbon (DLC) coating technology is pivotal, as it sheds light on both current limitations and areas ripe for innovation. While the unique properties of DLC coatings make them highly sought after in various industries, several obstacles hinder their widespread adoption and performance. Addressing these challenges can pave the way for more advanced applications and improvements in the technology.
Processing Limitations
The DLC coating process, whether via physical vapor deposition (PVD) or chemical vapor deposition (CVD), comes with its own set of processing hurdles. One notable limitation is the thickness of the DLC layer. A thicker coating can lead to issues like poor adhesion, especially on substrates with varying thermal expansion properties. This can result in chippings or peeling over time, significantly impacting the longevity of coated parts.
Moreover, the uniformity of the coating can be inconsistent, particularly on complex geometries. As the deposition relies on line-of-sight methods, shadowing effects can create areas where the coating is either too thin or entirely absent. Such variations can compromise the protective qualities and functionality of the coating.
"The intricacies of process control play a significant role in the effectiveness of DLC applications; even minor deviations can lead to major setbacks."
"The intricacies of process control play a significant role in the effectiveness of DLC applications; even minor deviations can lead to major setbacks."
This highlights the necessity for ongoing research and development to refine these processes. New methods aimed at improving uniformity and adhesion are crucial for maximizing the reliability of DLC applications in demanding environments.
Cost Factors
When examining DLC coating technology, cost stands out as a crucial factor affecting its adoption. The initial setup for PVD and CVD processes can be substantial, involving sophisticated equipment and materials. This can often deter smaller companies from investing in DLC solutions, favoring more economical alternatives.
Furthermore, the operational costs associated with these processes can also add up. For instance, the energy consumption during coating can be significant, particularly for facilities running at high volumes. In addition, maintaining a clean and controlled environment to prevent contamination during the coating process increases overall operational expenses.
Consequently, these cost elements can make DLC coatings less accessible for certain applications, particularly in industries where budget constraints are paramount.
Performance Under Extreme Conditions
DLC coatings are lauded for their durability and resistance to wear; however, when thrust into extreme conditions, such as high temperatures or complex chemical environments, their performance may falter. High temperatures can cause the DLC to lose its desirable properties or become brittle, undermining its effectiveness. This is a pressing concern in applications like aerospace, where components are often subjected to significant thermal stresses.
Additionally, while DLC is generally resistant to corrosion, certain chemicals can compromise its integrity. In environments with aggressive substances, the coating might degrade more rapidly than anticipated, leading to potential failures.
For this reason, it is imperative to conduct rigorous testing and analysis of DLC coatings under various extreme conditions to establish informed parameters for their application and ensure reliability.
In summary, while DLC technology presents exciting opportunities across numerous sectors, the challenges related to processing limitations, cost factors, and performance under extreme conditions need to be carefully navigated. Future advancements must focus on addressing these barriers to unlock the full potential of diamond-like carbon coatings.
Future Directions in Coating Research
As the technological landscape continues to evolve, so too does the diamond-like carbon (DLC) coating field, establishing itself as a crucial aspect for improving performance in various applications. Understanding future directions in DLC coating research is pivotal, given its potential to redefine the properties and functionalities of materials across multiple sectors. It serves as a springboard for innovations that can lead to improvements not just in the coatings themselves, but also in the longevity and efficiency of the tools and components they protect.
Investments in emerging techniques and materials are necessary to overcome the limitations seen in current DLC applications. Researchers and industries are increasingly looking at how integrating advanced technologies can enhance the coating process. The focus is on both improving existing methods and finding new pathways that allow DLC coatings to shine in more demanding environments.
The benefits of exploring future directions in this area are manifold. There’s the obvious advantage of creating coatings that withstand higher temperatures or resist wear better. Another consideration is the eco-friendliness of future DLC coating solutions. These developments bear a vital significance; they do not just ensure better performance, but also align with the demands for sustainable manufacturing practices.
Innovative Coating Techniques
In the realm of innovative coating techniques, researchers are exploring methods that can significantly change the way DLC coatings are applied. Among these, advanced sputtering methods, which harness magnetron technology, are garnering attention. This technique improves material utilization efficiency, a pressing concern in today’s manufacturing landscape. By minimizing waste during application, it not only lowers costs but also promotes sustainability.
Furthermore, plasma-enhanced chemical vapor deposition (PECVD) offers intriguing possibilities for tailoring the chemical structure of DLC coatings. Unlike traditional methods, PECVD tends to operate at lower temperatures, which is especially advantageous for sensitive substrates. This could potentially open doors to industries using materials that cannot handle extensive heat during processing.
Lastly, researchers are also delving into the use of nanotechnology. This involves embedding nanoparticles within the DLC coating to enhance its properties. For instance, adding nanocrystals could improve hardness and thermal stability, allowing for applications in sectors like aerospace and automotive.
Potential New Applications
As the future research progresses, potential new applications for DLC coatings are exciting. In the biomedical field, there’s promise for DLC coatings to serve as a base for implants and surgical tools. The non-toxic nature of DLC materials can lend themselves well to disrupt conventional forms of implant coatings, providing improved biocompatibility and durability, which is crucial in body environments.
Another area ripe for application is electronic devices. As consumer electronics trend towards miniaturization, friction and wear become enormous challenges. Here, DLC coatings can provide solutions by dramatically reducing wear on sensitive components. This can enhance product longevity and performance, meeting mounting consumer demands for durability in their devices.
Moreover, advancements in the energy sector could see DLC coatings being used in wind turbines or photovoltaic cells. The durability and light weight of DLC could help in making these technologies more efficient and reliable, which in part translates to enhanced energy output.
"The evolution of DLC coatings is not just about performance; it's about aligning with future market needs, emphasizing sustainability and efficiency."
"The evolution of DLC coatings is not just about performance; it's about aligning with future market needs, emphasizing sustainability and efficiency."
In summary, the future of diamond-like carbon coating research stands on the cusp of significant innovations, from groundbreaking techniques to new applications across various fields. Continuing this journey will not only bolster the capabilities of materials but also shape the trajectory of many industries that rely heavily on the strength, durability, and versatility offered by DLC coatings.
Closure
Wrapping up our exploration of diamond-like carbon (DLC) coatings, it's crucial to emphasize several key aspects of this multifaceted topic. First off, DLC coatings are not just an innovation; they're a game changer across multiple industries. Whether in the automotive realm, where enhanced friction properties lead to greater efficiency, or the aerospace sector, with its demands for lightweight but strong materials, the applications are vast and significant.
Recap of Key Points
- Definition and Composition: Diamond-like carbon coatings are primarily composed of carbon atoms structured in a way that mimics the hardness and characteristics of diamonds. This unique structure provides remarkable benefits in durability and performance.
- Process Overview: The techniques used, such as Physical Vapor Deposition (PVD) and Chemical Vapor Deposition (CVD), provide various ways to apply these coatings effectively. Each method has its pros and cons, influencing factors like coating thickness and uniformity.
- Applications: The uses range extensively from automobile parts to medical instruments. Each industry benefits uniquely from DLC's properties, minimizing wear and tear while extending the lifespan of components.
- Challenges: Like any technology, DLC coatings face hurdles, including limitations in processing conditions and cost concerns. Addressing these challenges is vital for the continued adoption of this technology.
- Future Directions: The future looks promising with ongoing research into innovative techniques and potential new applications that could change industries even further, showcasing DLC as a technology worth investing in.
"Continued exploration of DLC coatings will only enhance our technological capabilities, elevating standards across the board."
"Continued exploration of DLC coatings will only enhance our technological capabilities, elevating standards across the board."
The Significance of Continued Exploration
The importance of ongoing research in the field of DLC coatings cannot be overstated. As we delve deeper into the science behind these coatings, we uncover new possibilities that could revolutionize their applications. For instance, improving the performance under extreme conditions opens doors for industries like space exploration, where equipment must withstand harsh environments.
Moreover, advancements in coating techniques enhance the efficiency and cost-effectiveness of DLCs, making them more accessible to various sectors. Research could lead to the discovery of new carbon sources or compounds that boost the coating's overall performance, pushing boundaries in not just durability but in versatility.
As industries continually evolve, having cutting-edge tech like DLC coatings at their fingertips can be the difference between staying ahead or falling behind. The journey to mastering this coating is ongoing, and those who invest the effort now may very well shape the future of manufacturing and technology as a whole.