An In-Depth Exploration of AL6061 Aluminum Alloy
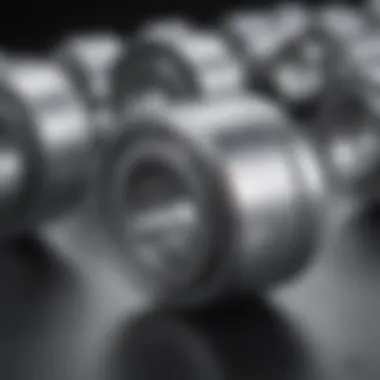
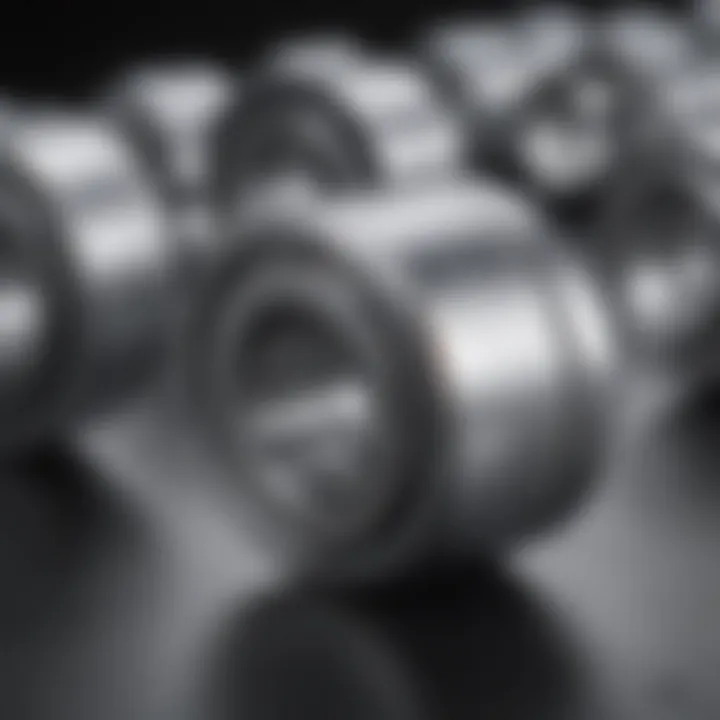
Intro
AL6061 is a widely recognized aluminum alloy that finds application in a variety of fields due to its favorable properties. This alloy is notable for its strength, workability, and resistance to corrosion. Understanding its composition is essential, as it provides insight into why AL6061 is selected for so many engineering projects. This article seeks to explore the foundational aspects of AL6061, offering the reader a clear view of its characteristics and applications.
Key Concepts
Definition of the Main Idea
AL6061 aluminum alloy is primarily composed of aluminum, magnesium, and silicon. The alloy is categorized as a heat-treatable aluminum alloy, allowing it to achieve high strength levels through aging treatments. Its versatility allows it to be used in various applications such as structural components, automotive parts, and even aerospace designs.
Overview of Scientific Principles
A crucial feature of AL6061 is its mechanical properties. These properties include yield strength, tensile strength, and elongation, which define how the material responds to forces and stresses. Generally, AL6061 possesses a yield strength of about 40,000 psi, coupled with a tensile strength around 45,000 psi, making it a reliable choice for structures requiring significant load-bearing capacity.
Another important aspect is the alloy's excellent corrosion resistance, which is primarily due to its aluminum content. This resistance is vital in ensuring the longevity of components in harsh environments. Additionally, AL6061 can be easily welded and machined, further expanding its usability in manufacturing processes.
"AL6061's blend of strength and workability makes it a favorite among engineers. The combination of properties opens numerous applications across industries."
"AL6061's blend of strength and workability makes it a favorite among engineers. The combination of properties opens numerous applications across industries."
Current Research Trends
Recent Studies and Findings
Current research on AL6061 involves exploring its performance under various conditions. Scientists are investigating its behavior when subjected to different heat treatments, as well as its performance in hybrid materials. Some studies have documented the effects of alloying elements on the mechanical properties of AL6061, indicating how alterations in composition can enhance its performance.
Significant Breakthroughs in the Field
Breakthroughs in the field of AL6061 alloys often involve modifications to improve its characteristics. For instance, recent findings highlight the development of AL6061 variants with improved fatigue resistance, which extends their lifespan in dynamic applications. These advances reflect the ongoing efforts to refine existing materials and expand their applications.
End
AL6061 aluminum alloy embodies a balance of multiple properties that make it indispensable in various industrial fields. Its strong mechanical characteristics and resistance to corrosion are just two reasons why it remains a material of choice for engineers and manufacturers. Additionally, with ongoing research aimed at optimizing its performance, the future of AL6061 looks promising.
This exploration offers a snapshot into the various aspects of AL6061, encouraging further investigation into its vast potential in engineering applications.
Prologue to AL6061 Aluminum Alloy
The AL6061 aluminum alloy holds significant importance in the engineering and manufacturing sectors. This alloy is valued for its strong combination of properties that include excellent corrosion resistance, good machinability, and weldability. These attributes make AL6061 suitable for a variety of applications ranging from structural components to intricate engineering parts.
As industries evolve and demands for lightweight yet sturdy materials increase, AL6061 becomes a focal point for engineers and designers looking to optimize their products. Understanding its characteristics not only assists professionals in making informed decisions but also sets the foundation for innovations in material science.
Background and Overview
AL6061 belongs to the aluminum-silicon-magnesium family of alloys, possessing a unique chemical composition that imparts distinct characteristics. The alloy is known for its versatility and is commonly produced through extrusion methods, which allow for various shapes and sizes. The primary alloying elements, such as magnesium and silicon, contribute to its mechanical properties and overall durability.
Historically, AL6061 was developed in the mid-20th century and has since gained traction in numerous sectors, primarily because of its favorable performance under diverse environmental conditions. The material is often used in the production of aircraft components, automotive parts, and various structural applications due to its specific advantages over other materials.
Importance of Aluminum Alloys
Aluminum alloys, including AL6061, are essential in modern industry for several reasons:
- Lightweight Nature: Aluminum's low density allows for the creation of lighter products without compromising strength.
- Corrosion Resistance: These alloys exhibit excellent resistance to corrosion, making them suitable for outdoor and marine environments.
- Recyclability: Aluminum is highly recyclable, which aligns with the global push towards sustainability in manufacturing.
- Versatile Applications: The broad range of mechanical properties of aluminum alloys allows for their use in a wide spectrum of applications, from aerospace to consumer electronics.
"The versatility and strength of aluminum alloys like AL6061 make them a cornerstone of modern engineering."
"The versatility and strength of aluminum alloys like AL6061 make them a cornerstone of modern engineering."
Thus, the focus on AL6061 is justified due to its comprehensive utility across various fields. Its significance extends beyond mere functionality, hinting at a future where lightweight and durable materials become standard in advanced manufacturing.
Chemical Composition of AL6061
Understanding the chemical composition of AL6061 aluminum alloy is crucial for appreciating its mechanical properties and applications. The specific elements utilized in the alloy govern its strength, corrosion resistance, and overall performance. This section delves into the primary alloying elements and smaller constituent elements that define AL6061, offering insights into their respective roles and importance.
Primary Alloying Elements
The primary alloying elements in AL6061 are silicon and magnesium. Silicon content typically ranges from 0.4% to 0.8%, while magnesium makes up about 0.8% to 1.2%. This combination results in a significant enhancement in strength, thereby allowing the material to be applied in various industries.
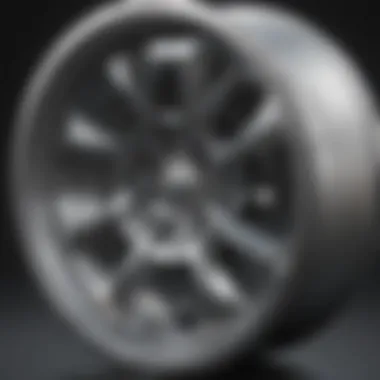
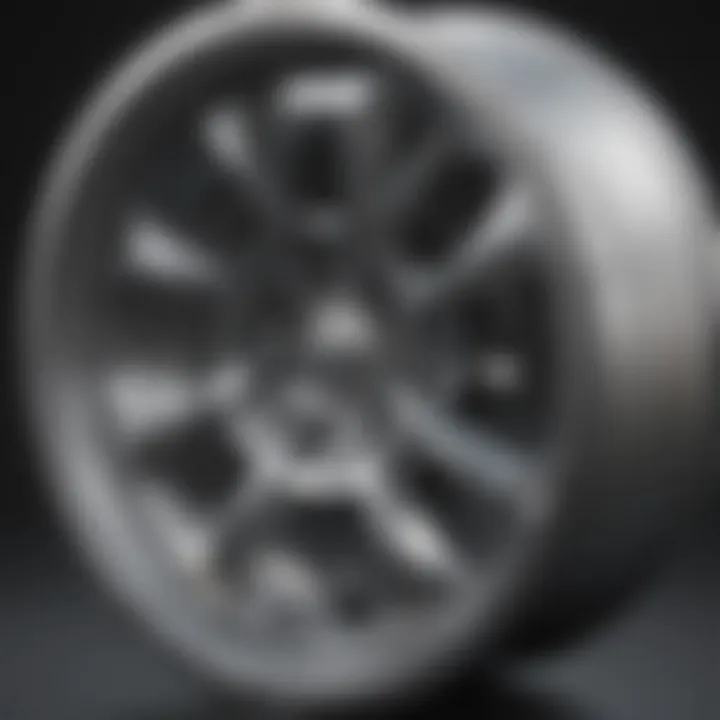
- Silicon: This element enhances castability and reduces the melting temperature. Its presence enhances fluidity during the casting process. Higher silicon levels can lead to a more brittle structure, so it's crucial to manage its concentration carefully.
- Magnesium: This contributes to both strength and corrosion resistance. Magnesium forms a solid solution with aluminum, which is essential for improving the yield strength of the final product. Notably, AL6061 gains substantial strength when subjected to heat treatment.
The proper balance of these elements creates an alloy that exhibits a robust combination of strength and workability, making it suitable for applications requiring structural integrity and durability.
Smaller Constituent Elements
Apart from the primary alloying elements, AL6061 contains smaller constituent elements, including copper, chromium, and manganese. Each of these elements adds specific characteristics to the alloy:
- Copper: Present in small quantities, copper improves overall strength and enhances the toughness of the alloy. The typical concentration of copper is around 0.15% to 0.4%.
- Chromium: This contributes to corrosion resistance while also acting as a grain refiner. A small addition, usually around 0.04% to 0.35%, is sufficient to optimize these properties without compromising ductility.
- Manganese: Although present at levels usually between 0.15% and 0.8%, manganese is vital for improving resistance to stress corrosion cracking. This ensures that parts made from AL6061 endure long-term service without degrading.
- Zinc and Iron: Traces of zinc and iron can also be found, though in limited amounts as they can negatively affect corrosion resistance if present in excess.
"The performance capabilities of AL6061 are directly linked to its chemical composition, making it essential for engineers to understand this relationship."
"The performance capabilities of AL6061 are directly linked to its chemical composition, making it essential for engineers to understand this relationship."
This comprehensive analysis of AL6061's chemical composition underscores its importance in manufacturing processes, and provides a strong foundation for exploring its mechanical properties in the next section.
Mechanical Properties
Understanding the mechanical properties of AL6061 aluminum alloy is essential for its application in various industries. Mechanical properties define how a material reacts under different types of forces and conditions. They are indicative of the performance and capabilities of the material in real-world environments. For AL6061, the primary mechanical properties include tensile strength, yield strength, fatigue resistance, and corrosion resistance. Each aspect plays a critical role in determining suitability for specific tasks and challenges in manufacturing and engineering.
Tensile Strength and Yield Strength
Tensile strength is a vital characteristic for AL6061, as it measures the alloy's ability to withstand pulling or stretching forces without failing. This strength is indicative of how the alloy performs under load, which is crucial in applications where structural integrity is paramount. AL6061 typically exhibits a tensile strength of around 310 MPa (megapascals), making it suitable for use in numerous fields, including automotive and aerospace.
Yield strength, on the other hand, is the point where the material begins to deform permanently. For AL6061, the yield strength is approximately 276 MPa. This property determines how much force can be applied before the material distorts, which is essential in applications requiring precision and accuracy. A higher yield strength contributes to better performance in load-bearing scenarios, especially in weight-sensitive designs.
Fatigue Resistance
Fatigue resistance is another crucial mechanical property. It refers to the material's ability to withstand repeated loading and unloading cycles without cracking or failing. AL6061 aluminum alloy demonstrates good fatigue strength, allowing it to be used in applications subjected to fluctuating loads. This characteristic is critical in fields such as automotive engineering, where components undergo numerous cycles of stress.
The fatigue life of AL6061 is significant for performance in dynamic applications, highlighting the need for careful design considerations in structural components.
The fatigue life of AL6061 is significant for performance in dynamic applications, highlighting the need for careful design considerations in structural components.
Across various applications, manufacturers often rely on fatigue resistance to ensure longevity and performance reliability. Engineers must consider this property when designing components that will face cyclic loading, as it directly affects safety and durability.
Corrosion Resistance
Corrosion resistance is vital for any alloy used outdoors or in hostile environments. AL6061 provides moderate corrosion resistance, thanks in part to the presence of silicon and magnesium in its composition. This resistance can be enhanced by various surface treatments and coating methods. Given its ability to resist corrosion, AL6061 is commonly used in marine applications and other situations where exposure to moisture or chemicals is a concern.
Protecting an AL6061 component from corrosion not only increases its lifespan but also maintains its structural integrity over time. Applications in coastal environments or automotive sectors, where exposure to brine or chemicals is expected, benefit from this property. Therefore, understanding the corrosion resistance of AL6061 is critical for any engineering project involving this alloy.
Manufacturing Processes Involving AL6061
Understanding the manufacturing processes involving AL6061 aluminum alloy is essential for both engineers and manufacturers. The production and fabrication methods play a crucial role in determining the alloy's final properties. It is important to choose appropriate techniques to fully capitalize on AL6061's characteristics, such as its strength-to-weight ratio and corrosion resistance. This section will focus on three main manufacturing techniques: casting, extrusion, and welding. Each method has unique benefits, limitations, and applications.
Casting Techniques
Casting processes are often the initial step in shaping AL6061 into a usable form. These techniques allow for complex geometries that might not be possible through other methods. There are different casting methods, such as sand casting and die casting, each with its distinct advantages.
- Sand Casting: This method is cost-effective for producing large pieces. It uses sand molds to form the desired shape. The advantage of sand casting lies in its ability to accommodate large and heavy components that require intricate details.
- Die Casting: Unlike sand casting, this technique employs reusable metal molds. It is best suited for high-volume production. Die-cast parts maintain high dimensional accuracy and improved surface finish. However, the initial cost of die molds can be significant.
Both methods enhance the mechanical properties of AL6061, providing strong and durable components for further manufacturing.
"The casting process allows for the versatility of designs while optimizing the mechanical properties of materials."
"The casting process allows for the versatility of designs while optimizing the mechanical properties of materials."
Extrusion Methods
Extrusion is another critical manufacturing process for AL6061. This method is particularly advantageous because it allows for the production of long sections with consistent cross-sections. Various extrusion techniques exist, including direct extrusion and indirect extrusion.
- Direct Extrusion: This method pushes the aluminum through a die, forming the desired shape. It is efficient and suitable for creating complex profiles with minimal waste.
- Indirect Extrusion: In this technique, the die moves towards the billet. Indirect extrusion generally produces a smoother surface finish and minimizes friction between the material and the die.
The extrusion process enhances the alloy's strength through work hardening, making it suitable for structural applications in automotive and aerospace industries.
Welding and Joining Processes

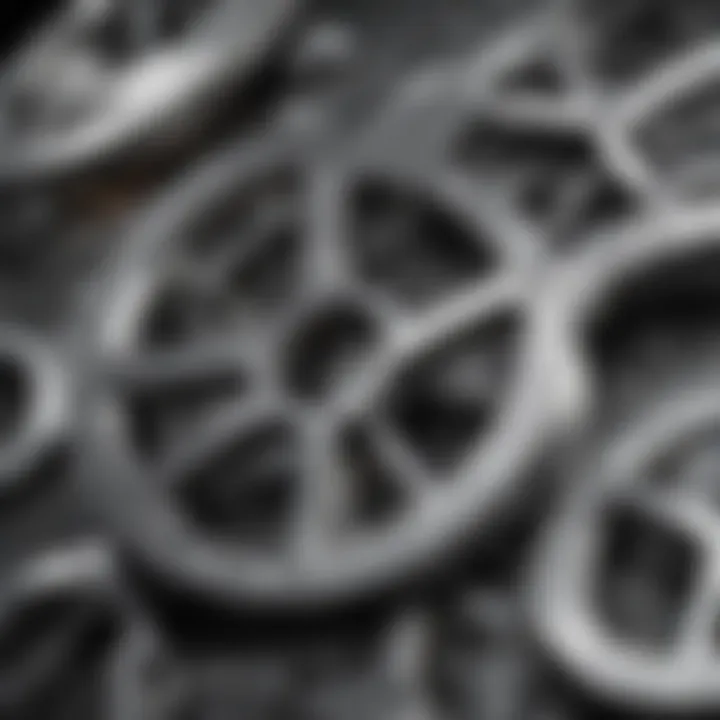
Welding and joining processes are vital in assembling components made of AL6061. Given its use in structural applications, it is necessary to understand how to properly join this alloy to ensure joint integrity and performance. Various methods can be used, including MIG welding, TIG welding, and friction stir welding.
- MIG Welding: Metal Inert Gas welding offers good results for AL6061 due to its speed and adaptability. However, control over heat input is critical to prevent warping or weakening the material.
- TIG Welding: Tungsten Inert Gas welding allows for precise control and produces strong, clean welds. While slower, it is suitable for thinner materials that require more finesse during the joining process.
- Friction Stir Welding: This solid-state process is ideal for AL6061, as it avoids melting and minimizes distortion. It aligns the material’s grain structure, resulting in superior strength at the weld joint.
These welding techniques ensure that components can be reliably assembled for demanding applications.
Applications of AL6061
The applications of AL6061 aluminum alloy are extensive and play a critical role in various industries. This section delves into the several uses of AL6061, highlighting its unique properties and advantages. The versatility of AL6061 allows for its use in a range of demanding environments, making it an essential material in aerospace, automotive, and construction contexts.
Aerospace Industry Usage
In the aerospace sector, AL6061 is favored for its excellent weight-to-strength ratio. This property is particularly crucial, as aircraft require materials that minimize weight without sacrificing structural integrity. AL6061 alloys are commonly used in airframes, engine components, and other critical structures. The alloy’s resistance to corrosion ensures longevity in various atmospheric conditions. Moreover, the ease of fabrication makes it suitable for complex shapes found in modern aircraft designs.
Automotive Engineering Applications
The automotive industry also benefits from AL6061’s unique characteristics. The lightweight nature aids in improving fuel efficiency, which is a growing concern in vehicle design. Automotive components such as frames, panels, and supports utilize AL6061 to achieve strength while keeping the overall vehicle weight low. Additionally, its response to various manufacturing processes, like extrusion and forming, provides manufacturers with great flexibility.
Construction and Structural Applications
AL6061 is widely used in construction and structural applications, thanks to its combination of strength, durability, and corrosion resistance. Many builders choose this alloy for facades, bridges, and other structural components exposed to the elements. The alloy's ability to be anodized offers an additional layer of corrosion resistance. Furthermore, this process enhances its aesthetic value, making AL6061 an attractive choice for architects and builders alike.
AL6061 aluminum alloy is vital across various industries, accurately balancing strength and weight while providing resistance to environmental degradation.
AL6061 aluminum alloy is vital across various industries, accurately balancing strength and weight while providing resistance to environmental degradation.
The adaptability of AL6061 to different applications signifies its importance in engineering and manufacturing, ensuring its relevance in current and future projects.
Comparison with Other Aluminum Alloys
The comparison of AL6061 with other aluminum alloys serves important functions in understanding its unique properties and applications. This analysis can guide professionals and researchers in selecting the right material for specific uses. Understanding such comparisons can help simplify the decision-making process while providing insights into the specific benefits and trade-offs associated with AL6061.
Two prominent aluminum alloys often compared to AL6061 are AL2024 and AL7075. Each of these alloys has distinct characteristics that can suit various needs.
Contrasting AL6061 with AL2024
AL2024 is known for its high strength and excellent fatigue resistance. It is primarily used in aerospace applications where these qualities are vital. The composition of AL2024 is rich in copper, which enhances its strength but also makes it less corrosion-resistant compared to AL6061.
- Strength considerations: AL2024 has higher tensile and yield strengths than AL6061 but at the cost of more complicated fabrication.
- Fabrication: AL6061 is more versatile in machining and forming than AL2024, making it more suitable for general-purpose applications.
- Corrosion resistance: While AL6061 is resistant to corrosion, AL2024 requires protective coatings when used in outdoor applications or harsh environments.
This demonstrates that while AL2024 might outperform AL6061 in specific metrics, the latter offers better overall adaptability.
Features of AL6061 vs. AL7075
AL7075 is another aluminum alloy recognized for its high strength-to-weight ratio. It also possesses excellent machinability and is stronger than AL6061. However, AL7075 is primarily alloyed with zinc, which can lead to issues with corrosion resistance.
- Strength vs. weight: AL7075 offers superior strength, making it a preferred choice for various military and aerospace applications where strength is crucial. This makes it an excellent choice for structural components.
- Weight considerations: AL6061, while not as strong, is lighter and easier to work with for many applications. Its weldability is also better, allowing for greater flexibility in design.
- Corrosion resistance: AL6061 shines in applications where corrosion resistance is a concern.
"Understanding the differences between these alloys is crucial for informed decisions in engineering and design."
"Understanding the differences between these alloys is crucial for informed decisions in engineering and design."
These interactions highlight that while AL6061 may not always be the strongest option, its versatility and corrosion resistance offer practical advantages that can be especially beneficial in many industries.
Cost-Effectiveness of AL6061
Understanding the cost-effectiveness of AL6061 aluminum alloy is vital for many industries. This analysis reveals how the balance of material performance and manufacturing expense can influence material selection. With the growing demand for efficient and sustainable practices, industries must consider not just the upfront costs but long-term investment returns. AL6061 presents a unique blend of functionality, versatility, and affordability that appeals to diverse manufacturing applications.
Market Trends and Pricing
The market for aluminum alloys, including AL6061, has shown dynamic changes due to several factors. First, the global economy impacts the pricing of aluminum. Factors such as supply chain disruptions, tariffs, and demand shifts contribute to price fluctuations. Prices of AL6061 can vary, typically falling within a range that reflects market demands.
- Demand in Key Industries: The aerospace and automotive sectors are primary consumers of AL6061, which helps drive prices based on their need for lightweight, durable materials.
- International Trade Policies: Regulations and trade agreements can affect the pricing structure significantly. Tariffs imposed on imported aluminum may lead to increased costs for manufacturers.
- Recycling and Sustainability: With increased focus on sustainability, recycled aluminum often offers a competitive edge in pricing, influencing how new alloys like AL6061 are priced.
Overall, staying updated with market trends is critical for businesses that rely on AL6061. Being informed helps in making purchasing decisions that can lead to cost savings and enhanced performance.
Economic Advantages in Manufacturing
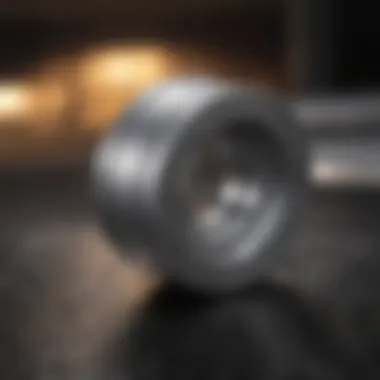

Cost savings during manufacturing processes involving AL6061 are substantial. Here are several economic advantages worth considering:
- High Strength-to-Weight Ratio: AL6061 provides excellent strength while remaining lightweight. This leads to reductions in material consumption, thus lowering costs.
- Ease of Fabrication: AL6061 is known for its good machinability and can be easily welded and formed, saving time and expenses in fabrication processes.
- Long Lifespan: The durability and corrosion resistance of AL6061 mean fewer replacements and repairs over time, making it an economical choice in the long term.
- Versatile Applications: With numerous applications ranging from aerospace to construction, manufacturers can diversify their offerings, enhancing market reach without additional material costs.
- Recyclability: The ability to recycle AL6061 leads to reduced costs in material recovery and supports sustainable practices, appealing to increasingly eco-conscious consumers.
As manufacturers continue to seek ways to reduce costs and improve their profit margins, AL6061 remains a compelling choice.
Environmental Impact of AL6061 Production
The environmental impact of AL6061 production must not be overlooked in any analysis of this widely used aluminum alloy. As industries strive for greater sustainability, understanding the ecological footprint of material production becomes paramount. This section discusses two critical aspects: sustainability and recycling, as well as energy consumption in production.
Sustainability and Recycling
Sustainability in the production of aluminum alloys like AL6061 refers to the ability to create materials while minimizing environmental harm. Aluminum is recyclable, which is one of its most significant advantages. Recycling plays a crucial role in reducing the demand for raw material extraction. The recycling process of aluminum requires only about 5% of the energy used in primary production. This substantial reduction in energy consumption makes recycling an attractive option for manufacturers.
Benefits of recycling AL6061 include:
- Reduced Energy Consumption: With lower energy needs, the overall carbon footprint of aluminum products diminishes.
- Conservation of Resources: Utilizing recycled aluminum lessens the need for mining bauxite, the primary source of aluminum.
- Lower Environmental Degradation: The mining and refining processes can have detrimental effects on local ecosystems. By recycling, these impacts are significantly mitigated.
It's vital for companies to understand not only the processing methods but also how their materials can be reused effectively. Implementing recycling protocols keeps AL6061 in circulation, contributing positively to sustainable practices. Furthermore, industries are increasingly required by regulations to manage waste and recycling, which adds another layer of responsibility.
Energy Consumption in Production
Energy consumption is another pivotal factor when assessing the environmental impact of AL6061. The production process of aluminum alloys is energy-intensive, particularly during the refining and smelting stages. For instance, primary aluminum production from bauxite ore can require substantial kilowatt-hours of energy per ton produced. In contrast, the secondary production from recycled aluminum has far lower energy demands.
Key considerations regarding energy consumption include:
- Source of Energy: The type of energy used can greatly affect the carbon footprint. For example, utilizing renewable energy sources such as wind or solar can reduce greenhouse gas emissions in aluminum production.
- Technological Innovation: Advancements in technology may lead to processes that minimize energy use in producing AL6061. This includes developments in electrification of smelting processes and efficiency in manufacturing techniques.
- Lifecycle Analysis: A full assessment of energy use includes evaluating energy consumed throughout the material's lifecycle, from production to end-of-life recycling. Understanding this can guide improvements in sustainable practices.
The importance of managing energy use in production cannot be overstated, especially as industries face increasing pressure to reduce their environmental impact.
The importance of managing energy use in production cannot be overstated, especially as industries face increasing pressure to reduce their environmental impact.
Future Directions in AL6061 Research
Research in AL6061 aluminum alloy has significant implications not just for material science but also for various industries relying on high-performance materials. Investigating future possibilities with AL6061 is vital for improving performance, reducing costs, and supporting sustainability. By exploring innovations and technological advancements, industry leaders and researchers can push the boundaries of what this versatile alloy can achieve across its applications.
Innovations in Alloys and Composites
The pursuit of innovation in alloys and composites involving AL6061 is vital for enhancing properties such as strength, ductility, and corrosion resistance. New alloy compositions can be developed to improve upon the existing characteristics of AL6061. This tailor-made approach allows for the creation of materials that meet specific requirements in various industries.
Some areas of focus include:
- Additive Manufacturing: Using AL6061 in 3D printing creates new opportunities for complex geometries and reduced material waste. Enhanced methods in this area can lead to more effective production methods.
- Hybrid Composites: The combination of AL6061 with other materials like carbon fiber is being explored to achieve lightweight and high-strength solutions. Hybrid composites could find applications in automotive and aerospace sectors.
- Nanotechnology: The integration of nanoparticles can be investigated to refine the mechanical properties of AL6061. Strengthening the alloy at the atomic level can result in remarkable performance metrics.
„Innovative research in alloy formulation is paving the way for next-generation materials that can redefine performance standards in various fields.”
„Innovative research in alloy formulation is paving the way for next-generation materials that can redefine performance standards in various fields.”
Technological Advances in Processing
Technological advancements in processing techniques also play a crucial role in shaping the future of AL6061. Innovations here can significantly impact economic viability and sustainability. Potential areas for improvement include:
- Optimized Fabrication Techniques: Enhancing extrusion and casting methods can lead to better surface finishes, improved dimensional tolerances, and overall performance. Employing advanced computational approaches can assist in the simulation and optimization of these processes.
- Automation and AI: Integrating automation in manufacturing processes ensures consistency and quality. AI can analyze data to optimize production runs and reduce waste, thus contributing to more efficient use of resources.
- Surface Treatments: New treatments, such as anodization or coatings, are being researched. These not only enhance the corrosion resistance of AL6061 but also improve its aesthetic value and longevity in various applications.
Queens of technology have the potential to unlock numerous benefits for AL6061, making it a more viable option for a broad spectrum of uses. Keeping stride with increasing demands for performance and sustainability will help in positioning AL6061 as a leader among aluminum alloys.
Finale and Summary
In concluding this exploration of AL6061 aluminum alloy, it is essential to emphasize its multifaceted role in various sectors. This summary encapsulates not only the highlighted attributes of the alloy but also its significance in advancing technology and engineering practices. Understanding the properties and advantages of AL6061 aids in appreciating its position in modern applications.
AL6061 exhibits excellent mechanical properties, including good corrosion resistance, weldability, and moderate to high strength. These characteristics make it a preferred material in industries such as aerospace, automotive, and construction, where there is a demand for lightweight yet durable materials.
Key Takeaways
- Versatility: AL6061 finds application across a wide range of fields, from structural components to intricate aerospace parts.
- Mechanical Strength: It offers notable strength-to-weight advantages compared to other materials, enhancing performance efficiency in various applications.
- Cost-Effectiveness: AL6061 is economic, which contributes to its popularity in large-scale manufacturing and production.
- Sustainability: The recycling potential of AL6061 aligns with increasing global emphasis on sustainable practices in materials use.
Significance of AL6061 in Industry
AL6061's significance extends beyond its material properties. In the aerospace industry, its lightweight nature helps improve fuel efficiency, a critical concern for modern aviation. Likewise, its applications in the automotive sector cater to the push for lighter vehicles to reduce emissions while maintaining safety standards.
The construction industry utilizes AL6061 for its structural integrity, offering solutions that are cost-effective as well as reliable. Furthermore, ongoing research into enhanced alloys and technological solutions indicates that AL6061 will continue to play a crucial role as industries evolve.
In summary, the exploration of AL6061 aluminum alloy reveals it as an essential material in engineering, demonstrating a blend of utility, strength, and adaptability. Its ongoing relevance in various sectors highlights the importance of understanding such alloys in driving future innovations.