Inertial Particle Separator: Mechanisms and Applications
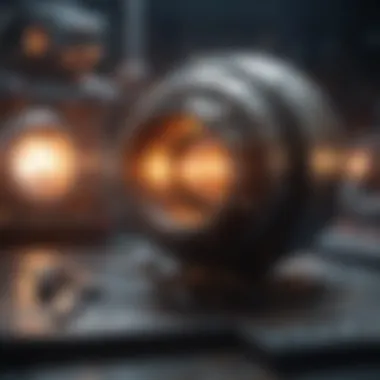
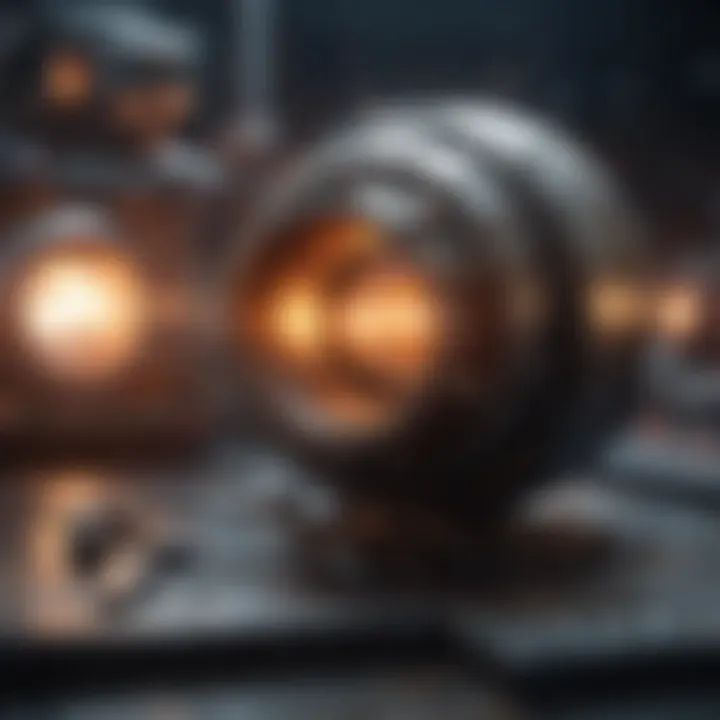
Intro
Inertial particle separators form a pivotal part of various scientific and industrial processes. They serve the purpose of extracting particles from a gas or liquid flow based on differences in their inertia. This foundational principle of physics underlies a multitude of applications—from air filtration to pharmaceuticals. Understanding the workings of these devices necessitates diving into their operational mechanisms, key components, and the real-world scenarios where they find application.
An inertial separator primarily utilizes centrifugal forces and inertial effects to segregate particles of differing size and density. Various designs capitalize on these principles, integrating both physical and mechanical elements to achieve efficient separation.
The critical essence of these separators lies not just in their theory, but also in their pragmatic use in industries such as manufacturing where air quality is essential, and biotechnology, where the purity of product is paramount. Key to their success is the ongoing research aimed at refining these devices to maximize performance while tackling challenges related to efficiency, scalability, and adaptability.
Delving deeper into this topic will shed light on the core scientific principles that govern inertial particle separation, recent advancements in research, and the hurdles innovators face as they seek to improve these crucial devices.
Key Concepts
Definition of the Main Idea
An inertial particle separator is an apparatus designed to separate solid particles from fluids (both liquid and gas) leveraging the principles of inertia. Unlike static filtration, where particulates are trapped by a medium, this approach allows for more dynamic control over the separation process. Here, particles of different sizes and densities undergo a physical shift due to inertia, enabling effective collection and removal.
Overview of Scientific Principles
The operating principle of inertial particle separators is deeply rooted in concepts from fluid dynamics and physics. Here are some critical factors:
- Inertia: In essence, this is the tendency of particles to maintain their state of motion. When fluid flow encounters a bend or a turn within a separator, heavier particles tend to resist the change in motion more than lighter ones, eventually moving toward the separator wall.
- Centrifugal Force: Within a rotating mechanism, centrifugal force causes particles to move outward from the center. This force becomes pivotal in enhancing the efficiency of separation processes, particularly in cyclonic designs.
- Drag Forces: As particles travel through a fluid, they experience resistance or drag. This effect is countered by the inertia of larger particles, which remains influential in determining their position in the flow. Understanding the interplay between drag and inertia is paramount for optimizing separator performance.
Current Research Trends
Recent Studies and Findings
Research in inertial particle separators has recently shifted focus towards improving the design and efficiency of these devices. Studies have investigated various geometrical configurations of separators, leading to findings that suggest that changes even at a micro-scale can dramatically enhance separation efficiency. Emerging technologies in sensor and material sciences are increasingly being harnessed to create better separators.
Significant Breakthroughs in the Field
Noteworthy advancements include:
- Smart Separators: Incorporating IoT technologies, these separators can adjust their operational parameters in real-time, responding to fluctuations in particle load and size.
- Nanotechnology Applications: Utilizing nanostructured materials has been shown to increase efficiency and effectiveness at separating ultra-small particles, which were previously challenging.
- Hybrid Designs: Integrating multiple separation principles, such as combining inertial with magnetic separation, provides new avenues for broader efficiencies and applications across various fields.
As these innovations take shape, inertial particle separators that were once seen as niche solutions are becoming ever more relevant in an array of industries, positioning them as essential tools for future projects.
Understanding Inertial Particle Separators
In the realm of engineering and environmental sciences, inertial particle separators play a vital role in maintaining purity and efficiency in various processes. Their ability to effectively separate particles from gases and liquids hinges on well-defined principles of physics, which not only underline their functionality but also contribute to advancements in technology. As industries increasingly seek efficient solutions for particle separation, it becomes crucial to grasp the significant mechanisms behind inertial separators, as well as their applications.
Definition and Basic Principles
An inertial particle separator is designed with the primary goal of separating solid particles or droplets from a fluid stream based on inertia. Inertia, in this context, refers to the tendency of a particle to resist changes in its motion. In simpler terms, when a fluid carries particles, those moving at different velocities will behave differently when subjected to changes in flow direction. This principle allows inertial separators to trap unwanted particles while letting the filtered fluid pass through.
The basic operation relies on several interrelated concepts:
- Velocity Differences: Fast-moving particles will continue on their path, while slower particles will be deflected, facilitating separation.
- Geometric Design: The shape and orientation of the inertial separator are crucial in enhancing its ability to achieve efficient particle separation.
- Density: Heavier particles tend to settle quicker than lighter ones, a factor exploited in various designs.
Understanding these fundamental aspects helps in comprehending the performance extremes and constraints of inertial particle separators, making them critical in fields such as chemical processing or environmental management.
Historical Context
The journey of particle separation technologies, including inertial methods, stretches back over a century, rooted deep in the industrial revolution when efficient material processing became essential. The early 20th century marked significant innovations, with advancements driven by evolving industrial needs.
By the mid-1900s, researchers began systematically exploring the principles governing particle dynamics and fluid interactions. This exploration laid the groundwork for modern inertial separators.
One pivotal moment occurred in the 1950s, when the development of more sophisticated fluid dynamics insights came into play. Engineers realized how refined geometrical designs could greatly enhance separation efficiency through tailored flow patterns. As industries grew and the demand for cleaner processes intensified, inertial separators found their niche in sectors ranging from oil and gas to pharmaceuticals.
Over the decades, technological innovations have continuously reshaped inertial particle separators. The evolution from rudimentary designs based on trial and error to high-tech, computationally optimized models illustrates a major advancement in not just engineering, but in understanding the underlying principles of fluid mechanics. Today, inertial particle separators are not just efficient—they are essential tools in ensuring processes remain clean, sustainable, and economical.
"Recognizing the historical context, we can appreciate not just the evolution of the technology but the foundational principles that guided its development."
"Recognizing the historical context, we can appreciate not just the evolution of the technology but the foundational principles that guided its development."
This understanding bridges the past and the present, allowing professionals and researchers to make informed decisions for future innovations.
Physical Principles Involved in Separation
Understanding the physical principles of inertial particle separators is crucial for grasping how these devices function across various applications. The interplay of inertia, fluid dynamics, and centrifugal forces all contribute to the effectiveness of the separator. This section will delve into these elements, highlighting their significance in optimizing the separation processes.
Inertia and Particle Dynamics
Inertia plays a central role in particle dynamics, especially when dealing with inertial particle separators. Simply put, inertia refers to an object's resistance to changes in its state of motion. In the context of particle separation, when a fluid containing particles flows through a separator, particles with greater mass will tend to maintain their trajectory due to inertia compared to lighter particles.
The effectiveness of inertial separation hinges on the size and density of the particles. Larger and denser particles experience greater inertial forces, which can cause them to deviate from the path of the fluid flow. This principle is paramount, particularly in scenarios where it’s crucial to separate debris or contaminants from a principal medium. The ability of the separator to harness inertia properly means that its design must consider factors like particle size distributions and the physical properties of the target materials.
Fluid Dynamics and Flow Patterns
Next in line is fluid dynamics, which captures how fluids behave and interact with solid particles during the separation process. The flow patterns created within the separation chamber are essential for achieving efficient particle differentiation. There are various flow regimes—laminar and turbulent, to name a couple—that influence how particles settle and separate.
- Laminar Flow: Occurs when fluid moves in parallel layers, with minimal disruption between them. This behavior can be beneficial in separating fine particles since it allows for more precise movement.
- Turbulent Flow: Characterized by chaotic changes in pressure and flow velocity. While this might enhance mixing, it can complicate particle separation if not properly managed.
To optimize the separator’s efficiency, engineers often model flow patterns to ensure adequate residence time for particles to interact with the forces acting on them. Moreover, the design of the inlet and outlet must be adapted to control fluid velocity and ensure that the optimal state of flow is achieved.
Role of Centrifugal Forces
Centrifugal forces are another significant player in the separation game. When the separator operates under rotational movement—either by design or due to the dynamics of the flow—this creates a force that pushes particles away from the center. Relying on this force is particularly effective for enhancing the separation of heavy particles from lighter ones, as it can amplify the inertial effects already discussed.
As particles travel through the separation chamber, those with greater mass experience stronger centrifugal forces, effectively pushing them outwards where they can be collected. The balance between centrifugal force and the opposing forces, such as drag, must be meticulously calculated for the setup to function optimally.
The physical principles of inertia, fluid dynamics, and centrifugal forces all work in harmony to make inertial particle separations efficient. Understanding these mechanics opens doors to improved designs and applications across various fields.
The physical principles of inertia, fluid dynamics, and centrifugal forces all work in harmony to make inertial particle separations efficient. Understanding these mechanics opens doors to improved designs and applications across various fields.
In essence, developing a well-informed understanding of these principles not only aids in appreciating the operational mechanics of inertial particle separators but also paves the way for advancements in the technology, fostering innovation in how we approach particle separation in numerous sectors.
Components of Inertial Particle Separators

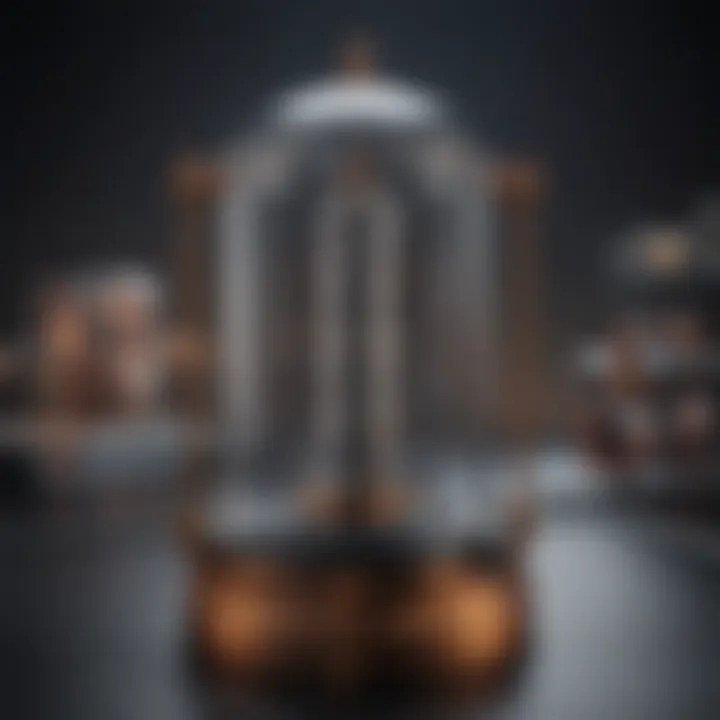
Inertial particle separators are essential devices designed to effectively segregate particles from gases or liquids based mainly on their inertia. Understanding their components provides crucial insight into how these separators function and the considerations that influence their design. The separation efficiency hinges not just on how the particles behave within a given medium, but also on specific elements integral to the design and operational capabilities of the separator. By focusing on these elements, designers and engineers can enhance performance and adapt the technology across various applications.
Separation Chamber Design
The separation chamber is arguably the heart of an inertial particle separator. Its design is paramount since it must strategically create the right conditions for particles of varying sizes and densities to be separated effectively. In its simplest form, the chamber's shape influences airflow patterns, which in turn affects how particles are retained or expelled.
Key considerations in the design include:
- Geometry: A streamlined, perhaps conical shape can help maximize particle inertia. This design fosters a quicker transition of the fluid, which is essential as particles navigate through the separator.
- Surface Texture: The interior surface finish matters, too. A rougher texture could allow for better particle adhesion or agglomeration, depending on the design's intent.
- Dimensions: Finally, the size of the separation chamber must align with the intended application. Larger chambers might capture more particles but could also lead to inefficient airflow, while smaller chambers may provide better control but can become quickly clogged.
Inlet and Outlet Configurations
Getting the inlet and outlet configurations right is vital for the overall efficacy of the separator. Properly designed inlets ensure a smooth entry of the flow into the chamber, minimizing turbulence and maximizing the potential for separation. In contrast, the outlets must allow for efficient discharge of the segregated phases.
For inlets, consider:
- Flow Direction: The angle at which the fluid enters can dramatically impact separation. A tangential or angled entry can enhance centrifugal force effects, assisting in particle separation.
- Size and Shape: A wider inlet may allow for larger bulk flows, but could increase the likelihood of unintentional particle re-entrainment if not matched with adequate outlet design.
As for outlets, they should be strategically placed to facilitate:
- Controlled Exit: An ideal outlet design ensures that only the separated product exits while retaining the undesired particles.
- Versatility: Options to adapt outlet sizes or configurations based on varying flow rates ensures that the separator can function under different operational scenarios.
Collection Mechanisms
Once particles are separated, an effective collection mechanism is crucial for retaining the desired materials and preventing losses. These mechanisms can vary widely depending on the application but generally fall into a few key categories:
- Cyclonic Collections: Many inertial particle separators utilize cyclonic action where particles, forced to the perimeter of the chamber by centrifugal force, settle into a collection area at the bottom. This method is beneficial for larger particles and is widely used in industrial applications.
- Gravitational Settling: Another method relies on gravity to assist in the separation. Heavier particles simply fall out of the flow stream, gathering in designated areas for easy removal. This mechanism works well in applications with a broad range of particle sizes.
- Mechanical Collectors: For fine particulates, mechanical collectors, such as filters or electrostatic collectors, can be employed post-inertial separation to capture the lingering particles that did not get caught in the initial separation phase.
A well-designed collection mechanism not only saves on material but also reduces the need for secondary processes, making it an invaluable aspect in the overall design of inertial particle separators.
A well-designed collection mechanism not only saves on material but also reduces the need for secondary processes, making it an invaluable aspect in the overall design of inertial particle separators.
These components, when optimized, work synergistically to deliver high-performance separation. Understanding and innovating within this framework leads to enhanced efficiency, making inertial particle separators vital tools across various industries, from environmental engineering to chemical processing.
Applications in Various Industries
Exploring the applications of inertial particle separators reveals their significance in multiple sectors, notably in enhancing efficiency and meeting industry standards. These devices are pivotal for ensuring product purity, reducing environmental impact, and streamlining processes. Each industry faces unique challenges and opportunities, making an understanding of their applications essential for professionals engaged in chemical processing, environmental engineering, and materials science.
Chemical Processing
In chemical processing, inertial particle separators are crucial for removing unwanted solid particles from liquids and gases. The efficient separation of different phases leads to increased product quality and reduced downtime due to maintenance and cleaning.
Key benefits include:
- Improved Purity: High purity levels in chemical products are paramount. By removing contaminants early in the process, separators ensure that the final product meets stringent standards.
- Process Optimization: Integrating these separators can enhance flow rates and reduce the workload on downstream processes, leading to a more efficient production cycle.
- Cost Savings: Reducing the amount of waste and rework minimizes costs associated with manual filtering methods.
Those in the industry rely on separators to enhance operational efficiency while maintaining the quality of output. For instance, companies often combine inertial separators with other techniques, leading to a hybrid system that amplifies performance and reduces operational costs.
Environmental Engineering
The relevance of inertial particle separators in environmental engineering cannot be overstated. These devices play a vital role in air and water purification systems, addressing the pressing issue of pollution control.
Consider the following elements:
- Air Quality Management: Separators assist in capturing particulate matter from industrial exhaust, contributing to improved air quality and compliance with regulatory standards.
- Waste Treatment: In wastewater management, they help in the removal of solids before further treatment, thus extending the lifespan of subsequent purification systems.
- Sustainability: The adoption of inertial separators supports sustainability efforts, allowing organizations to minimize their environmental footprint while adhering to governance policies.
For example, in the coal industry, these separators can effectively remove fly ash from emissions, thereby improving overall environmental performance and reducing costs associated with fines for exceeding emission limits.
Materials Science
In materials science, inertial particle separators can help in nanomaterial synthesis and characterization processes. The precise application of these separators aids researchers in the development and refinement of new materials.
Important considerations include:
- Product Consistency: Achieving uniformity in material properties is essential. Inertial separators ensure that only the right particle sizes remain in the production stream, enhancing the properties of the end materials.
- Innovation in Materials: The ability to manipulate particle sizes and compositions allows scientists to develop innovative materials with tailored characteristics, which can open doors to new applications.
- Efficiency in Research and Development: By speeding up the separation process, researchers can focus on experimenting and discovering new applications for advanced materials.
In one case, a recent study highlighted how the separator technology advanced the speed of producing quantum dots, leading to applications in electronics and photonics domains.
Comparison with Other Separation Techniques
In the realm of particle separation methodologies, understanding where inertial particle separators fit into the greater picture is crucial. Their unique mechanisms make them distinct from other conventional methods like centrifugal separators, filtration, and electrostatic separation. Each technique has its own strengths and weaknesses, which can affect efficiency, cost, and applicability in various scenarios. This section aims to outline these comparisons, highlighting the benefits and potential considerations that come into play when selecting between these methodologies.
Centrifugal Separators
Centrifugal separators operate based on the principle of centrifugal force. They rotate a mixture at high speeds, which causes denser particles to move outward while lighter particles remain closer to the axis of rotation. This method is quite effective for separating larger particles from a liquid medium, but it can be energy-intensive.
Pros of Centrifugal Separators:
- High efficiency for liquids with large particle sizes.
- Ability to handle a wide range of feed compositions.
- Established technology with significant industrial applications.
Cons of Centrifugal Separators:
- High operational costs related to energy use.
- Equipment can be bulky, requiring significant space.
- Not always suitable for smaller particles where inertial effects may dominate.
In many cases, the choice between an inertial separator and a centrifugal one can hinge on the specific properties of the particles being separated and the desired outcome. Inertial separators can often be more efficient when dealing with variable particle sizes since they utilize direct mass movement, rather than relying predominantly on centrifugal force.
Filtration Methods
Filtration involves passing a suspension through a medium that allows smaller particles to pass while retaining larger ones. This can be done through various filter types, such as bag, cartridge, or membrane filters. Filtration techniques are widely accepted for their simplicity and effectiveness in many applications, particularly in water treatment and chemical processing.
Pros of Filtration Methods:
- Versatile and adaptable for different particle sizes and types.
- Generally lower operating costs compared to other methods.
- Simple to implement and maintain.
Cons of Filtration Methods:
- Can be limited by clogging, which reduces efficiency over time.
- May require pre-treatment of fluids for optimal performance.
- Not suitable for very fine particles or those that alter fluid properties (like emulsions).
While inertial separations can also handle complex mixtures, traditional filtration methods might not cope with changes in particle concentration as effectively as inertial separations can.
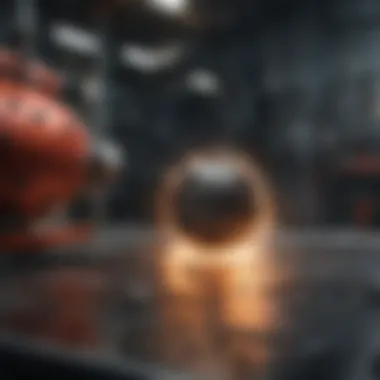
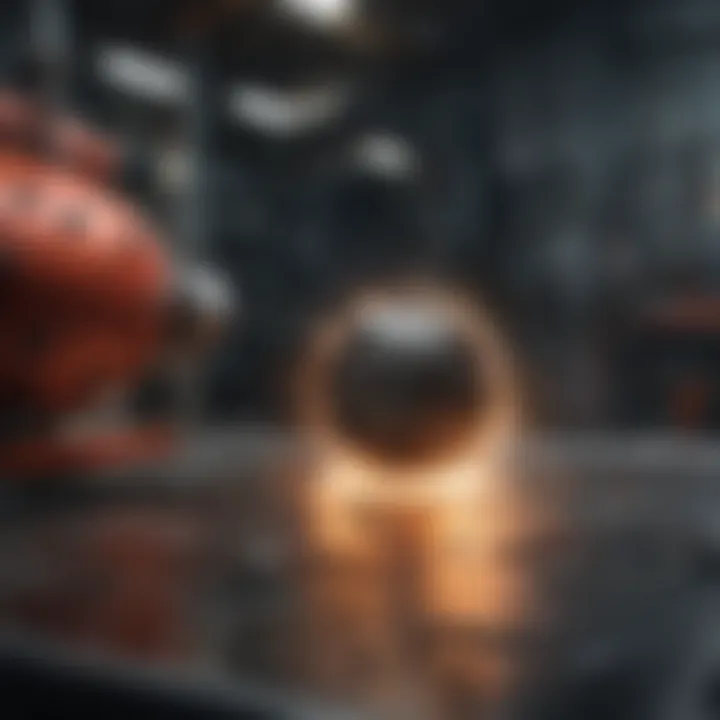
Electrostatic Separation
Electrostatic separation relies on the separation of charged particles using electric fields. It is especially useful in the mineral processing sector for separating conductive and non-conductive materials. While this technique shows promise for certain applications, it has its intricacies.
Pros of Electrostatic Separation:
- Effective for separating substances based on electrical properties.
- Low energy consumption when operational parameters are optimized.
- Capable of handling fine particles that may be challenging for other separation methods.
Cons of Electrostatic Separation:
- Requires a controlled environment to prevent interference from moisture or dust.
- Not ideal for materials with similar electrical or physical properties.
- Equipment can be expensive to set up and maintain.
In this context, inertial particle separators provide an alternative by utilizing physical forces rather than electrical charges to distinguish between particles. This could lead to better results in certain applications where particle behavior in fluids holds more significance compared to electrostatic properties.
In summary, while inertial particle separators stand out with their specific mechanisms, it's essential for professionals and researchers to evaluate the context of use against other separation techniques. Balancing factors like efficiency, cost, and specific application requirements will guide users in making informed choices.
In summary, while inertial particle separators stand out with their specific mechanisms, it's essential for professionals and researchers to evaluate the context of use against other separation techniques. Balancing factors like efficiency, cost, and specific application requirements will guide users in making informed choices.
Design Considerations and Challenges
Design considerations and challenges in the context of inertial particle separators are crucial elements that dictate the effectiveness and efficiency of these systems. These separators must not only function optimally within varied operational conditions but also ensure reliability and safety. As industries evolve, the demands placed on these systems increase, leading to a myriad of design complexities that need addressing.
Optimization of Performance
One of the primary challenges is optimizing performance. Designing an inertial particle separator that maximizes separation efficiency while minimizing energy consumption is a tightrope walk. Various factors play a role in optimization:
- Flow Rate: The speed at which fluid enters the separator is vital. Too high a flow could overwhelm the system, while too low may not allow for efficient separation.
- Particle Size Distribution: The separator must be able to handle a range of particle sizes. A uniform design might suffice for a specific case, but real-world application often involves varying dimensions.
- Operational Pressure: Adjusting operating pressure can influence performance significantly. Finding the right balance can enhance separation while reducing the risk of system failure.
It’s a bit like tuning a musical instrument, where every small adjustment can lead to either a harmonious result or a cacophony.
Material Selection
The choice of materials in constructing inertial particle separators cannot be overlooked. Materials directly affect durability, efficiency, and the overall longevity of the equipment. Some key considerations include:
- Corrosion Resistance: Given the environments they often operate in, careful selection of materials that can withstand chemicals or other corrosive elements is paramount. Stainless steel or specific alloy formulations may be necessary in harsher settings.
- Weight vs. Strength: There’s often a trade-off between using lighter materials versus those that provide greater structural integrity. This balance is particularly important in portable or mobile applications where weight is a concern.
- Cost Considerations: Material choice also factors heavily into the economic feasibility of a design. While high-end materials might yield better performance, manufacturers need to consider the entire lifecycle cost, including maintenance and replacement.
Selecting appropriate materials is akin to choosing the right ingredients in a recipe; the outcome heavily depends on this initial decision.
Scalability and Cost Efficiency
Finally, scalability and cost efficiency play significant roles in modern design considerations. A system that works well on a small scale may not necessarily translate to larger applications without extensive modifications. Scalability involves:
- Modular Design Features: Incorporating segments that can be added or removed offers flexibility. Such designs allow for easy upgrades or adjustments based on operational demands.
- Cost Evaluation: Every phase, from design to implementation, must be assessed for its economic impact. Engaging in thorough cost-benefit analyses can help avoid future financial pitfalls.
- Market Adaptation: Being aware of market trends and customer needs can guide design scalability. As industries move toward advanced technologies, separators must be adaptable to incorporate new innovations without substantial overhauls.
Without scalability in mind, companies risk finding themselves in a rut, unable to meet evolving demands or technologies.
In the end, navigating these design considerations and challenges requires a holisitic approach. A clear strategy, incorporating mechanical, material, and economic factors, will ensure the relevant technology optimally fulfills its intended application.
Future Directions in Research
The study of inertial particle separators is unfolding a manifold of possibilities for future research. The evolving demands of various industries, alongside environmental concerns, are setting the stage for innovations that stretch well beyond traditional methodologies. Diving into this topic reveals potential enhancements in performance, efficiency, and applicability, which are imperative for bridging the gap between current technology and future needs.
Technological Innovations
Technological innovations remain at the forefront of advancing inertial particle separator systems. Recent leaps in material science and computational modeling are fueling breakthroughs that help refine separator design and function. For example, using advanced materials like composites can drastically reduce weight while enhancing durability. This is no small feat, as previous separators often suffered from wear and tear, resulting in decreased efficacy and higher maintenance costs.
Moreover, incorporating nanotechnology for surface modifications can create surface designs that promote better particle adhesion or flow dynamics, honing in on efficiency. By leveraging simulations and computer-aided design tools, researchers can explore complex geometries without the risks associated with physical prototyping. Technologies such as 3D printing are also making it feasible to create intricate designs that were once deemed impossible.
Integration with Automation
Automation is another critical avenue for future research. As industries aim for greater productivity, integrating inertial particle separators into automated systems proves advantageous. The ability to control separation processes in real-time not only improves accuracy but also enhances the overall throughput of operations. For instance, implementing sensors that monitor flow rates and particle sizes can facilitate adaptive behavior, ensuring that the separator dynamically adjusts to varying conditions throughout its operation.
Moreover, automation can streamline maintenance procedures, with predictive analytics having the capability to forecast when a separator requires service. The potential for developing smarter systems thus presents an exciting landscape, where operators can focus on strategic activities rather than routine checks.
Environmental Impact Studies
Considering the mounting pressure to illustrate environmental stewardship in industrial practices, conducting comprehensive environmental impact studies on inertial particle separators winds up becoming essential. These studies could explore how improving the efficiency of separation technologies might reduce waste and associated emissions. Focussing on life cycle assessments, researchers can gauge how these systems stack against other separation techniques, from raw material sourcing to end-of-life disposal.
Furthermore, understanding the ecological implications of particle separation can lead to more sustainable design and operational practices. This not only addresses industry regulations but also fosters public trust, as companies can showcase measurable improvements in their environmental footprint.
Case Studies of Inertial Particle Separation
Examining case studies of inertial particle separation offers a window into practical applications of theoretical concepts. These studies not only demonstrate the effectiveness of these separation mechanisms but also shed light on the potential pitfalls. Such insights can be invaluable, especially for professionals and researchers navigating this specialized field.
The studies analyzed encompass a range of industries, from environmental engineering to chemical processing. Each case illustrates specific methodologies, challenges, and outcomes related to the implementation of inertial particle separators. Understanding these real-world applications helps bridge the gap between academic research and industrial implementation, ultimately guiding future projects and innovations.
Successful Implementations
There are notable instances of successful applications of inertial particle separators that serve as prime examples of innovation in various fields. For instance, in the chemical processing industry, a facility specializing in pharmaceutical manufacturing adopted an inertial separation system to enhance product purity. By integrating a customized separation chamber design, they significantly reduced contamination rates.
Another striking case can be observed in the environmental sector. A wastewater treatment plant implemented an inertial particle separator to effectively manage the separation of sludge from treated water. The integration of this technology improved overall efficiency and reduced operational costs while ensuring compliance with environmental standards.
Key elements that make these implementations successful include:
- Tailored design: Adapting the separator’s design to fit specific operational needs.
- Performance optimization: Regular assessments and modifications based on performance data!
- Collaboration: Engaging with engineering teams to streamline installation and operation processes.
"Understanding the nuances in implementation can lead to remarkable advancements in separation technology."
"Understanding the nuances in implementation can lead to remarkable advancements in separation technology."
Lessons Learned from Failures
While success stories are inspiring, failures also provide important lessons. Several attempts to implement inertial particle separators have faced significant hurdles. For example, a mining company once invested heavily in inertial separation technology to manage fine particulates in ore processing. Unfortunately, they encountered frequent blockages due to a lack of adequate inlet design, affecting throughput and leading to costly downtimes.
In another instance, a food processing plant experienced challenges when the particle separator could not handle the variety and viscosity of materials processed. This discrepancy resulted in inadequate separation and ultimately product loss.
Crucial takeaways from these experiences include:
- Thorough feasibility studies: Before implementing new technology, a comprehensive analysis of existing operational parameters is essential.
- Flexibility in design: Being prepared to adapt designs based on operational feedback rather than sticking rigidly to initial specifications.
- Continuous education and training: Ensuring that all staff understand both the machinery and the processes can prevent many common pitfalls.
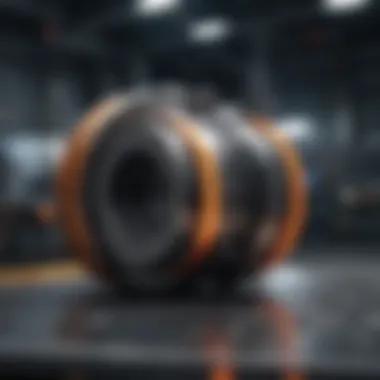
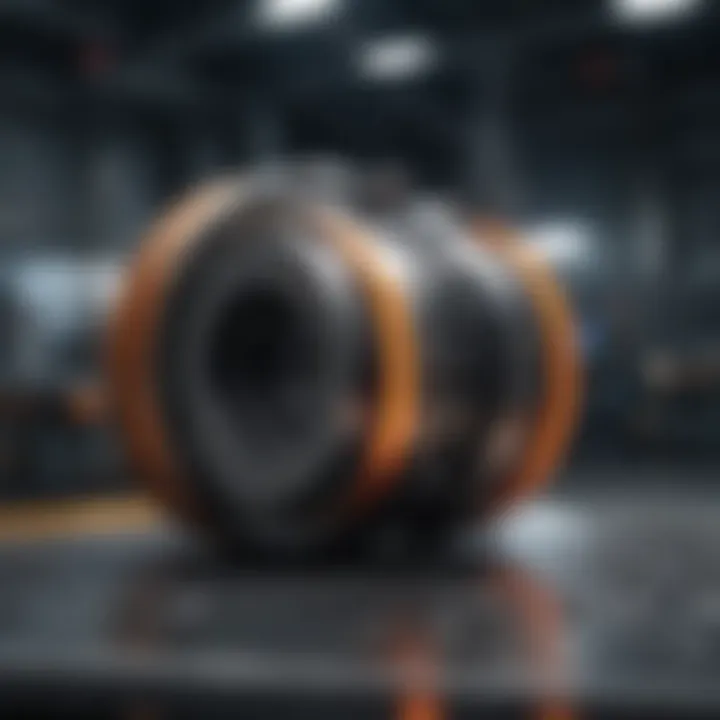
By reflecting on both successes and failures, the field of inertial particle separation can advance further, guiding new innovations and improving existing technologies.
Regulatory and Safety Considerations
The importance of regulatory and safety considerations in the operation of inertial particle separators cannot be overstated. These systems are widely used in industries where the efficient separation of particles from gases or liquids is critical for both environmental compliance and operational efficiency. Adhering to regulatory guidelines not only ensures product quality and safety but also plays a significant role in minimizing risks related to health and environmental impacts. Regulatory frameworks provide the necessary assurance that these systems are designed and maintained to operate safely and effectively.
Industry Standards and Guidelines
To navigate the complex landscape of regulatory requirements, various industry standards and guidelines have been established. Organizations such as the American National Standards Institute (ANSI) and the International Organization for Standardization (ISO) provide comprehensive frameworks that guide the design and implementation of inertial particle separators.
These standards cover a range of topics, including:
- Design criteria: Ensuring that separators are built to withstand operational stresses and meet performance metrics.
- Testing protocols: Outlining methods to validate the efficiency and reliability of particle separation.
- Material safety: Specifying acceptable materials that do not pose risks during operation, especially in chemical processing contexts.
Following these guidelines not only enhances safety but also boosts the overall credibility of the manufacturers and users in the market.
Risk Management Practices
Implementing effective risk management practices is key to ensuring the long-term success and safety of inertial particle separators. These practices involve identifying potential hazards, assessing their impact, and putting measures in place to mitigate risks.
Some critical aspects of risk management in this area include:
- Regular Maintenance: Routine checks and maintenance schedules can prevent operational failures that might lead to hazardous situations.
- Staff Training: Ensuring that operators are well-trained and understand the procedures for safely handling the equipment can significantly reduce human error.
- Emergency Protocols: Establishing clear procedures for emergencies can help minimize downtime and environmental impact in the event of a failure.
- Environmental Impact Assessments: Conducting assessments can help foresee potential environmental issues, ensuring that any adverse effects are addressed proactively.
In essence, it’s crucial that both manufacturers and operators take regulatory and safety matters seriously. A well-structured approach to these considerations not only fosters safer operational environments but also builds stronger public trust and compliance with legal frameworks.
"A proactive stance on regulatory and safety considerations can transform potential challenges into opportunities for improvement and innovation."
"A proactive stance on regulatory and safety considerations can transform potential challenges into opportunities for improvement and innovation."
By focusing on these elements, industries can ensure the efficient and safe operation of inertial particle separators, fulfilling both operational needs and societal obligations.
Interdisciplinary Approaches
In the ever-evolving landscape of technology and science, interdisciplinary approaches become more than just a buzzword—they're a necessity. Especially when dealing with intricate systems like inertial particle separators, the blending of different fields fosters innovation and enhances performance. In this section, we delve into the essence of interdisciplinary work, considering how it impacts the design, function, and enhancement of these separators.
Collaborations Across Fields
Collaboration across various disciplines can yield considerable advantages. For instance, bringing together engineers, chemists, and environmental scientists can result in a more robust design of a particle separator. Each expert offers a unique perspective and skill set. Engineers might focus on the mechanical aspects, optimizing the design for efficiency. Chemists can analyze the composition of particles and fluids involved in the separation process, ensuring effective interactions between them. Environmental scientists, on the other hand, can provide insights on sustainable practices and the ecological impact of design choices.
In practical terms, an example of such a collaboration is seen in the development of inertial particle separators for wastewater treatment. Here, civil engineers work alongside environmental experts to ensure that the system not only functions effectively to remove particulates but does so in a way that complies with environmental regulations.
"Interdisciplinary work strikes at the heart of innovation—combining knowledge and expertise is the key to solving complex problems."
"Interdisciplinary work strikes at the heart of innovation—combining knowledge and expertise is the key to solving complex problems."
Role of Data Science and Modeling
Entering the realm of data science and modeling, the significant impact of these fields on inertial particle separators cannot be overstated. Advanced data analytics can help in predicting system performance and identifying potential bottlenecks before they become problematic. For instance, predictive modeling using machine learning techniques can simulate various operational conditions, allowing engineers to visualize how changes in flow rates or particle sizes might affect separation efficiency.
Moreover, data science plays a crucial role in optimizing maintenance schedules. By analyzing operational data, teams can identify patterns that indicate when a separator is likely to need maintenance. This predictive maintenance can prevent costly downtimes and extend the equipment's life span.
Integrating data science not only enhances understanding of dynamics but also informs better design decisions. Collaboration between data scientists and engineers can lead to innovative algorithms that improve separation processes and facilitate the adaptation to new materials or operational challenges.
In essence, interdisciplinary approaches incorporate a broad spectrum of knowledge and expertise, ensuring that inertial particle separators not only meet current demands but are also prepared for future challenges. In such a complex field, collaboration is not just advantageous; it is essential.
User Perspectives and Feedback
User perspectives and feedback play a crucial role in enhancing the efficacy and utility of inertial particle separators. Understanding how various stakeholders interact with and perceive these technologies can guide future developments, optimize designs, and refine operational processes. By capturing insights from users, manufacturers can align their products with real-world needs, ensuring that the separators perform not only according to specifications but also in practical, everyday applications.
Insights from Industry Professionals
Industry professionals bring a wealth of knowledge gained from direct experiences with inertial particle separators. Their insights often shed light on both the strengths and weaknesses of different systems. For instance, an engineer in the chemical processing sector may highlight how separators effectively reduce contaminants in process streams, thus enhancing product purity and compliance with regulations. They might stress the operation's simplicity, but also mention the challenges of initial setup and calibration.
Moreover, discussions may point out the importance of training staff adequately, as improper handling can compromise efficiency.
- Customizability: Professionals also suggest the need for adaptable designs that can accommodate various particle sizes and fluid viscosities, reflecting the diverse nature of their applications.
- Maintenance Issues: They note that regular maintenance training is essential, as neglect can lead to performance drop-off.
- Feedback Loops: Continuous communication between end-users and designers forms a feedback loop that fosters innovation and keeps technology on the cutting edge.
Customer Experiences
Customer experiences offer another layer of perspective, often revealing the impact of inertial particle separators on daily operations. Firms that have invested in these systems share their journeys, which can range from initial skepticism to eventual satisfaction. A manufacturing plant manager might recount how integrating a high-capacity inertial particle separator into their workflow drastically reduced downtime due to contamination issues. This not only saved costs but also improved overall productivity.
On the flip side, some customers express frustration when facing complex troubleshooting processes or when expected performance levels aren't met initially. Their experiences underscore the importance of clear documentation and customer support. A few points from customer feedback include:
- Ease of Use: Customers appreciate straightforward interfaces and intuitive controls.
- Technical Support: Quick access to expert assistance is often a deciding factor in satisfaction.
Collectively, these perspectives highlight the ongoing conversation between technology suppliers and users. By listening closely and adapting based on feedback, developers can refine designs and enhance the functionality of inertial particle separators. This collaborative approach not only leads to better products but also fosters a sense of partnership among stakeholders.
Finale and Summation
Wrapping up the exploration of inertial particle separators, it’s clear that they play a significant role across various scientific fields and industries. This section not only reflects on the importance of these separators in practical applications but highlights a few key elements that are crucial for understanding their mechanisms, benefits, and overall impact.
First and foremost, inertial particle separators are essential for the efficient removal of unwanted particles from gaseous and liquid streams. This application is not just about purity but relates to the broader implications of health, safety, and environmental compliance. For instance, in chemical processing, the ability to maintain high material integrity while minimizing contamination speaks volumes about both operational efficiency and product quality.
Moreover, from an engineering perspective, the diversity in designs and configurations shows adaptability to various operating conditions. This capacity is especially valuable in industries facing stringent regulations and performance requirements. Understanding how different components function together provides insight into optimizing systems for better throughput and lower operational costs.
In summary, this article reinforces the idea that inertial particle separators are not merely mechanical devices; they embody a fusion of engineering, physics, and practical application that ultimately enhances productivity and sustainability in numerous sectors. As companies and researchers increasingly look towards optimizing their processes, the knowledge gleaned from this exploration will serve as a foundation for future innovations and improvements.
Key Takeaways
- Inertial particle separators are vital for maintaining product quality in various industries such as chemical processing and environmental engineering.
- Their design allows for customization based on specific operational requirements, which helps to optimize performance and efficiency.
- Understanding the fundamental principles behind these separators can lead to innovative solutions for enhancing productivity and meeting regulatory obligations.
Future Research Opportunities
The current landscape of inertial particle separators presents several avenues for future research. Here are a few potential directions:
- Innovative Designs: Exploring new configurations that maximize separation efficiency while minimizing energy consumption.
- Material Advancements: Investigating better materials that could withstand harsh operational environments and enhance durability.
- Integration with AI Technologies: Utilizing machine learning models to predict performance outcomes based on varying operational parameters.
- Comprehensive Lifecycle Assessments: Conducting studies to quantify the environmental impacts from the production to disposal of these separators.
- Educational Resources: Developing materials for students and professionals focusing on the principles and applications of inertial separation technologies.
Advancing in these areas can significantly contribute to the effectiveness of inertial particle separators, leading to better practices that align with sustainability goals.
"The future belongs to those who believe in the beauty of their dreams." — Eleanor Roosevelt
"The future belongs to those who believe in the beauty of their dreams." — Eleanor Roosevelt
Continuing to push the boundaries of what is possible in this field could pave the way for significant improvements in industrial practices and environmental stewardship.