Manufacturing Stainless Steel: A Comprehensive Guide
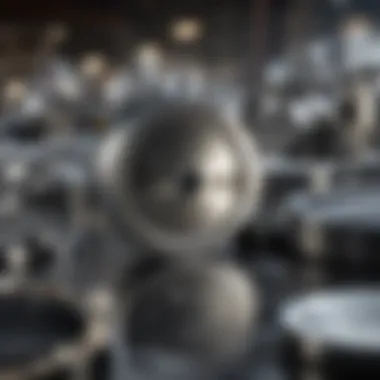
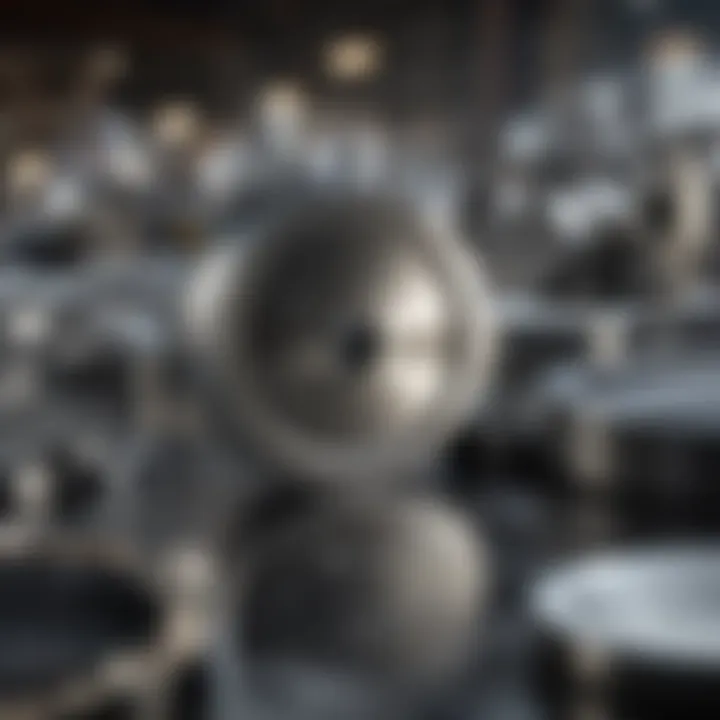
Intro
Stainless steel is more than just a shiny surface you see on kitchen sinks or cutlery. Itâs an embodiment of innovation in materials engineering, balancing aesthetic appeal with functional resilience. Its journey from raw materials to a finished product is a fascinating saga, ingraining itself in nearly every facet of modern life. This exploration will lead you through critical landmarks in the manufacturing process of stainless steel, illuminating the depths of its importance in contemporary applications.
In a world that continually demands durability and sustainability, the significance of stainless steel cannot be overstated. Its anti-corrosive nature and ability to withstand extreme temperatures make it indispensable in industries ranging from construction and automotive to medicine. But what exactly goes into making this formidable material? Let's break it down.
Key Concepts
Definition of the Main Idea
Stainless steel is an alloy primarily composed of iron, chromium, and, in some cases, nickel. The addition of chromiumâtypically at least 10.5%âis what grants stainless steel its remarkable resistance to rust and corrosion. The manufacturing process involves multiple stages: selecting materials, blending ingredients, smelting in furnaces, and creating the final product via casting or rolling techniques. Understanding these stages is vital to appreciating the complexity and ingenuity behind stainless steel.
Overview of Scientific Principles
The creation of stainless steel hinges on various scientific principles, particularly the metallurgy associated with alloys. At a basic level, metallurgy examines how different metals behave when combined. In stainless steel, the interrelationship between iron, chromium, and any supplemental elements results in unique characteristics.
The preservation of properties like tensile strength and ductility during the manufacturing process relies heavily on controlled heating and cooling cycles. These cycles impact the crystalline structure of the metal, influencing its durability under stress and resistance to environmental factors.
**"The strength of stainless steel lies not only in its composition but in the meticulous care taken during its fabrication. Each decision, from material selection to cooling rates, plays a crucial role in the final product."
**"The strength of stainless steel lies not only in its composition but in the meticulous care taken during its fabrication. Each decision, from material selection to cooling rates, plays a crucial role in the final product."
Current Research Trends
Recent Studies and Findings
Research in stainless steel manufacturing is continuously evolving. Recent studies have focused on the development of more sustainable processes. For instance, the use of recycled stainless steel has gained traction. With an ever-increasing emphasis on minimizing waste and lowering carbon footprints, many manufacturers are exploring efficient recycling methods which can reduce energy consumption significantly.
Additionally, innovations in alloy composition are drawing researcher attention. By experimenting with different elementsâsuch as titanium, molybdenum, and manganeseâscientists aim to enhance the corrosion-resistance properties of stainless steel, making it suitable for even more demanding applications.
Significant Breakthroughs in the Field
One notable breakthrough involves advancements in additive manufacturing. The introduction of 3D printing technology to stainless steel production allows for the creation of complex geometries that traditional methods cannot achieve. This could potentially revolutionize industries like aerospace or healthcare, where bespoke components are often required.
Overall, as we delve deeper into the manufacturing process of stainless steel, it becomes clear that the journey is as intricate as the material itself. From its scientific principles to the latest research trends, this exploration will equip you with a deeper understanding of what it takes to produce this essential alloy.
Intro to Stainless Steel
Stainless steel is ubiquitous in today's world, playing a crucial role in various industries, from construction to culinary applications. Understanding this material and its manufacturing process is not just a matter of knowledge but is also essential for anyone involved in design, engineering, or any field where durability and aesthetics are important. The importance of comprehending stainless steel extends beyond its basic properties; it involves appreciating how its characteristics influence practical applications and technological advancements.
Definition and Characteristics
Stainless steel is defined as a steel alloy containing a minimum of 10.5% chromium, which provides it with exceptional resistance to corrosion. It is this corrosion resistance combined with its mechanical strength that sets stainless steel apart from other materials. Commonly, stainless steel is categorized into various grades such as austenitic, ferritic, and martensitic, each serving different purposes based on their unique properties.
Some of the key characteristics of stainless steel include:
- Corrosion Resistance: The chromium content forms a thin layer of oxide on the surface, protecting it from rust.
- High Durability: Stainless steel can withstand high levels of stress without deformation.
- Aesthetic Appeal: Its shiny, smooth finish makes it a preferred choice in architecture and design.
- Temperature Resistance: This material maintains integrity in extreme heat and cold, making it suitable for a variety of environments.
Stainless steel's versatility is further augmented by its ability to be molded into various forms, including sheets, pipes, and rods. This adaptability encourages its extensive use across industries, making it indispensable in modern manufacturing and engineering.
Historical Context and Development
The evolution of stainless steel traces back to the early 20th century. The invention of this alloy is often credited to Harry Brearley in 1913, who stumbled upon the unique properties of the material while investigating wear-resistant materials for gun barrels. This serendipitous discovery marked the beginning of a new era in metallurgy.
Subsequent developments led to different stainless steel grades, responding to the increasing demands for specialized properties. The expansion of stainless steel applications took off in the mid-1900s with the advent of industrialization, particularly in the food processing and medical sectors. The ability to create equipment that could withstand corrosive conditions without compromising hygiene changed the landscape of manufacturing processes forever.
In the decades that followed, stainless steel became a staple in construction and architecture, used in everything from skyscrapers to kitchen utensils. Its combination of functionality and beauty allows designers and engineers to explore innovative solutions to modern challenges.
Thus, understanding the introduction and evolution of stainless steel provides critical insights into its applications and potential for future developments.
Raw Materials in Stainless Steel Production
The manufacturing of stainless steel hinges significantly on the raw materials utilized. The extraction, refinement, and combination of these elements shape the properties that make stainless steel a sought-after choice in various industries. Understanding these raw materials helps unravel the complexities of this robust material and emphasizes its importance in modern-day applications.
Several elements play pivotal roles during stainless steel production, with iron, chromium, and nickel taking center stage. The interplay among these key ingredients not only results in the unique features of stainless steel but also raises questions about sustainability and sourcing.
Key Elements: Iron, Chromium, Nickel
Stainless steel is primarily an alloy of iron mixed with varying amounts of chromium and nickel. Iron serves as the fundamental building block owing to its abundance and mechanical strength. This metal, however, isnât enough on its own. Adding chromium, at least 10.5% by weight, is what gives stainless steel its characteristic corrosion resistance. It forms a thin, passive layer of chromium oxide that protects the iron from rusting and deterioration, something thatâs invaluable for applications in harsh environments.
Nickel, generally ranging from 8% to 12%, has its own set of benefits which includes enhancing the ductility and toughness of the alloy. This combination of iron, chromium, and nickel results in various grades of stainless steel, each tailored for specific needs.
"The blend of these elements reflects the balance between cost and performance, forming the backbone of modern engineering materials."

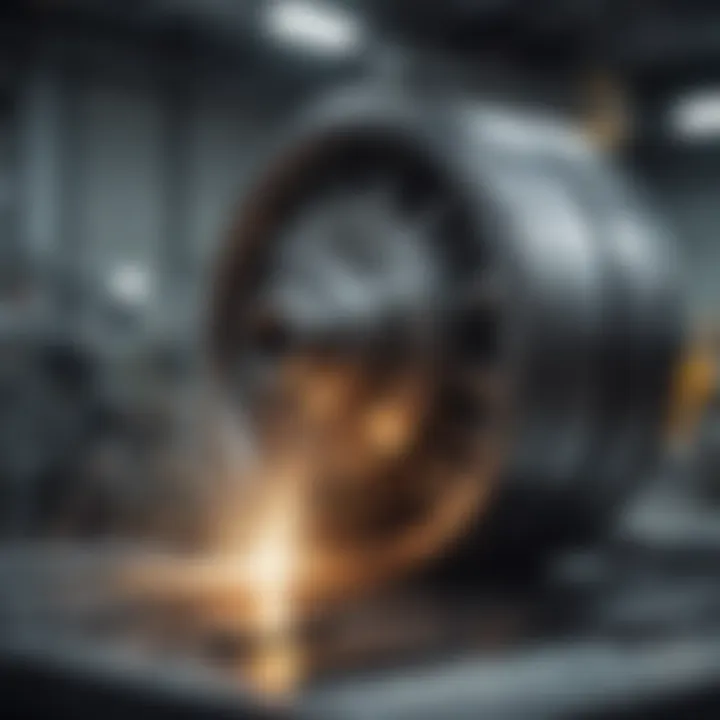
"The blend of these elements reflects the balance between cost and performance, forming the backbone of modern engineering materials."
Utilizing these key elements impacts the price and availability of stainless steel. As demand fluctuates, the sourcing of raw materials like nickel can become a worry considering geopolitical factors and mining practices.
Recycling Scrap Metal
In the context of raw materials, one cannot overlook the significance of recycling scrap metal. The stainless steel industry is quite efficient in recycling, with estimates suggesting that over 70% of the new stainless steel is made from recycled materials. This not only alleviates the pressure on primary resources but also minimizes environmental impacts associated with the extraction and refinement of metals.
Recycling scrap metal involves the collection and processing of discarded stainless steel items like appliances, automotive parts, and other products. Once gathered, these materials undergo a meticulous sorting process followed by shredding. The resultant shreds are melted down in electric arc furnaces, where the desired composition is carefully re-established. This method not only conserves natural resources but also significantly reduces greenhouse gas emissions compared to traditional manufacturing methods.
The use of recycled content in stainless steel production stands as a testament to the industry's commitment to sustainability. As stakeholders push towards greener manufacturing practices, recycling will continue to play a crucial role in shaping the future of stainless steel, ensuring that the valuable properties weâve come to depend on remain closely tied to responsible resource management.
Stainless Steel Manufacturing Process
The stainless steel manufacturing process sits at the heart of the entire industry, shaping not only the physical properties of the material but also its applicability across various sectors. Understanding this process is crucial, as it encompasses everything from the first extraction of raw materials to the final touches of finishing techniques. Each stage plays a significant role in ensuring that the final product meets stringent quality standards and is suitable for its intended use.
The nuances of this process come with myriad benefits. A well-executed manufacturing line can enhance material durability, increase resistance to corrosion, and expand versatility in application. Therefore, keeping abreast of advancements in manufacturing techniques enables companies to optimize performance and reduce waste while adhering to environmental considerations.
Extraction and Alloying
The journey of stainless steel begins with the extraction of raw materials, primary among them being iron ore, chromium, and nickel. The quality and purity of these materials are vital; any impurities can compromise the final product's strength and resistance. To extract these materials, various methods such as open-pit mining and underground mining are employed.
Once the raw materials are sourced, the alloying process commences. It's a delicate balance of combining different elements to create specific grades of stainless steel. For instance, mixing varying proportions of chromium and nickel yields distinct characteristics in the alloyâsome grades exhibit better ductility, while others heighten corrosion resistance. This precision in alloy formulation is essential for meeting industry standards, ensuring that the stainless steel can handle its designated roles from kitchen appliances to aerospace components.
Melting Techniques: Electric Arc and Induction
Following alloying, the next stage is melting, where the raw alloy is transformed into molten form, preparing it for shaping. There are predominantly two techniques employed: electric arc melting and induction melting.
Electric arc furnaces utilize electrical arcs to produce immense temperatures, melting the scrap metal along with other raw materials. This method is favored for its capacity to recycle scrap, making it a greener choice compared to traditional methods. On the other hand, induction melting employs electromagnetic fields to heat the alloy, offering finer temperature control and reducing contamination risks. While both techniques have their merits, the choice often hinges on the intended properties of the final product and production scale.
Forming Processes: Casting and Rolling
After melting, we move into the forming phase, where the molten metal is cast into specific shapes or rolled into sheets. Two primary processes dominate this stage: casting and rolling.
- In casting, the molten stainless steel is poured into molds and allowed to solidify. This method can produce intricate shapes that would be challenging to achieve through other means. It is particularly advantageous for large components.
- Rolling, however, takes the solidified metal and passes it through rollers to create sheets of various thicknesses. This technique is essential for applications where large surfaces or specific thicknesses are required, such as in construction materials or kitchenware.
Both forming methods are crucial in defining the physical characteristics of the final product, ensuring it meets the diverse requirements set forth by different industries.
Finishing Techniques: Annealing and Pickling
Once the stainless steel has been formed, it enters the finishing phase involving techniques such as annealing and pickling.
- Annealing is a crucial step where heat is applied to relieve internal stresses, increasing ductility and toughness. This process not only improves the mechanical properties but also helps in enhancing corrosion resistance by allowing chromium to oxidize and form a protective layer.
- On the other hand, pickling serves to cleanse and refine the surface of the metal. It involves chemical treatment to remove oxides and scaling, ensuring a smooth and polished finish. The choice of pickling agents and process duration can deeply affect the end quality of the stainless steel.
"Understanding the stainless steel manufacturing process is not just about knowing the steps; it's about appreciating the intricate science that makes this versatile material so indispensable across sectors."
"Understanding the stainless steel manufacturing process is not just about knowing the steps; it's about appreciating the intricate science that makes this versatile material so indispensable across sectors."
Through each of these stagesâextraction, alloying, melting, forming, and finishingâthe stainless steel undergoes a transformation that reflects the expertise of its makers. Each step necessitates careful consideration to produce a final product that serves its purpose effectively, marking the vital richness behind what appears to be just another metal.
Quality Assurance in Stainless Steel Production
Quality assurance in stainless steel production is not just a procedural step; itâs a critical component that can define the overall product quality and safety standards. In industries where stainless steel is a main player, like construction or medical device manufacturing, the integrity of the material is non-negotiable. A failure in such industries can lead to catastrophic outcomes, making quality assurance indispensable for maintaining trust and compliance.
From the raw material selection right through to the finished product, every stage of stainless steel production requires strict adherence to quality control norms. Simply put, it ensures that the product fulfills its intended purposeâwhether itâs resisting corrosion, maintaining strength, or ensuring a certain aesthetic.
Material Testing Methods
Material testing methods are the backbone of quality assurance in stainless steel production. This step comprises a variety of tests that ascertain not just the physical properties of stainless steel, but also its chemical makeup. The aim is to ensure that the alloy meets or exceeds expected standards.
Some prominent testing methods include:
- Chemical Analysis: Using techniques like Optical Emission Spectrometry, producers can analyze the exact composition of the stainless steel to verify that the necessary elements, such as chromium and nickel, are present in their required quantities.
- Mechanical Testing: Tests like tensile strength tests and hardness tests examine the material's performance under various stresses and loads.
- Non-Destructive Testing (NDT): This vital method allows for the detection of internal flaws without harming the material. Methods like ultrasonic and magnetic particle testing are common here.
By executing these tests diligently, manufacturers can reduce the risk of defects, ensuring a reliable end product that adheres to safety regulations. For instance, insufficient nickel content could lead to the steel being susceptible to corrosion, especially in marine environments.
Standards and Certifications
Following rigorous material testing, adhering to established standards and certifications ensures that stainless steel products meet industry requirements. There are several international standards that govern the production of stainless steel, including ASTM (American Society for Testing and Materials), ISO (International Organization for Standardization), and EN (European Norm). Each of these bodies sets specific criteria that manufacturers must comply with.
Certifications can provide more than just a tick in a box. They function as a trusted endorsement that the product is
- Safe for Use: Many sectors, especially medical and food, have stringent regulations that mandate usage of certified materials.
- Marked Improvement in Marketability: Products that are certified often see better acceptance in the market as they are backed by rigorous quality assurance methods.
- Reduction of Liability: Should a defective product result in legal claims, having certifications can mitigate legal risks significantly.


"A good quality assurance system is not an expense; it's an investment in the longevity and reputation of your manufacturing process."
"A good quality assurance system is not an expense; it's an investment in the longevity and reputation of your manufacturing process."
These standards and certifications build a framework within which stainless steel production can flourish, continuously evolving while still ensuring that quality remains a foremost priority.
Applications of Stainless Steel
The applications of stainless steel span various fields, demonstrating its unmatched versatility and reliability. In this article, we'll delve into three critical areas where stainless steel plays a pivotal role: construction and architecture, medical devices, and culinary applications. Understanding these applications is vital, as they showcase how the properties of stainless steel benefit our daily lives and industries.
In Construction and Architecture
Stainless steel has become a cornerstone in construction and architectural design for several compelling reasons. Its remarkable corrosion resistance, high strength-to-weight ratio, and aesthetic appeal make it an ideal choice for various applications.
For instance, stainless steel is frequently used in building facades and structural components. Its longevity ensures that structures remain visually appealing for years, requiring less frequent maintenance. Not to mention, the ability to withstand harsh environmental conditions, such as high humidity or salty air near coastal regions, makes it a preferred material for skyscrapers and bridges.
Furthermore, stainless steel offers design flexibility. Architects often appreciate its sleek, modern look, which can effortlessly blend with both contemporary and traditional styles. Here are some common applications:
- Roofing and Cladding: Provides excellent weather resistance and an attractive finish.
- Handrails and Balustrades: Offers safety and durability without compromising design aesthetics.
- Structural Support: Used in beams and columns for its high tensile strength.
The unique ability of stainless steel to be recycled without loss of quality adds to its appeal, making it a sustainable choice for construction.
The unique ability of stainless steel to be recycled without loss of quality adds to its appeal, making it a sustainable choice for construction.
In Medical Devices
The medical industry heavily relies on stainless steel due to its hygiene, durability, and biocompatibility. Surgical tools, implants, and diagnostic equipment are often crafted from this material, ensuring safety and efficiency during medical procedures.
One major advantage of stainless steel in healthcare is its resistance to corrosion and staining, which is essential in hospitals where sanitation is a top priority. For example, instruments like scalpels, forceps, and needles are primarily manufactured using stainless steels like 316L, which is not only resistant to rust but also easy to sterilize.
- Implants: Stainless steel is used in various implants, such as orthopedic pins and plates, as it can integrate into the body without causing harm.
- Surgical Instruments: Tools crafted from stainless steel are designed for durability and precision, making them a reliable option for surgeons.
- Hospital Equipment: From carts to sterilizing equipment, stainless steel provides long-lasting solutions that can withstand rigorous cleaning processes.
In Culinary Applications
Stainless steel's influence in the culinary world is profound. As kitchen and dining essentials, pots, pans, and utensils crafted from stainless steel are not only practical but also timeless.
The material's non-reactive nature prevents food from acquiring metallic tastes, and it is highly resistant to staining, making it the go-to choice for many chefs. Plus, stainless steel cookware distributes heat evenly, which is key to preparing delicious meals.
In addition, stainless steelâs strength allows for products that can endure frequent use and maintain their integrity over time. The sleek, polished finish also adds a touch of elegance to both home and professional kitchens.
Some common culinary applications include:
- Cookware: Offering durability and heat resistance, allowing for versatile cooking techniques.
- Cutlery: Stainless steel knives and forks provide longevity and maintain a sharp edge.
- Food Storage: Containers made from stainless steel offer durability and are often designed to be portable and stackable.
In summary, the applications of stainless steel showcase its indispensable nature across various industries. Whether enhancing structures, ensuring safety in medical environments, or elevating culinary experiences, stainless steel remains a material of choice, cherished for its properties and versatility.
Environmental Impact of Stainless Steel Production
The manufacture of stainless steel plays a significant role in shaping both the economy and environment. Itâs essential to analyze how the production process relates to environmental sustainability. The stainless steel industry has often faced scrutiny over its energy consumption and waste byproducts. Yet, there has been a shift towards more eco-friendly practices, reflecting an increasing awareness of the environmental footprint. Ensuring environmentally responsible production methods not only supports regulatory compliance but enhances public perception and marketability of the steel itself.
Sustainability Measures in Manufacturing
In the quest for greener steel production, sustainability measures have become a focal point. Companies are increasingly adopting practices that reduce their overall impact on the environment. Some methods include:
- Energy Efficiency: Many manufacturers are investigating renewable energy sources to power their operations, such as solar and wind energy. Efforts to improve energy efficiency in existing processes can also lead to significant reductions in emissions.
- Process Optimization: By optimizing production processes, plants can minimize scrap production and lower material waste. This includes refining the fabrication techniques used in forming and processing stainless steel.
- Innovative Material Use: Incorporating recycled materials into the production pipeline proves to be a valuable strategy. The use of scrap metal in creating new stainless steel helps conserve natural resources and reduces the overall energy costs of extraction and processing.
- Water Conservation: Water is a crucial element in the manufacturing process, and many companies have set ambitious targets to reduce consumption and manage wastewater effectively.
These measures not only improve the sustainability profile of the companies involved but also often result in economic benefits through reduced operational costs and increased efficiency.
Recycling and Waste Management
Recycling plays a pivotal role in the stainless steel production cycle. It is one of the most recycable materials, and its recovery processes have been refined to maximize yield. Here are crucial points to consider about recycling and waste management in this field:
- Recycling Rate: Stainless steel has a remarkable recycling rate, estimated to be around 90%. This means that time-tested steel can find new life instead of ending up in landfills, reducing the demand for raw materials.
- Closed-loop Systems: Each stage of the production can integrate closed-loop systems, allowing materials to be repeatedly recycled. This results in better resource management and diminished environmental impacts associated with mining and material transport.
- Awareness of E-Waste: As technology evolves, stainless steel is becoming prevalent in electronic devices. Manufacturers are focusing on developing efficient processes to recover steel from e-waste.
- Waste Minimization Strategies: By implementing strategic waste management practices, companies not only comply with regulations but also contribute to a circular economy where waste is minimized and resource use is optimized.
"Sustainable practices are no longer just a trend; they are the future of manufacturing."
"Sustainable practices are no longer just a trend; they are the future of manufacturing."
In summary, the environmental impact of stainless steel production is multifaceted. While challenges exist, the industry's evolving approach towards sustainability and recycling promises a more responsible and efficient future. This benefits not just the manufacturers, but society as a whole, through reduced environmental degradation.
Advancements in Stainless Steel Technologies
In the realm of stainless steel production, advancements are more than just technical improvements; they reflect the industry's response to changing demands, environmental challenges, and the quest for enhanced material performance. These innovations are pivotal as they not only contribute to efficiency but also enhance the qualities that make stainless steel a sought-after material in various applications.
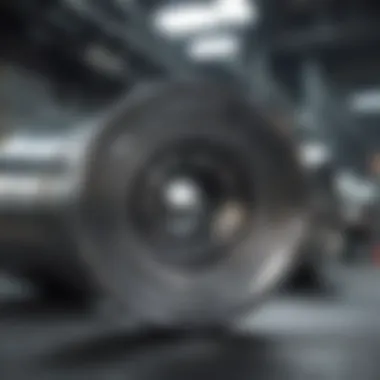
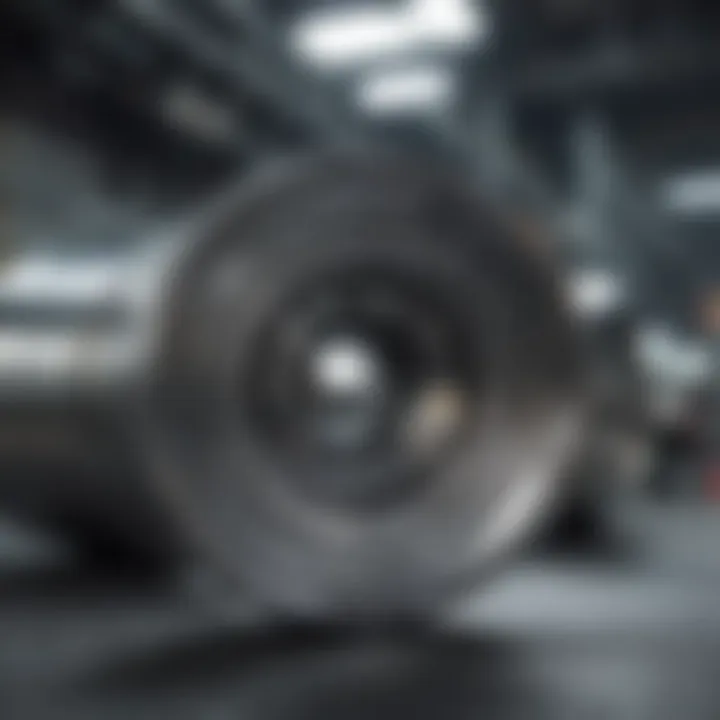
Innovations in Production Techniques
The journey of stainless steel starts with raw materials, but the real magic happens during production. Recent innovations in production techniques have redefined the way stainless steel is manufactured. For instance, the introduction of precision casting has allowed manufacturers to create complex shapes with minimal waste. This method isn't just cost-effective; it also reduces the carbon footprint associated with traditional casting methods.
Moreover, automation and robotics have become integral in the manufacturing process. Automated systems improve consistency, minimize human error, and streamline operations. For example, robotic arms are now used in welding and assembly, resulting in more precise seams and improved durability.
One noteworthy technique on the rise is 3D printing, which offers unprecedented customization possibilities. Unlike traditional processes, 3D printing facilitates the creation of bespoke components that may not be possible with conventional methods. This technology is particularly useful in industries requiring unique or low-volume parts, such as aerospace and medical devices.
"The advancements in production techniques are not just about faster output; they are about creating superior products that meet the stringent requirements of modern applications."
"The advancements in production techniques are not just about faster output; they are about creating superior products that meet the stringent requirements of modern applications."
Emerging Trends in Alloy Development
While production techniques evolve, the alloys themselves are also undergoing transformations. The development of high-performance alloys is an exciting trend. These advanced materials often incorporate elements such as nitrogen, manganese, and even titanium, which enhance the corrosion resistance and strength of stainless steel. As industries like oil and gas push for materials capable of withstanding harsher conditions, these specialized alloys are gaining traction.
Another significant trend is the focus on lightweight materials. With increasing emphasis on reducing weight without sacrificing strength, manufacturers are experimenting with lower densities in alloy composition. This shift is particularly beneficial for the automotive and aerospace sectors, where every ounce matters.
Furthermore, thereâs a growing market for bio-compatible stainless steel alloys in medical applications. These materials are designed to meet specific health standards, ensuring safety for use within the human body. The nuances in alloy compositionâtailored for particular applicationsâdemonstrate how advancements in alloy development can impact various fields profoundly.
As technology propels the industry forward, new sustainability measures are also being integrated into alloy production. With awareness of environmental footprints on the rise, producers are searching for ways to incorporate recycled materials without compromising quality. This innovative approach aims to balance performance and environmental responsibility, thus reshaping the future of stainless steel production fundamentally.
Global Landscape of Stainless Steel Production
The stainless steel industry plays a critical role in the global economy, impacting numerous sectors from construction to manufacturing. Understanding the global landscape of stainless steel production not only highlights which countries are the key players in this arena but also uncovers the economic intricacies tied to demand and innovation in the industry. This section of the article will delve into the major producers and regions involved in stainless steel manufacture, as well as the driving market demand and economic factors that influence production levels and trends.
Major Producers and Regions
When we consider the major producers of stainless steel, names like China, Japan, and the United States come to mind. China's production far outstrips that of any other nation, accounting for over half of the world's supply. This dominance can largely be attributed to its substantial industrial base and continuous investments in production capabilities. Moreover, countries such as India and South Korea have also carved out significant shares in the market, driven by advancements in technology and an expanding local demand.
- China: A powerhouse in production, employing vast resources and workforce.
- Japan: Known for quality and precision, often targeting high-performance applications.
- United States: Focused on advanced manufacturing techniques, emphasizing sustainability.
- India: Rapid growth fueled by urbanization and increasing industrial activity.
- South Korea: Betters its technology, focusing on export markets alongside domestic needs.
These key regions not only produce substantial quantities of stainless steel but also set trends that resonate globally. For instance, the rise of eco-friendliness in production, such as through efficient recycling processes and lowering carbon footprints, begins in these major manufacturing hubs and influences global practices.
"In an interconnected world, the actions of a few producers can ripple across the entire industry, altering both prices and innovation paths."
"In an interconnected world, the actions of a few producers can ripple across the entire industry, altering both prices and innovation paths."
Market Demand and Economic Factors
Market demand for stainless steel is intricately tied to broader economic factors, often fluctuating with industrial growth and consumer trends. The automotive and construction industries are primary consumers, both requiring high-strength yet malleable materials that stainless steel provides. Additionally, advancements in technology also create niche markets such as food processing and medical equipment, leading to increased demand.
Several factors influence this ever-evolving market:
- Economic Growth: Increased activities in construction lead to higher demand for stainless steel.
- Technological Integration: New applications in diverse fields create additional demand.
- Trade Policies: Tariffs and regulations can alter competitiveness among countries.
- Sustainability Concerns: Rising awareness pushes industries toward environmentally friendly materials and processes.
To put it plainly, the success and challenges of stainless steel manufacturing are not happening in isolation. They are part of a larger economic narrative that reflects global trade patterns and shifts in consumer preferences. As we move forward, examining these trends provides insight into the potential directions of the industry.
Future Outlook in Stainless Steel Manufacturing
The future of stainless steel manufacturing is a topic that combines various elements, from technological advancements to environmental considerations. This section sheds light on what lies ahead in an industry pivotal to many sectors, including construction, automotive, and healthcare. The need for strong and corrosion-resistant materials with improved sustainability drives innovation and research in this realm.
Challenges Facing the Industry
Despite its robust applications, the stainless steel manufacturing industry grapples with a multitude of challenges. One prominent issue is the volatile nature of raw material prices, particularly nickel and chromium. Fluctuations can lead to unpredictable cost structures, impacting budget forecasts and pricing strategies.
Additionally, stringent environmental regulations complicate the landscape. Factories face mounting pressure to minimize their carbon footprints and waste outputs, requiring significant investment in cleaner technologies. There's also an ongoing labor shortage, with skilled workers becoming harder to find as experienced staff retire, leading to a knowledge gap.
Some of the main challenges include:
- Raw material pricing instability
- Regulatory compliance and environmental constraints
- Workforce shortages and skills gap
- Competition from alternative materials like aluminum and plastics
These factors necessitate adaptive strategies for producers to remain competitive.
Potential Developments and Solutions
To navigate these challenges, the stainless steel industry is likely to witness several key developments and innovative solutions. First, embracing advanced technologies like automation and AI can streamline processes, improve efficiency, and reduce costs. By implementing smart manufacturing practices, companies can better manage resource allocation and waste reduction.
Moreover, investing in research and development is crucial for formulating new stainless steel alloys that are both cost-effective and environmentally friendly. For example, new âlow-carbonâ stainless steels are being designed to use fewer harmful materials while still maintaining essential properties.
Another exciting avenue is the enhanced focus on recycling practices. As demand for sustainable practices grows, recycling scrap stainless steel can significantly alleviate pressure on raw material markets and reduce energy use during production. This circular economy approach not only helps the environment but simultaneously stabilizes costs.
A few key developments to watch include:
- Artificial intelligence in material testing
- Sustainable alloys with lower environmental impact
- Increased recycling efforts and processes
- Collaboration with research institutions for innovative solutions
"Innovation is the backbone of resilience in the stainless steel industry; new methods and materials are not just beneficial, they are essential."
"Innovation is the backbone of resilience in the stainless steel industry; new methods and materials are not just beneficial, they are essential."
With these innovations on the horizon, the industry stands at a precipice, ready to evolve and adapt to an ever-changing global market.