Metal Laminates: Comprehensive Overview and Trends
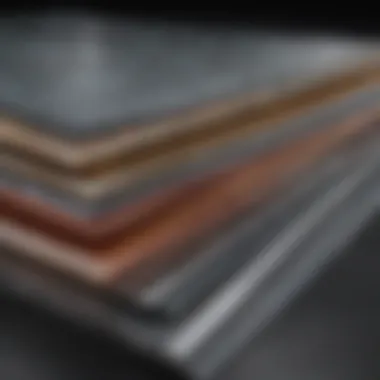
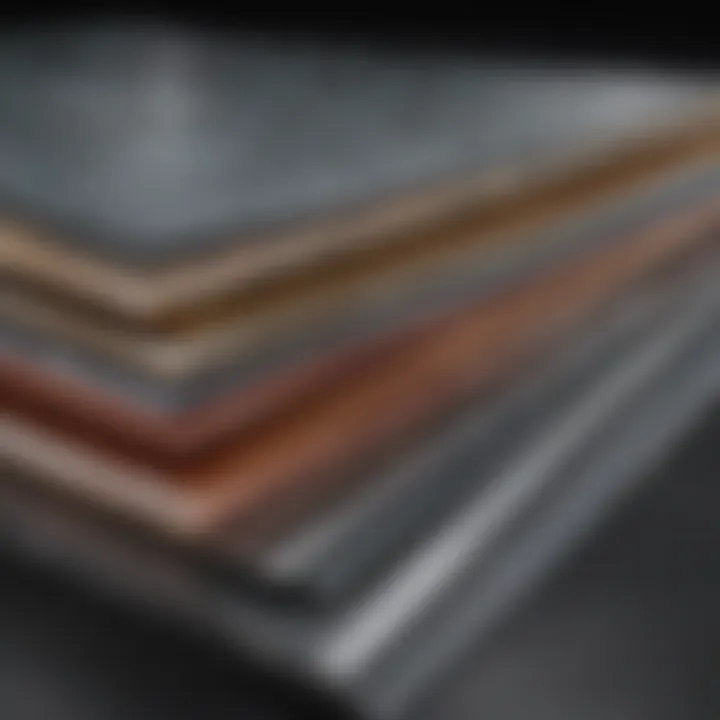
Intro
Metal laminates represent a significant advancement in material science, combining various metals to create a versatile product with enhanced properties. Their unique structure allows for a wide range of applications, making them critical in many industries, from aerospace to automotive. This section introduces the essential concepts that underpin the understanding of metal laminates.
Key Concepts
Definition of the Main Idea
Metal laminates consist of multiple layers of different metals bonded together. This layering can enhance strength, durability, and resistance to corrosion. These properties make metal laminates useful for constructing surfaces that need to endure harsh conditions.
Overview of Scientific Principles
The manufacturing of metal laminates relies on several scientific principles, such as metallurgy and material bonding techniques.
Some relevant principles include:
- Adhesion: The process by which the layers bond together.
- Thermal expansion: Different metals expand at different rates, a factor that must be considered during product design.
- Stress distribution: The laminate structure can help distribute stress throughout the material, enhancing overall stability.
Understanding these principles is crucial for anyone involved in the design and engineering processes relating to metal laminates.
"Metal laminates not only incorporate aesthetic considerations but also structural integrity, showcasing an evolution in material design."
"Metal laminates not only incorporate aesthetic considerations but also structural integrity, showcasing an evolution in material design."
Current Research Trends
Recent Studies and Findings
Recent research has focused on improving the properties of metal laminates. Researchers are exploring combinations of metals that can yield better results in terms of weight reduction and strength enhancement. Notably, the integration of lightweight alloys into laminated structures is gaining attention.
Significant Breakthroughs in the Field
Innovations in adhesive technology have also played a role in the development of metal laminates. New adhesives can withstand even greater stresses and temperature fluctuations, ensuring stronger bonds between layers. For professionals in the field, staying updated on these advancements can provide competitive advantages and enhance product quality.
Through this exploration of metal laminates, we will delve deeper into their manufacturing processes and diverse applications.
Prologue to Metal Laminates
Metal laminates represent a unique intersection of materials engineering and practical application. Their importance in modern industries cannot be overstated. They offer a blend of properties derived from different metals, enabling enhanced performance compared to single-material solutions. This section serves to underscore the essential elements and benefits of metal laminates, framing the discussion with significant considerations.
Metal laminates are essentially composite materials that fuse layers of different metals. This layering allows engineers to create materials that combine the advantageous properties of each metal—such as strength, conductivity, and corrosion resistance. The resulting product can outperform traditional materials in various applications.
Further, distinct characteristics give metal laminates their utility. Notably, they can be tailored to specific needs in areas such as structural integrity, weight reduction, and thermal management. Their application spans diverse industries, including aerospace, automotive, and consumer electronics, making them vital components in cutting-edge technologies.
Definition and Characteristics
Metal laminates can be defined as engineered materials composed of multiple layers of metal, bonded together to create a single, cohesive product. Each layer contributes unique properties, resulting in a composite that can achieve remarkable performance metrics.
Key characteristics of metal laminates include:
- High strength-to-weight ratio: Their layered structure often results in a significant reduction in weight while maintaining or enhancing strength.
- Enhanced durability: By combining different metals, laminates can exhibit improved resistance to wear and tear.
- Tailored thermal properties: Depending on the metals used, these laminates can effectively manage heat flow, crucial in applications like electronics.
The versatility of metal laminates is one of their standout features. For instance, the electromagnetic shielding applications and heat dissipation are just two examples of how the right combination can create a product ready to meet the demands of contemporary technology.
Historical Background
The development of metal laminates can be traced back to the early 20th century, when engineers began experimenting with composite materials to improve mechanical properties. Initial uses were primarily found in aerospace, where minimizing weight while maximizing structural integrity was paramount.
Advancements in bonding technologies and layering techniques during the mid-1900s led to more widespread adoption of metal laminates. This historical progression has seen their applications expand into other sectors, such as automotive and electronics, where innovation necessitated new solutions to performance challenges.
As industries continue to evolve, the quest for materials that contribute to efficiency and performance remains. The journey of metal laminates from experimental materials to essential industrial components reflects a significant shift in material science, driven by the need for advanced solutions in a demanding market.
Metal laminates are more than just materials; they are a testament to the evolution of engineering practices that meet the complex needs of modern technology.
Metal laminates are more than just materials; they are a testament to the evolution of engineering practices that meet the complex needs of modern technology.
In summary, the introduction to metal laminates sets the stage for a comprehensive exploration of their capabilities, historical significance, and the scientific principles behind their properties.
Composition of Metal Laminates
The composition of metal laminates is fundamental to understanding their versatility and functionality across various industrial applications. This section aims to delineate the critical materials and techniques involved in constructing metal laminates. Key aspects include the distinction between different metals, the layering methods employed, and the implications of these choices on the final product's performance.
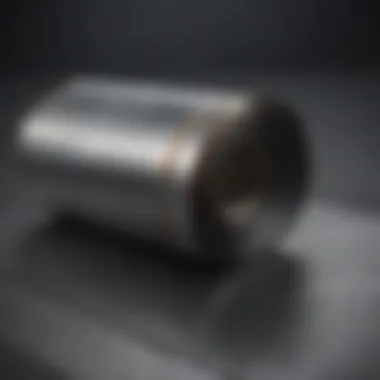
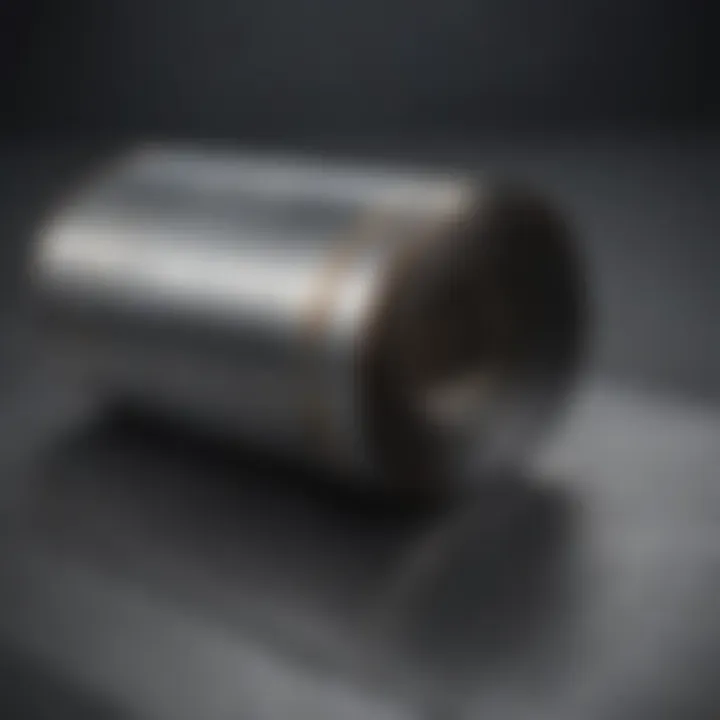
Types of Metals Used
Metal laminates are typically composed of layers of various metals, each selected for its specific properties. Some of the most commonly used metals include:
- Aluminum: Known for its lightweight and corrosion-resistant qualities, aluminum is often used in applications where weight reduction is essential.
- Stainless Steel: This metal offers significant strength and durability, making it suitable for high-stress environments.
- Copper: Copper provides excellent thermal and electrical conductivity, which is vital in electronic applications.
- Titanium: Due to its high-strength-to-weight ratio and resistance to extreme temperatures, titanium is often found in aerospace industries.
The choice of metal influences not only the physical attributes of the laminate but also its cost and potential applications. Matching the metal properties with the intended use of the laminate is crucial for achieving optimal performance and functionality.
Layering Techniques
Layering techniques play a vital role in the production of metal laminates. Different methods are used to bond layers together, each affecting the resulting laminate's performance. Common techniques used include:
- Adhesive Bonding: This method uses special adhesives to bond layers. It provides a seamless finish and allows for flexibility in design.
- Mechanical Bonding: Mechanical fasteners can be used to secure layers together, ensuring structural integrity, but may add weight or impact surface aesthetics.
- Cladding: In this technique, one metal is wrapped around another. This is effective for protecting against corrosion without compromising strength.
- Roll Bonding: The layers are passed through rollers, which compress and bond them together. This technique can produce strong, homogenous laminates.
Each technique comes with its own set of benefits and challenges. For instance, adhesive bonding is effective for thin layers but may not provide the same level of strength as roll bonding. Thus, selecting a layering technique must consider the specific requirements of the end use.
The choice of composition and technique directly affects the durability, weight, and overall performance of the metal laminate, making it an essential area of consideration in design and manufacturing.
The choice of composition and technique directly affects the durability, weight, and overall performance of the metal laminate, making it an essential area of consideration in design and manufacturing.
Manufacturing Processes for Metal Laminates
Manufacturing processes for metal laminates are crucial to understand as they determine the properties and suitability of these materials for various applications. The techniques used can have significant implications on the performance, cost, and efficiency of the final product. Therefore, grasping these processes is essential for researchers and professionals involved in material science and engineering.
Industry Standard Techniques
Industry standard techniques for creating metal laminates are well established and widely adopted by manufacturers. One of the most common methods is cold rolling, where sheets of metal are passed through rollers to achieve the desired thickness and surface finish. This process not only enhances the mechanical properties but also improves the laminate's aesthetics. Cold rolling maintains the grain structure of the metal, contributing to the durability of the laminate.
Additionally, hot rolling is another prevalent standard technique. In this method, metal plates are heated and then subjected to rolling. Hot rolling allows for larger reductions in thickness and is often applied where strong mechanical properties are needed.
Laminating processes can also involve using adhesives or bonding agents to join layers of different metals. An example includes using epoxy resins, which enhance the adhesion between layers, creating a strong interfacial bond. The effectiveness of these adhesives can significantly affect the laminate’s structural integrity.
"The choice of manufacturing technique dictates not only the quality of the laminate but also its long-term functionality in practical applications."
"The choice of manufacturing technique dictates not only the quality of the laminate but also its long-term functionality in practical applications."
Emerging Manufacturing Innovations
With the advancement of technology, emerging manufacturing innovations are reshaping how metal laminates are produced. One noteworthy innovation is the introduction of 3D printing technologies. These methods allow for customized designs and complex shapes that traditional manufacturing cannot achieve easily. Furthermore, 3D printing can reduce material waste, offering a more sustainable approach to production.
Another innovation involves the utilization of laser welding. This technique provides precise and controlled welding capabilities, ensuring strong bonds between metal layers without significant thermal distortion. It can cater to diverse materials and thicknesses, improving flexibility in design.
Integrating nanotechnology into the manufacturing process is also gaining traction. The addition of nanoparticles can enhance certain properties like strength or corrosion resistance, making laminates more versatile across different industries.
In summary, the manufacturing processes for metal laminates are characterized by established standard techniques, such as cold and hot rolling, as well as innovative methods like 3D printing and laser welding. Each method has particular advantages and implications for the material’s lifecyle. Understanding these processes enhance the development and application of metal laminates, ultimately pushing the boundaries of what is possible with these materials.
Applications of Metal Laminates
The applications of metal laminates represent a critical area of exploration within this study. The diverse nature of these materials, coupled with their unique properties, opens numerous possibilities across multiple sectors. Understanding how metal laminates are utilized helps enhance our knowledge about their potential benefits and challenges. They are integral in producing lightweight yet strong components, which is essential in today’s fast-evolving technological landscape.
Industrial Applications
In industrial settings, metal laminates are frequently employed for their strength and versatility. They serve in machinery, construction, and manufacturing sectors, providing enhanced structural integrity while reducing overall weight. Often, layered metals can withstand harsh environments and significant wear.
For instance, the automotive industry relies on metal laminates in components such as chassis and body panels. These laminates not only reduce the vehicle weight but also improve durability and fuel efficiency. In construction, metal laminates can be used in flooring and roofing materials, offering fire resistance and insulation, thus contributing to energy savings in buildings.
Consumer Electronics
The realm of consumer electronics has also seen significant advancements thanks to metal laminates. Devices like smartphones, laptops, and tablets often utilize these materials in their casings and internal components. The use of metal laminates allows manufacturers to design slimmer products without compromising quality and performance.
The combination of lightweight and robust properties makes these laminates ideal for circuit boards and other electrical components. Furthermore, metal laminates enhance thermal management. Effective heat dissipation is vital in compact devices, and metal laminates assist in achieving this by conducting heat away from sensitive areas.
Aerospace and Automotive
In aerospace and automotive industries, the applications of metal laminates are particularly noteworthy due to the stringent requirements for performance and safety. In aerospace, these materials contribute to the creation of lightweight structures that can handle extreme conditions. The reduction in weight leads to lower fuel consumption and greater efficiency.
In the automotive sector, innovative uses of metal laminates enable the production of components that are not only lightweight but also significantly more resilient. Vehicle manufacturers seek to incorporate these materials into frames, engine mounts, and even decorative finishes to improve both performance and aesthetic appeal.
"Metal laminates provide the critical performance requirements needed for modern aerospace and automotive applications, emphasizing weight reduction and enhanced strength."
"Metal laminates provide the critical performance requirements needed for modern aerospace and automotive applications, emphasizing weight reduction and enhanced strength."
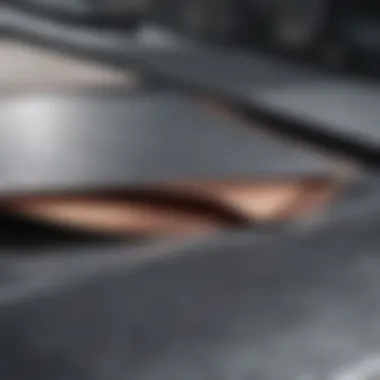
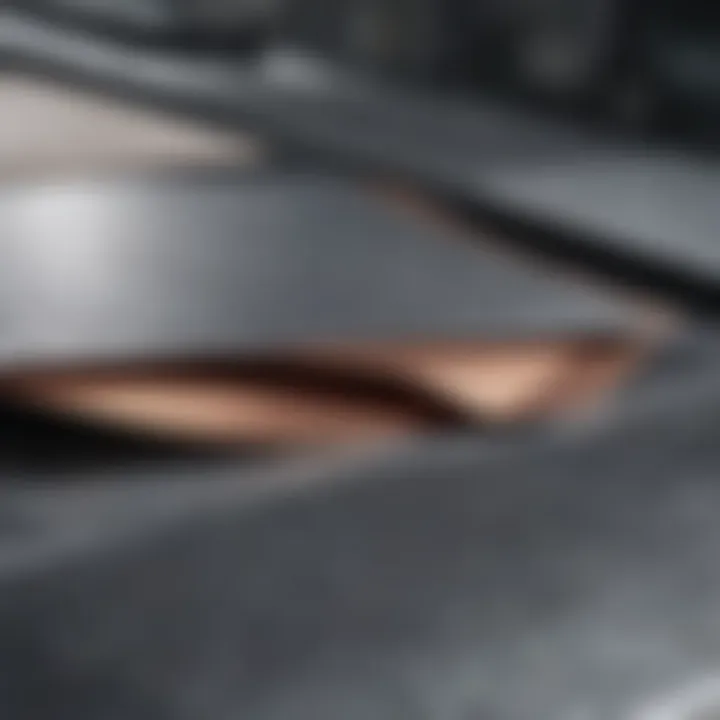
With a focus on advancements in design and technology, metal laminates are poised to play a vital role in future developments in both the aerospace and automotive sectors.
Mechanical Properties of Metal Laminates
The mechanical properties of metal laminates are crucial for understanding their performance in various applications. These properties include strength, durability, thermal conductivity, and electrical conductivity. The significance of these properties cannot be understated, as they directly impact the functionality and reliability of products made from metal laminates. High-strength and durable laminates can withstand extreme conditions, while good thermal and electrical conductivity enhances performance in specific applications.
Strength and Durability
Strength and durability are paramount features when discussing metal laminates. These laminates are designed to combine different metal layers, resulting in a material that often surpasses the individual properties of its components. The layering technique allows for optimizing the mechanical properties, ensuring that the final product is resilient under stress and has an extended lifespan. Materials like aluminum are often combined with steel to provide an excellent balance of lightweight yet robust structures.
Mechanical testing indicates that various configurations yield diverse outcomes in strength. For instance, a laminate that combines titanium and stainless steel shows remarkable tensile strength. This combination is suitable for applications that require superior resistance to both mechanical stress and environmental effects. It is essential to select the right combination to maximize the potential of the laminate in real-world scenarios.
Moreover, durability extends beyond mere strength. It also encompasses the material's ability to resist wear and fatigue over time. Metal laminates are often utilized in industries where failure could lead to catastrophic results, such as in aerospace or automotive applications. This added durability is a key selling point for manufacturers looking to enhance the safety and longevity of their products.
Thermal and Electrical Conductivity
Thermal and electrical conductivity are two other critical mechanical properties of metal laminates, especially when applied in industries that require efficient heat dissipation and electrical performance. Metal laminates often incorporate materials like copper or aluminum due to their outstanding thermal and electrical properties.
In electronics, for example, metal laminates are utilized for heat sinks and components that need efficient heat management. The aluminum-copper laminate is notable for its high thermal conductivity, making it an excellent choice for applications where heat buildup is an issue. This leads to better performance and prevents potential failures that could arise from overheating.
Besides thermal management, electrical conductivity is equally vital. Depending on the composition, metal laminates can either promote or restrict electrical flow. This property is essential in manufacturing electronic devices, circuit boards, and connectors. The balance between weight, strength, and conductivity must be carefully considered during the design phase to ensure optimal performance.
"The choice of metals in laminates can significantly impact their thermal and electrical performance, making material selection critical for design engineers."
"The choice of metals in laminates can significantly impact their thermal and electrical performance, making material selection critical for design engineers."
Comparative Advantages of Metal Laminates
Understanding the comparative advantages of metal laminates is essential in appreciating their role in modern applications. These materials combine various metals, leveraging their strengths while mitigating weaknesses. In this section, we will explore two primary advantages: cost-effectiveness and weight reduction, both crucial in a variety of industries.
Cost-Effectiveness
Metal laminates often present a favorable cost profile compared to solid metals. This distinction arises from a few factors. First, metal laminates can reduce material waste. By using a layering process, manufacturers minimize the amount of raw material needed. This approach can translate into lower manufacturing costs and better pricing for end-users.
Furthermore, metal laminates can contribute to lower shipping costs. Given their lightweight nature, they are easier and cheaper to transport. This is particularly pertinent for industries where shipping expenses are significant. For instance, businesses involved in aerospace or automotive components find that reducing weight translates directly to both operational and logistics savings.
Consider this list of cost-related benefits of metal laminates:
- Lower raw material costs due to reduced waste.
- Decreased shipping expenses because of weight reduction.
- Enhanced pricing for end-users leading to better market competitiveness.
In addition, the lifespan of metal laminates often exceeds that of traditional materials. Their layered structure can offer better resistance to environmental degradation, which translates into lower maintenance costs. Thus, investing in metal laminates not only pays off through initial savings but also through long-term fiscal prudence.
Weight Reduction and Portability
The intrinsic property of metal laminates to reduce weight is indispensable in many sectors. The layering technique enables compounding of materials without significantly increasing overall mass. This attribute plays a vital role in industries like aerospace, automotive, and even consumer goods.
In aerospace, reducing weight is a paramount consideration. Every kilogram saved leads to fuel efficiency. Aircraft manufacturers like Boeing use metal laminates in their designs to maximize performance without compromising durability. Their lighter weight aids in further enhancing fuel efficiency, leading to reduced operating costs over the aircraft lifecycle.
Key aspects of weight reduction and portability include:
- Improved fuel efficiency in transportation applications.
- Enhancements in overall product portability, making assembly easier.
- Possibilities for innovative designs owing to lower structural load requirements.
Furthermore, the nature of metal laminates allows for their use in mobile devices. Lighter materials mean sleeker designs, appealing to consumers looking for portability. In this fast-paced world, where mobility is crucial, utilizing metal laminates provides companies with a competitive edge in technology sectors.
"The lightweight nature of metal laminates opens up new opportunities in product design and functionality."
"The lightweight nature of metal laminates opens up new opportunities in product design and functionality."
Challenges in the Use of Metal Laminates
The discussion around metal laminates must address the challenges faced in their application. Understanding these limitations is crucial for researchers and professionals who seek to maximize the advantages of this technology. Identifying and overcoming the challenges can lead to more effective use and innovation in various industries.
Adhesion Issues
Adhesion problems often arise during the manufacturing and application of metal laminates. The bond strength between layers is critical for performance. If the adhesion fails, it can lead to delamination, affecting durability and functionality.
Several factors influence the adhesion quality. Surface preparation is one of them. If surfaces are not adequately cleaned or treated, the adhesive might not bond properly. Furthermore, the choice of adhesive plays a significant role. Not all adhesives perform well under various environmental conditions. Selecting the right one requires an understanding of the material properties and the intended use.
To improve adhesion, professionals often turn to various treatments. Surface roughening, chemical priming, or using specialized adhesives can enhance bond strength and performance under stress. However, these solutions often come at an increased cost or complexity of the manufacturing process.
"The effectiveness of adhesion is often the linchpin for the longevity and success of metal laminates across diverse applications."
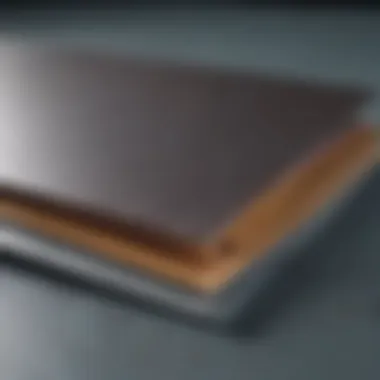
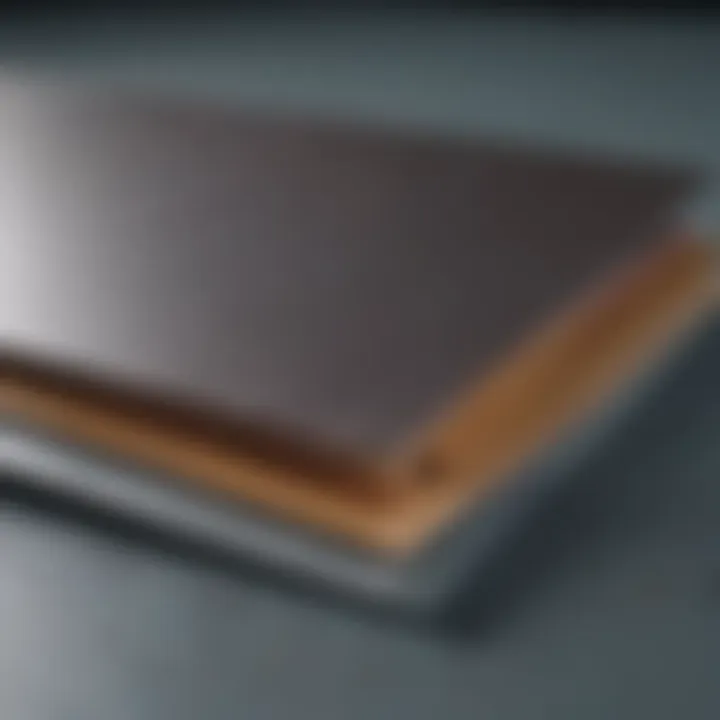
"The effectiveness of adhesion is often the linchpin for the longevity and success of metal laminates across diverse applications."
Environmental Resistance
Metal laminates face challenges concerning environmental resistance. These materials must withstand factors such as moisture, temperature variations, and corrosive agents, depending on their operational context. Failure to resist these elements can compromise the integrity and lifespan of the laminates.
Corrosion is a particular concern. Metals, when layered, can create areas that trap moisture, leading to rust or degradation over time. Manufacturers must consider corrosion-resistant metals or protective coatings to address this issue.
Temperature changes also affect metal laminates’ performance. Expansion and contraction can cause stress at the layered interfaces, potentially leading to failure. Selecting appropriate materials that can mitigate thermal impact is an essential consideration during the design phase.
In summary, while metal laminates offer significant advantages, addressing adhesion issues and ensuring environmental resistance are crucial for their successful implementation. Understanding these challenges allows professionals to develop solutions that enhance performance and longevity.
Future Trends in Metal Laminate Technology
The evolution of metal laminate technology is crucial for various industries that rely on the benefits of improved materials. Technological advancements are facilitating innovative applications and improving the performance of metal laminates. This section will explore significant trends shaping the future landscape of this field.
Advancements in Materials Science
Recent progress in materials science has led to the development of new alloys and composites for metal laminates. Researchers are focusing on enhancing the properties of metal layers to improve strength, lightweight characteristics, and resistance to corrosion. For instance, using titanium or high-strength aluminum armor can significantly increase the durability of laminates used in harsh environments.
Another noteworthy advancement is the use of nanotechnology. Incorporating nanomaterials into metal laminates can enhance mechanical properties and thermal stability. This can lead to increased performance in applications ranging from aerospace to consumer electronics. Researchers are exploring how nano-coatings can change the interface between metal layers, enhancing their adhesion and overall effectiveness.
"The integration of nanotechnology in materials science can catalyze breakthroughs in metal laminate applications, providing new functionalities and improving existing ones."
"The integration of nanotechnology in materials science can catalyze breakthroughs in metal laminate applications, providing new functionalities and improving existing ones."
Sustainability Considerations
As industries become more conscious of their environmental footprint, sustainability emerges as a pivotal concern in metal laminate technology. The production of traditional materials often involves energy-intensive processes. However, newer techniques aim to reduce waste and lower emissions. Utilizing recycled metals is at the forefront of sustainable practices in this realm.
Moreover, innovations in bio-based adhesives and coatings lessen the ecological impact while maintaining high performance. Companies are exploring eco-friendly manufacturing techniques, focusing on the circular economy which emphasizes reuse and resource efficiency.
Incorporating sustainability into metal laminate manufacturing not only meets regulatory requirements but also appeals to a more environmentally aware consumer base. This aspect is increasingly crucial in securing a competitive edge in the marketplace.
Ultimately, advancements in materials science and sustainability are setting the stage for a promising future in metal laminates. The interplay of these elements will play a key role in defining the material's applications and benefits in various sectors, especially in a world where efficiency and environmental responsibility mutually coexist.
Case Studies of Metal Laminates in Action
Case studies play a crucial role in the understanding of metal laminates. They provide real-world examples that illustrate the practical applications and advantages of these materials. Through examining various cases, one can derive insights about efficiency, innovation, and the performance of metal laminates across manufacturing sectors. Not only do case studies highlight successes, but they also address potential challenges that might arise when integrating metal laminates into existing processes.
Successful Industrial Implementations
In the industrial landscape, metal laminates have found their way into several successful implementations. One notable example involves the aerospace sector. Companies such as Boeing have utilized metal laminates for components like fuselage panels and wing structures. This choice is due to the contribution of metal laminates to strength without a substantial weight increase. Lower weight translates directly to fuel efficiency—a key consideration in the aviation industry.
The automotive industry also successfully employs metal laminates. For instance, Tesla has integrated these materials into the design of its electric vehicle batteries. The laminated structure enhances performance while optimizing space and minimizing weight. This case underscores the adaptability of metal laminates across different sectors, showcasing how these materials meet industry demands for both resilience and efficiency.
"Metal laminates' unique properties have led to breakthroughs in areas previously constrained by traditional materials."
"Metal laminates' unique properties have led to breakthroughs in areas previously constrained by traditional materials."
Innovative Use Cases
Beyond traditional applications, innovative use cases for metal laminates are emerging continually. In the electronics field, companies like Samsung have pioneered the use of metal laminates in the production of smartphones. These laminates provide improved durability and a sleek aesthetic without sacrificing performance. The integration of metal layers enhances thermal management—vital for high-performance devices.
Another exciting development is in 3D printing. Using metal laminates has allowed manufacturers to explore complex geometries that were not feasible with single-material approaches. For instance, firms employing selective laser melting technology create intricate components that leverage the strengths of multiple alloys. This trend points to a future where hybrid structures, enabled by metal laminates, could revolutionize manufacturing processes across multiple industries.
In summary, studying the case examples of metal laminates reveals their transformative potential. Success stories in aerospace and automotive sectors underline the role of metal laminates in enhancing performance, while innovative applications in electronics and 3D printing illustrate their versatility. Understanding these cases not only solidifies the relevance of metal laminates but also inspires ongoing experimentation and development in this advanced field.
End
The conclusion of this article on metal laminates underscores their significance in various industrial applications and the art of modern design. As this exploration has revealed, metal laminates are not just materials; they are crucial components that enhance functionality and performance. Their capacity to combine different metals allows engineers and designers to tailor products for specific needs, achieving an optimal balance of strength, weight, and cost-efficiency.
Recap of Key Points
To summarize, several critical aspects emerged throughout the discussion:
- Composition and Types: Metal laminates are composed of layers of metals such as aluminum, steel, and copper, each bringing unique properties that can be exploited for specific applications.
- Manufacturing Processes: Advances in manufacturing techniques have paved the way for more precise and efficient production methods, ensuring that metal laminates meet industry standards while remaining innovative.
- Applications: The versatility of metal laminates is showcased across various fields, including aerospace, automotive, and consumer electronics. Their ability to provide lightweight but durable solutions is their key advantage.
- Challenges and Solutions: Despite their benefits, issues such as adhesion and environmental resistance need careful consideration. Ongoing research is crucial to address these challenges and enhance the performance of metal laminates.
- Future Trends: The article highlighted the trajectory of future innovations in materials science and the growing emphasis on sustainability, indicating a clear direction for development in this sector.
Final Thoughts
In closing, understanding metal laminates extends beyond just their properties; it hinges on recognizing their potential impact on future designs and products. As industries continue to evolve and demands for innovative solutions increase, metal laminates will undoubtedly play a crucial role. Recognizing this is vital for students, researchers, and professionals, as it informs their approaches to design and materials selection. Engaging with this topic can yield new insights that enhance both research and practical applications in a range of fields.
"Metal laminates exemplify the integration of multiple properties into a single functional material, a synergy that drives innovation."
"Metal laminates exemplify the integration of multiple properties into a single functional material, a synergy that drives innovation."
This comprehensive exploration of metal laminates encourages deeper investigation and application in respective fields, paving the way for advancements that align with modern challenges. Thus, the future for metal laminates is not just bright; it is full of potential.