Understanding Aluminum Passivation Processes for Corrosion Resistance
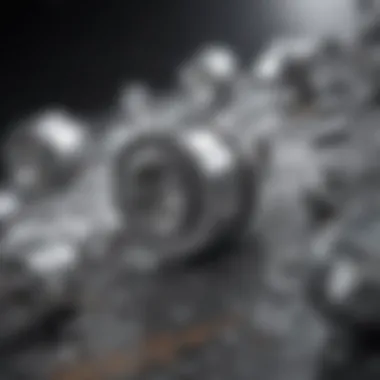
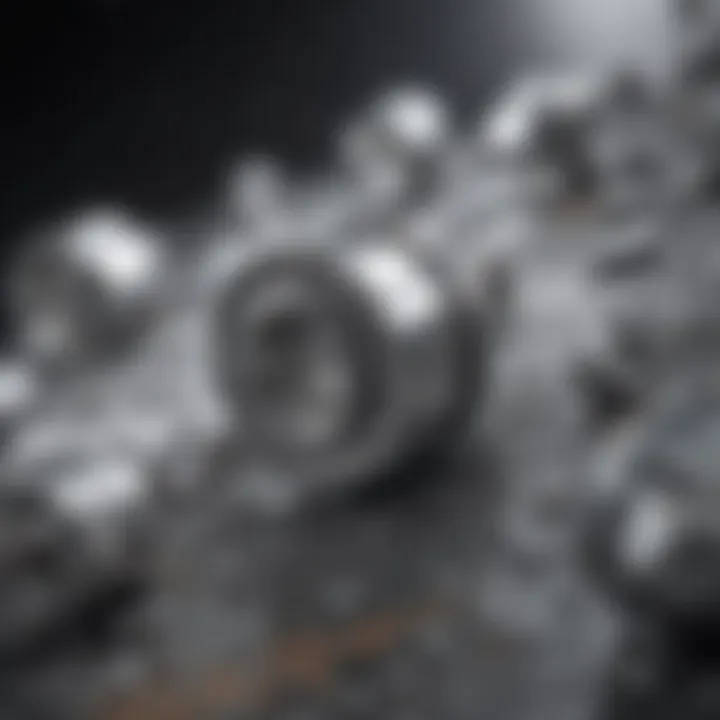
Intro
Aluminum, often lauded for its light weight and corrosion resistance, still has its vulnerabilities. Corrosion can strike like a thief in the night, undermining its durability and leading to greater issues down the line. To tackle this challenge, the passivation process emerges as a valuable technique, enhancing aluminum's innate properties and securing its place in a variety of applications.
In this exploration, we will embark on a detailed journey through the passivation process of aluminum. We’ll dissect the why and how, diving into the scientific principles, current trends in research, and what the future may hold. In doing so, we hope to arm readers with a deeper understanding, whether you are a student dipping your toes into materials science, a researcher seeking the latest breakthroughs, or a professional eager for practical insights in your field.
Intro to Aluminum Passivation
In the grand tapestry of materials science, aluminum stands out as a remarkable metal. Yet, it is not immune to the rust that time and environment can bring. This is where the process of passivation plays a crucial role. Understanding aluminum passivation—its definition, significance, and various techniques—provides valuable insights for students, researchers, and industry professionals alike.
Definition of Passivation
Passivation is a treatment process that enhances the natural oxidation layer on aluminum surfaces, creating a barrier that increases the metal's corrosion resistance. When aluminum is exposed to air, an oxide layer forms naturally, but this layer can be fragile and insufficient for protecting the underlying metal in harsher environments. The essence of passivation lies in strengthening and stabilizing this oxide layer. This is typically achieved through chemical or electrochemical methods that result in a thicker, more resilient oxide film. In simpler terms, it’s about making aluminum tougher and less prone to the ravages of oxidation.
Importance of Passivation
The importance of passivation cannot be overstated. It serves multiple practical benefits:
- Corrosion Resistance: By promoting a stronger oxide layer, passivation significantly reduces the rate of corrosion, a must-have attribute especially in industries dealing with harsh substances.
- Longevity: Passivated aluminum components tend to last longer, making them economically favorable over time. Rather than replace materials prematurely, manufacturers can rely on passivated elements to perform consistently.
- Safety and Reliability: In fields like aerospace and automotive, the integrity of materials is paramount. Passivation helps ensure that aluminum remains structurally sound even under extreme conditions, enhancing overall safety.
- Aesthetic Qualities: The process can also enhance the visual appeal of aluminum surfaces, making them smoother and more lustrous. For architectural applications, this is particularly advantageous, tying functionality into design.
In a nutshell, understanding aluminum passivation equips industry stakeholders with the knowledge to optimize the performance and lifespan of aluminum products. The following sections will explore the chemistry behind this essential process and elucidate various techniques employed in the passivation of aluminum.
The Chemistry Behind Passivation
The chemistry behind passivation is an essential topic for understanding how aluminum function in various environments. The interplay of oxidation and the formation of an oxide layer plays a critical role in protecting aluminum from corrosion. When aluminum is exposed to the atmosphere, it naturally undergoes oxidation. However, this process is not merely a cosmetic change; it's the cornerstone of the passivation process, acting as a shield that enhances the material's longevity and durability.
Oxidation and Aluminum
Oxidation is a fundamental reaction that occurs when aluminum encounters oxygen in its surroundings. In this process, aluminum atoms lose electrons and form positively charged ions. This chemical reaction can be represented simply as:
[ 4Al + 3O_2 \rightarrow 2Al_2O_3 ]\
This equation indicates that four atoms of aluminum react with three molecules of oxygen to yield aluminum oxide. What’s fascinating is that this aluminum oxide layer is only a few nanometers thick, yet it significantly changes the material's properties. By forming this oxide layer, aluminum prevents further oxidation from taking place, effectively creating a protective barrier.
This protective layer might be thin, but it’s crucial. Think of it as a coat that keeps a person dry on a rainy day. Once the layer is intact, it minimizes the interaction of aluminum with corrosive elements, which could otherwise penetrate the metal and lead to degradation.
Formation of the Aluminum Oxide Layer
The formation of the aluminum oxide layer is a complex process influenced by several factors. Initially, when aluminum is exposed to air, moisture is absorbed, and an aluminum hydroxide layer forms. Quickly, this layer dehydrates and transforms into a dense oxide layer, commonly known as alumina, represented as ( Al_2O_3 ).
Key Point: The alumina layer forms immediately upon exposure to air, providing urgent protective attributes.
Key Point: The alumina layer forms immediately upon exposure to air, providing urgent protective attributes.
Factors such as temperature, humidity, and the presence of contaminants can affect the formation and integrity of this layer. For instance, increasing temperature can accelerate the formation of the alumina layer, leading to quicker passivation. Conversely, contaminants like salts or organic compounds can hinder layer formation, allowing corrosion to set in.
Factors Influencing Oxide Layer Thickness
The thickness of the oxide layer varies significantly based on a range of influences. Here are some of the prominent factors:
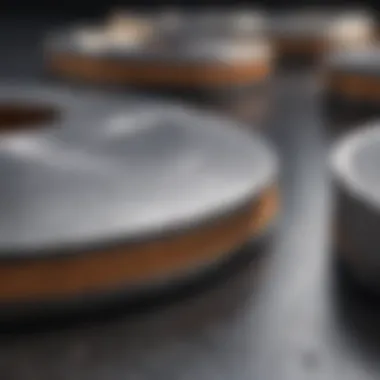
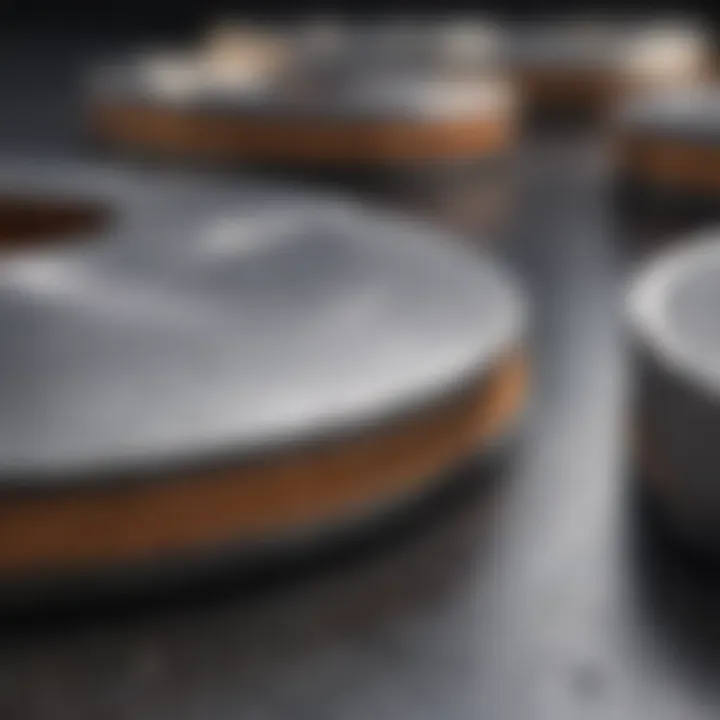
- Electrolytic Conditions: During anodization, an electrochemical process can be utilized to artificially thicken the oxide layer. The resulting layer not only enhances corrosion resistance but also allows for the incorporation of dyes or additional protection.
- Exposure Time: The longer aluminum is exposed to oxygen and moisture, the thicker the oxide layer will become, up to a certain limit. However, this may lead to a compromise in the physical properties of the aluminum.
- Alloy Composition: Different aluminum alloys exhibit varying responses to oxidation, influenced by the presence of alloying elements like copper or magnesium, which can either promote or impede oxide layer development.
- Environmental Conditions: The external conditions in which aluminum is situated can greatly affect oxide layer thickness. A humid and salty environment will typically yield a thinner oxide layer than dry air, leading to a greater susceptibility to corrosion.
Passivation Techniques
The effectiveness of passivation is not just rooted in its fundamental principles, but importantly in the techniques employed to achieve it. Each method carries its own set of advantages and considerations that play a critical role in protecting aluminum from corrosion. Understanding these techniques can significantly influence material selection, treatment choices, and ultimately, the longevity of aluminum components in various applications.
Chemical Passivation Methods
Using Chromate Solutions
The use of chromate solutions in chemical passivation is a time-tested approach, renowned for its efficacy in offering a robust protective layer. Chromate conversion coatings yield a film that not only enhances corrosion resistance but also improves adhesion for subsequent paint applications. Its ability to form a durable layer at relatively low temperatures is a notable characteristic. This can be especially advantageous in industries where thermal sensitivity is a concern.
A unique feature of chromate solutions is their compatibility with a wide range of aluminum alloys, making it a popular choice across various sectors. However, one must bear in mind the environmental implications; chromates are classified as hazardous substances, raising significant health and ecological concerns. Thus, the balance of benefits against these risks is crucial in decision-making processes.
Phosphate Treatments
In contrast, phosphate treatments provide a distinct method of chemical passivation that has garnered attention for its adaptability. This technique involves the application of phosphoric acid or alkaline phosphate solutions, leading to the formation of a phosphate coating that enhances corrosion resistance.
The key characteristic of phosphate treatments is their ability to produce a more porous and adherent surface than chromate processes, making them particularly suitable for further coatings. Not only do they boost resistance against corrosion, but also improve paint adhesion and surface finish. On the downside, the level of protection might not be as pronounced as with chromate solutions, and attention to detail is essential during application to achieve desired outcomes.
Electrochemical Passivation
Anodizing Process
The anodizing process stands out in the realm of electrochemical passivation. By immersing aluminum in an acidic electrolyte and applying an electric current, a thick aluminum oxide layer forms on the surface. This process significantly enhances corrosion resistance and is coupled with improved abrasion resistance as well.
Anodizing is a favored technique because it can be tailored for specific requirements; variations in the process can modify oxide thickness. An additional advantage of anodizing is the ability to dye the oxide layer, allowing for aesthetic as well as functional enhancement. However, this method can be more cost-intensive and less compatible with all alloy types, thus requiring careful consideration.
Electrolytic Treatment
Electrolytic treatment also utilizes an electrical charge to modify the aluminum surface, although it differs from the anodizing process in its specifics. This treatment promotes the formation of a thicker oxide layer than traditional anodizing. It’s especially advantageous in industries requiring stringent corrosion protection and can be adjusted for various environmental challenges.
One key characteristic of electrolytic treatment is its rapid processing time, alongside the ability to control the thickness of the oxide layer with precision. Though effective, it requires stringent quality control measures, as flaws in the coating process can compromise the protective qualities of the aluminum.
Mechanical Passivation
Brushing Techniques
Mechanical passivation, especially through brushing techniques, involves physically removing oxide layers and contaminants from aluminum surfaces, providing a fresh base for subsequent treatments or applications. The simplicity yet effectiveness of this method is its defining trait, allowing for an immediate improvement in surface condition.
Brushing not only enhances surface finish but also prepares metals for further chemical treatments, making it an essential step in many manufacturing processes. However, it demands careful handling; aggressive brushing can lead to unwanted scratches and may compromise the material's overall integrity.
Media Blasting
Media blasting, or abrasive blasting, is another method in mechanical passivation where fine particles are blasted onto a surface to create a clean, rough profile. This technique is highly regarded for its efficiency in removing old coatings and contaminants, paving the way for better adhesion of new finishes.
One of its key traits is its ability to treat large surfaces uniformly and quickly, reducing pre-treatment time. Nevertheless, it may also present challenges; if not performed correctly, it can create residual abrasions that affect both appearance and performance. Hence, controlling the blasting parameters is crucial for optimal results.
"Each passivation technique has its unique merits and potential drawbacks; the choice between them should always align with application needs and environmental considerations."
"Each passivation technique has its unique merits and potential drawbacks; the choice between them should always align with application needs and environmental considerations."
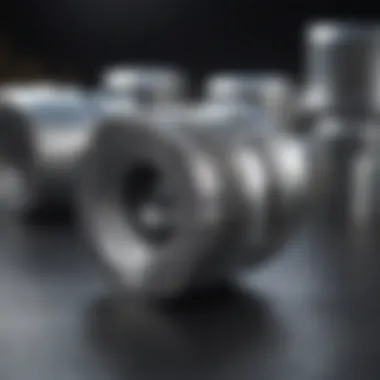
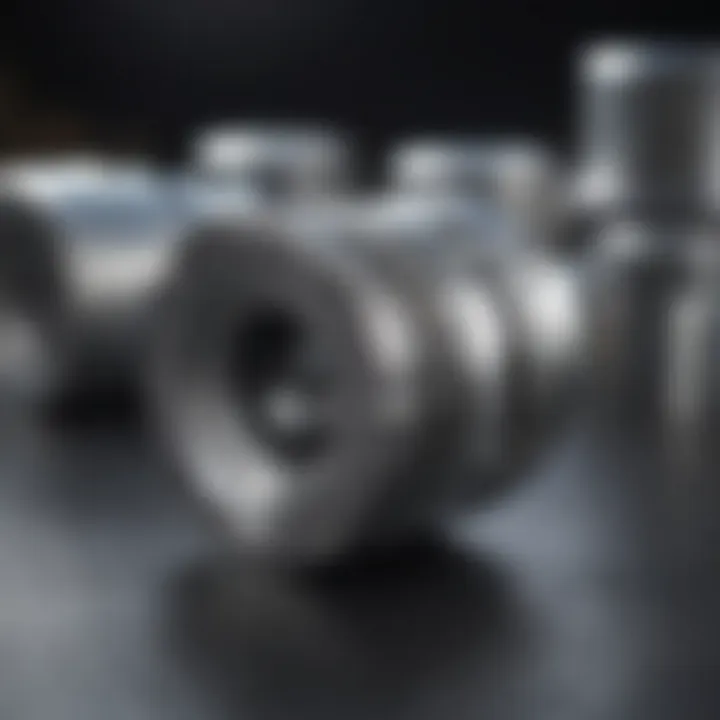
In summation, the landscape of passivation techniques is rich and varied. From the chemical methods like chromate solutions and phosphate treatments to the electrochemical and mechanical approaches, understanding their nuances is essential for harnessing aluminum's full potential in numerous applications.
Applications of Passivated Aluminum
The applications of passivated aluminum are both diverse and integral to a multitude of industries. Understanding this topic gives insight into how aluminum can effectively resist corrosion and degradation, ultimately extending its longevity and enhancing its performance in various settings. From the sky-high demands of aerospace to the rigorous conditions in automotive environments, the benefits of passivation are apparent. Moreover, construction applications highlight aluminum's role in sustainability while achieving aesthetic appeal. As we explore these applications, we see that the advantages of passivated aluminum go beyond mere functional attributes—they speak volumes about reliability, safety, and environmental consciousness.
Aerospace Industry
In the aerospace sector, the stakes are as high as the altitudes these crafts achieve. Passivated aluminum plays a vital role in ensuring durability and safety. The extreme conditions that aircraft experience, including fluctuating temperatures and exposure to corrosive elements like humidity and salt, necessitate materials that stand the test of time.
- Weight-to-strength ratio: Aluminum’s natural lightweight nature combined with passivation leads to an optimal strength-to-weight ratio, crucial for fuel efficiency.
- Corrosion prevention: The aluminum oxide layer acts as a formidable barrier against oxidants, preventing the degradation of the aircraft's components, whether it's in the fuselage, wings, or landing gears.
The result is not just an airworthy vessel; passivated aluminum fosters operational reliability and ensures passenger safety. Airline manufacturers and suppliers often prioritize materials that offer these advantages, highlighting passivation as a non-negotiable treatment in modern aerospace design.
Automotive Sector
The automotive industry is another cornerstone in which passivated aluminum shines. Modern vehicles are designed with a keen focus on performance, safety, and longevity. Passivation enhances aluminum's ability to manage these demands effectively.
- Enhanced aesthetics: Passivated surfaces can be painted or anodized to achieve visually appealing finishes, which is something car manufacturers heavily invest in for branding.
- Resistance to environmental factors: Oil, salt, and harsh weather can quickly erode untreated aluminum. Passivated aluminum parts have proven to resist such wear, preserving both functionality and appearance over the lifespan of the vehicle.
Additionally, with the push towards electric vehicles (EVs), aluminum is becoming the go-to choice for battery casings due to its lighter weight and flexibility. Passivated aluminum aids in maintaining the structural integrity necessary to house high-voltage systems, solidifying its place in both traditional vehicles and emerging technologies.
Building and Construction
The benefits of passivated aluminum extend to the building and construction sector, where durability meets design. Construction projects today increasingly prioritize materials that contribute to sustainability while delivering robust performance.
- Architectural innovation: The aesthetic versatility of passivated aluminum allows for bold architectural choices, from sleek facades to intricate decorative elements. Not only do these choices need to be visually appealing, but they also must withstand various weather elements.
- Longevity and maintenance: Buildings made of passivated aluminum require significantly less maintenance compared to those utilizing untreated metals. This leads to cost savings for owners over time.
Sustainability is another critical factor in modern construction, as architects and builders seek out materials that align with green building standards. Passivated aluminum not only reduces waste through a longer lifecycle but often comes from recyclable sources, making it a smart choice for eco-conscious projects.
"When considering longevity, appearance, and environmental impact, passivated aluminum stands out as a pivotal material in both public and private architecture."
"When considering longevity, appearance, and environmental impact, passivated aluminum stands out as a pivotal material in both public and private architecture."
In summary, the applications of passivated aluminum cross various industries, reinforcing the material's significance in enhancing durability, performance, and sustainability. As research pushes further into innovative applications and development of passivation techniques, the capabilities of passivated aluminum promise to expand even further.
Environmental Considerations
The passivation process of aluminum presents certain environmental considerations that require careful thought and action. With the growing awareness of sustainability and the impact of industrial processes on natural ecosystems, it becomes crucial to address how aluminum passivation interacts with the environment. Not only does this pertain to the chemicals utilized, but also to the overall lifecycle of aluminum products. The following subsections delve into these aspects, assessing both the potential hazards and the innovative alternatives available.
Impact of Passivation Chemicals
Passivation involves various chemicals that play a vital role in forming protective oxide layers on aluminum surfaces. However, the environmental footprint of these substances can be a significant concern. For instance, traditional methods often employ chromate-based solutions, which are effective but notorious for their toxic effects on both human health and the environment. This creates a tricky balance: while the passivation ensures durability and corrosion resistance, its very chemicals can taint water sources and soil.
Contamination is not just an abstract menace; it manifests in various forms. One prominent issue is the leaching of harmful chemicals into groundwater, potentially affecting drinking water quality.
"The environmental cost of corrosion is often overshadowed by its immediate economic impact, highlighting a need for more sustainable practices in passivation processes."
"The environmental cost of corrosion is often overshadowed by its immediate economic impact, highlighting a need for more sustainable practices in passivation processes."
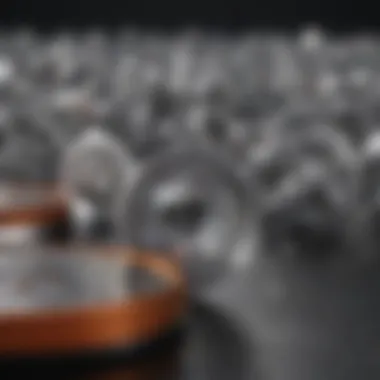
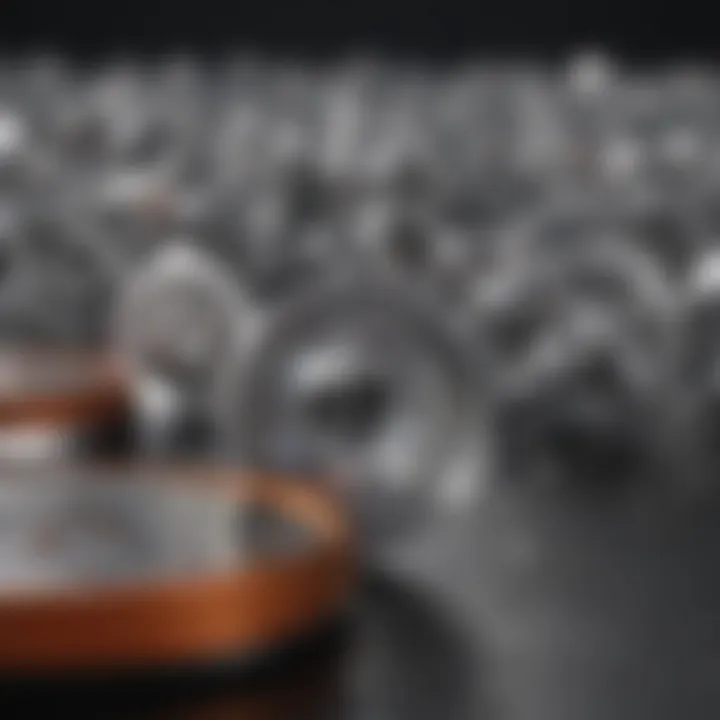
Additionally, industries must adhere to stringent regulations related to waste disposal and emissions, which adds another layer to operational complexity. As regulatory scrutiny tightens, the pressure to develop less harmful alternatives intensifies.
Sustainable Passivation Alternatives
The search for sustainable alternatives to conventional passivation methods is gaining momentum, and various approaches are emerging. One notable avenue is the use of eco-friendly chemicals that are less harmful to the environment while maintaining a similar level of effectiveness. For example, non-toxic phosphate solutions have found traction in the industry, providing effective corrosion resistance without the perils associated with chromates.
Moreover, innovations in green chemistry are leading to the development of new materials and methods that can further reduce the ecological impact. Examples include bio-based agents derived from natural sources, which have shown potential in providing adequate protection for aluminum without environmental hazards.
In addition to chemical alterations, the overall process efficiency can also be optimized. Energy-saving techniques not only lower the cost of production but also lessen the environmental footprint of the manufacturing operations.
In summary, as the global community shifts towards sustainable practices, the aluminum passivation sector faces both challenges and opportunities. Understanding the environmental implications of passivation chemicals, along with exploring greener alternatives, is fundamental to creating a more sustainable future in aluminum processing.
Challenges in Passivation Processes
When we talk about the passivation of aluminum, we can’t ignore the challenges that often crop up in this intricate procedure. The ability of aluminum to resist corrosion directly hinges on the effectiveness of the passivation process, but there are a number of elements that can complicate matters. Understanding these challenges is paramount for both practical applications and research advancements.
One significant aspect involves the effects of contaminants that can interfere with the formation of the protective oxide layer. In certain cases, oils, dirt, or even moisture can settle on the aluminum surface before passivation occurs. If these contaminants aren’t properly cleaned or removed, they can lead to an incomplete or uneven oxide layer, compromising the integrity and function of the passivated aluminum. A thorough surface preparation is not just a step to take lightly—it’s absolutely essential. The performance of the oxide film is directly linked to how clean the surface is before the passivation process begins.
"An ounce of prevention is worth a pound of cure."
This saying rings true in the realm of aluminum passivation. Cleaning the surface effectively prior to the passivation treatment can save a lot of headaches in the long run.
"An ounce of prevention is worth a pound of cure."
This saying rings true in the realm of aluminum passivation. Cleaning the surface effectively prior to the passivation treatment can save a lot of headaches in the long run.
Another challenge is the variability in aluminum alloys. The diversity of aluminum alloys available today is both a blessing and a curse. Different alloys contain various alloying elements, such as copper or manganese, which can impact how aluminum reacts during the passivation process. For instance, higher copper content alloys may have different oxide layer characteristics compared to those with silicon or magnesium. This variability means that what works for one alloy may not work for another, making it vital to tailor the passivation technique to match the specific alloy type being used.
Here are some considerations related to these challenges:
- Pre-treatment: A robust cleaning and surface preparation process is vital, as it sets the stage for effective passivation.
- Alloy Assessment: Identifying the composition of the alloy can optimize the passivation strategy. This can include adjusting chemical concentrations in treatments according to the particular alloy type.
- Monitoring: Real-time monitoring of the passivation process can help identify issues early on, thus allowing for corrective measures to be implemented immediately.
The complexities involved in the passivation of aluminum demand a detailed understanding of various factors, as these directly affect the alloy's long-term performance in diverse environments. By acknowledging these challenges, professionals can improve procedures and develop more effective techniques, ultimately enhancing the reliability of aluminum components across various industries.
Future Directions in Aluminum Passivation Research
The field of aluminum passivation is evolving constantly due to the increasing demands for enhanced corrosion resistance and sustainable practices. As industries push for materials that not only perform better but also have lower environmental impact, the direction of research is pivotal. Understanding the future avenues in this area is vital for students, educators, researchers, and industry professionals aiming to stay ahead in their respective fields. The innovations in the passivation process promise several benefits, from cost-efficiency to improved performance metrics.
Innovative Materials for Passivation
In the realm of passivation, new materials are redefining standards. Researchers are increasingly turning their attention to bio-based and green chemicals to replace traditional chromate solutions known for their toxicity. Biopolymers and natural extracts offer promising alternatives. For instance, polysaccharides, derived from plants, have shown potential in forming effective protective layers on aluminum surfaces.
Some key developments include:
- Nano-coatings: These materials create extremely thin films that enhance aluminum's protective qualities without significantly altering its appearance or bulk properties.
- Graphene-based materials: Graphene is being studied for its remarkable strength and conductivity, possibly providing a game-changing method for aluminum passivation.
- Hybrid systems: Combinations of organic and inorganic materials offer tailored solutions, producing layers that protect against moisture and salts more effectively than traditional methods.
This shift not only addresses environmental concerns but can also lead to higher performance outcomes, creating a win-win situation. With innovative materials paving the way, the future of aluminum passivation looks promising.
Improving Process Efficiency
Another aspect warranting attention is the efficiency of the passivation processes themselves. As technologies advance, there’s a big push towards streamlining methodologies. Electrochemical methods like anodizing are being refined to reduce energy consumption and waste. The integration of automation and smart technologies can also enhance precision, ensuring even coating and minimal resource depletion.
Key tactics for enhancing process efficiency include:
- Real-time monitoring systems: Utilizing sensors and data analytics helps in maintaining optimal conditions during passivation, reducing variability and ensuring consistent results.
- Recycling chemicals: The ability to recover and reuse chemicals employed in passivation processes not just reduces costs but also lowers the environmental footprint.
- Modular systems: Developing flexible systems that can adapt to various production scales ensures that smaller operations can implement efficient methods without hefty investments.
"The future of aluminum passivation is not just about protection, it's about sustainable innovation that meets the demands of modern industries."
"The future of aluminum passivation is not just about protection, it's about sustainable innovation that meets the demands of modern industries."
With each step taken towards improving materials and methods, the industry might very well discover novel pathways that transcend the current limitations of aluminum passivation.