Understanding Mechanical Pressure Sensors in Depth
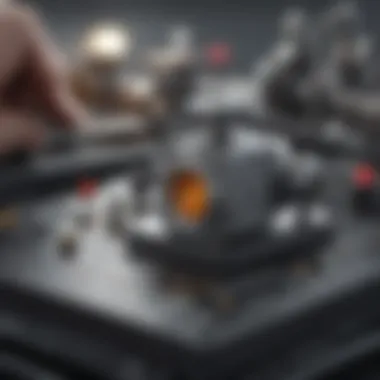
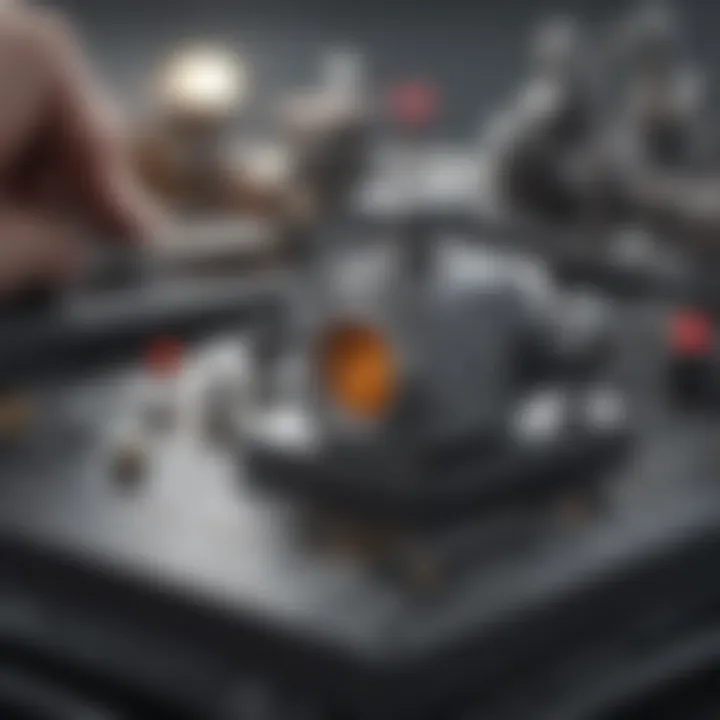
Intro
Mechanical pressure sensors play a crucial role in various industries, from manufacturing to healthcare. By converting physical pressure into an electrical signal, these devices enable accurate monitoring and control. Understanding their inner workings can offer invaluable insights into how we measure and respond to pressure changes in numerous environments.
In today's world, where precision is key, mechanical pressure sensors have become indispensable tools in both scientific research and industrial applications. Whether it's tracking the pressure of fluids in a pipeline or monitoring blood pressure in a medical setting, the significance of these sensors cannot be overstated. Additionally, as technology continues to advance, the capabilities and applications of these sensors are expanding, making it essential for professionals and researchers alike to grasp the fundamental principles and future trends of this field.
The following sections will dissect the core concepts related to mechanical pressure sensors, dive into current research trends, and explore how the ongoing innovations are shaping their future use. By the end of this article, readers will not only understand how these sensors function but also appreciate the pivotal role they play in enhancing accuracy and reliability in practical applications.
Prolusion to Mechanical Pressure Sensors
In the realm of modern technology, the role of pressure sensors cannot be overlooked. Mechanical pressure sensors serve as pivotal elements in a variety of applications, from industrial manufacturing to aerospace engineering. Their significance lies not just in measurement but also in ensuring safety and efficiency in operations. The accuracy of pressure readings is aligned closely with operational success, making it crucial for developers and engineers to understand these devices both on a fundamental level and in context of their practical applications. This article unfolds the intricacies behind mechanical pressure sensors, shedding light on their principles, various forms, and future trajectories.
Definition and Importance
A mechanical pressure sensor is defined as a device that measures the pressure of gases or liquids by converting the mechanical stimulus into an electrical signal. This simple yet effective mechanism has far-reaching implications across multiple fields. Understanding their importance begins with recognizing their ubiquitous presence in everyday technology. Whether it's monitoring blood pressure in medical devices or ensuring optimal performance in industrial pipelines, these sensors are essential.
The importance extends to reliability; accurate readings from pressure sensors are necessary to prevent catastrophic failures in systems where pressure is critical. For example, the aerospace sector relies heavily on these devices during flight tests and operational phases, minimizing risks associated with pressure fluctuations.
Historical Context
To appreciate the present advancements in mechanical pressure sensors, one must take a step back to explore their historical development. The concept of measuring pressure has been around since the late 17th century, with the invention of the barometer by Evangelista Torricelli. This laid the groundwork for modern sensing technologies. The Bourdon tube, invented in the mid-19th century, marked a significant leap in pressure measurement accuracy and became widely adopted in industrial applications.
Over time, advancements continued, with various materials and technologies enhancing the precision and durability of sensors. The 20th century saw the incorporation of piezoelectric materials, leading to the creation of sensors capable of reliable readings under varying conditions. These innovations not only increased the functionality of pressure sensors but also expanded their applicability across numerous industries.
The trajectory leading up to today’s devices is a testament to a relentless pursuit of accuracy and efficiency. Each leap in technology from mechanical to electronic systems further paved the way for the sophisticated sensors that are defining our industrial future. With every iteration, the essence of pressure measurement remains the same, yet the complexity and capabilities have sprung to new heights.
Principles of Pressure Measurement
Understanding the principles behind pressure measurement is crucial in grasping how mechanical pressure sensors function. These principles illuminate the various methods used to measure pressure, which ultimately defines the sensor's design and application. They form the backbone of sensor technology and influence the performance, accuracy, and reliability of measurements in numerous applications.
In the realm of mechanical pressure sensors, precise measurement is not just about numbers, but it's about ensuring safety and efficiency in industrial environments and critical applications such as aerospace and healthcare. With a solid understanding of these principles, one can appreciate the nuanced challenges that engineers face when designing sensors that must operate under varying conditions. This knowledge can also guide innovations and improvements in sensor technology, making it indispensable for students, researchers, and professionals.
Understanding Pressure
Pressure, fundamentally, is defined as the force exerted per unit area. When we talk about measuring pressure, what we usually mean is how much force is being applied to a given surface. It can occur in various forms, like atmospheric, absolute, gauge, and vacuum pressure.
- Atmospheric Pressure: This is the pressure exerted by air at any given point in the Earth's atmosphere. It fluctuates based on altitude and weather conditions.
- Absolute Pressure: This type measures the total pressure exerted on a surface, including the atmospheric pressure.
- Gauge Pressure: This measures pressure relative to the atmospheric pressure and is commonly used in everyday scenarios, like inflating tires.
- Vacuum Pressure: This measures pressures below atmospheric pressure. It's crucial in vacuum applications, where the absence of air is essential.
Understanding these different pressure types helps one grasp how mechanical pressure sensors operate in very specific scenarios. For instance, when calibrating a sensor, knowing whether one needs to measure gauge pressure or absolute pressure can significantly impact the outcome of the readings. The design of the sensor must cater to the specific type of pressure it measures, incorporating the necessary safety margins and operational guidelines associated with each.
Mechanical Principles at Play
At the core of mechanical pressure sensors are various mechanical principles that govern how pressure is transformed into measurable signals. Several fundamental phenomena come into play:
- Material Deformation: Most mechanical pressure sensors rely on materials that deform under stress. For instance, a diaphragm, commonly found in pressure sensors, bends when pressure is applied. This bending can be quantified to provide an accurate reading of pressure levels.
- Force Transformation: The mechanical setup of sensors allows applied force to be converted into a measurable form. For example, in a Bourdon tube sensor, pressure causes the tube to uncoil or expand, and the movement can then be translated into rotational movement, which is used to indicate pressure on a gauge.
- Piezoresistivity: In piezoresistive sensors, materials change their electrical resistance in response to applied pressure. This change can be measured electrically, providing a precise pressure reading. Piezoresistive materials are commonly used in applications that require high accuracy and sensitivity.
These principles are not just theoretical concepts—they are what make mechanical pressure sensors effective and reliable in the real world. The knowledge of how materials behave under pressure and how those behaviors can be harnessed for measurement is critical for anyone involved in the design and application of pressure sensors. Understanding these mechanical principles helps drive innovation, leading to more efficient and trustworthy sensor technologies.
"Effective measurement starts with knowing the underlying principles that affect both design and application. Without a well-rounded understanding, even the best sensors may miss the mark."
"Effective measurement starts with knowing the underlying principles that affect both design and application. Without a well-rounded understanding, even the best sensors may miss the mark."
In summary, grasping the principles of pressure measurement is vital for anyone in the field. It lays a foundation that supports advancements in sensor design and inspires solutions for challenges faced across diverse applications, from industrial settings to aerospace and beyond.
Types of Mechanical Pressure Sensors
Understanding the different types of mechanical pressure sensors is essential to grasping their application in various fields. Each sensor type comes with its own set of advantages, use-cases, and design considerations. This section will shed light on three popular types of mechanical pressure sensors: diaphragm-based sensors, Bourdon tube sensors, and piezoresistive sensors. Through this exploration, readers will appreciate how the specific characteristics of each sensor suit them for dedicated functions across industries.
Diaphragm-based Sensors
Diaphragm-based pressure sensors utilize a flexible membrane that deforms in response to applied pressure. This deformation is then converted to an electrical signal or is measured directly. These sensors are particularly favored for their versatility and sensitivity. One of the significant advantages of diaphragm-based sensors is their capability to handle both static and dynamic pressure measurements efficiently.
In many industrial applications, from HVAC systems to food processing, diaphragm sensors can provide real-time data that is crucial for operational decisions. Their compact size makes them suitable for confined spaces, making them a go-to choice in many designs.
Factors to keep in mind when selecting a diaphragm-based sensor include:
- Material: Common materials include stainless steel and polymers, which are chosen based on the environment and medium to be measured.
- Pressure Range: These sensors often have varying pressure ranges, so matching the right sensor to the application is key.
- Temperature Sensitivity: The diaphragm must withstand specific temperature ranges to maintain accuracy.
An interesting point to note is that when comparing diaphragm sensors with others, they often exhibit less mechanical wear due to their design, resulting in longer lifespans and lower maintenance needs.
Bourdon Tube Sensors
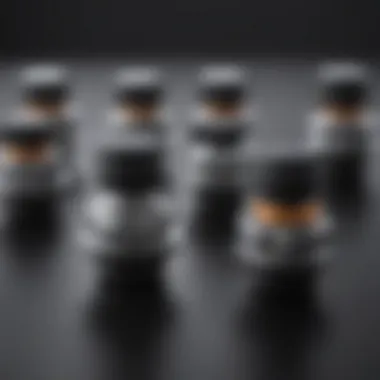
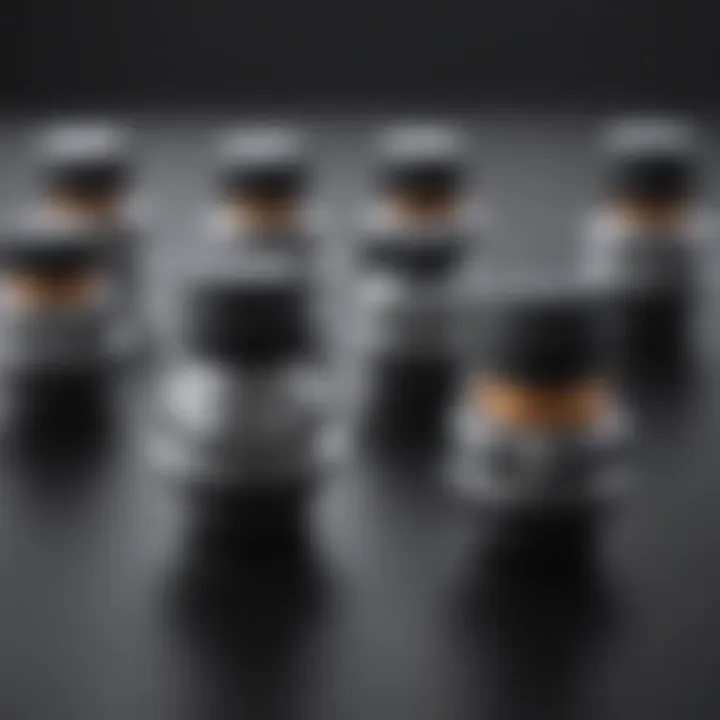
Bourdon tube sensors, named after their inventor, are another staple in mechanical pressure measurement. These sensors operate using a curved tube that straightens with increasing pressure. The degree of straightening is measurable and can be correlated to the specific pressure reading.
Bourdon tube sensors are notably robust and excel in high-pressure environments. Their simplicity in design is one reason these sensors have been around for so long. They require minimal maintenance and can operate in harsh conditions, making them favorable for applications like natural gas, steam, and hydraulic systems.
Key considerations when working with Bourdon tube sensors include:
- Installation: Proper installation is vital; any misalignment can lead to measurement errors.
- Calibration: Regular calibration ensures that they continue delivering accurate readings.
- Material Durability: They are often made from materials like brass or stainless steel, which contribute to their longevity.
Keep in mind that their mechanical nature means they can be less sensitive to small pressure changes, so they might not be the best fit for all applications where precise measurements are fundamental.
Piezoresistive Sensors
Piezoresistive sensors represent a more modern approach to mechanical pressure measurement. They rely on the piezoresistive effect, where the electrical resistance of a material changes under mechanical stress. This sensor type typically incorporates silicon as a base material, which contributes to its sensitivity and accuracy.
One of the cruxes of piezoresistive sensors is their ability to monitor minute pressure changes, making them ideal for applications requiring precision. This includes use in medical devices, automotive applications, and aerospace.
The advantages to keep in mind include:
- High Sensitivity: Due to their construction, they offer exceptionally high sensitivity even for low pressure scenarios.
- Temperature Compensation: Many designs now incorporate temperature compensation, enhancing reliability across varying conditions.
- Small Size: Their compact nature allows integration into various devices without taking up significant space.
However, they often require more sophisticated circuitry for signal processing, which can add to system complexity. Overall, their capability to offer high-resolution measurements makes them a strong contender in the modern sensor landscape.
"Choosing the appropriate sensor type hinges on understanding the specific requirements of your application and the characteristics each sensor brings to the table."
"Choosing the appropriate sensor type hinges on understanding the specific requirements of your application and the characteristics each sensor brings to the table."
In summary, each type of mechanical pressure sensor has its own unique benefits and challenges. Understanding these differences is crucial for making informed decisions based on specific needs in industrial, medical, or technical applications.
Materials Used in Mechanical Pressure Sensors
Understanding materials is quite crucial when it comes to mechanical pressure sensors. The choice of materials not only impacts the sensitivity and reliability of the sensors but also determines their operational lifespan and performance in extreme environments. Selecting the right materials can lead to improvements in precision, durability, and overall efficiency, making this topic more than just an academic exercise. In this section, we will delve into the various materials typically used in the fabrication of these sensors, look into their distinct properties, and also explore emerging materials that are shaping the future of sensor technology.
Common Materials and Their Properties
Mechanical pressure sensors are typically made from materials that can withstand different levels of stress and environmental conditions. Here are some of the most commonly used materials in their manufacture:
- Stainless Steel: Renowned for its corrosion resistance and mechanical strength, stainless steel is often used in pressure sensor housings. Its ability to function in extreme environments—from high temperatures to high humidity—makes it a favorite among manufacturers.
- Silicon: Leveraging its piezoresistive properties, silicon is an essential material in creating micro-machined sensors. Silicon-based sensors are known for their high sensitivity and effectiveness in compact designs.
- Copper Alloys: These alloys are often utilized for Bourdon tube sensors due to their excellent mechanical properties and good thermal conductivity. Copper's malleability allows it to be formed into intricate shapes, providing effective pressure sensing in industrial applications.
- Ceramics: For applications requiring high-temperature resistance, ceramic sensors and components can be employed. Their stability under extreme conditions makes them prime candidates in situations where metals may falter.
Each material has its own unique characteristics that make it suitable for certain applications. For example, while stainless steel is favored for its durability, silicon shines in scenarios where size and precision are critical.
Emerging Materials in Sensor Technology
As technology advances, new materials are continually being developed, contributing to more efficient and reliable mechanical pressure sensors. Here are several noteworthy materials currently making waves:
- Graphene: This carbon allotrope is turning heads for its remarkable conductivity and flexibility. When integrated into pressure sensors, graphene could potentially usher in sensors that are not just lighter but also more responsive.
- Polymer Composites: Engineers are exploring polymers that combine flexibility with strength. This offers new possibilities for sensor designs, especially in applications where weight and flexibility are essential, such as in aerospace.
- Smart Materials: Shape-memory alloys and piezoelectric materials are redefining sensor capabilities. These materials can react to environmental changes dynamically, allowing for greater adaptability in varying pressure conditions.
- Bio-based Materials: The push for sustainability has prompted research into biodegradable materials for sensors. This could have positive implications for environmental conservation in the manufacturing of pressure sensors.
The materials chosen in the design and construction of mechanical pressure sensors can greatly influence their overall effectiveness, emphasizing the need for ongoing research and development in this area.
The materials chosen in the design and construction of mechanical pressure sensors can greatly influence their overall effectiveness, emphasizing the need for ongoing research and development in this area.
With these emerging materials, the field of mechanical pressure sensing is paving the way for innovative applications not previously thought possible. From enhancing accuracy to durability, the future of sensor technology looks promising. As students, researchers, or professionals looking to deepen your understanding, recognizing the importance of materials in pressure sensors can lead to significant insights in their application, development, and functionality.
Applications of Mechanical Pressure Sensors
Understanding the applications of mechanical pressure sensors is pivotal. These devices are not only essential but also quite diverse in their utilization across various sectors. The pressure sensors have proven their worth by contributing to enhance safety, efficiency, and functionality in a host of industries. From industrial plants to the healthcare sector, their role cannot be overstated. When you consider the intricacies of modern systems, the benefits they bring come into sharper focus: improved monitoring, precise control, and increased automation.
Industrial Usage
In industrial settings, mechanical pressure sensors are indispensable for monitoring processes. They are widely used in manufacturing facilities where controlling pressure is critical for safety and productivity. Whether it’s in hydraulic systems or pneumatic actuators, these sensors help keep everything running smoothly. For instance, in a factory that fills bottles under pressure, poor measurement could lead to overflowing or under-filling, impacting both waste and profit.
A few key areas within industrial usage include:
- Process Control: Ensures systems operate within safe limits, thus avoiding disastrous failures.
- Leak Detection: Identifying leaks early helps mitigate risks and saves resources by reducing material loss.
- Performance Optimization: Data from these sensors informs process adjustments that lead to improved efficiency.
Applications in Aerospace
Mechanical pressure sensors also find a home in the aerospace industry. Here, pressure measurements are critical for ensuring the safety and performance of aircraft. From monitoring cabin pressure to ensuring fuel systems maintain optimal levels, these sensors play a crucial role.
For example, cabin pressure sensors help maintain the appropriate atmospheric conditions for passenger comfort and safety. Furthermore, pressure sensors in fuel systems help monitor and manage fuel flow effectively. By ensuring the right pressure, manufacturers can enhance engine performance and fuel efficiency.
A few notable uses in aerospace include:

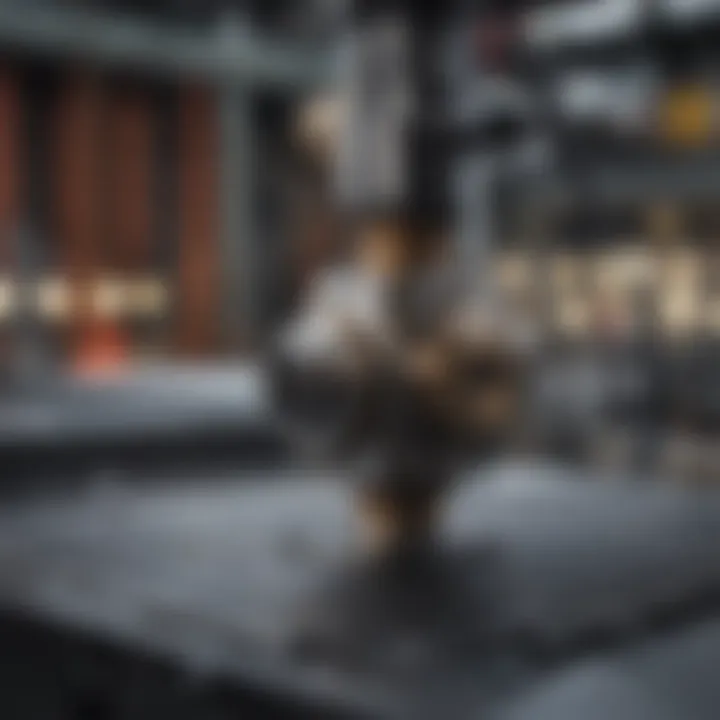
- Fuel System Optimization: Ensures correct fuel delivery to engines.
- Environmental Control: Maintains comfortable cabin conditions.
- Safety Monitoring: Alerts systems to any abnormal pressure conditions that may arise.
Uses in Medical Equipment
The medical field greatly benefits from mechanical pressure sensors as well. Pressure measurement is often crucial in devices like ventilators and anesthesia machines. Accurate pressure tracking is paramount in these applications to ensure patient safety. Any deviation in pressure can lead to serious medical consequences.
For instance, in respiratory support systems, accurate pressure monitoring helps deliver the right amount of air to a patient. Furthermore, in infusion pumps, pressure sensors ensure that medication is administered at precise rates, thus preventing overdoses or underdosage.
Other critical uses in medical equipment include:
- Monitoring Blood Pressure: Essential for managing cardiovascular health.
- Detecting Obstructions: Ensures that respiratory equipment is free from blockages, which could compromise treatment.
- Custom Medical Devices: Tailored solutions using sensors for specialized interventions.
"Mechanical pressure sensors transform raw physical data into key insights, making them vital in modern technology."
"Mechanical pressure sensors transform raw physical data into key insights, making them vital in modern technology."
In summary, mechanical pressure sensors play an integral role across multiple sectors. Knowing how they apply in various fields not only deepens comprehension of their importance but also shines a light on the necessity for ongoing advancements in sensor technology. This ensures that industries can continue to function optimally and safely in a high-pressure world.
Challenges in Mechanical Pressure Sensor Design
In the realm of mechanical pressure sensors, understanding the challenges faced during their design is crucial for enhancing performance and reliability. These devices are instrumental in countless applications, from industrial measurement to medical diagnostics, therefore, addressing these challenges directly contributes to the precision and effectiveness of the technologies relying on them.
Calibration Issues
Calibration stands as one of the foremost challenges in the design of mechanical pressure sensors. This process involves adjusting the sensor readings to align with known standards, ensuring accuracy in measurements. Pressure sensors can drift over time due to various factors: environmental influences, mechanical wear and tear, or even material fatigue. The importance of regular calibration cannot be overstated; it’s critical for maintaining the integrity of data collected during operations.
Here's why calibration issues are particularly significant:
- Precision Maintenance: Accuracy can diminish if sensors are not calibrated correctly. A consistently inaccurate sensor can lead to erroneous readings, which may result in costly downtime or dangerous conditions in industries where safety is paramount.
- Standard Compliance: Various industries are bound by strict regulatory standards that dictate acceptable accuracy for measurements. Failure to maintain compliant sensors can lead to significant liabilities and loss of reputation.
- Cost Implications: Frequent recalibration can be costly for businesses, especially if it requires taking equipment offline. Initial designs that incorporate self-calibrating mechanisms can offset these ongoing expenses, making them more attractive for operational longevity.
In essence, calibration isn’t merely an afterthought; it’s a foundational aspect that can either undergird or undermine the very functionality of mechanical pressure sensors.
Temperature Sensitivity
The second layer of challenges lies in temperature sensitivity, which directly influences sensor performance. Mechanical pressure sensors are affected by temperature fluctuations, causing the readings to shift due to thermal expansion or contraction of materials used in their construction.
Consider the following points regarding temperature sensitivity:
- Measurement Inaccuracy: As temperatures rise or fall, pressure readings can inaccurately reflect the actual environmental conditions. This can have grave implications in sectors like aerospace and pharmaceuticals, where specific temperature profiles are non-negotiable.
- Material Constraints: The materials chosen for sensor construction must undergo rigorous testing to evaluate their behavior across different temperature ranges. Ideally, the chosen materials should exhibit minimal changes in mechanical properties with thermal variations. This necessitates ongoing research into new materials that can withstand diverse operating conditions without sacrificing performance.
- Environmental Consideration: In applications like meteorology or deep-sea exploration, sensors are subjected to extreme conditions. Engineers must incorporate compensatory mechanisms or select materials that can handle such stressors without misrepresenting the pressure they measure.
To navigate these challenges, engineers and designers must engage in thorough materials research and testing, often looking to advances in composites or alloys that provide stability. Collaboration across fields—from material science to precision engineering—can yield designs that tackle these inherent temperature sensitivity issues effectively.
"The reliability and accuracy of mechanical pressure sensors heavily rests upon addressing the challenges within calibration and tempreature response. Without proactive design considerations, the risks associated with measurement errors become amplified."
"The reliability and accuracy of mechanical pressure sensors heavily rests upon addressing the challenges within calibration and tempreature response. Without proactive design considerations, the risks associated with measurement errors become amplified."
Technological Advancements in Sensor Technology
The field of mechanical pressure sensors is not static; it continues to evolve with breakthroughs in technology that enhance performance and usability. Technological advancements are particularly significant in this realm because they not only improve accuracy and efficiency but also broaden the applications of these sensors across various industries. As industries aim for better data management and process automation, these advancements create pathways for innovative solutions that cater to modern demands.
Microelectromechanical Systems (MEMS)
Microelectromechanical systems, more commonly referred to as MEMS, have revolutionized pressure sensing technology. These tiny, integrated devices combine mechanical and electrical components on a single chip. Their size allows them to be deployed in a variety of settings, from automotive applications to consumer electronics.
The precision offered by MEMS sensors provides unparalleled sensitivity. They can detect minute pressure changes, making them invaluable in high-stakes environments where accuracy is essential. Moreover, these systems are typically energy-efficient, which extends their operational life—an important factor for battery-powered devices. Many consider MEMS the backbone of modern sensor technology due to their ability to scale, making them both cost-effective and versatile.
Some key advantages of MEMS technology include:
- Compact Size: This attribute enables sensor integration into tight spaces where traditional sensors would be impractical.
- Low Cost of Production: As manufacturing processes improve, MEMS sensors can be produced at a lower cost, promoting wider adoption.
- Ability to Integrate: MEMS sensors can work alongside other components, fostering advancements in IoT and smart systems.
"The move towards MEMS in pressure sensing signifies not just a technological leap but a foundational shift in how we perceive and utilize sensors in everyday applications."
"The move towards MEMS in pressure sensing signifies not just a technological leap but a foundational shift in how we perceive and utilize sensors in everyday applications."
Wireless Sensor Technology
Wireless sensor technology represents another momentous stride in the mechanical pressure sensor landscape. Traditionally, sensors required physical connections to transmit data, which limited their mobility and flexibility. Wireless technology eliminates this constraint, allowing for more dynamic applications.
These sensors communicate over networks without the need for cumbersome wiring, making installation easier and reducing costs associated with infrastructure. They interact seamlessly with cloud computing systems, enabling real-time data analysis and monitoring from virtually anywhere. This is particularly advantageous in fields like agriculture, where farmers can monitor soil pressure remotely, adapting irrigation practices swiftly to optimize yields.
Key benefits of wireless sensor technology include:
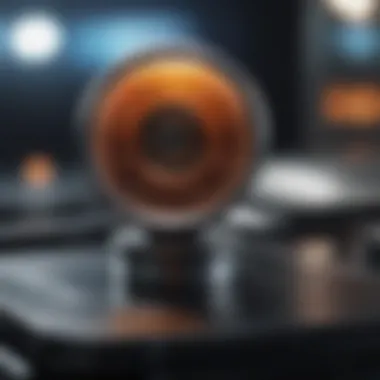

- Enhanced Mobility: Sensors can be placed in hard-to-reach locations without physical constraints.
- Real-Time Monitoring: Data can be accessed instantaneously, providing critical insights for decision-making processes.
- Cost Reduction: Eliminating cables and connectors lowers installation and maintenance costs, a boon for large-scale projects.
In summary, the forward march of technological advancements in sensor technology—most notably through MEMS and wireless capabilities—holds tremendous potential for the future. As these systems become more sophisticated, they promise to elevate mechanical pressure sensors from mere measurement tools to integral components of complex monitoring and automation systems.
The Role of Accuracy and Reliability
Accuracy and reliability are the cornerstones of mechanical pressure sensors. Without them, any form of measurement can become questionable, even misleading. In various fields—be it industrial manufacturing, aerospace engineering, or healthcare—the precision of pressure measurements can directly impact safety, performance, and operational efficiency.
When we talk about accuracy, we refer to how close a measured value is to the actual (true) value. Reliable sensors ensure that these measurements remain consistent over a period or set under the same conditions. A sensor could, for instance, repeatedly provide accurate readings under stable conditions but fail when subjected to external factors like temperature variations. Thus, choosing the right sensor is not just about its specifications but also about understanding the environment in which it will operate.
Standards and Testing Protocols
The integrity of mechanical pressure sensors is largely determined by the standards that govern their design and manufacturing processes. Several organizations, such as the International Organization for Standardization (ISO) and the American National Standards Institute (ANSI), lay out detailed guidelines for sensor testing. Adherence to these standards ensures that the sensors perform reliably across various applications.
In practice, the following steps are crucial for evaluating sensor accuracy:
- Calibration: Regular calibration against known pressure sources helps maintain accuracy.
- Systematic Testing: Testing under varying conditions—temperature fluctuations, humidity levels, and pressure extremes—validates reliability.
- Certification: Obtaining certifications from reputable bodies can signify that sensors have met rigorous standards.
For example, a sensor utilized in a healthcare environment must meet certain guidelines to ensure it operates safely and reliably. The stakes are high; a failure in medical equipment can lead to dire consequences. Hence, testing protocols must be exhaustive.
Impact on Industrial Processes
The ripple effects of accurate and reliable pressure measurement in industry can’t be overstated. In manufacturing plants, a small deviation in pressure can lead to major product defects, increased wastage, or even accidents. Accuracy is especially critical in industries like oil and gas, where minute changes in pressure can indicate leaks or other dangerous anomalies.
For instance, consider a scenario in which a Bourdon tube sensor is employed to monitor the pressure of a high-stakes hydraulic system. If the sensor fails to provide accurate readings, it could result in operational failures that not only halt production but also pose substantial safety risks to personnel.
An effective strategy would be:
- Implementing real-time monitoring systems that continuously compare sensor outputs against established benchmarks.
- Establishing a feedback loop with regular maintenance checks on sensors to spot potential inaccuracies before they escalate.
The interconnected nature of today’s industrial landscape also means that inaccuracies in one area can have cascading effects. Thus, reliability in pressure measurement is not merely an attribute; it's a requisite for smooth and safe operations.
Future Trends in Mechanical Pressure Sensors
As we look to the future, mechanical pressure sensors are poised to undergo significant transformations driven by several trends. Such advancements not only enhance their capabilities but also extend their applications, making them indispensable across various industries. Understanding these trends is crucial for anyone involved in engineering, manufacturing, or technology.
Integration with IoT Devices
The Internet of Things (IoT) is revolutionizing how we approach monitoring and data collection. By integrating mechanical pressure sensors with IoT devices, real-time data transmission becomes feasible, allowing for more responsive and adaptive systems. This integration can facilitate features like predictive maintenance, where sensors can signal when a device is likely to fail based on pressure readings.
One major advantage of IoT integration is mobility. Imagine a manufacturing unit where pressure sensors are hooked up to a central database, with every fluctuation monitored remotely. This not only saves time but also enables quicker decision-making. Furthermore, data analytics can uncover insights related to pressure trends, ultimately optimizing operational efficiency.
- Enhanced Monitoring: Pressure readings can now be transmitted continuously over networks, providing instantaneous feedback.
- Cost Reduction: With predictive maintenance capabilities, companies can reduce downtime and lower operational costs.
- Security Enhancements: As devices are interconnected, there are new opportunities and needs for secure data transmission, ensuring that sensitive information remains safe.
The ability to access sensor data in real time changes the game, allowing professionals to go beyond surface-level observations and tap into deeper, actionable insights.
The ability to access sensor data in real time changes the game, allowing professionals to go beyond surface-level observations and tap into deeper, actionable insights.
Increased Demand in Renewable Energy
The shift towards cleaner energy sources has increased the demand for mechanical pressure sensors. With renewable energy technologies like wind and solar power rapidly gaining traction, these sensors play a vital role in optimizing performance and ensuring safety. For instance, in wind turbines, pressure sensors monitor hydraulic systems that adjust blade pitch based on atmospheric conditions.
Renewable energy applications highlight the versatility of mechanical pressure sensors. Here are some specific areas where they are becoming crucial:
- Hydraulic Systems: In solar thermal systems, sensors help manage fluids effectively, which is key for heat transfer and overall efficiency.
- Environmental Monitoring: These sensors are used to monitor ambient pressure changes, crucial in predicting weather patterns for solar farms.
- Energy Management Systems: Mechanical pressure sensors can integrate with smart grids to enhance energy distribution and reliability.
Investing in mechanical pressure sensors for these applications brings multiple benefits, including improved energy efficiency and compliance with environmental regulations. The trend indicates a shift towards smarter, more responsive energy systems that leverage traditional sensor technologies in innovative ways.
Ending
In wrapping up our discussion about mechanical pressure sensors, it's crucial to understand their pivotal role in various domains. Not only are these sensors integral to modern technology, but they also offer vital accuracy that can make or break processes across industries. As sensor technology continues to evolve, comprehending the functionalities and potentializations of these devices becomes increasingly relevant.
Summary of Key Points
Mechanical pressure sensors serve a multitude of purposes in both industrial and scientific applications. From monitoring pressure in gas pipelines to ensuring safe operation in medical devices, their significance cannot be overstated. Key takeaways include:
- Principles of Operation: Understanding how mechanical pressure sensors work, including the physical principles that drive their functionality.
- Diverse Types and Materials: A look into the various types of sensors such as diaphragm-based and Bourdon tube models, along with emerging materials that enhance performance.
- Applications: Extensive usage across sectors like industrial manufacturing, aerospace, and healthcare, highlighting their adaptability.
- Challenges and Trends: Acknowledgment of obstacles in calibration and temperature sensitivity, paired with discussing future trends such as integration with IoT devices.
Final Thoughts on Mechanical Pressure Sensors
Mechanical pressure sensors are vital in navigating the complexities of modern engineering and science. With their continued evolution, influenced by advances in materials and technology, they are well-poised to meet increasing demands for accuracy and reliability.
The future of pressure sensing technology looks bright—and as the mechanization of our world progresses, these devices will play an ever more significant part in ensuring efficiency and safety across applications. Awareness of their operational principles, strengths, and limitations equips professionals and researchers to leverage mechanical pressure sensors effectively in addressing both current and future challenges.
"In a world where precision is of utmost importance, the role of mechanical pressure sensors stands tall, ensuring that every action counts."
"In a world where precision is of utmost importance, the role of mechanical pressure sensors stands tall, ensuring that every action counts."
Ultimately, the study of mechanical pressure sensors provides profound insights into instrumentation, drawing connections across various disciplines. The implications of their application stretch far beyond mere measurements, seeping into the very fabric of modern technology.