Understanding Plasma Vapor Deposition Technology
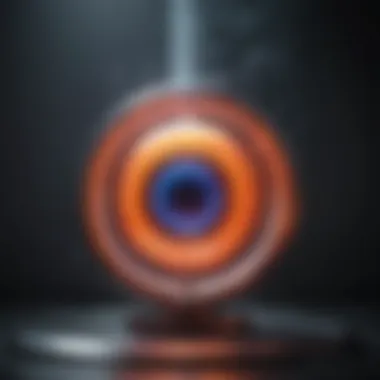
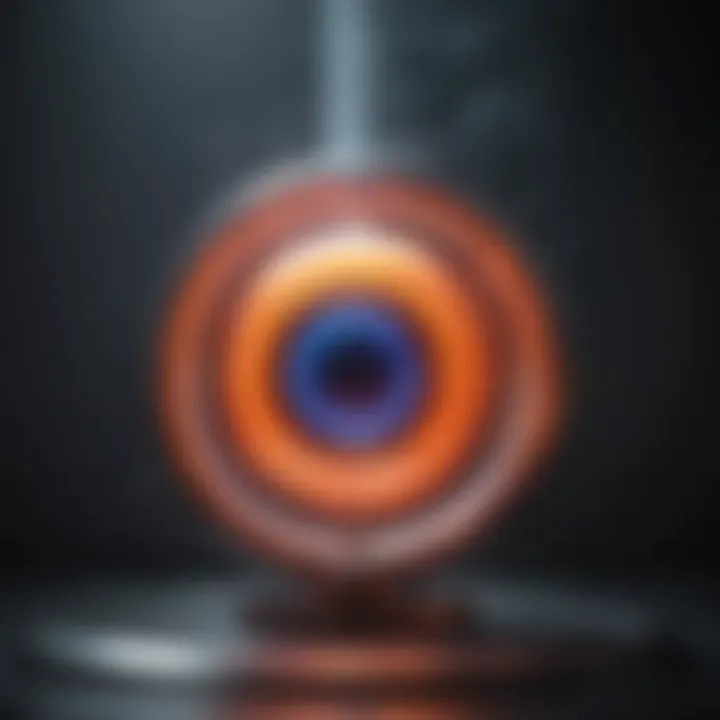
Intro
Plasma vapor deposition (PVD) stands at the crossroads of innovation and practicality, a game changer in the realm of manufacturing and engineering. As industries search for advanced materials, the technique of PVD emerges as a powerful method to apply thin films and coatings. This process employs plasmaāa state of matter where gases are ionized and electrically conductiveāto enhance the surface properties of various substrates. The intersection of plasma physics and materials science makes PVD not just remarkable, but essential for progress.
In this article, we will take a closer look at the key concepts underlying plasma vapor deposition, shedding light on its foundational principles. We will explore current research trends and highlight the fascinating innovations that are propelling PVD into new realms of application. Whether youāre a student, researcher, or industry professional, this examination aims to equip you with a thorough understanding of PVD's significance in modern technology.
Prologue to Plasma Vapor Deposition
Plasma vapor deposition (PVD) has carved out a significant niche in the modern industrial landscape. As we delve into this topic, itās essential to recognize how this method not only revolutionizes surface engineering but also plays a crucial role across several fields, including electronics, optics, and materials science. The ability to apply thin films with such precision brings with it numerous advantages that deserve an in-depth examination.
Definition and Overview
At its core, plasma vapor deposition is a process that involves the deposition of thin films onto a substrate through the interaction of materials in a plasma state. The unique aspect of PVD lies in its dual mechanism of utilizing both vaporization of solid materials and plasma, unlocking an array of possibilities for various applications. In a more straightforward sense, itās akin to painting a surface with highly controlled layers, ensuring enhanced performance and longevity.
This technique stands out for its versatility. The coatings applied can range from metallic to dielectric films, which means it holds sway over an expansive range of propertiesāthese thin films can enhance conductivity or optical transparency, vital for applications in fashionable tech devices or cutting-edge optics. Among professionals and researchers alike, PVD is recognized not merely as a fancy coating technique but as a sophisticated approach that elevates material properties significantly.
Historical Context
Reflecting on the journey of PVD, it is fascinating to note its roots. The journey of plasma technology began in the early 20th century, initially primarily in the realm of physics and chemistry. But in the mid-1970s, the real game-changer happened when researchers thought to harness plasma for material deposition purposes. This innovation opened doors previously thought to be unreachable.
Take the case of the aerospace industry. It was one of the first to appreciate the advantages of PVD, particularly concerning wear resistance on turbine blades. As these applications arose, PVD techniques evolved. The early methods were rather rudimentary. Fast forward, and with advancements in technology, techniques like sputtering and evaporation became widely popular.
In summary, the historical progression of plasma vapor deposition illustrates how a once niche field has burgeoned into a critical player in various industries. Recent innovations continue to redefine the boundaries of what is possible with PVD, fueling further exploration and discovery, making it imperative for students and professionals alike to grasp its significance.
Fundamental Principles of PVD
Understanding the fundamental principles of Plasma Vapor Deposition (PVD) is crucial for grasping its practical applications, significance, and the ongoing advancements in technology. PVD offers a unique way to apply coatings and films that are essential in various industries, from electronics to biomedical applications. This section highlights the core elements of PVD: the physics of plasma, the mechanics of vapor deposition, and how this process interacts with different substrates. Each aspect contributes to the effectiveness and versatility of PVD, making it an area of keen interest for students, researchers, and professionals alike.
Physics of Plasma
At its core, plasma is often described as the fourth state of matter. Itās crucial to understand that plasma differs significantly from gases; it consists of electrically charged particles, including ions and electrons. This charged state allows plasmas to respond strongly to electromagnetic fields, which is vital in PVD processes.
In practical terms, plasma is generated under controlled conditions in a vacuum chamber, allowing for high-energy collisions between particles. The heating from these collisions causes atoms and molecules to be emitted from a solid materialāthis is where the magic begins. The importance of the physics behind plasma in PVD can be boiled down to three key points:
- Energy: The energy levels of the particles in plasma determine the rate of material deposition. Higher energy can lead to more efficient coatings.
- Ionization: Ionized gases create a cloud of charged species that can travel and engage with substrates effectively.
- Reactivity: The reaction of plasma with various materials can enhance adhesion and create unique properties in the coatings, such as increased hardness or chemical resistance.
Mechanics of Vapor Deposition
Vapor deposition is like a ballet of atoms, where precise choreography leads to the desired end product. It involves the transformation of solid materials into a vapor phase, which then condenses onto a substrate to form a thin film. Several distinct methods exist, but let's focus on the essentials of how this works.
The process generally unfolds in three main stages:
- Material Evaporation: The source material is heated through various meansābe it thermal heating, electron-beam evaporation, or laser ablationāleading to its transition into vapor.
- Transportation of Vapor: The vapor travels through the vacuum, avoiding contamination and degradation. This phase is critical as it affects how uniformly the material reaches the substrate.
- Condensation and Film Formation: Upon contact with the cooler substrate, the vapor condenses, leading to film formation. The quality of the film depends not only on the deposition rate but also on factors like temperature, pressure, and substrate material.
Through these steps, one can appreciate how thoroughly careful control can drive the outcome in PVD processes, affecting everything from uniformity to crystallization of the coatings.
Interactions Between Plasma and Substrates
In the world of PVD, how the plasma interacts with the substrate is pivotal for achieving optimal results. These interactions are nuanced and can make or break the quality of the thin films developed.
The key elements to consider include:
- Surface Preparation: For adhesion to occur effectively, substrates often need to undergo surface treatments to promote better bonding with the deposited material.
- Energy Transfer: As plasma contacts the substrate, energy transfer occurs. The degree of this transfer can affect the substrate's properties, like its temperature, which can in turn change how well or poorly the coating adheres.
- Reactivity: Different materials can react differently when exposed to plasma. For instance, metals may yield a different outcome compared to polymers or ceramics.
These intricacies in interaction require meticulous control and understanding, which can be the difference in pushing the boundaries of what PVD can achieve. This variable nature is what makes studying the fundamental principles so compelling.
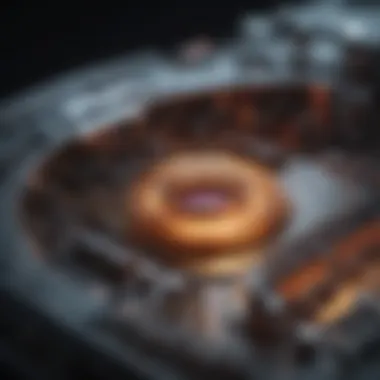
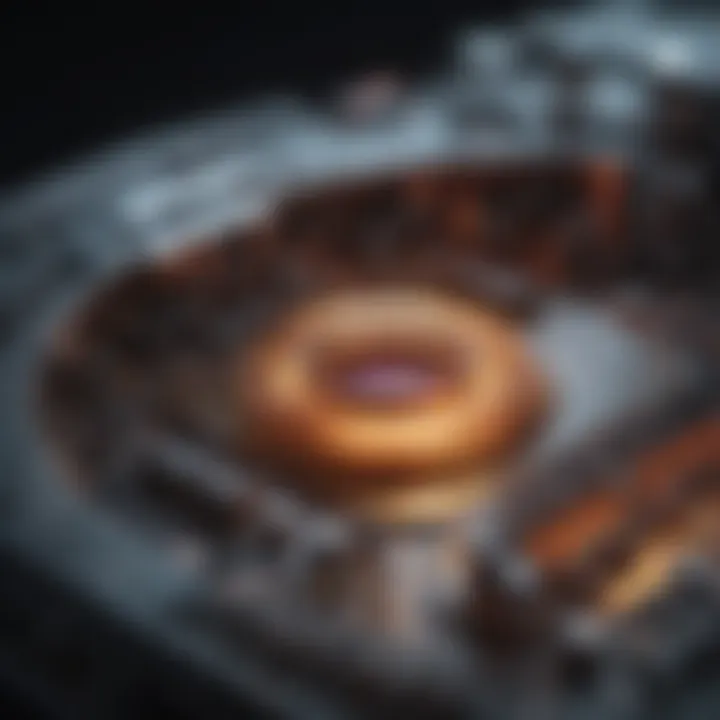
In summary, grasping the fundamental principles of PVD reveals the complexity and dynamism of the processes behind thin-film technology. This understanding aids in pushing forward innovations that enhance the capabilities and applications of PVD across different sectors.
In summary, grasping the fundamental principles of PVD reveals the complexity and dynamism of the processes behind thin-film technology. This understanding aids in pushing forward innovations that enhance the capabilities and applications of PVD across different sectors.
Types of Plasma Vapor Deposition Techniques
Understanding the various techniques employed in plasma vapor deposition is crucial for appreciating the nuances and applications of this technology. Each technique offers different benefits, influencing the performance and suitability for specific industrial applications. The exploration of these methods not only illuminates their individual characteristics but also highlights their collective impact on various fields.
Physical Vapor Deposition
Physical vapor deposition, or PVD, is a method whereby material is vaporized from a solid or liquid source and subsequently condensed onto a substrate to form a thin film. Within PVD, one finds several methods, including evaporation and sputtering.
One notable advantage of PVD is its ability to achieve coatings with excellent adherence and uniformity. The process allows for a wide range of materials, enabling industries to select optimal coatings for particular environments. However, itās worth noting that while the technology lends itself well to many applications, certain limitations on deposition rates can hinder efficiency.
Chemical Vapor Deposition
Chemical vapor deposition (CVD) is a divergent avenue within the realm of vapor deposition techniques. Unlike PVD, CVD relies on chemical reactions to deposit material onto substrates, typically yielding dense and uniform films. This technique holds significance particularly in semiconductor manufacturing, where precision and uniformity are paramount.
There is, however, a price to pay in terms of capital costs and complexity. The equipment for CVD can be intricate, requiring careful controls and materials that can lead to potentially hazardous byproducts. Nevertheless, the end results often justify the means, as CVD can produce coatings that boast high performance and tailored properties, such as electrical conductivity or chemical resistance.
Sputtering Techniques
Sputtering techniques are another formidable component of plasma vapor deposition methods. This process involves bombarding a target material with energetic ions, causing atoms to be ejected and then deposited onto a substrate. Sputtering enjoys the reputation of being highly versatile, applicable to various materials including metals, ceramics, and even polymers.
The advantages here include excellent film quality and the capability to deposit films at much lower temperatures than traditional PVD methods. This lower thermal requirement establishes sputtering as an ideal choice for delicate substrates that may be damaged by excessive heat. However, the complexity of the equipment and the need for maintaining a vacuum environment can be seen as areas for improvement.
Ion Beam Deposition
Ion beam deposition is perhaps the most sophisticated among the PVD techniques. This method uses an ion beam to target a specific material, which is subsequently deposited onto the substrate under vacuum conditions. The precision of ion beam deposition makes it particularly attractive for high-tech applications in microelectronics and optics.
Itās known for producing thin films with exceptional accuracy and control over thickness and composition. Yet, similar to its counterparts, ion beam deposition isnāt without its hurdles, primarily regarding cost and time efficiency. The complexity of the process can turn away smaller enterprises that may not have extensive resources.
In summary, the types of plasma vapor deposition techniques offer a diverse set of capabilities suited to a range of applications. Each has its own inherent benefits and challenges that must be weighed when considering the best method for a given project. By examining these techniques closely, one gains insight not only into the workings of PVD but also into its transformative impact on modern technology.
Advantages of Using PVD
When discussing plasma vapor deposition, it's crucial to take a moment to appreciate the advantages this technology offers over traditional methods of coating and thin film applications. Not only does PVD boast exceptional attributes in surface quality and environmental sustainability, but it also provides specific benefits that can make a significant difference across various industries.
Surface Quality and Uniformity
One of the standout benefits of PVD lies in its ability to achieve an impeccable surface quality and uniformity on substrates. In this realm of technology, the term 'surface quality' is no mere buzzword. In essence, it refers to how smooth and even a coating appears on a substrate after the PVD process. The consistency is achieved through the meticulous layer-by-layer application of material in a vacuum. Each deposition results in coatings that are often superior compared to those produced by other methods like electroplating or painting, which can be quite variable.
- Thinness and Precision: PVD allows for the creation of extremely thin coatings, sometimes just a few nanometers thick. This precision ensures that minimal change occurs in the dimensions of the base material, a crucial element when working with delicate components.Pr
- Adhesion: The coatings deposited via PVD have excellent adhesion properties. This durability comes from the way the atoms bind to the surface, leading to superior resistance against wear and corrosion. For industries like electronics, this means longer-lasting components and improved performance.
- Aesthetic Appeal: In sectors like optics, the visual uniformity of the coating cannot be overstated. The clarity and brilliance achieved in optics through PVD can elevate an ordinary product into something remarkable, helping companies stand out in a crowded marketplace.
"PVD technology transforms the very nature of materials by enhancing their physical properties and aesthetic value, serving as a game-changer for many applications."
"PVD technology transforms the very nature of materials by enhancing their physical properties and aesthetic value, serving as a game-changer for many applications."
Environmental Considerations
In a world increasingly focused on sustainability, PVD stands out for its environmentally friendly aspects when compared to more traditional coating techniques. This isn't just about following trends; it speaks directly to the responsible practices that modern industries must adopt.
- Reduced Waste: The efficiency of the PVD process contributes to lower waste production. Unlike many wet processes which require large amounts of chemicals, PVD utilizes solid sources for material deposition. Hence, there is minimal leftover material that needs disposal.
- Minimal Hazardous Emissions: The related chemical vapor deposition methods generally produce harmful byproducts and volatile organic compounds (VOCs) that pose risks to human health and the environment. PVD minimizes these emissions, offering a safer alternative.
- Conserving Resources: By requiring less energy than some alternative deposition techniques, PVD is a practical choice for resource conservation. Innovative technology enhancements are continuously driving this aspect further, aligning industry practices with global sustainability goals.
The advantages of PVD, particularly in terms of surface quality and its environmental alignment, underscore its significance in modern applications. As conversations around sustainability grow more nuanced, the ability of technologies like PVD to contribute positively to both product performance and ecological responsibility will likely become a cornerstone of industry standards.
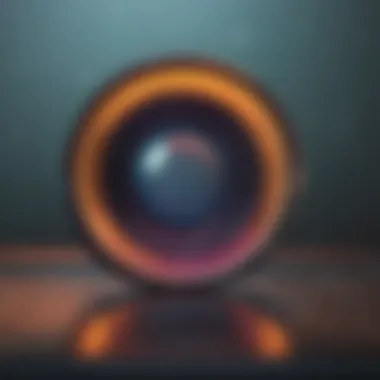
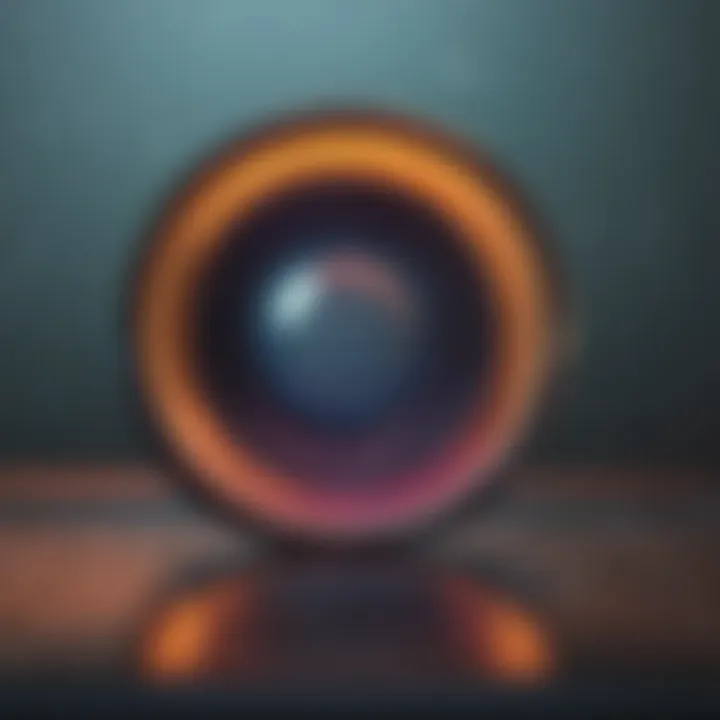
Challenges and Limitations
In any tech-driven field, challenges and limitations can't be brushed aside. Theyāre like that little pebble in your shoe when youāre trying to take a long hikeāannoying, but you gotta address it. For Plasma Vapor Deposition (PVD), knowing these hurdles is essential for students, buyers, and professionals alike who are pursuing its extensive applications across diverse industries.
Process Complexity
PVD techniques, though cutting-edge, often come loaded with complexities that can prove daunting. Setting up the machinery and calibrating the parameters is no walk in the park. Multiple factors must be harmonized, such as temperature management, pressure levels, and plasma characteristics. A slight misstep in these areas can lead to ineffective coatings, adversely affecting the final productās performance.
In addition, expertise is imperative when operating PVD systems. Not all technicians can handle the conventions and specifics of each methodology, such as sputtering or ion beam deposition. Specialized training is crucial to mitigate errors that could derail a project. When investing in PVD technology, whether for electronics or optics, recognizing the intricacy of the process is paramount.
This complexity can also translate into longer production times and increased costs. Each trial and error cycle takes time and resources, raising the stakes for industries needing rapid production. It often means balancing efficiency with precision, which places constraints on lead times. Here's a quick rundown of complexities in the PVD process:
- Setup and Calibration: Careful alignment of equipment and conditions is critical.
- Monitoring and Adjustment: Real-time feedback mechanisms are generally needed.
- Training Requirements: Skilled personnel are necessary to navigate the setups.
"The right mix of experience and technology can make or break PVD effectiveness."
"The right mix of experience and technology can make or break PVD effectiveness."
Material Limitations
While PVD boasts a broad spectrum of materials that can be used, it isnāt without its restrictions. Certain materials may not respond well during the deposition process, leading to suboptimal results. For instance, some semiconductor substrates can be tricky. They require precise environmental conditions; otherwise, reliability suffers and defects can occur.
Moreover, some coatings might not adhere properly to specific substrates, leading to issues like delamination or wear. Not every material is compatible with every technique; hence, manufacturers must conduct extensive testing to determine how well a particular coating will perform given their specific circumstances. Hereās a brief look at some material limitations:
- Adhesion Issues: Not all materials bond well, influencing durability.
- Thermal Sensitivities: Some substrates can warp under deposition temperatures.
- Cost-Effectiveness: Premium materials often come with hefty price tags, risking budget overruns.
In summary, while PVD offers a pioneering approach to thin-film technology, understanding its challenges, particularly process complexities and material limitations, is crucial for rational decision-making. By acknowledging these elements, industries can better leverage the technology for their unique applications.
Applications of Plasma Vapor Deposition
Plasma vapor deposition serves a crucial role in various industries due to its unique ability to deposit thin films that exhibit desirable properties like durability and reduced friction. This technology finds applications in sectors from electronics to medical devices, providing efficiency and enhancing product performance. Understanding these applications is essential not just for theoretical knowledge but for practical implementation and innovation in technology.
Electronics Industry
The electronics industry is one of the primary beneficiaries of plasma vapor deposition techniques. In this field, the demand for effective coatings is ever-present. One significant application is in the manufacturing of semiconductors, where PVD is utilized to create thin layers of material that are essential for integrated circuits. These thin films contribute to improved electrical performance while minimizing physical space, which is vital for increasingly miniaturized devices.
Moreover, PVD is instrumental in enhancing the surface properties of electronic components. For instance, using titanium nitride as a coating material can provide a hard, wear-resistant surface that not only prolongs the life of the devices but also improves their overall functionality. This collision of durability and lightness creates components that are efficient, which is a key performance indicator in modern electronics.
Optics and Photonics
In optics, plasma vapor deposition showcases its prowess through the development of high-quality coatings on lenses, filters, and mirrors. Coatings deposited via PVD can significantly enhance the transmission and reflection of light, which are necessary traits for optical devices. This is especially relevant in applications involving lasers and high-precision instruments.
Furthermore, thin films can alter the optical properties of surfaces, allowing for anti-reflective coatings or mirror-like finishes that boost performance. This tailoring of optical characteristics is pivotal in the design of modern consumer electronics such as smartphones and televisions, where display quality is paramount. Additionally, the use of PVD in producing multilayer coatings extends into both scientific research and commercial products, underscoring its versatile applicability in the realms of optics and photonics.
Biomedical Applications
When it comes to biomedical applications, the role of plasma vapor deposition cannot be overstated. Medical devices require not only functionality but safety as well when interacting with biological environments. PVD can be utilized to create coatings that enhance biocompatibility and reduce bacterial adhesion on surgical instruments and implants. For example, titanium and its alloys can be coated using PVD to improve their integration into human tissue, significantly increasing the success rates of implants.
In addition to implants, PVD techniques are also applied in the creation of drug delivery systems. By controlling the loading capacity and release rates through the structure of the thin films, scientists can design more effective treatment methods. From stents to prosthetics, the innovations driven by plasma vapor deposition in the biomedical field show promise for improving patient outcomes and reducing infection rates.
"PVD is not just a technique; it's a gateway to advancements across industries, changing the very fabric of how products are made and consumed."
"PVD is not just a technique; it's a gateway to advancements across industries, changing the very fabric of how products are made and consumed."
Recent Innovations in PVD Technology
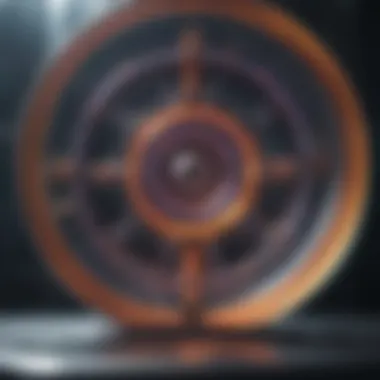
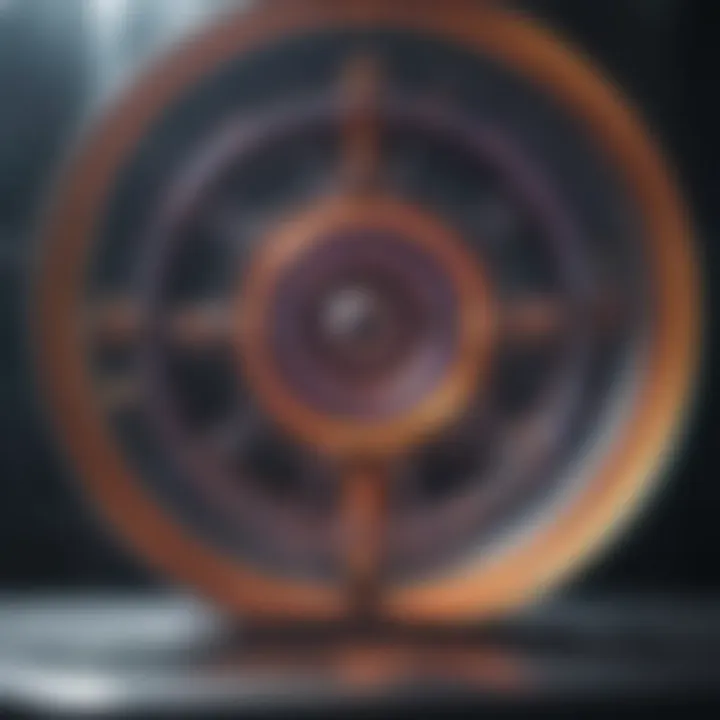
Recent developments in plasma vapor deposition (PVD) technology have significantly transformed the landscape of thin film applications. As industries rely on the consistent performance and durability of coatings, staying abreast of innovations becomes crucial. These advancements not only enhance material properties but also streamline processes, making PVD increasingly valuable in various sectors.
Advancements in Materials Development
The evolution of materials used in PVD is paramount. New materials designed for specific applications have emerged, offering improved performance characteristics. For instance, high-temperature superconductors and multi-layer coatings are now commonplace and cater to specialized needs in fields like aerospace and electronics.
- Novel Alloys and Composites: Recent work focuses on combinations of metals and ceramics to create coatings that could withstand extreme conditions. These materials not only offer superior hardness but also maintain integrity under thermal stress.
- Nanostructured Films: There's a surge in using nanotechnology to develop films with enhanced properties such as increased strength and lighter weight. These films are particularly significant in automotive and aerospace applications, where weight reduction can lead to improved fuel efficiency.
- Eco-Friendly Materials: Amid growing ecological concerns, thereās a push towards utilizing non-toxic materials in PVD processes. This shift not only addresses environmental impacts but also aligns with increasing regulations focused on sustainability.
The ongoing pursuit for innovative materials is not just about performance; it's about shaping a sustainable future in manufacturing and product development.
The ongoing pursuit for innovative materials is not just about performance; it's about shaping a sustainable future in manufacturing and product development.
Efficiency Improvements in Processes
Efficiency in PVD processes is another area where recent innovations shine. By optimizing techniques, manufacturers can increase throughput, reduce costs, and minimize waste.
- Process Automation: The integration of advanced robotics and AI has made it possible to automate PVD systems, allowing for more precise control over coating parameters. This not only enhances repeatability but also significantly reduces human error in the process.
- Real-Time Monitoring: Implementing sensors and data analytics in PVD chambers supports real-time process optimization. Operators can now monitor conditions consistently, which enables swift adjustments that maintain coating quality.
- Temperature and Pressure Control: Innovations targeting more effective regulation of substrate temperature and chamber pressure lead to improved adhesion and uniformity of coatings.
Overall, the advancements in materials and efficieny improvements within PVD technology signify a promising future for the technique. These innovations will undoubtedly impact various applications, providing enhanced performance and contributing to a more durable, sustainable path in manufacturing.
Future Perspectives for Plasma Vapor Deposition
The ongoing evolution of plasma vapor deposition technology reveals promising advancements that could redefine its application in various sectors. As we glance toward the future, we encounter essential elements like sustainability, customization, and the integration of advanced materials. Each of these factors plays a vital role in enhancing the overall utility of PVD processes, making it a topic worth close examination.
Emerging Trends
The landscape of plasma vapor deposition is witnessing notable trends that align with current industrial demands. Here are several key developments:
- Eco-Friendly Techniques: Environmental concerns are at the forefront for many industries. Emerging PVD processes are focusing on reducing waste and energy consumption. Techniques that harness alternative energy sources, such as solar or wind, are gaining traction.
- Enhanced Material Variety: There is a notable increase in research aimed at developing new materials suited for PVD. Materials like graphene, being lightweight and strong, are becoming increasingly relevant, pushing the boundaries of what can be achieved with PVD technology.
- Smart Manufacturing: Integrating PVD with smart manufacturing practices is another trend to watch. Automation and data analytics can optimize processes, ensuring higher precision and efficiency in thin film applications. This transition allows for real-time quality assessments, which is necessary for industries such as electronics that require stringent specifications.
In light of these trends, companies employing PVD technology can enhance their competitive advantages while staying relevant in rapid industrial shifts.
Potential Areas for Research and Development
The horizons for plasma vapor deposition technology extend well into the realm of research and development. Here are several potential areas ripe for exploration:
- Nanostructured Coatings: Investigating ways to enhance the properties of coatings at the nanoscale. Research can ca.optimize adhesion, durability, and functionality, opening up avenues in fields like biomedical implants or high-performance consumer goods.
- Functional Film Development: Developing films that serve multiple purposes could provide substantial benefits. For example, creating coatings that are not only protective but also possess electrical conductivity or thermal management properties. These kinds of innovations could enhance the functionality of electronic devices significantly.
- Cross-Disciplinary Approaches: A potential area lies in the intersection of PVD with fields like nanotechnology and biotechnology. Collaborative research could yield new coatings that cater to specific needs in agriculture or healthcare, expanding the scope of PVD applications.
Furthermore, fostering collaborations between academic institutions and industry could stimulate breakthroughs that transform how PVD technology is perceived and utilized in the coming years.
Future perspectives hold a treasure trove of possibilities for expanding the boundaries of plasma vapor deposition, influencing its role across various industries.
Future perspectives hold a treasure trove of possibilities for expanding the boundaries of plasma vapor deposition, influencing its role across various industries.
The End
Wrapping things up, this article sheds light on the pivotal role of Plasma Vapor Deposition (PVD) in modern technology and industry. Understanding PVD isnāt merely an academic exercise; itās essential for grasping how coatings and films can enhance material properties across a myriad of applications. The seamless integration of PVD into sectors like electronics and optics illustrates its significance in fostering innovation and improving performance.
Summary of Key Points
- Definition: Plasma Vapor Deposition is a process that applies thin films to surfaces using the properties of plasma to enhance adhesion and durability.
- Techniques: Different methodologies, such as Physical Vapor Deposition and Chemical Vapor Deposition, have distinct applications and advantages.
- Environmental Benefits: PVD processes are noted for lower emissions compared to traditional coating methods, making them more environmentally friendly.
- Challenges: Despite its many advantages, PVD faces hurdles like complexity in operations and limitations with certain materials.
- Future Prospects: Emerging trends indicate a strong focus on improving efficiency and exploring new materials, which could significantly broaden the scope of PVD in the coming years.
Final Reflections on PVD
As we look forward, the potential of Plasma Vapor Deposition seems vast and inviting. Its ability to improve material propertiesābe it in terms of strength, corrosion resistance, or aesthetic appealāpositions it as a cornerstone technology in several industries. The contributions of PVD toward the development of lightweight, durable electronic components and high-performance optical devices cannot be overstated.
For those working within technology sectors, PVD is not just a topic for discussion; it's a tool that can lead to practical advancements, driving innovation forward. Its adaptability and capability to integrate new materials feed into a long-term vision of sustainable progress.
For those working within technology sectors, PVD is not just a topic for discussion; it's a tool that can lead to practical advancements, driving innovation forward. Its adaptability and capability to integrate new materials feed into a long-term vision of sustainable progress.
In summary, Proficient knowledge of PVD methods and applications is not only beneficial but necessary for staying relevant in an ever-evolving technological landscape.