In-Depth Analysis of 7075 Metal: Composition and Uses
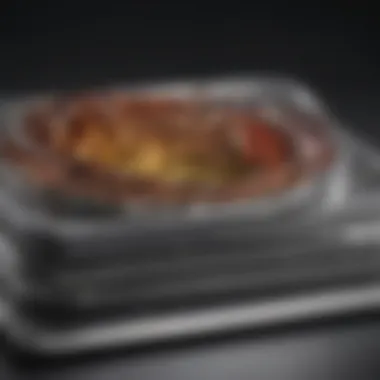
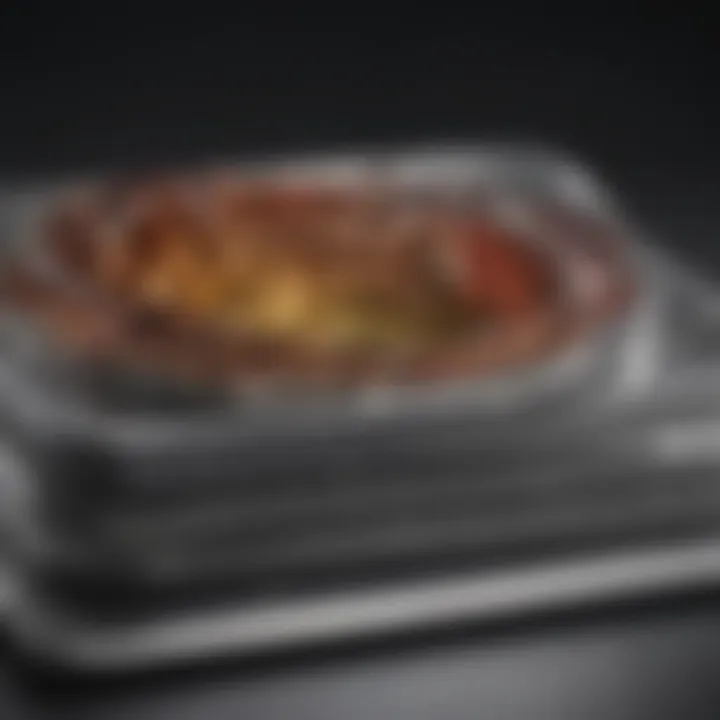
Intro
7075 metal is a high-strength aluminum alloy that is widely recognized in engineering and manufacturing industries. Understanding the specific elements of its composition and properties is crucial for professionals who work with this material. Its application ranges from aerospace structures to military equipment.
This article will delve into the composition, characteristics, and applications of 7075 aluminum alloy. The aim is to provide the reader with an informed perspective on how this material can be utilized effectively in various contexts.
Key Concepts
Definition of the Main Idea
7075 aluminum alloy is primarily known for its exceptional mechanical properties, particularly its strength-to-weight ratio. It is categorized under the 7000 series of aluminum alloys, which are primarily composed of zinc as the major alloying element.
Overview of Scientific Principles
The effectiveness of 7075 metal is derived from its unique blend of metals. Typically, it includes components like magnesium and copper along with zinc, which significantly enhance its properties. This alloy maintains a high level of corrosion resistance compared to other alloys while offering remarkable tensile strength.
"7075 aluminum alloy is often used in situations where strength is paramount and weight savings is critical."
"7075 aluminum alloy is often used in situations where strength is paramount and weight savings is critical."
Current Research Trends
Recent Studies and Findings
Recent research on 7075 metal focuses on improving its fatigue resistance and surface treatments that enhance its corrosion properties. For instance, studies have shown that applying anodic oxidation can increase resistance to wear and fatigue, making it suitable for even more demanding applications.
Significant Breakthroughs in the Field
One significant breakthrough in working with 7075 aluminum is the development of heat treatment processes that optimize its performance. Advanced heat treatment techniques lead to an improvement in the overall strength of the alloy, making it a prime candidate for industries requiring both durability and lightness.
In summary, 7075 metal is a critical material in various engineering practices. Its unique properties and ongoing research developments reflect its importance in modern manufacturing and engineering sectors.
Preface to Metal
7075 metal is a high-strength aluminum alloy that has gained recognition for its remarkable mechanical properties and resilience to various forms of stress. This alloy is widely utilized across multiple industries, particularly where performance is critically important. Understanding its history, composition, and the advantages it brings to engineering will provide deeper insights into its application and relevance today.
Historical Context
The development of 7075 aluminum alloy can be traced back to World War II, when there was a high demand for materials that combined lightweight characteristics with exceptional strength. This alloy was originally designed for applications in the aerospace sector, where every ounce of weight saved could contribute to improved fuel efficiency and performance. Over the decades, as technology advanced, the applications of 7075 expanded significantly. It has become a preferred material not just for aerospace applications but also for military, automotive, and sports equipment manufacturing. 7075’s development marked a significant advancement in metallurgy and has consistently been at the forefront of aluminum alloy research.
Current Relevance of Alloy
Today, 7075 aluminum maintains its status as one of the highest strength aluminum alloys available. Its applications continue to grow, especially in sectors where a combination of strength, lightweight nature, and corrosion resistance are essential. The growing focus on lightweight construction in industries such as automotive and aerospace, in part driven by sustainability initiatives, has amplified the demand for materials like 7075. Furthermore, modern manufacturing techniques, including advanced machining and additive manufacturing, allow for more efficient use of 7075. This has led to innovative products that leverage the material’s favorable properties. 7075 is certainly a critical player in contemporary engineering practices, demanding attention not just for its mechanical capabilities but also for its adaptability in diverse applications.
Chemical Composition of Metal
The chemical composition of 7075 metal significantly influences its properties and applications, marking it as a pivotal aspect of its overall utility. Understanding the alloy's specific elements and their interactions is crucial for professionals in engineering and manufacturing. The composition not only dictates mechanical performance but also informs decisions about which environments the alloy can endure. Therefore, analyzing this section provides insights necessary for optimal application across various fields.
Primary Alloying Elements
7075 aluminum is predominantly an aluminum-zinc alloy, where the primary alloying elements include zinc, magnesium, copper, and small additions of other metals.
- Zinc - Typically the major alloying element, zinc contributes to the alloy's strength and hardness. The higher the zinc content, the greater the potential for stress corrosion cracking, which is a factor to consider in application.
- Magnesium - This element enhances the alloy's resistance to corrosion and improves weldability. The magnesium content also influences the toughness of the material, especially when combined with zinc.
- Copper - Present in smaller quantities, copper imparts additional strength but can also make the alloy more susceptible to corrosion under certain conditions, which must be managed depending on the intended application.
- Other elements - Manganese, silicon, and chromium are also present in trace amounts. Their contribution, while less notable individually, collectively enhances the alloy's overall performance in specific conditions.
The combination of these elements allows 7075 to exhibit high strength, making it particularly suited for structural applications where performance is critical.
Variations in Composition
Variations in the composition of 7075 metal can arise from different tempering processes. Each temper brings attributes to the aluminum alloy’s overall properties.
- T6 Temper - This is the most common form of 7075 alloy, known for its high strength. It involves solution heat treatment followed by aging which locks in the alloy's hardness.
- T651 Temper - Similar to T6 but includes additional processes to relieve stresses, this variation enhances machinability at the cost of some strength.
- Other Tempers - Variations like T73 and T76 exist to cater to specific environmental conditions and applications, each tailored with slight adjustments to composition.
"Choosing the correct temper is essential for determining the application suitability of 7075 metal, influencing performance and longevity."
"Choosing the correct temper is essential for determining the application suitability of 7075 metal, influencing performance and longevity."
These alterations can lead to significant distinctions in mechanical properties. They must be carefully considered to ensure the right balance between strength, workability, and resistance to environmental factors.
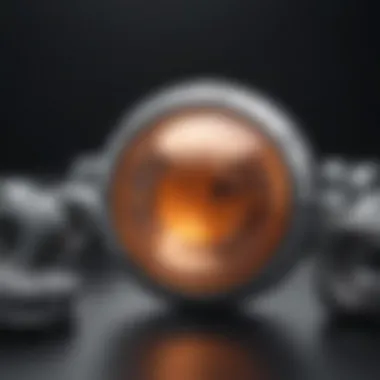
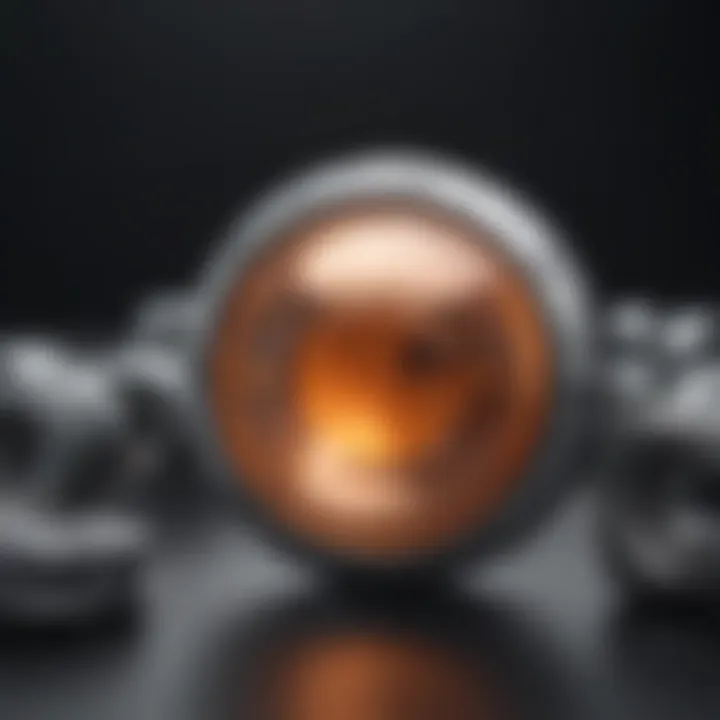
In summary, the chemical composition is crucial for the performance of 7075 metal. Understanding its primary alloying elements and variations provides the basis for its successful application in diverse industries. This knowledge is particularly valuable for students and professionals seeking a comprehensive grasp of materials science.
Manufacturing Processes of Aluminum
The manufacturing processes of 7075 aluminum are crucial for its application and performance. Understanding these processes allows for better manipulation of the alloy's properties, aligning production techniques with the specific needs of various industries. Each method impacts the final attributes of the alloy, such as its mechanical strength, workability, and resistance to corrosion.
Manufacturing involves careful selection of methods and techniques tailored to the desired end use of the metal. This section explores the primary techniques used to process 7075 aluminum, focusing specifically on casting techniques and forming and machining processes.
Casting Techniques
Casting is a fundamental method used to shape metal by pouring it into a mold. In the case of 7075 aluminum, several casting methods are suitable due to the alloy's characteristics. Common techniques include sand casting, die casting, and permanent mold casting. These methods allow for the creation of complex geometries often required in aerospace and automotive components.
- Sand Casting: This method uses a mixture of sand and a binding agent to create a mold. It is suitable for low-volume production and intricate designs. However, it may result in a rougher surface finish compared to other techniques.
- Die Casting: This high-pressure process forces molten aluminum into a mold. It is known for producing high-volume parts with excellent dimensional accuracy. Though the initial cost of die casting equipment is high, the per-unit cost decreases significantly with increased production.
- Permanent Mold Casting: This technique involves using reusable molds, allowing for better surface finish and dimensional control. It can bridge the gap between sand and die casting in terms of production rates and cost efficiency.
While casting techniques can define the basic shape of a product, the selection of the technique greatly influences the performance qualities of the final part, such as strength and ductility.
Forming and Machining Processes
Once casting is done, forming and machining operations are often required to achieve the final specifications of 7075 aluminum components. These processes are essential for enhancing dimensional accuracy and surface quality. The standard methods include extruding, forging, and machining.
- Extrusion: In this process, heated 7075 aluminum is forced through a die to create long shapes with uniform cross-sections. It's widely used in producing components for aircraft structures due to its capability to produce strong yet lightweight profiles.
- Forging: This mechanical deformation process involves shaping the metal by applying compressive forces. For 7075, forging is advantageous as it enhances the grain structure, improving strength properties. It is commonly used in applications that require high durability, like aerospace parts.
- Machining: After forming, precision machining is often employed to achieve the required tolerances. Techniques like milling, turning, and drilling help in creating specific features on 7075 aluminum products. This step is critical for ensuring that parts fit correctly within complex assemblies, as found in the aerospace sector.
7075 aluminum, with its unique combination of strength and lightweight nature, is essential in applications where performance and reliability are paramount.
7075 aluminum, with its unique combination of strength and lightweight nature, is essential in applications where performance and reliability are paramount.
Physical Properties of Metal
The physical properties of 7075 metal are essential for understanding its performance in various applications. These characteristics influence how the material behaves under different environmental conditions. Among the key aspects of physical properties are density, weight, thermal conductivity, and electrical conductivity. Understanding these factors helps engineers and manufacturers choose suitable materials for their projects.
Density and Weight
7075 aluminum alloy is known for its low density, typically around 2.81 g/cm³. This makes it lightweight and desirable for applications where weight reduction is paramount. The low weight of 7075 allows for easier handling and transportation during manufacturing and construction processes. The high strength-to-weight ratio also allows for the development of strong structures without significant mass.
Important points about density and weight include:
- Impact on Aerospace Applications: In aerospace, reducing weight can improve fuel efficiency and overall performance. 7075 is frequently used in aircraft components, where every gram counts.
- Impact on Material Selection: Designers factor in density to optimize their materials for strength and performance. A balance between weight and structural integrity is crucial in engineering.
- Variation Factors: While the density is relatively consistent, slight variations can occur based on specific alloying elements used in formulation.
Overall, the density and weight of 7075 metal provide significant advantages in design and apply in numerous industries requiring durable yet lightweight materials.
Thermal and Electrical Conductivity
Thermal conductivity in metals dictates how efficiently heat transfers through the material. For 7075 aluminum, thermal conductivity is about 130 W/m·K. This property is important in thermal management applications, where heat dissipation is vital for performance and safety.
In terms of thermal properties:
- Heat Dissipation: Applications that involve high temperatures, such as aerospace components, benefit from 7075's ability to manage heat effectively.
- Design Considerations: Engineers must consider thermal expansion alongside conductivity. 7075 experiences expansion with temperature changes, and this can influence the design of assemblies.
Regarding electrical conductivity, 7075 has lower conductivity than other pure aluminum alloys. The electrical conductivity is about 30% IACS (International Annealed Copper Standard). This makes it less suitable for applications demanding high electrical conductivity but serves well in structural roles where electrical characteristics are less critical.
Important notes about thermal and electrical conductivity:
- Importance in Welding: The lower conductivity of 7075 can affect the welding process, requiring more power and careful control during fabrication.
- Applications in Specific Industries: While not optimal for electrical applications, its thermal characteristics are advantageous in some industrial settings, such as automotive heat exchangers.
The understanding of both density and conductivity makes 7075 aluminum a solid choice for specific high-performance uses, particularly in industries where both weight and heat management are crucial factors.
Mechanical Properties of Aluminum
The mechanical properties of 7075 aluminum are pivotal in understanding how this alloy performs under various conditions. 7075 is particularly respected for its high strength, which is essential in applications where load-bearing capabilities are critical. Engineers and manufacturers often seek materials that can withstand stresses without succumbing to fatigue or deformation.
This alloy exhibits a combination of tensile strength, yield strength, fatigue resistance, and impact resistance, making it a prime choice for demanding industries such as aerospace and automotive. Knowing the specific mechanical attributes can aid in selecting the right material for a project, ensuring structural integrity and safety in design.
Tensile Strength and Yield Strength
Tensile strength refers to the maximum amount of tensile (pulling) stress that a material can endure before failing. In 7075 aluminum, the tensile strength can reach up to 700 MPa, depending on the temper and heat treatment. This high tensile strength is advantageous for components that experience significant loads.
Yield strength is the point at which a material begins to deform permanently. For 7075, yield strength values can range around 570 MPa, making it exceptionally resilient. The increase in strength correlates with certain alloying elements, particularly zinc and copper, which enhance the overall stability of the structure.
What makes these properties notable is their contribution to the reliability of components made from 7075. Applications such as aircraft frames or automotive parts demand materials that not only resist deformation but also maintain functionality over time.
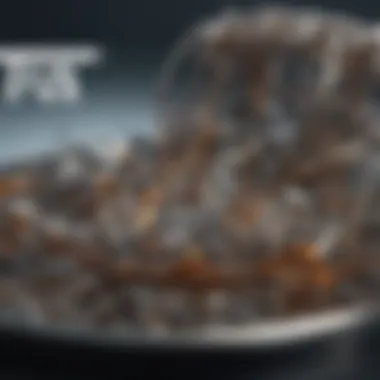
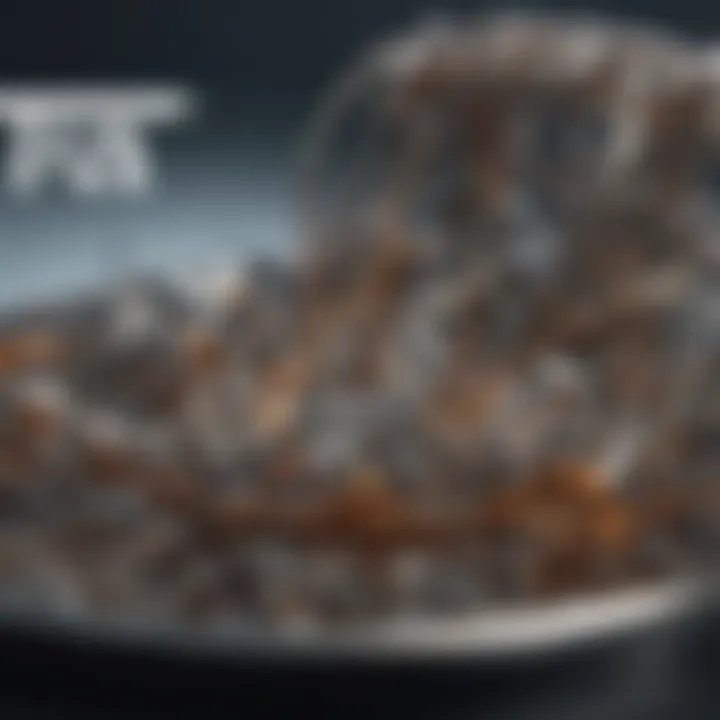
Fatigue Resistance
Fatigue resistance is crucial for items that face cyclic loading. It describes a material's ability to withstand repeated stress without succumbing to failure, a vital characteristic for components used in dynamic environments.
7075 aluminum has been engineered to provide excellent fatigue resistance, which is key in applications like aerospace, where parts undergo repeated load cycles over their lifecycle. Researchers have noted that the alloy's fatigue strength can be significantly influenced by heat treatment and microstructural characteristics.
Understanding the fatigue limits of 7075 allows engineers to predict how components will perform under operational stresses. This insight is integral for safety assessments and design optimizations, ensuring longevity and reliability in critical applications.
Impact Resistance
Impact resistance refers to the ability of a material to absorb energy during an impact without fracturing. 7075 aluminum's impact resistance is noteworthy for situations where sudden forces may be encountered.
In aerospace and military contexts, components are subjected to harsh conditions, making impact resistance a decisive property. The alloy’s ability to withstand impact helps in minimizing catastrophic failures during unexpected situations.
However, while 7075 demonstrates considerable impact resistance, it is important to recognize limitations. Under certain conditions, like extreme temperatures or corrosive environments, the performance may vary. Therefore, understanding the conditions under which the material will operate aids in making better choices for specific applications.
"The diverse mechanical properties of 7075 aluminum illustrate why it is revered in industries demanding high performance and reliability."
"The diverse mechanical properties of 7075 aluminum illustrate why it is revered in industries demanding high performance and reliability."
By analyzing tensile strength, yield strength, fatigue resistance, and impact resistance, a comprehensive picture emerges, highlighting why 7075 aluminum remains a favored choice in engineering and manufacturing. Understanding these properties is essential for utilizing this alloy effectively.
Corrosion Resistance in Alloy
Corrosion resistance is a critical aspect when discussing the performance and longevity of 7075 aluminum alloy. As it is commonly used in demanding environments, particularly in the aerospace and automotive industries, understanding how 7075 reacts to various corrosive elements is essential. The purpose of this section is to articulate the mechanisms of corrosion in 7075 metal and compare its resistance to other materials. This understanding can guide engineers and designers in making informed decisions about material selection for specific applications.
Overview of Corrosion Mechanisms
Corrosion in metals, including aluminum alloys, often arises from chemical reactions with environmental agents such as moisture, salts, and acids. For 7075 alloy, two primary forms of corrosion are of particular concern: localized corrosion and pitting corrosion.
- Localized Corrosion: 7075 can experience localized corrosion due to its susceptibility to galvanic effects. This occurs when dissimilar metals come into contact in the presence of an electrolyte, leading to accelerated corrosion at the site of contact.
- Pitting Corrosion: This is a localized form of corrosion that creates small holes or pits in the metal surface. In 7075, factors like alloy composition and surface treatment can significantly impact the extent of pitting corrosion.
It is worth noting that the presence of alloying elements, especially copper in 7075, may enhance its susceptibility to these forms of corrosion if not adequately protected. Thus, surface treatments like anodizing often play a vital role in improving corrosion resistance.
Comparative Corrosion Resistance
When comparing corrosion resistance, 7075 aluminum alloy shows varied performance in relation to other commonly used metals. Key points to consider include:
- 7075 vs. 6061 Aluminum: 6061 aluminum has inherently better corrosion resistance due to its lower copper content. It is preferred in applications where environmental exposure is a concern, while 7075 may be chosen for its superior strength, provided protection is applied.
- 7075 vs. Steel: Steel typically exhibits lower corrosion resistance compared to aluminum alloys. However, when not protected, 7075 can suffer severe corrosion in climates with high humidity or saline exposure. Steel, when galvanized, can perform well under certain conditions, highlighting a key consideration in material selection.
- Surface Treatments and Coatings: Employing proper surface treatments can significantly improve the corrosion resistance of 7075. Options include anodizing, applying protective coatings, or employing chemical conversion coatings, each offering various levels of protection.
Common Applications of Aluminum
7075 aluminum alloy is a significant material choice in various industries due to its unique properties. Understanding how and where this alloy is utilized helps to showcase its importance. The combination of high strength and relatively lightweight characteristics makes it ideal for demanding applications. Furthermore, organizations often choose 7075 for projects where durability and reliability are non-negotiable. This section will delve into three major areas of application: the aerospace sector, the automotive industry, and sporting goods manufacturing. Each subsection will address the specific advantages that 7075 brings to these fields.
Aerospace Industry Utilization
In aerospace, 7075 aluminum alloy plays a critical role. It is often employed in components requiring exceptional strength while minimizing weight. Components such as aircraft wings, fuselage parts, and other structural components heavily rely on this alloy. The mechanical strength of 7075 ensures that these parts can withstand the intense forces experienced during flight.
Some key reasons for its use in aerospace include:
- High Strength-to-Weight Ratio: This is crucial as weight reduction improves fuel efficiency.
- Fatigue Resistance: Aircraft often face cyclic loads. 7075’s ability to endure these stresses is vital.
- Corrosion Resistance: Although it requires protective coatings, its inherent resistance to corrosion helps maintain performance and longevity in harsh environments.
Automotive Industry Applications
The automotive industry has also recognized the benefits of using 7075 aluminum. Components like chassis, suspension parts, and body structures utilize this alloy to improve strength while keeping overall vehicle weight low. 7075 aids in enhancing fuel efficiency and overall performance.
Specific advantages include:
- Enhanced Performance: With 7075, cars achieve better handling and acceleration due to reduced weight.
- Safety: Components that can endure high stress contribute to the vehicle's safety standards, providing better protection in case of accidents.
- Manufacturability: 7075 can be machined and shaped efficiently, allowing for complex designs which are common in modern vehicles.
Sporting Goods Manufacturing
In sporting goods, the use of 7075 aluminum is widespread. Products like bicycles, golf clubs, and other equipment benefit from its strength and lightweight properties. This is particularly important for athletes who require performance-enhancing gear without excessive weight.
Some notable points include:
- Durability: The alloy can withstand impact, making it suitable for high-stress applications.
- Customization: Manufacturers can easily process 7075, producing tailored sporting equipment that meets specific customer needs.
- Performance Improvement: Using 7075 not only improves the lifespan of sporting goods but also enhances user experience in terms of feel and handling.
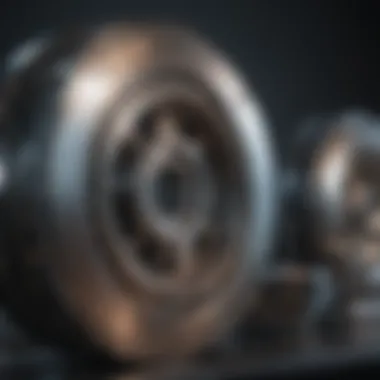
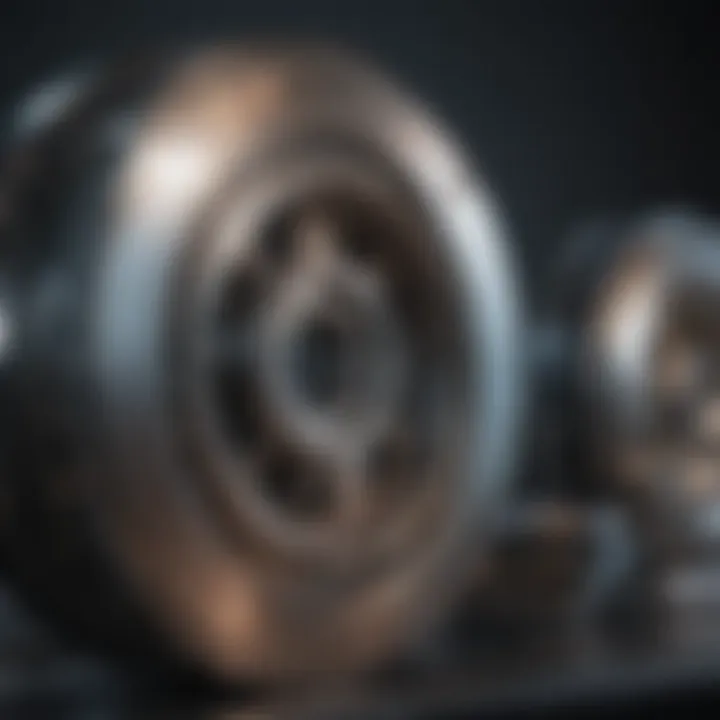
Overall, the versatility of 7075 aluminum brings substantial improvements across multiple industries, demonstrating its essential role in engineering and manufacturing.
Overall, the versatility of 7075 aluminum brings substantial improvements across multiple industries, demonstrating its essential role in engineering and manufacturing.
Advantages of Using Metal
The use of 7075 metal alloy in various industries is largely due to its notable advantages, which set it apart from other materials. Understanding these benefits is critical for engineers, manufacturers, and researchers who seek reliable materials for high-performance applications. The advantages stem from its excellent mechanical properties and adaptability.
High Strength-to-Weight Ratio
One of the defining features of 7075 aluminum alloy is its high strength-to-weight ratio. It offers maximum strength while maintaining a relatively low weight. This characteristic makes it highly desirable in aerospace and automotive applications.
- Efficiency in Design: The reduced weight allows engineers to design lighter structures without compromising on strength. This becomes essential in industries where every ounce counts, such as in aircraft manufacturing.
- Enhanced Performance: Components made from 7075 can withstand higher loads and stress, leading to enhanced performance and reliability. This is particularly important in the aerospace sector, where safety and efficiency are paramount.
- Reduced Fuel Consumption: In automotive applications, using lighter materials like 7075 contributes to better fuel efficiency, which is increasingly important given current environmental concerns.
"The high strength-to-weight ratio of 7075 aluminum not only improves performance but also contributes to significant cost savings in fuel and material costs."
"The high strength-to-weight ratio of 7075 aluminum not only improves performance but also contributes to significant cost savings in fuel and material costs."
Versatility in Usage
The versatility of 7075 metal is another significant advantage. Its properties make it suitable for a vast range of applications across different sectors.
- Wide Range of Applications: Beyond aerospace, 7075 aluminum finds its place in sports equipment, marine structures, and even military applications, highlighting its adaptability.
- Customizability: 7075 is available in various forms, including sheets, plates, and extrusions. This allows manufacturers to tailor the alloy to specific needs, leading to innovative designs and solutions.
- Compatibility with Other Materials: 7075 can be easily combined with other materials, further enhancing its usability. For instance, it is often used in combination with thermoplastics or composites to create hybrid products that utilize the strengths of each material.
In summary, the advantages of using 7075 metal revolve around its exceptional strength, lightweight nature, and versatility, making it a material of choice in demanding engineering applications. Understanding these benefits informs better design and material selection for projects across various industries.
Limitations of Aluminum Alloy
The discussion of 7075 aluminum alloy is incomplete without acknowledging its limitations. Understanding these constraints is crucial for engineers and designers when selecting materials for specific applications. While 7075 showcases impressive strength and other characteristics, its drawbacks affect performance and usability. Identifying these limitations helps erase misconceptions surrounding its applicability and encourages informed decision-making in material selection.
Workability Challenges
One primary limitation of 7075 metal is its workability. This aluminum alloy is harder than many others due to its high strength. The hardness can make it difficult to machine and form into desired shapes, thus necessitating specialized tools and techniques. Implementing practices like heat treatment can enhance its machinability, but it may add complexity to the manufacturing process.
For those in the manufacturing field, it is vital to be aware of the recommended methods for processing 7075. Some impact on workability includes:
- Tool Wear: Increased hardness often leads to faster wear on cutting tools.
- Machining Speed: Slower feed rates may be necessary during machining to achieve desired precision.
- Drilling Difficulties: Creating holes can be particularly challenging; specialized bits are often required.
These factors can translate to increased production times, higher labor costs, and potential wastage during production.
Cost Considerations
The financial implications of using 7075 aluminum cannot be overlooked. Although this alloy offers advanced features, its cost is significantly higher than many other aluminum alloys. Several factors contribute to this elevated pricing:
- Material Sourcing: The alloying elements used in 7075, including zinc, are often more expensive than the elements used in other alloys.
- Manufacturing Complexity: As mentioned earlier, the difficulty in machining can lead to increased operational costs.
- Heat Treatments: Additional processes for enhancing properties can inflate the overall cost due to energy demand and labor.
All these cost factors could make 7075 aluminum less appealing for projects with tight budgets or lower performance requirements. However, for applications demanding high strength and durability, the investment might be justified.
The limitations of 7075 aluminum alloy should not discourage its use; instead, they emphasize the importance of matching material properties to application needs.
The limitations of 7075 aluminum alloy should not discourage its use; instead, they emphasize the importance of matching material properties to application needs.
Future Trends in Aluminum Alloy Research
The study of 7075 aluminum alloy is evolving, with future trends focusing on enhancing its properties and applications. These advancements are crucial for industries that depend on this alloy for its high strength and favorable weight characteristics. This section will explore essential aspects surrounding the innovations in alloy development and sustainability practices in production.
Innovations in Alloy Development
Researchers are committed to optimizing 7075 aluminum alloy to meet modern engineering needs. Innovations are crucial for improving its mechanical properties and expanding its applications. Some key areas of focus include:
- Microstructure refinement: Efforts to enhance the microstructure can lead to a stronger and more ductile alloy. This involves adjusting the heat treatment processes to achieve finer grain structures.
- New alloying elements: Incorporating elements like lithium or scandium can enhance the alloy's strength and reduce weight while maintaining its overall mechanical integrity. These strategic additions are intended to improve performance in high-stress environments.
- Additive manufacturing: Advances in 3D printing technology are enabling the precise use of 7075. This method can create complex shapes and reduce waste, ultimately lowering production costs.
Each of these innovations aims to bolster the properties of the 7075 alloy, making it more resistant to fatigue and improving its usability in various applications.
"The future of 7075 alloy lies in the balance between strength, weight, and versatility in application, driven by continued research and development in metallurgy."
"The future of 7075 alloy lies in the balance between strength, weight, and versatility in application, driven by continued research and development in metallurgy."
Sustainability Practices in Production
Sustainability is becoming a vital consideration in the production of industrial materials, including 7075 aluminum alloy. Addressing environmental impacts is essential for the long-term viability of industries relying on this alloy. Critical sustainability practices include:
- Recycling initiatives: Aluminum is highly recyclable, and using recycled content in the production of 7075 helps lower the overall carbon footprint. Industries are actively seeking to incorporate greater percentages of recycled aluminum into their processes.
- Energy-efficient production methods: Implementing energy-efficient technologies during the manufacturing process minimizes energy consumption. This not only reduces costs but also lessens environmental impacts associated with energy use.
- Waste management practices: Efficient waste management is crucial to reduce materials discarded during production. Techniques such as recovering scrap and reprocessing can significantly decrease waste output.
These sustainability practices are not only essential for reducing environmental impact but also for meeting increasing regulations and consumer demands for responsible sourcing and production practices in the manufacturing sector.