Fiber Reinforced Composites: An In-Depth Exploration
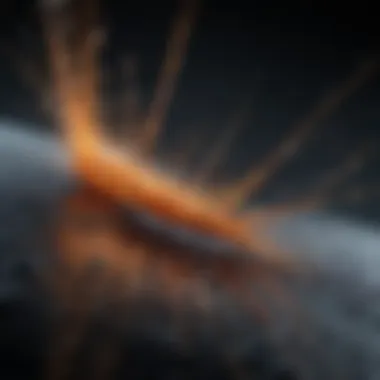
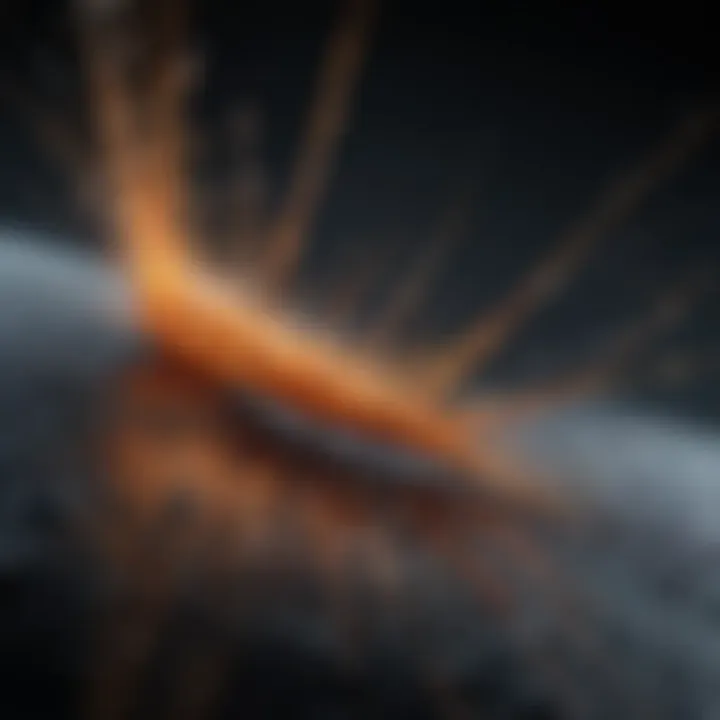
Intro
The landscape of materials science is a constantly shifting terrain, where the pursuit of stronger, lighter, and more durable materials is ever paramount. Among the myriad of advancements, fiber reinforced composites (FRC) emerge as a fascinating development. These compositions, entwining fibers within a matrix, not only enhance physical attributes but also open doors to innovative applications across various sectors. From aerospace to automotive, marine to civil engineering, their versatility is indisputable.
There’s an old saying that good things come in layers. When it comes to fiber reinforced composites, this adage rings particularly true. The fibers contribute strength and stiffness, while the matrix binds them together, providing the necessary shape and structure. It's this unique interplay that allows for remarkable improvements over traditional materials.
Through this article, we journey into the world of FRC. We will dissect its key concepts, explore the ongoing research trends, and ponder the future that lies ahead. Along the way, you’ll see how these composites are not just an academic pursuit but a practical solution to real-world challenges. So, let’s roll up our sleeves and dive deeper into this intricate arena.
Prolusion to Fiber Reinforced Composites
Fiber reinforced composites are increasingly recognized as pivotal elements in modern engineering and material science. Understanding their significance unlocks a plethora of advantages that these materials offer. These composites consist of a matrix embedded with fibers, both of which contribute to unique mechanical properties, making them extremely valuable. As industries strive for materials that are not just strong but also lightweight and versatile, fiber reinforced composites step up to the plate.
Lowering weight while maintaining strength is a primary driver behind the adoption of these composites across diverse sectors. For example, in the aerospace industry, reducing weight directly translates to improved fuel efficiency. In automotive applications, using these materials can enhance performance while also contributing to fuel economy. The versatility of fiber reinforced composites allows them to be tailored to specific needs, providing a significant advantage over traditional materials.
While the performance benefits are clear, it is also essential to comprehend the cost and environmental considerations associated with these materials. Factors such as raw material sourcing, manufacturing techniques, and end-of-life disposal greatly influence the overall profile of a fiber reinforced composite. Hence, a thorough understanding of these elements is critical for any engineering endeavor involving these advanced materials.
The aim of this section is to set the stage for a deeper exploration. Whether you are a student, researcher, or professional in the field, grasping the fundamentals of fiber reinforced composites is crucial. This overview will illuminate not just the mechanics of these composites but also the rich history behind their development and the continuous innovations driving their future.
Defining Fiber Reinforced Composites
Fiber reinforced composites can be defined as a structure combining a reinforcing fiber with a binding matrix. The matrix, often a resin or plastic, supports the fiber and helps distribute loads. The fibers, typically made from materials such as glass, carbon, or aramid, are crucial because they provide the composite with its enhanced strength and rigidity. This interdependence between fiber and matrix results in a material with properties that far surpass those of its individual components.
- Reinforcing Fibers: These fibers provide strength and stiffness to the composite. They come in various types and forms depending on the application.
- Matrix Materials: These materials serve as the backbone, holding the fibers in place while protecting them from damage.
As we dissect this definition further, one could say that the true power of fiber reinforced composites lies in their combination. It is this harmonious balance that yields exceptional performance characteristics.
Historical Development
The journey of fiber reinforced composites dates back several decades. Initially, composite materials were primarily utilized for specialized applications such as aerospace and military. The early adopters found these materials advantageous due to their remarkable strength-to-weight ratio.
In the mid-20th century, the use of fiberglass revolutionized the industry. By incorporating glass fibers into a resin matrix, manufacturers could produce stronger and lighter components than ever before. The ability to mold these composites into complex shapes opened up new possibilities, leading to widespread applications in boats, automotive parts, and even household items.
As technology advanced, carbon fibers entered the scene, providing even greater strength and reduced weight. This shift expanded the horizons for composite utilization. Today, aramid fibers—best known under the brand name Kevlar—have introduced new dimensions in impact resistance and durability, particularly in safety gear and ballistic protection.
The ongoing evolution in manufacturing techniques and materials science continues to shape the future of fiber reinforced composites. Innovations in nanotechnology and bio-based matrices are paving the way for new applications and functionalities that were previously unimagined. The developments over the years illustrate a compelling narrative of adaptability, innovation, and enhanced performance in the realm of materials science.
Composition of Fiber Reinforced Composites
Understanding the composition of fiber reinforced composites is essential. The way these materials are put together significantly affects their performance and suitability for various applications. These composites consist of two main components: the reinforcing fibers and the matrix material. Each of these elements plays a critical role. The fibers are responsible for carrying loads, while the matrix binds the fibers together and protects them from environmental damage.
Choosing the right fibers and matrix materials can enhance mechanical properties, leading to better strength, stiffness, and durability. This section delves into the specifics of both components, providing insight into why certain combinations are favored in the industry.
Types of Fibers
Selecting the appropriate types of fibers is pivotal in determining the overall effectiveness of the composite. The most commonly used fibers include glass fibers, carbon fibers, and aramid fibers. Each type has its unique characteristics that contribute to the performance of the composite.
Glass Fibers
Glass fibers have a high strength-to-weight ratio and excellent corrosion resistance. This makes them very popular in a variety of applications, especially in marine and automotive industries.
- Key Characteristic: Their light weight paired with high tensile strength.
- Benefits: Glass fibers are usually more cost-effective compared to other fibers.
- Unique Feature: They withstand moisture and temperature fluctuations quite well.
- Advantages: They are excellent for applications that require durability without a hefty price tag.
- Disadvantages: However, glass fibers have lower fatigue resistance compared to tougher materials, which can pose issues over time.
Carbon Fibers
Now, on the flip side, carbon fibers are known for their exceptional stiffness and low density, making them a top choice for high-performance applications, like aerospace and high-end sports equipment.
- Key Characteristic: Incredible tensile strength and rigidity.
- Benefits: While they are considerably more expensive, their performance in demanding conditions often justifies the cost.
- Unique Feature: Carbon fibers can easily withstand extreme temperatures.
- Advantages: Lightness and strength are their biggest selling points, translating into improved fuel efficiency in vehicles and planes.
- Disadvantages: They can be brittle and may crack under specific conditions, which requires careful handling.
Aramid Fibers
Aramid fibers, best known through the brand name Kevlar, are frequently utilized in applications where strength and impact resistance are paramount, such as in body armor and aerospace parts.
- Key Characteristic: High resistance to abrasion and impact.
- Benefits: They can absorb significant energy before failure, making them suitable for protective equipment.
- Unique Feature: Aramid fibers maintain their properties even when exposed to high temperatures and chemicals.
- Advantages: They contribute to the strength without adding substantial weight, which is crucial in many uses.
- Disadvantages: These fibers are often more expensive than glass and can be challenging to manufacture into composites.
Matrix Materials
Following the discussion of fibers, the matrix materials deserve equal attention. They serve as a critical element in holding the fiber structure and ensuring the composite's integrity. Two main types of matrix materials are thermoplastics and thermosetting resins.
Thermoplastics
Thermoplastics are versatile materials that become pliable upon heating. They can be reshaped, making them suitable for processes where reprocessing is required.
- Key Characteristic: Ability to be remolded upon heat application.
- Benefits: This feature is beneficial for applications needing repairs or modifications without compromising integrity.
- Unique Feature: They are often easier to recycle than thermosetting resins, enhancing sustainability aspects.
- Advantages: Generally lower manufacturing costs due to adaptable processing methods.
- Disadvantages: They can have lower heat resistance than thermosetting alternatives, limiting their use in high-temperature environments.
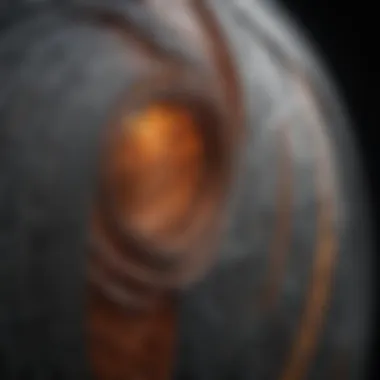
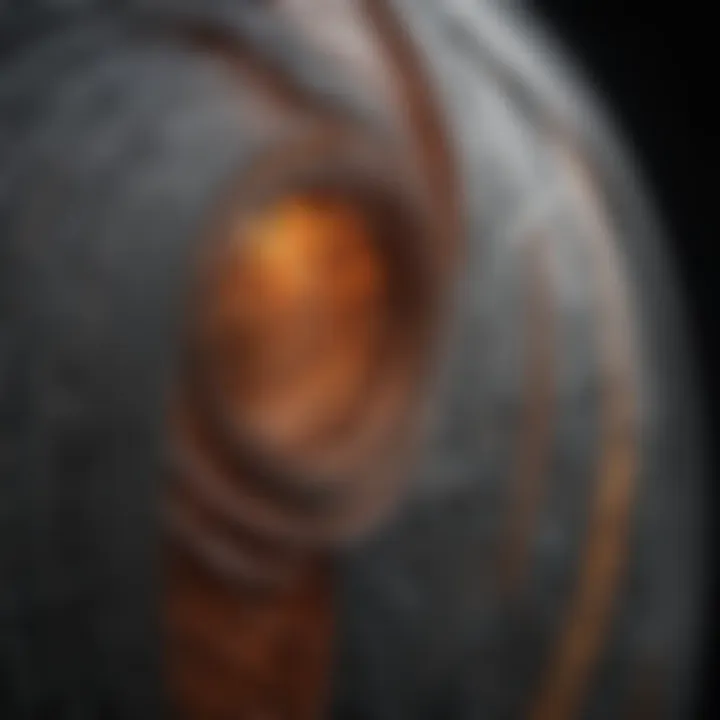
Thermosetting Resins
Contrastingly, thermosetting resins harden permanently once cured and do not soften when heated again. This rigidity offers distinct advantages in specific applications.
- Key Characteristic: They provide superior rigidity and structural integrity.
- Benefits: Ideal for parts that must withstand heavy loads and stresses without bending or deforming.
- Unique Feature: They are generally more resistant to solvents and environmental degradation.
- Advantages: The strength and weight characteristics are favorable for aerospace and automotive applications.
- Disadvantages: The drawback to thermosetting resins is their limited reusability, as they cannot be remolded once set, which adds challenges in terms of repair and recyclability.
Manufacturing Processes
The manufacturing processes of fiber reinforced composites play a crucial role in determining their final properties, usability, and overall performance. These processes not only influence production efficiency but also impact the material's strength, durability, and applicability across various sectors such as aerospace, automotive, and construction. Selecting the right manufacturing technique is essential, as it dictates how well the fibers and matrix integrate, which in turn affects the composite's mechanical characteristics. In this section, we will delve into three prominent manufacturing methods: Hand Lay-Up Techniques, Resin Transfer Molding, and Filament Winding.
Hand Lay-Up Techniques
Hand lay-up is one of the most straightforward and commonly used methods for creating fiber reinforced composites. In this process, layers of fibers are manually laid onto a mold, where a resin is then applied to bind these layers together. This technique offers several advantages:
- Flexibility in Design: Hand lay-up allows for intricate designs and shapes since the artisan has full control over the placement of each fiber layer.
- Cost-Effective: Compared to other methods, the initial investment is low, making it an attractive choice for small to medium-scale production runs.
- Quick Prototyping: Ideal for making prototypes, since adjustments to the design can be easily implemented.
However, it’s worth noting that this method comes with its downsides, such as:
- Quality Variation: The quality can vary significantly based on the skill level of the operator. Variations in fiber distribution might lead to inconsistencies in properties.
- Labor Intensive: The process is time-consuming and requires skilled labor.
This method is effective for applications where performance requirements allow for variability in fiber orientation.
Resin Transfer Molding
Resin Transfer Molding (RTM) is another prominent method that brings several enhancements to the manufacturing process. In RTM, dry fiber preforms are placed in a mold, after which resin is injected under pressure. This process leads to high-quality, consistent composites and presents benefits like:
- Enhanced Mechanical Properties: RTM generally produces composites with better mechanical performance due to the uniform distribution of resin and fibers.
- Reduced Labor Time: Since the process is automated, it reduces the time taken for production significantly.
- Lower Voids: The pressure helps fill the mold more completely, leaving fewer voids that can compromise structural integrity.
Despite its advantages, there are some considerations:
- Higher Initial Investment: The equipment and setup involved can be costly, which may deter smaller operations.
- Complexity: The method requires careful design and control of both the mold and resin flow, which might complicate production.
Ultimately, RTM is perfect for high-performance applications requiring precision and reliability.
Filament Winding
Filament winding is primarily used in manufacturing cylindrical or spherical structures and is particularly favored in making pressure vessels and pipes. In this method, continuous fiber filaments are drawn through a resin bath and wound onto a rotating mandrel in specific patterns. This technique delivers numerous advantages:
- Uniform Strength Distribution: The winding allows for precise control over the fiber orientation, which maximizes strength in the areas where it’s needed most.
- High Production Rate: Once set up, filament winding can produce parts relatively quickly, enhancing overall productivity.
- Mold-Free Production: Parts can be created without a conventional mold, allowing for more complex geometries.
Yet, it’s crucial to consider some challenges:
- Specialized Equipment: The machinery involves more complexity and higher costs than simpler methods like hand lay-up.
- Design Limitations: While effective for specific shapes, it’s not as versatile when it comes to producing intricate or non-cylindrical structures.
The precision offered by filament winding makes it indispensable in specialized industries.
The choice of manufacturing process significantly influences the quality, performance, and cost-effectiveness of fiber reinforced composites.
The choice of manufacturing process significantly influences the quality, performance, and cost-effectiveness of fiber reinforced composites.
Understanding these distinct processes provides clarity on how fiber reinforced composites are made and helps stakeholders select the best method suited for their specific applications. As technology progresses, advancements in manufacturing processes continue to enhance the capabilities and potential of these robust materials.
Mechanical Properties of Fiber Reinforced Composites
When delving into the world of fiber reinforced composites, the topic of mechanical properties takes center stage. These properties are what set fiber reinforced composites apart from traditional materials, making them a go-to choice across various industries. Understanding strength, stiffness, damping, and fatigue resistance isn’t just academic—it plays a pivotal role in design and application decisions. Whether it's aerospace, automotive, or construction industries, the mechanical strengths of these materials define how they perform under stress and over time.
Strength and Stiffness
Strength is often the first aspect folks consider, and rightly so. In simple terms, strength refers to the ability of a material to withstand an applied load without failure. Fiber reinforced composites score high marks here, owing largely to the fibers embedded within the matrix. These fibers—whether they be aramid, carbon, or glass—carry a significant portion of the load.
So, why does stiffness matter? Stiffness measures how much a material deflects under stress. High stiffness not only enhances structural integrity but also contributes to overall durability. For instance, carbon fiber composites are prized for their remarkable stiffness-to-weight ratio, making them a preferred choice in high-performance applications like racing cars and aircraft.
Moreover, the combination of strength and stiffness creates a synergy that elevates structural performance. Think of it this way: high strength allows a composite to carry heavy loads, while high stiffness keeps deformations minimal. This dual capability is critical in applications where precision is paramount.
"The durability of a material is only as good as its ability to sustain continuous forces without excessive deformation."
"The durability of a material is only as good as its ability to sustain continuous forces without excessive deformation."
Damping and Fatigue Resistance
Now, let’s discuss damping—an often overlooked mechanical property, but one that can’t be underestimated. Damping refers to a material’s ability to dissipate energy, which is important for reducing vibrations in structures. Fiber reinforced composites naturally excel in this area, thanks to the viscoelastic nature of the matrix materials. This energy absorption reduces the wear and tear on the material, extending its lifespan and reliability in service.
Fatigue resistance is closely linked to damping, yet it brings another layer of complexity to the table. This resistance describes how well a material can withstand repeated loading and unloading cycles. In simpler terms, it’s crucial for applications that involve constant stress, like in bridges or airplane wings.
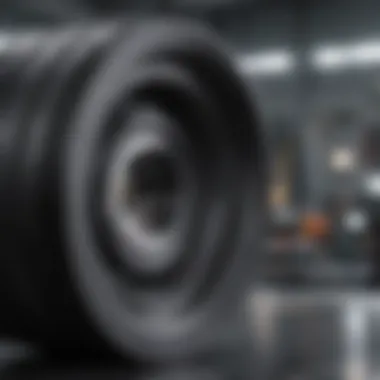
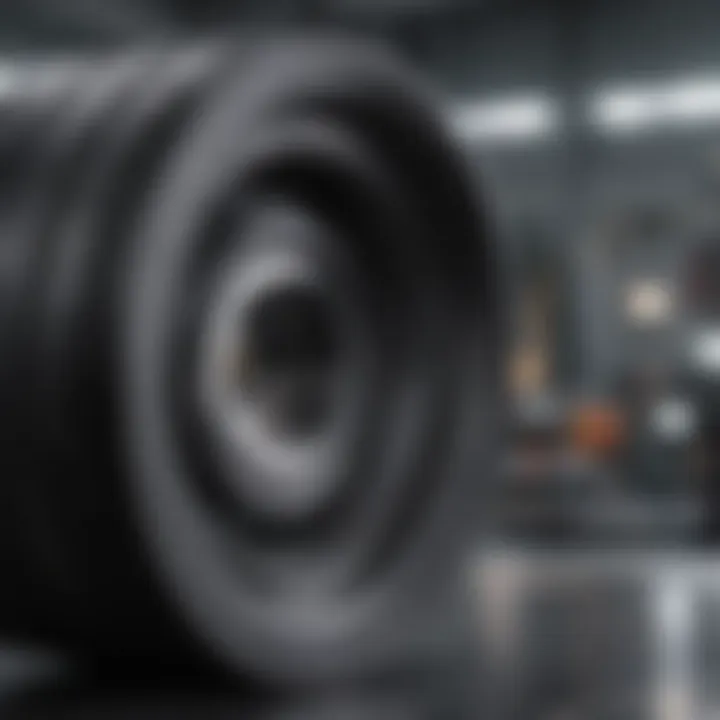
While traditional materials may succumb to fatigue cracks, fiber reinforced composites often demonstrate remarkable endurance. For example, many manufacturers perform rigorous fatigue testing on composites, revealing their ability to maintain structural integrity even after thousands of load cycles. This endurance directly correlates to safety, making these materials vital in critical infrastructure applications.
Applications of Fiber Reinforced Composites
The significance of fiber reinforced composites in today’s industries cannot be overstated. These materials have made waves across various sectors, offering solutions that traditional materials simply cannot. Their ability to combine high strength-to-weight ratios, durability, and resistance to environmental degradation makes them invaluable in applications that require performance without compromise. In this section, we dive into specific industries that have embraced these composites, detailing their use and the benefits they offer.
Aerospace Industry
In the aerospace sector, weight reduction is of utmost importance. Aircraft manufacturers are continually seeking ways to improve fuel efficiency and performance. Fiber reinforced composites shine in this area; they significantly lessen the overall weight of aircraft while maintaining structural integrity. Components such as wings, fuselage sections, and even interior parts see extensive use of composites. Notably, the Boeing 787 Dreamliner utilizes around 50% composites in its structure, showcasing the industry’s shift towards these materials.
Some advantages seen in this sector include:
- Enhanced Performance: Reduced weight means improved aerodynamics and fuel savings.
- Corrosion Resistance: Composites can withstand the harsh conditions of high-altitude flight without compromising strength.
- Design Flexibility: Manufacturers enjoy greater freedom in designing complex shapes that are more difficult to achieve with metals.
"The shift to fiber reinforced composites is not just a trend; it's a necessity driven by the demands of modern aviation."
"The shift to fiber reinforced composites is not just a trend; it's a necessity driven by the demands of modern aviation."
Automotive Sector
The automotive industry too is reaping the benefits of fiber reinforced composites. With the drive towards sustainability and fuel efficiency, car manufacturers are constantly on the lookout for materials that contribute to lighter, yet safe vehicles. By incorporating composites into structural components and body panels, automakers can not only cut down on vehicle weight but also enhance performance.
Some key points include:
- Improved Fuel Efficiency: Lighter vehicles consume less fuel, aligning with global initiatives for reduced emissions.
- Crashworthiness: Composites absorb energy during impacts, providing better protection for passengers.
- Aesthetic Qualities: Composites allow for unique designs and can be molded into various shapes, making vehicles more visually appealing.
Construction Applications
The construction industry is catching up with the benefits of fiber reinforced composites, especially in structures that demand resilience and longevity. These materials are utilized both in new constructions and for reinforcing existing structures. For example, applications range from bridge reinforcement to seismic retrofitting and even in creating building facades.
Key considerations include:
- Durability: Composites are more resistant to weathering, chemicals, and other environmental factors compared to traditional materials.
- Lightweight Solutions: Their lower weight can simplify transport and installation while improving the overall load-bearing capacity of structures.
- Cost Efficiency: Although initial costs might be higher, over time, their durability and maintenance-free nature contribute to long-term savings.
In summary, the applications of fiber reinforced composites extend into diverse industries, revolutionizing how we think about materials in engineering, design, and construction. The push for innovation continues to unveil new potentials for composites, confirming their role as a critical component in our technological tomorrow.
Advancements and Innovations
The field of fiber reinforced composites is constantly evolving, driven by innovations that enhance material performance and broaden their applications. As industries strive for lighter, stronger, and more efficient materials, advancements in this realm not only satisfy those demands but also pave the way for new possibilities in various sectors. The significance of such advancements can’t be overstated; they hold the key to coupling performance with sustainability and cost-effectiveness. Understanding these innovations can equip professionals and researchers with insights into the future trajectories of composite materials, ensuring they remain at the forefront of modern engineering.
Nanocomposites
Nanocomposites stand at the cutting-edge of material science, representing a fusion between nanotechnology and fiber reinforced composites. Essentially, these materials incorporate nanoscale particles into a polymer matrix, which enhances the overall properties without significantly increasing weight. This innovative approach results in important benefits:
- Strength and Durability: The inclusion of nanoparticles can significantly improve mechanical strength and thermal stability. When a polymer is combined with reinforced fibers at the nanoscale, the result is a composite that can withstand greater stresses and higher temperatures.
- Enhanced Barrier Properties: Nanocomposites are often recognized for their superior barrier characteristics, making them suitable for applications where resistance to moisture or gas permeation is critical. This is particularly essential in fields like packaging and construction, where durability matters.
- Lightweight Design: Using nanoparticles allows manufacturers to achieve greater performance metrics without bloating the weight of the final product. This quality is crucial, especially in aerospace and automotive industries, where minimizing weight translates to improved fuel efficiency and reduced emissions.
"The integration of nanotechnology in composites is not just a step forward; it’s a leap into a future where materials can perform beyond current limits."
"The integration of nanotechnology in composites is not just a step forward; it’s a leap into a future where materials can perform beyond current limits."
However, there are considerations when working with nanocomposites. The manufacturing processes can be more complex and might require specialized equipment. Additionally, regulatory concerns surrounding the safety and environmental impact of nanoparticles necessitate careful attention.
Reinforcement Techniques
Reinforcement techniques play a crucial role in maximizing the capabilities of fiber reinforced composites. Depending on the desired properties and applications, various methods can be employed to improve the bond between fibers and the matrix material, leading to optimized performance. Here are some noteworthy techniques:
- Hybrid Reinforcement: This method employs multiple types of fibers working in concert within the same matrix. For instance, combining carbon and glass fibers can yield composite materials that harness the strengths of both, adding functionality for specific uses across industries.
- Surface Modification: Treatments applied to the fiber surface, such as chemical bonding or physical roughening, can improve adhesion to the matrix. These modifications are paramount for achieving notable improvements in material strength and reducing delamination risks.
- Advanced Matrix Systems: Incorporating novel resin systems—such as bio-based resins or epoxy blends—can elevate the performance of the reinforced composite. These advanced matrices can provide better compatibility and distribution of stress, leading to increased durability.
- 3D Printing Techniques: The rise of additive manufacturing has opened new doors. 3D printing enables precise control over fiber orientation and placement, allowing for customized reinforcement that adapt to the demands of different load conditions. The agility of this method, paired with its potential for reduced waste, positions it as a significant advancement worth exploring further.
These advancement and innovations not only address existing limitations in fiber reinforced composites but also set the stage for future breakthroughs. Understanding and applying these advancements will be critical as industries aim to meet modern demands for efficiency, performance, and sustainability in their material choices.
Environmental Considerations
The increasing spotlight on sustainability in recent years compels industries to evaluate their environmental impact. This drive for responsible practices holds especially true for fiber reinforced composites, materials that promise high performance but raise questions about their lifecycle, from production to end-of-life management. In this section, we’ll delve into the relevance of this topic, focusing on two key areas: recyclability and biocomposite developments.
Recyclability of Composites
Recyclability stands as a critical aspect in the discussion surrounding fiber reinforced composites. Given their widespread use across various industries, the fate of these materials post-use deserves significant consideration. Traditional composites pose recycling challenges due to their heterogeneous nature. Often combining materials that do not break down easily, they can end up in landfills, contributing to environmental degradation. But things are changing!
- Several innovative recycling methods are gaining traction, including mechanical recycling, which involves grinding the composite into smaller pieces, allowing it to be repurposed in new applications. This method can significantly reduce waste, although it might alter the physical properties of the material.
- Another nascent approach is chemical recycling, which seeks to decompose the polymers and fibers into their original monomers. This technique holds great promise, as it can potentially allow for the recovery of valuable raw materials, turning waste into a resource rather than just rubbish.
While these advancements are promising, it’s vital to note that the scalability of these processes is still under investigation. Regulatory frameworks and technology need to align seamlessly to pave the way for effective recycling practices across the globe.
"Waste is a resource in the wrong place."
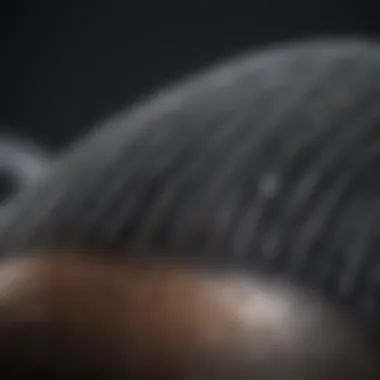
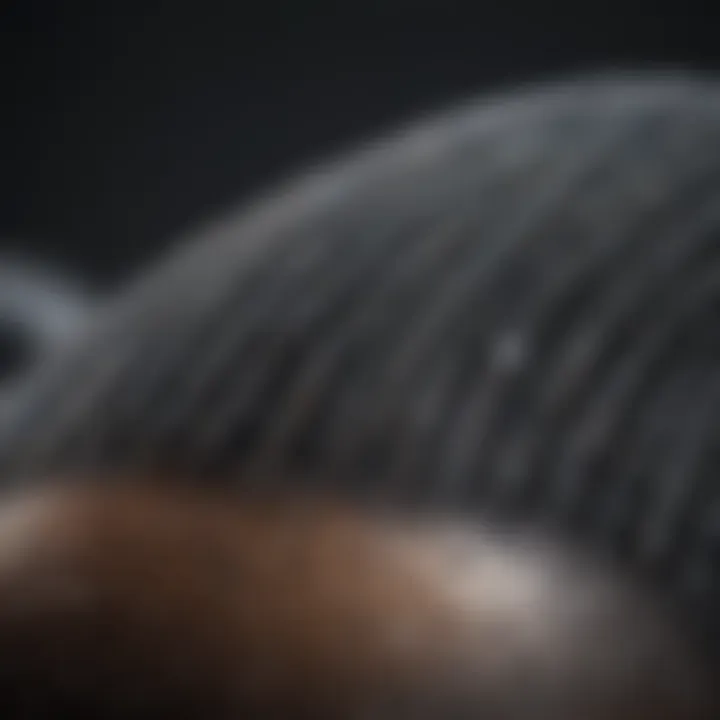
"Waste is a resource in the wrong place."
Biocomposite Developments
The pursuit of more sustainable materials has sparked interest in biocomposites, which integrate natural fibers and bio-based matrix materials. These composites are lauded for their lower environmental impact as they can be produced from renewable resources, making them a viable alternative to traditional fiber reinforced composites.
Examples of biocomposites include:
- Hemp-infused composites: These composites utilize hemp fibers as reinforcement. Hemp grows rapidly and requires minimal pesticide intervention, making it a sustainable choice.
- Flax and jute fibers: Flax offers tensile strength, while jute is cost-effective, both presenting compelling options for eco-friendly applications.
On the matrix side, there are biopolymers derived from starch or polylactic acid (PLA), which can further enhance the sustainability quotient.
Yet, just as with recyclability, drawbacks exist. Biocomposites may not yet match the mechanical performance of conventional materials for every application. Furthermore, biocomposite production and processing technologies are still developing, which means there’s a bit of a learning curve ahead for industries looking to transmute into more sustainable practices.
The intersection of fiber reinforced composites and environmental responsibility underscores a growing acknowledgement that innovation and sustainability can, and should, go hand-in-hand. As we move forward, embracing these considerations not just for compliance, but for genuine advancement, sets a precedent for future materials in engineering.
Challenges in Fiber Reinforced Composites
Fiber reinforced composites offer excellent mechanical properties compared to traditional materials. However, these benefits do not come without their share of challenges. Understanding the challenges is vital for engineers, manufacturers, and researchers alike, especially as the industry continues to evolve. This section will highlight significant hurdles faced in the realm of fiber reinforced composites, notably cost implications and manufacturing complexity.
Cost Implications
The financial aspect of fiber reinforced composites cannot be overlooked. While these materials boast superior performance characteristics—such as high strength-to-weight ratios and corrosion resistance—these advantages often come with hefty price tags. First off, the raw materials themselves can be expensive. For instance, carbon fibers, known for their impressive strength, often cost significantly more than traditional materials like steel or aluminum.
When assessing costs, manufacturers also need to consider the production processes. Specialized equipment and techniques, such as resin transfer molding or filament winding, require a more considerable upfront investment. Moreover, training the workforce to handle sophisticated manufacturing processes adds another layer of expense. The delicate balancing act of cost versus performance makes it critical for businesses to evaluate whether the benefits justify the investment.
In today's competitive landscape, where companies are relentless in cutting costs, managing the price of fiber reinforced composites is an ongoing issue. Manufacturers must grapple with the reality that, despite lower material costs in other sectors, the specialized nature of composites doesn't always lend itself to competitive pricing. Some companies seek ways to offset costs by:
- Incorporating alternative fiber materials: Utilizing natural fibers can sometimes reduce expenses.
- Streamlining production processes: Optimizing manufacturing steps can yield savings without compromising quality.
- Investing in research and development: Finding innovative methods to reduce costs long-term can help stabilize finances.
Manufacturing Complexity
Manufacturing fiber reinforced composites involves a multitude of intricate processes, and this complexity presents another challenge. Each step—from selecting the right fibers to curing the matrix—demands precision and expertise. The custom nature of composites means that each application can require a different approach, making standardization a difficulty.
Issues can arise at any stage of the manufacturing process. For example, handling and mixing resins correctly is crucial. If done poorly, the final product's performance can suffer significantly. The curing process—how the composite sets and hardens—is another sensitive point. Potential defects like voids or misalignment can result if not monitored closely during curing, leading to costly rework or scrapped parts.
Further, the need for quality assurance cannot be understated. Regular testing and inspections are paramount in ensuring reliability and safety, especially in critical industries like aerospace and automotive. This increased scrutiny translates to further costs and complexity for manufacturers—each step in the process must adhere to strict standards, increasing the burden on production timelines.
"Although fiber reinforced composites hold great promise, a keen understanding of the unique challenges they present is essential for successful integration into modern applications."
"Although fiber reinforced composites hold great promise, a keen understanding of the unique challenges they present is essential for successful integration into modern applications."
In summary, while fiber reinforced composites stand at the forefront of advanced materials, the road to widespread adoption is paved with challenges. Addressing cost structures and manufacturing complexities will be pivotal in advancing the technology and making it more accessible across various sectors. Engaging in strategic planning and innovation will be key for those looking to harness the benefits of these remarkable materials.
Future Trends
The arena of fiber reinforced composites is undergoing dynamic shifts, which makes it vital to grasp the future prospects of these materials. As industries evolve and adapt to changing demands, advancements in fiberglass and carbon fiber technology are becoming increasingly consequential. This section explores how market growth and technological enhancements are shaping the future of fiber reinforced composites.
Market Growth Prospects
The market for fiber reinforced composites is not just expanding; it is skyrocketing, thanks to several driving forces. One significant factor is the increasing application in sectors like aerospace and automotive, where the need for lightweight yet robust materials is paramount. As companies strive for fuel efficiency and performance, the demand for these composites is predicted to rise significantly.
Potential growth avenues include:
- Aerospace: The aviation sector is projected to invest heavily in composite materials to enhance fuel economy and passenger safety.
- Automotive: As electric vehicles gain traction, there’s a pronounced shift towards materials that offer weight savings while maintaining structural integrity.
- Construction: Emerging trends suggest an escalating incorporation of these materials in building frameworks for improved durability and reduced maintenance costs.
Moreover, studies indicate that by the year 2030, the global composite materials market could be worth billions, with fiber reinforced composites leading the charge. This potential prompts industries to rethink their strategies and invest in research for newer composite formulations that cater to both environmental and structural demands.
Technological Integrations
Alongside market growth, technological breakthroughs in the realm of fiber reinforced composites deserve attention. Innovations are reshaping manufacturing methods and material properties, pivotal in enhancing the composite's usability.
A few notable integrations include:
- 3D Printing: As this technology gains foothold, the ability to produce complex composite structures is becoming a reality. This method not only speeds up production but also allows customization and reduced material wastage.
- Smart Materials: The emergence of composites embedded with sensors heralds a new age where materials can monitor health conditions in real-time, providing immediate feedback during usage, crucial in aerospace and automotive applications.
- Eco-Friendly Alternatives: Advances in biocomposites, which utilize natural fibers and bio-based resins, are catching wind. This shift not only meets performance requirements but also addresses growing environmental concerns, aligning with the sustainability goals many companies are now striving to achieve.
"Innovation and growth in the fiber reinforced composites market not only influence manufacturing processes but also set the stage for the material’s pervasive use in various industries."
"Innovation and growth in the fiber reinforced composites market not only influence manufacturing processes but also set the stage for the material’s pervasive use in various industries."
Together, these market growth prospects and technological integrations create a vivid picture of a future rich with possibilities for fiber reinforced composites, illustrating their essential role in the evolution of material science.
The End
Fiber reinforced composites have carved a niche in modern engineering and technology, reflecting a careful fusion between material science and the demands of various industries. Understanding the significance of these composites is essential, as they present numerous advantages over traditional materials. Their unique properties lead to lightweight structures with high tensile strength, making them ideal for applications ranging from aerospace to construction.
Summary of Key Insights
The exploration of fiber reinforced composites reveals several key points:
- Versatility: These materials are tailored for diverse applications, driven by the specific requirements of industries. For instance, in aerospace, carbon fiber composites offer both lightweight and high strength, which is essential for flight efficiency.
- Cost-Benefit Balance: While the initial costs may be higher due to complex manufacturing processes, the lifecycle cost often proves favorable. The strength and durability of these composites lead to reduced maintenance costs and longer service life.
- Environmental Considerations: As sustainability becomes imperative, advancements in recycling techniques and biocomposites show promise. This evolution aligns with modern demands for greener materials.
- Technological Integration: The future shows emphasis on integrating smart technologies with fiber reinforced composites, enhancing monitoring capabilities in real-time applications.
- Challenges: Despite their advantages, issues related to high production costs and manufacturing intricacies present hurdles that require ongoing research and innovation.