Exploring the Smelting Industry: Challenges and Evolution
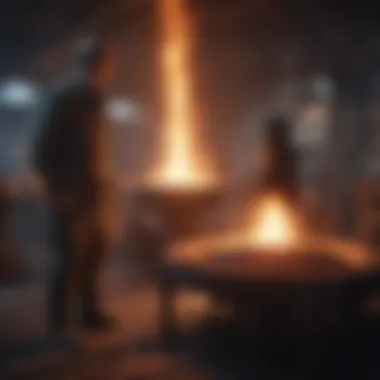
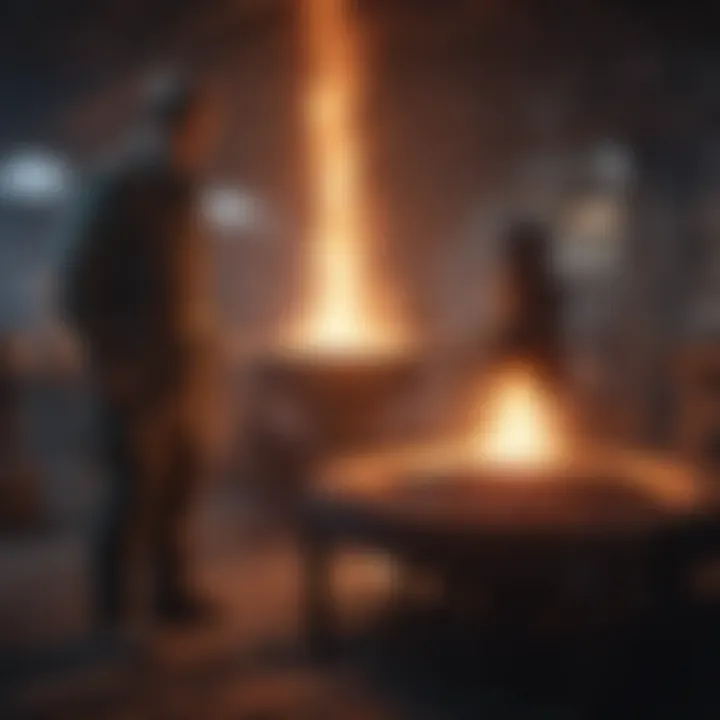
Intro
The smelting industry, while often overshadowed by other industrial sectors, plays a critical role in the world as we know it. It’s a process that converts metal ores into usable forms by applying heat, effectively “cooking” the raw materials until they yield metals essential for various applications across modern life. But this industry is not just about high temperatures and melting heaps of minerals; it encompasses a rich tapestry of history, technology, economics, and environmental concerns that intertwine in complex ways.
This exploration ventures into understanding how smelting has evolved from rudimentary techniques to advanced technological applications. We will dive into the scientific principles that underlie the smelting processes, analyze current research trends, and discuss the implications of these advancements on our economy and environment. It is crucial to grasp that as industries flourish, they carry the burden of their ecological footprints, making it imperative to evaluate the balance between innovation and sustainability.
In a world rapidly shifting towards greener technologies, the smelting industry faces numerous challenges and opportunities. Our comprehensive investigation aims to shed light on both the intricate workings of smelting and its vital role in shaping the metal production landscape.
Overview of the Smelting Industry
The smelting industry plays a vital role in converting raw ores into usable metals. It serves as the backbone of metal production across various sectors, including construction, automotive, and electronics. Understanding its intricate processes, historical context, and economic significance is essential for anyone looking to grasp the full scope of metal manufacturing.
This section is dedicated to unraveling the complexities of the smelting industry. By examining key definitions, historical antecedents, and its societal impacts, we aim to provide a holistic understanding of this vital sector.
Definition and Purpose
Smelting refers to the process of extracting a metal from its ore by heating and melting. The primary goal is to separate the pure metal from impurities and other constituent materials. This is often achieved through various methods, including pyrometallurgy, hydrometallurgy, and electrometallurgy. Each method has its own unique practices and applications depending on the type of metal involved.
The purpose of smelting is not just to produce raw metal; it also lays the groundwork for further refinement and processing. Metals resulting from smelting are then used in a multitude of products ranging from everyday items to high-tech applications.
Historical Context
Origin of Smelting
The origin of smelting can be traced back to ancient civilizations, where it emerged as a critical technological innovation. The earliest evidence suggests that metals, particularly copper, were smelted around 4500 BC in places like Anatolia (modern-day Turkey). This marked a groundbreaking leap forward—societies transitioned from the Stone Age to the Bronze Age, enriching their lives with tools, weapons, and decorative items made from metal.
A key characteristic of this period is the relationship between smelting and the birth of trade. The ability to produce metal tools spurred not only local economies but also trade routes that allowed for the exchange of both raw materials and finished products across distances. This laid the very foundations of commerce as we know it.
Evolution Through Ages
As time marched on, the processes of smelting evolved alongside societal needs and technological advancements. By the Middle Ages, techniques had improved significantly, allowing for more efficient extraction methods and higher purity levels of produced metals. The advent of coke smelting, specifically in the 18th century, revolutionized the production of iron, making it more accessible and economical.
One unique feature of these developments was the shift from charcoal, which was limited by wood supply, to coke derived from coal; this not only boosted production but also minimized deforestation. The benefits of these advancements continue to echo in present-day practices, where energy efficiency is a significant concern.
Impact on Societal Development
The influence of the smelting industry can't be overstated when we consider its broader societal implications. The ability to produce metals in large quantities facilitated the advent of industrialization in the 19th century. Factories sprung up across Europe and America, catalyzing urban growth and changing lifestyles fundamentally.
However, with this progress also came challenges. The increased demand for raw materials led to exploitation of resources and environmental degradation. Understanding these factors is crucial for comprehending contemporary issues regarding sustainability and resource management in today's smelting practices.
Key Smelting Processes
Understanding the key smelting processes is essential for anyone interested in the industry. These processes form the backbone of metal extraction and refinement and play a crucial role in determining the efficiency, cost-effectiveness, and environmental impact of metal production. This section examines the various types of smelting and the step-by-step procedures involved, illuminating how these methods shape the modern metallurgical landscape.
Types of Smelting
Pyrometallurgical Smelting
Pyrometallurgical smelting stands out for its reliance on high-temperature processes to melt ores. By applying intense heat, it converts metal ores into liquid form, allowing for easier extraction of valuable metals like copper, nickel, and lead. One key characteristic of pyrometallurgy is its straightforward methodology, which usually involves the use of furnaces, like blast furnaces or electric arc furnaces.
The significant advantage here is its efficiency in processing large volumes of ores. However, there are downsides, notably the heavy energy consumption and the associated greenhouse gas emissions, which raise environmental concerns.
Hydrometallurgical Smelting
This technique diverges from the traditional heat-based methods and utilizes aqueous solutions to extract metals from their ores. Hydrometallurgical smelting is particularly effective for metals like gold and silver, which can be dissolved in cyanide solutions. Its defining feature is the relatively lower energy requirement compared to pyrometallurgy.
It's an appealing option for those focusing on sustainable practices since it results in less carbon footprint when properly managed. However, the use of toxic chemicals in this process can introduce significant environmental risks if not handled carefully.
Electrometallurgical Smelting
Electrometallurgy uses electrical energy to drive the extraction and refinement of metals, making it a cutting-edge approach within the smelting industry. This method is particularly favored for metals like aluminum and magnesium. A key characteristic of this process is its potential for high purity levels in the end product, a feature highly sought after in various industrial applications.
While this technological method promises lower emissions compared to traditional methods, it can be costly to implement, which could pose a barrier for smaller operations. Additionally, it requires advanced equipment, making it less accessible to all players in the smelting arena.
Step-by-Step Process
Ore Preparation
Ore preparation serves as a foundational step in the smelting process. This phase is essential as it involves the crushing and grinding of ore materials to liberate the desired metals. A significant characteristic of this step is the focus on enhancing ore particle size and uniformity, which allows for better extraction efficiency.
Effective ore preparation can substantially impact the overall recovery rates in smelting, making it a pivotal part of the journey from ore to finished metal. Neglecting this step may lead to increased costs and lower yields.
Reduction Techniques
Reduction techniques take center stage after ore preparation. This segment is crucial because it's where the actual transformation of ores into pure metals occurs. Various methods can be employed during reduction, such as carbon reduction or direct reduction using hydrogen. A key aspect is the choice of method dictated by both the type of ore and the desired quality of the metal.
The right reduction technique can significantly influence the quality and efficiency of the smelting process. However, some methods may be more suited to certain ores, which again underlines the necessity for careful planning and research.
Refining and Casting
The final stage of the smelting journey involves refining and casting, where the metal is purified and formed into final products. This step is characterized by processes that ensure the elimination of impurities, enhancing the properties and quality of the final metal.
An interesting feature of refining is the use of both physical and chemical methods to ensure superior alloy characteristics. The casting process further shapes the molten metal into molds, creating various forms required by manufacturers.
Having accurate control over these final processes is crucial for industries relying on high-standard finished goods. However, the variability in alloy properties can present challenges, requiring ongoing adjustments and refinements to maintain quality, especially when dealing with different material compositions.
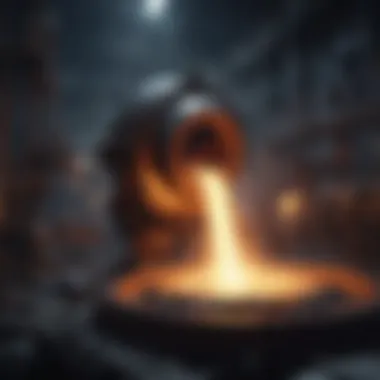
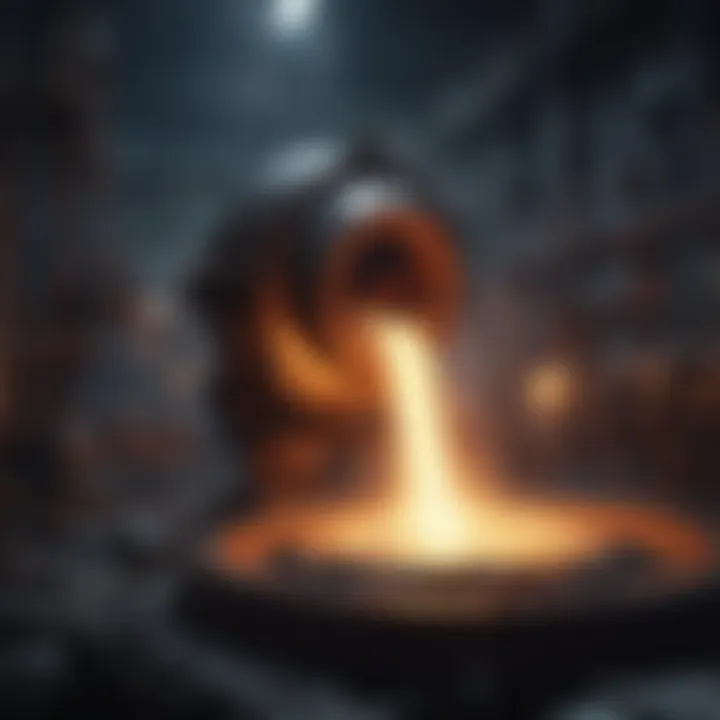
Materials Involved in Smelting
The materials utilized in the smelting process are fundamental to the industry’s operations and outputs. This section aims to unravel how different ores and the adjunctive materials, i.e., flux and reductants, play crucial roles in determining the efficiency and quality of metal production. By diving into specific ores processed and the role of various materials, readers will gain insight into the practical considerations and the inherent benefits associated with these elements.
Common Ores Processed
Iron Ore
Iron ore stands as one of the most pivotal materials in the smelting industry, primarily due to its abundance and inherent properties. This raw material serves as the backbone for steel production, which is essential in various sectors from construction to automotive manufacturing. One key characteristic of iron ore is its high iron content, making it a sought-after choice for smelting operations aimed at producing high-purity metal. However, a unique feature of iron ore is the need for effective reduction strategies during processing; otherwise, impurities can affect the final product quality.
While this ore shines for its effectiveness in producing manageable costs and a steady supply stream, it also comes with drawbacks such as environmental concerns stemming from its extraction and processing. Thus, understanding these dynamics is vital for addressing efficiency and compliance challenges within the industry.
Copper Ore
Shifting the focus to copper ore, its role similarly cannot be understated in the smelting landscape. With its excellent conductivity, copper is vital for electrical applications, plumbing, and various alloys. A key characteristic here is its relatively low melting point, which allows for easier and more efficient processing compared to heavier metals.
One notable advantage of copper ore is its significant recyclability. The smelting of copper entails less energy compared to other materials, which not only improves sustainability but also reduces operational costs. However, the unique challenge lies in managing the byproducts generated, requiring smelting facilities to adopt advanced waste management techniques.
Lead Ore
Lead ore, often less discussed but equally significant, serves specific industries such as batteries and radiation shielding. Lead’s dense and malleable properties make it highly useful. A highlighted feature of lead ore in the smelting process is the importance of controlling toxicity—smelting operations need to be meticulous in factoring environmental regulations into their operations. This can create a more complex production timeline, which may hinder efficiency if not handled properly.
Advantages include its capability to produce byproducts that can be further utilized, such as lead sulfide, enhancing the resource recovery processes. Nonetheless, balancing lead production with safety programs is critical, reflecting the attention to environmental impacts in modern smelting.
Role of Flux and Reductants
Definition of Flux
Flux serves as a critical accessory in the smelting process, facilitating the removal of unwanted impurities from the ore. Specifically, it combines with other materials during heating to form a liquid slag, separating itself from the valuable metal. The main characteristic that makes flux indispensable is its ability to lower the melting point of the raw materials, thus improving energy efficiency during smelting.
This unique feature of flux contributes significantly to process outcomes, enhancing overall efficiency and product quality. However, it's essential to consider that the choice of flux can vary based on the desired end product and the type of ore being processed, thus requiring careful consideration within any smelting strategy.
Common Reductants Used
The use of reductants in smelting is crucial as it plays a central role in the reduction of metallic oxides into pure metals. Generally, carbon is the predominant reductant, but alternatives like hydrogen or aluminum are also utilized depending on the setting. The key aspect of using reductants lies in their ability to compete for oxygen present in the ores, unlocking the pure metal during smelting.
The unique feature of reductants involves their substantial influence on the temperature profiles and energy requirements of the process. Each reductant carries its own operational considerations, meaning that while carbon is cost-effective, the choice may ultimately hinge on environmental compliance and efficiency targets.
Impact on Process Efficiency
Process efficiency in smelting directly correlates with the types of materials used, particularly the selection of ores, flux, and reductants. When appropriately chosen, these elements can enhance reactions, speeding up the metal recovery rates and minimizing energy use. A crucial characteristic of efficient smelting is its ability to recapture waste materials; therefore, understanding the full spectrum of the inputs becomes paramount for operational success.
One significant advantage is the potential for increased throughput, translating to higher profitability. However, a key drawback is that improper material selection can lead to inefficiencies, wastage, and environmental concerns, necessitating continuous assessment within smelting operations.
Economic Significance of Smelting
The smelting industry isn’t just about transforming raw ores into metals; it plays a crucial role in the global economy. This significance goes beyond mere numbers. It influences job creation, local and international markets, and even shapes the very fabric of nations. By understanding these economic aspects, one can appreciate smelting's impact on metal production and its broader implications.
Global Market Dynamics
Market Size and Growth Trends
The smelting market is massive and continues to grow, supported by increasing demand for metals in various sectors, from construction to technology. The growth can be seen in the rising demand for copper and steel as economies industrialize. According to recent reports, the global smelting market size reached billions in revenue in 2022, demonstrating a compound annual growth rate of around 4% over recent years. This trend indicates a robust market, reflecting advances in smelting technology and a global shift towards more metal-intensive products.
What sets this growth apart is its resilience in the face of economic fluctuations. For instance, despite the COVID-19 pandemic's shockwaves, the demand for essential metals didn’t wane significantly. Companies that adapted quickly fared better, proving that flexibility in operations can be beneficial in uncertain times.
Key Players in the Industry
Several key players dominate the smelting scene, including Rio Tinto, BHP Billiton, and Glencore. These companies have established a strong foothold in the market, thanks to their extensive operations and diverse portfolios. Their presence underscores the competitive landscape of the smelting sector and highlights the importance of innovation in staying ahead.
Each of these firms not only contributes to job creation but also pushes for advancements that enhance efficiency and sustainability. However, it’s not just the big players that matter; medium-sized and smaller enterprises also play a vital role. They often lead in niche markets or specialize in particular ores, making vital contributions to localized economies.
Global Supply Chain Considerations
The smelting industry is integrated into a broader global supply chain that’s increasingly complex. This interconnection means that local events can ripple across the globe, impacting costs and availability. For example, a mining strike in South America can delay ore shipments to smelters in Asia, affecting metal prices globally.
This dependency on international supply chains adds both strengths and vulnerabilities. On one hand, having diverse sources of raw materials can lead to stability, but on the flip side, it can also lead to significant risk during geopolitical tensions or natural disasters. Navigating these considerations is crucial for smelting companies, which must create strategies to ensure the smooth operation of their global logistics.
Employment and Industry Contribution
Job Creation Trends
The smelting industry is a major employment driver, creating numerous jobs across various skill levels. From unskilled laborers to advanced metallurgists, the workflow is diverse. Job creation trends indicate a stable demand for workers that has persisted even amid economic challenges.
Moreover, the industry often invests in training programs, enhancing the skills of the workforce, ensuring they can keep pace with technological advancements. This focus on development benefits both employees and employers, fostering a more competent labor market.
Sector's Contribution to GDP
The smelting industry significantly contributes to national Gross Domestic Product (GDP). In many countries, especially those rich in minerals, smelting operations account for a large share of industrial output. This is especially true for emerging economies where raw materials serve as crucial export commodities.
The unique feature here is the multiplier effect – as smelting facilities produce metals, they also create a demand for ancillary industries, such as transportation and equipment manufacturing, further boosting GDP. Regions that host smelting plants often see a thriving economy due to sustained job creation and economic activity.
Skilled vs. Unskilled Labor
Navigating the balance of skilled and unskilled labor is essential for the smelting industry. Skilled labor, often characterized by technical expertise and specialized training, commands higher wages but is also critical in improving the quality and efficiency of smelting processes. Conversely, unskilled labor provides the necessary support to keep operations running smoothly.
Interestingly, shifts towards automation in smelting are reshaping the labor landscape. While it may reduce the demand for unskilled positions, it increases the demand for skilled workers who can manage and maintain advanced technologies. This continuous evolution challenges the industry to foster a workforce prepared for the future.
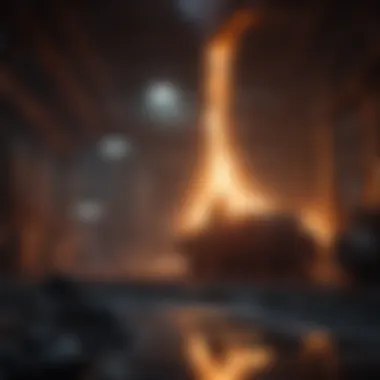
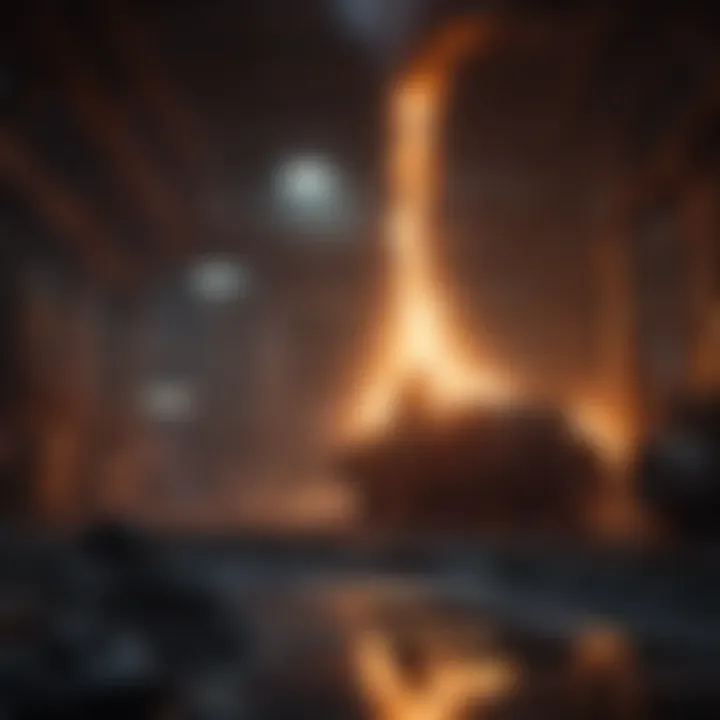
Environmental Considerations
Environmental considerations play a critical role in understanding the smelting industry, especially given its profound impact on the ecosystem. The process of smelting, while essential for metal production, brings along several environmental challenges that need addressing. By examining various facets of these issues, the article aims to shed light on how the industry is adapting to mitigate its ecological footprint and promoting sustainability.
Impact of Smelting on the Environment
The environmental implications of smelting are vast. This section takes a closer look at three primary aspects: air pollution, water resource management, and waste management challenges.
Air Pollution Issues
Air pollution resulting from smelting operations is not a trivial concern. Smelting emits sulfur dioxide and particulate matter, which can lead to respiratory problems in nearby communities. The key characteristic here is that these emissions can often exceed regulatory standards, posing a significant threat to public health. This is a critical point in the article because it emphasizes the pressing need for effective mitigation strategies.
One unique feature of air pollution in the smelting industry is its direct correlation with the types of materials used in the process. For example, lead and copper smelting tend to emit larger amounts of pollutants compared to iron smelting. Analyzing this aspect is beneficial as it not only educates the reader about the specific risks but also indicates areas where improvement and innovation are necessary.
Water Resource Management
Water resource management in smelting is another focal point. The process requires vast amounts of water, often putting immense strain on local resources. The key characteristic that stands out is the debate over water usage: the balance between production needs and environmental sustainability. This is a pertinent topic as it shows the evolving challenges that smelting operations face in maintaining efficiency without exhausting crucial water supplies.
The unique feature of water management issues lies in its cyclical impact; polluted water can impair local ecosystems and, in turn, affect the smelting operation's sustainability. Highlighting this allows for an expanded discussion on the importance of responsible water use and treatment processes, which is essential for long-term survival of both the industry and local environments.
Waste Management Challenges
Waste management is another substantial challenge for the smelting industry. The production process generates a significant volume of waste that can be hazardous. The key characteristic of this issue is its dual nature; not only does waste management involve dealing with existing waste, but it also requires preventing future waste generation.
This article considers waste management as a beneficial focus area because it presents an opportunity for technological advancement. One unique feature of current waste management practices is the growing trend to recycle and reuse materials. Some smelters are investigating ways to convert waste back into useable forms, which not only reduces environmental impact but can also offer a financial incentive.
Sustainability Practices
Sustainability is becoming increasingly important within the smelting industry. This section discusses how emerging green technologies, regulatory frameworks, and sustainable operations are shaping the future of smelting.
Emerging Green Technologies
Emerging green technologies are breaking new ground within the smelting industry. These advancements focus on reducing emissions and improving energy efficiency. The key characteristic of these technologies is their ability to integrate clean energy solutions, such as solar and wind power, into traditional processes. This represents a significant step towards a more sustainable approach to smelting.
A unique aspect of these technologies is that they often require initial investment, which can be a barrier for smaller operations. Yet, the long-term benefits, such as reduced costs and improved regulatory compliance, make these technologies a critical consideration for future industry developments.
Regulatory Frameworks
Regulatory frameworks play a pivotal role in shaping industry practices. They enforce standards that companies must meet, thus guiding operations toward more sustainable practices. The key characteristic of these frameworks is their evolving nature; as environmental science advances, regulations must adapt.
This article highlights the opportunity for companies to gain a competitive edge by exceeding these regulations, leading to a unique feature: proactive environmental stewardship can enhance a company’s reputation and market share in the long term.
Case Studies of Sustainable Operations
The examination of case studies related to sustainable operations offers practical insight into effective strategies implemented by smelting companies. Key characteristics of these case studies often include innovative processes that minimize waste and energy consumption, setting benchmarks for the industry.
A unique feature of focusing on these case studies is that they provide tangible examples of success, allowing other companies to follow suit. The sharing of best practices can inspire further adoption of sustainable methods across the industry.
Technological Advancements in Smelting
Technological advancements in smelting have been vital to the development and efficiency of the industry. The move towards more sophisticated methods and processes not only enhances productivity but also addresses the growing concerns surrounding environmental impacts and economic sustainability. These advancements have led to the rise of innovative techniques that aim to optimize resources, reduce waste, and improve overall metal recovery. In this section, we unpack the innovations reshaping the smelting landscape and the challenges that come with them.
Innovations in Smelting Technology
Automation and Smart Manufacturing
Automation and smart manufacturing represent a significant leap in smelting operations. The integration of advanced robotics and AI-driven systems streamlines processes that were once labor-intensive. For instance, automated furnaces enable uniform heating and contribute to enhanced material properties. The key characteristic that sets this apart is the precision it brings to the smelting process. This level of accuracy reduces operational errors and increases product consistency, making it a favored approach in modern smelting plants.
One unique feature of automation is the ability to monitor operations in real time. Managers can quickly adjust parameters, ensuring optimal performance. However, while automation improves efficiency, it does come with challenges, such as the initial high investment costs and the potential for job displacement.
Process Optimization Techniques
Process optimization techniques focus on fine-tuning the steps in smelting to maximize yield while minimizing costs. Techniques such as simulation modeling allow companies to predict the outcomes of different operational strategies before implementing them. This characteristic of foresight makes it invaluable for decision-makers.
The unique feature of these techniques lies in their data-driven nature. By analyzing vast amounts of historical performance data, companies can identify bottlenecks and inefficiencies. Yet, one downside is that smaller operations often lack the capital or expertise to deploy these sophisticated models, potentially widening the gap between larger and smaller firms in the industry.
Energy Efficiency Improvements
Energy efficiency improvements have become paramount in the quest for sustainability in smelting. By adopting technologies like electric arc furnaces and heat recovery systems, smelting operations are significantly reducing their energy consumption. The distinctive aspect of these improvements is their dual benefit: not only do they lower operational costs, but they also align with global movements towards reducing carbon emissions.
A unique feature of energy-efficient systems is their ability to harness waste heat and repurpose it, thus closing the loop in energy usage. Despite their many advantages, challenges persist; retrofitting existing plants to accommodate these new technologies can require significant financial resources and strategic planning.
Challenges in Adopting New Technologies
Despite the potential benefits of these advancements, several challenges inhibit their widespread adoption.
Economic Barriers
Economic barriers stand out as a significant hurdle in the transition to modern smelting technologies. High upfront costs associated with new equipment or processes can deter companies, especially smaller ones, from making these investments. Additionally, fluctuating market conditions can make it hard to justify such investments. Firms may need to weigh the potential long-term savings against the immediate financial outlay, which can be a tough balancing act.
The characteristic of economic barriers is that they not only affect individual companies but can also have far-reaching implications for the industry as a whole.
Technological Reluctance
Technological reluctance often arises from a fear of change. Implementing new systems means altering established workflows and can create discomfort among workers and management alike. This reluctance can stymie progress. One key feature is that companies may prefer to stick to what they know, operating under the notion that if it isn’t broken, why fix it?
The downside is that this resistence to change can limit a company’s capacity to innovate, keeping them from reaping the benefits of cutting-edge technologies.
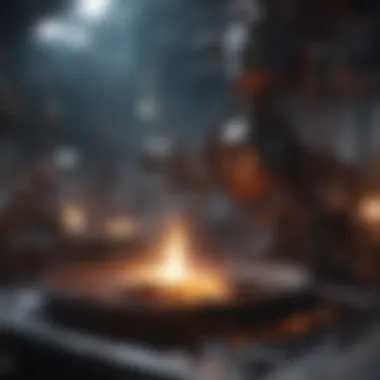
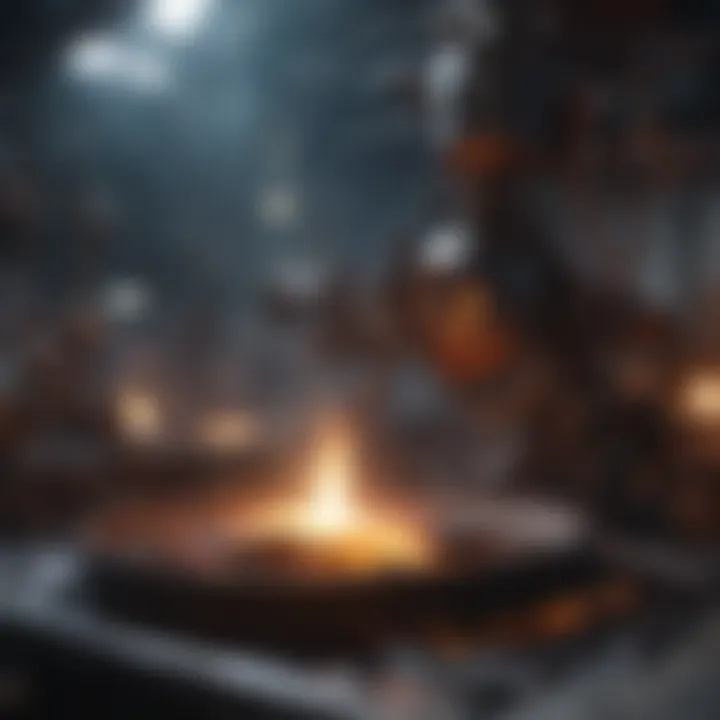
Integration with Existing Processes
Integrating new technologies into already existing workflows is no small feat. This process requires thorough planning and often, the retraining of staff to accommodate the changes. The characteristic of this challenge lies in the complexity of modern smelting operations, where multiple systems need to work in tandem.
Moreover, integration can be hampered by incompatible systems, leading to inefficiencies in operations. The benefit, however, is that overcoming such hurdles can lead to a transformative effect on overall productivity and sustainability in the long run.
"Staying ahead in the smelting industry requires not just innovation, but also a willingness to embrace change and adapt to new realities."
"Staying ahead in the smelting industry requires not just innovation, but also a willingness to embrace change and adapt to new realities."
Future Prospects for the Smelting Industry
As the smelting industry evolves, understanding its future prospects is critical for stakeholders across the board. The landscape is shifting due to numerous factors: economic changes, environmental challenges, and shifting consumer preferences. This section highlights specific elements, benefits, and considerations relevant to the future of smelting.
Economic Trends and Forecasts
Market Predictions
When discussing market predictions, one key aspect stands out: demand stability. The smelting sector often mirrors the needs of construction and manufacturing industries, which remain robust in growing economies. The unique feature of this aspect is its ability to adapt to fluctuations in raw material prices and technological advancements. Challenges include predicting economic downturns, which can leave the market vulnerable. However, companies that invest smartly in innovation often weather the storms better, making this approach a worthy consideration in our analysis.
- Key Characteristics of Market Predictions:
- Trends often correlate with global infrastructure projects.
- Increased recycling is changing ore demand.
Potential Growth Areas
Within potential growth areas, electrification and eco-friendly technologies offer promising avenues. There’s a push towards integrating clean energy in smelting operations, which can lead to new investment opportunities and reduced costs in the long run. The advantage here is twofold: companies can help combat climate change while also tapping into emerging markets focused on sustainable practices. However, companies need to weigh the risks of implementing new technology against their current production capabilities.
- Key Characteristics of Potential Growth Areas:
- Eco-friendly smelting processes may attract new investments.
- Energy-efficient technologies can lower operational costs.
Risks and Opportunities
The landscape for risks and opportunities is constantly fluctuating. One prominent risk is regulatory pressure demanding lower emissions, pushing some companies to make swift, potentially costly changes. Conversely, opportunities arise from innovation – companies that embrace R&D might find themselves leading the market. Being attuned to policy changes and consumer trends can differentiate successful firms from their competitors.
- Key Characteristics of Risks and Opportunities:
- Stricter regulations could increase operational costs.
- Adopting new technologies could open up new markets.
Adapting to Global Changes
Climate Change Impact
The impact of climate change on smelting is undeniable. As environmental policies tighten globally, smelting companies face the challenge of reducing their carbon footprint. This is significant since it affects not only operations but also consumer perceptions. The unique aspect is that companies must act decisively to maintain compliance while still aiming for profitability. Adapting quickly can lead to a firmer market position in the eyes of environmentally conscious consumers.
- Key Characteristics of Climate Change Impact:
- Emission regulations require new technology.
- Consumers increasingly favor sustainable products.
Global Trade Dynamics
Trade dynamics present another essential consideration. Tariffs, trade agreements, and geopolitical tensions can influence raw material costs and availability. Understanding these shifts is essential for long-term planning. Balancing domestic and international needs can provide flexibility and cushion against sudden changes. It often leads businesses to explore regional partnerships, helping them bolster their presence in global markets.
- Key Characteristics of Global Trade Dynamics:
- Impact of tariffs and international relationships on prices.
- Potential for regional partnerships to stabilize supply chains.
Evolving Consumer Demands
In the smelting sector, evolving consumer demands matter tremendously. The shift towards responsible sourcing and sustainability is changing how companies operate. This necessitates transparency in supply chains and production methods. The distinctive feature here is the growing trend of consumers willing to pay a premium for ethically produced metals, thereby pushing innovation further within the industry. Ignoring this shift could risk alienating a vital segment of the market.
- Key Characteristics of Evolving Consumer Demands:
- Increased demand for ethically sourced materials.
- Growing market for recycled metals as consumers shift preferences.
In summary, the future of the smelting industry hinges on adaptability and foresight. Companies that stay ahead of trends in economic dynamics, environmental regulations, and consumer demands will likely navigate the complexities ahead with greater ease.
In summary, the future of the smelting industry hinges on adaptability and foresight. Companies that stay ahead of trends in economic dynamics, environmental regulations, and consumer demands will likely navigate the complexities ahead with greater ease.
Culmination
In drawing a close on the complexities of the smelting industry, it’s crucial to understand the intricate web that binds its various dimensions. The significance of this sector transcends mere metal production; it plays an essential role in the overarching economic framework and environmental stewardship. The smelting industry serves not just as a conduit for material transformation but also as a reflection of technological evolution, economic resilience, and sustainability initiatives.
Summarizing Key Insights
As we look back at the critical aspects discussed throughout this article, several key insights can be highlighted:
- Historical Significance: The roots of smelting trace back to ancient civilizations, revealing its integral part in shaping human society through metallurgical innovation.
- Technological Evolution: From early rudimentary methods to modern automation, the smelting processes have evolved considerably—emphasizing the industry's adaptability and forward-thinking nature.
- Economic Impacts: The sector’s contribution to global markets cannot be overstated. Employment opportunities and GDP contributions underline its importance in supporting livelihoods and national economies.
- Environmental Challenges: The impact of smelting processes on the environment is substantial, raising concerns regarding air and water pollution. Yet, the rise of sustainability practices offers a hopeful path forward.
- Future Prospects: Anticipating market shifts, evolving regulations, and technological advancements will be essential for stakeholders aiming to navigate the future landscape of smelting.
Overall, these insights lay the foundation for understanding not only the present state of the smelting industry but also its potential trajectory.
Final Thoughts on the Future
Looking ahead, the smelting industry stands at a crossroads, faced with an array of challenges and opportunities. The increasing pressure to adopt greener practices and minimize environmental impact is undeniable. Innovations towards sustainable technologies may be the key to transforming how the industry operates, fostering a balance between economic profitability and ecological responsibility.
Moreover, as consumer demands shift towards more ethically sourced materials, smelting operations may need to re-evaluate their practices. Adapting to new regulatory frameworks and harnessing advancements in automation will likely play pivotal roles in propelling the industry into a new era.
The future of smelting is not just about metals; it's about a sustainable vision that aligns technological adaptability with environmental consciousness.
The future of smelting is not just about metals; it's about a sustainable vision that aligns technological adaptability with environmental consciousness.
In wrapping up our exploration, the smelting industry reflects a greater narrative of human innovation and resilience, offering a lens through which we can examine our broader interactions with nature and technology. As we move forward, it will be imperative for all stakeholders to engage with these shifts, ensuring that the industry's evolution continues to serve not just economic goals but also the sustainability of our planet.