Lithium Cell Manufacturing: Innovations and Insights
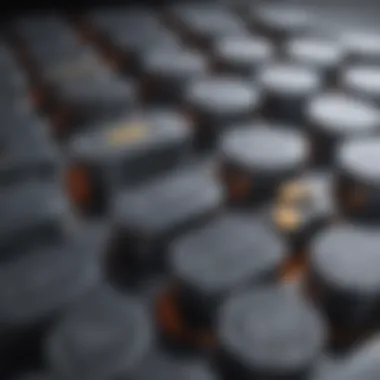
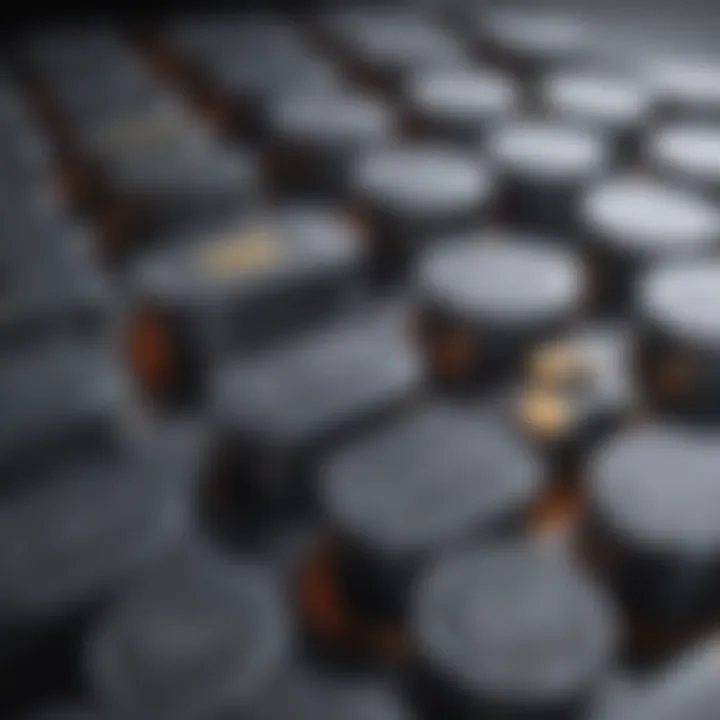
Intro
The lithium cell manufacturing process represents a cornerstone in the ever-evolving landscape of energy storage. As society pushes toward sustainable energy solutions, the importance of understanding how these cells are crafted cannot be overstated. Lithium-ion batteries power everything from electric vehicles to portable electronics, ensuring that energy storage is both efficient and reliable. Notably, the world is increasingly investing in these technologies, which are integral to reducing carbon emissions and enhancing energy efficiency.
At the heart of lithium cell manufacturing is the seamless synergy of materials, innovative technologies, and stringent methodologies that contribute to the creation of these advanced energy devices. From the selection of raw materials to the final testing phases of production, each step is an intricate dance of precision and engineering prowess. Moreover, the quest for sustainability has sparked significant innovations in manufacturing processes, pushing the boundaries of what is possible with lithium cells. This article aims to dissect these facets in detail, illuminating the complexities and advancements that define modern lithium cell manufacturing.
Prolusion to Lithium Cell Technologies
Lithium cell technologies have emerged as a cornerstone in the realm of energy storage, making strides into various sectors, from consumer electronics to electric vehicles. The significance of understanding these technologies cannot be overstated as the world pivots towards greener energy solutions. The very essence of lithium batteries revolves around their ability to store and release energy efficiently, adapting to the growing demands for portable energy.
The nuances in manufacturing lithium cells are not mere technicalities; they form the bedrock of innovation in energy solutions. The key elements include the types of lithium batteries available, the chemistry involved, and the production processes that ensure quality and sustainability. Diving deeper into these components, we unravel their interconnectedness that leads to advancements in performance, safety, and environmental impact.
Historical Context
The journey of lithium cell technology dates back to the late 20th century when they were first utilized in niche applications. The early adopters of lithium batteries primarily revolved around consumer electronics, paving the way for their significant role in daily life. The 1991 introduction of lithium-ion batteries marked a turning point, allowing for higher energy densities compared to traditional lead-acid batteries. Since then, the technology has evolved tremendously, with ongoing research focused on enhancing performance and lifespan.
Today, lithium polymer and lithium iron phosphate cells are among the options available, each tailored for specific needs and applications. The timeline has proven crucial in shaping where we stand now—lithium technologies are no longer an afterthought; rather, they've become pivotal in the shift towards electric mobility and renewable energy sources.
Importance in Modern Applications
In our current landscape, the relevance of lithium cell technologies is hard to miss. From powering smartphones to electric cars, their presence is pervasive and growing.
- Energy Transition: As the world seeks alternatives to fossil fuels, lithium batteries support the transition to renewable energy systems, allowing for efficient storage of solar and wind energy.
- Enhanced Portability: Consumer demands for lightweight, high-capacity batteries drive innovation, ensuring that devices are more efficient and user-friendly.
- Economic Impact: The growing sector contributes significantly to job creation and economic growth, particularly in manufacturing and research.
"The lithium battery landscape not only boosts technology but also champions sustainability and economic opportunities across the globe."
"The lithium battery landscape not only boosts technology but also champions sustainability and economic opportunities across the globe."
Core Components of Lithium Cells
Understanding the core components of lithium cells is crucial, as these elements form the backbone of battery function and efficiency. Lithium batteries, particularly lithium-ion cells, have become the heart of modern portable power sources. The intricacies of their chemistry, the selection of electrolytes, and the choice of anode and cathode materials all play significant roles not only in performance but also in safety and longevity.
Lithium Ion Chemistry
Lithium-ion chemistry represents a groundbreaking advance in energy storage technology. At its core, this chemistry centers around the movement of lithium ions between the anode and cathode during charge and discharge cycles. When a lithium ion battery is charged, lithium ions migrate from the cathode to the anode, resulting in chemical reactions that store energy.
This interplay is not merely a backdrop to the conversation; it has practical ramifications. For instance, the efficiency of energy transfer during these cycles is pivotal for applications from smartphones to electric vehicles.
The stability of lithium compounds is a particularly important factor. Variations like lithium cobalt oxide exhibit high capacity but may lead to thermal runaway, while lithium iron phosphate is considered safer, albeit with less energy density. Engaging in ongoing research to optimize these materials ensures that advancements in lithium ion chemistry directly contribute to better performance and safety in real-world applications.
Electrolyte Selection
Electrolytes serve as the lifeblood of lithium cells, facilitating the conduction of ions. The selection process is not as straightforward as picking something off the shelf; it involves weighing various options and their implications. Electrolytes can be liquid, solid, or gel-based, each type bringing its own unique benefits and drawbacks.
For example, liquid electrolytes often offer better ionic conductivity, which translates to higher performance. However, there's a trade-off in terms of safety and volatility. In contrast, solid electrolytes promise increased safety and stability but are currently hampered by lower conductivity.
Furthermore, the choice of electrolyte interacts deeply with the anode and cathode materials, influencing overall efficiency and lifespan of lithium-ion batteries.
Anode and Cathode Materials
The materials used for the anodes and cathodes are arguably the most defining aspects of lithium cells. Both play distinct yet interdependent roles in the energy storage mechanism. The anode, commonly made from graphite, engages lithium ions during charging. Various other materials like silicon are being explored for their higher capacities, but they come with challenges such as volume expansion.
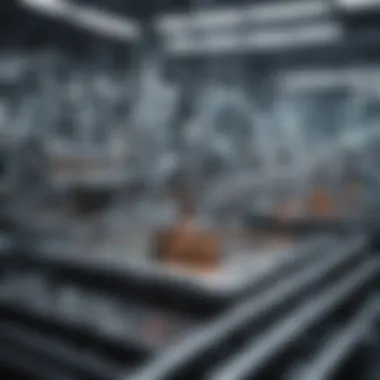
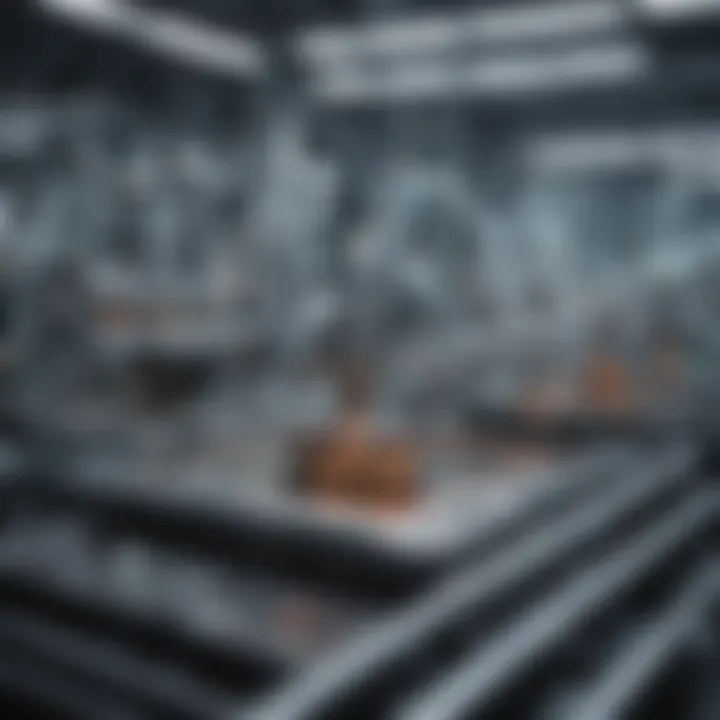
On the flip side, the cathode materials often include combinations like lithium nickel cobalt aluminum oxide. Each of these materials contributes unique characteristics to the battery, such as energy density and thermal stability. Policymakers and manufacturers need to consider the environmental impact of these materials, as mining and processing them can have significant ecological ramifications.
Manufacturing Process Overview
The manufacturing process in lithium cell production is a pivotal stage that determines not just the quality, but also the performance of the final product. As lithium-ion batteries power everything from smartphones to electric vehicles, understanding the intricacies of production is crucial for those involved in the energy sector. This section captures the essence of the various manufacturing stages, ensuring that the delicate balance between efficiency, quality, and sustainability is struck.
Raw Material Sourcing
Sourcing the right materials is akin to finding the golden key that unlocks the door to high-performance lithium cells. Quality raw materials significantly influence the battery's capacity, cycle life, and overall effectiveness. Lithium carbonate, the cornerstone of lithium-ion batteries, is primarily extracted from brine pools and hard rock mining. The sourcing process involves careful consideration of not just price, but also the environmental impact of extraction methods.
In recent years, sustainable sourcing practices have gained traction. The focus has shifted towards recycling lithium from old batteries, reducing reliance on earth-mined resources. Companies are now seeking partnerships with local suppliers who adhere to ethical mining practices. This aligns with the growing consumer demand for environmentally responsible energy solutions.
Electrode Preparation Techniques
Once the materials are sourced, the next step is electrode preparation, which is vital for battery performance. This process involves several stages:
- Mixing: The active materials—usually some form of lithium—are combined with conductive additives and a binder to ensure structural integrity. This is like making a cake; you need the right ingredients mixed in just the right proportions.
- Coating: The mixed slurries are then coated onto metal foils, typically copper for the anode and aluminum for the cathode. This creates a thin layer, which is crucial for efficient ion transport during charging and discharging.
- Drying: After coating, the electrodes undergo a drying process to remove any residual solvent, ensuring optimal performance.
- Rolling and Cutting: The plates are rolled into a thin, seamless layer and cut into the desired shape, preparing them for assembly. This stage demands precision, as any flaws can lead to weak points in the battery.
Cell Assembly
The final phase in the manufacturing process is cell assembly, which can be regarded as the orchestration of all previous stages. Here, the prepared electrodes are brought together along with the electrolyte, forming the heart of the battery. This stage typically involves:
- Stacking or Winding: Depending on the cell design, electrodes are either stacked or wound into a cylindrical shape, which allows for compact designs without sacrificing performance.
- Sealing: Once the electrodes and electrolyte are in place, the cells are sealed, often in a cleanroom environment to prevent contamination. Any exposure to air or moisture can compromise battery performance.
- Formation Cycling: Finally, the batteries undergo formation cycling, which involves charging and discharging the cells a few times to stabilize them. This step is critical in ensuring that the cells operate at their full potential once they reach consumers.
Quality Control in Lithium Cell Production
Quality control is like the backbone of lithium cell production, ensuring each cell meets performance and safety standards before it hits the market. This meticulous process helps in mitigating risks and enhancing product reliability, which is paramount given the rising stakes of energy storage solutions in today's fast-paced world. Without effective quality control, production defects can lead to significant costs and safety hazards.
In lithium cell manufacturing, quality control encompasses various stages of the production line—from raw material sourcing to final assembly. Each step must be carefully monitored and evaluated. For instance, an impurity in the electrolyte could result in diminished performance or even cell failure. Hence, the role of quality control is not just a box-ticking exercise but a necessary practice for delivering high-efficiency batteries.
Moreover, robust quality control practices enforce regulatory compliance, which is becoming increasingly important as governments and industries push for stricter safety and environmental standards. For manufacturers, this means not only adhering to regulations but harnessing the benefits of certified products that can command higher market prices. Products passing quality standards build confidence among consumers and stakeholders alike.
Testing Methods
When it comes to testing methods in lithium cell production, manufacturers rely on a comprehensive suite of techniques to evaluate various performance parameters. These include but are not limited to:
- Performance Testing: This involves measuring capacity, energy density, and cycle life under controlled conditions. High-quality cells should exhibit consistent performance over numerous charge-discharge cycles.
- Safety Testing: Given the potential hazards associated with lithium batteries, such as thermal runaway, safety testing is critically important. Methods might include short circuit tests, puncture tests, and thermal cycling tests to evaluate how cells respond under extreme conditions.
- Electrochemical Testing: This technique determines the cell's efficiency through methods like impedance spectroscopy, which helps assess the internal resistance and overall health of the cell.
- Visual Inspection: Although it may seem simple, visual inspections of the cells for physical defects, such as leaks or seals, can prevent many operational failures later.
These testing methods are not just routine procedures; they are a lifeline aimed at ensuring the integrity and safety of the final product. In an industry that’s often under the microscope, having rigorous testing protocols can enhance a manufacturer's reputation in a competitive landscape.
Standards and Regulations
Standards and regulations form the bedrock of quality assurance in lithium cell manufacturing. They provide a framework that guides manufacturers towards achieving a uniform level of quality and safety in their products.
The following key standards often apply in this field:
- International Electrotechnical Commission (IEC) Standards: These global standards focus on safety and performance requirements for lithium-ion batteries, ensuring they can be safely used in consumer electronics, automotive, and industrial applications.
- Underwriters Laboratories (UL) Certification: UL certifications signal that a product has met specific safety criteria in stringent tests, reassuring customers and manufacturers in markets like electric vehicles.
- REACH Compliance: As environmental regulations tighten, the EU’s REACH regulation requires manufacturers to assess the risks associated with chemical substances used in battery production, ensuring minimal environmental impact.
Adhering to these standards not only helps in ensuring the quality of the batteries produced but also enhances market acceptance and trust. The complex landscape of regulations can be overwhelming, but manufacturers who prioritize compliance will often find themselves better positioned in the market, ultimately impacting their bottom line and sustainability efforts.
"Effective quality control transforms challenges into opportunities, paving the way for resilient, high-quality products that stand the test of time."
"Effective quality control transforms challenges into opportunities, paving the way for resilient, high-quality products that stand the test of time."
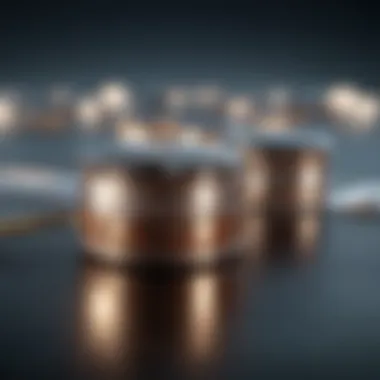
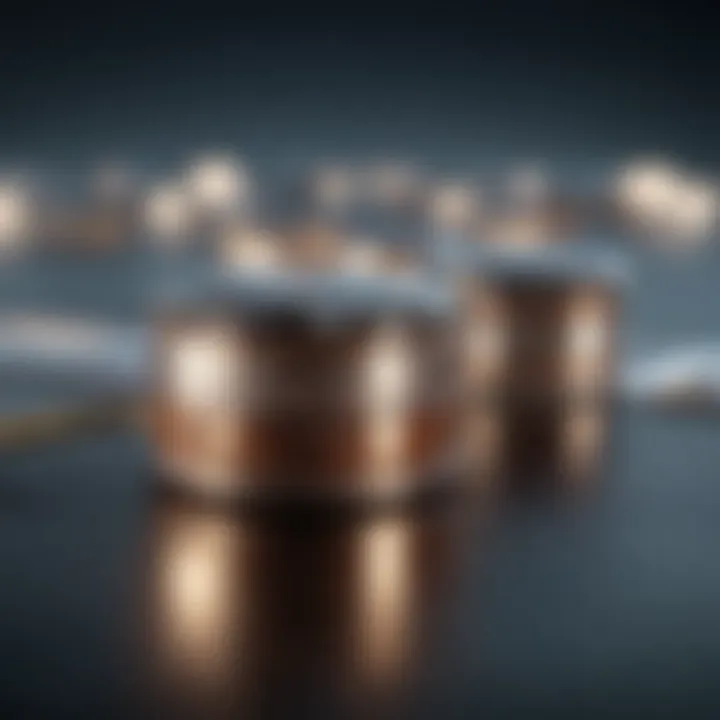
In summary, quality control in lithium cell production is not simply an obligation; it is an integral component that intertwines testing methods and regulatory adherence into the very fabric of manufacturing excellence.
Advancements in Lithium Battery Manufacturing
The landscape of lithium battery manufacturing is constantly evolving, driven by innovations that aim to enhance efficiency, sustainability, and performance. As the demand for energy storage solutions surges, particularly through electric vehicles and renewable energy integration, advancements in this sector become increasingly imperative. These innovations not only address the challenges of production but also significantly impact the longevity and effectiveness of lithium cells, which are prevalent in many modern applications. Understanding these advancements is crucial for anyone involved in the industry or closely following technological developments in energy solutions.
Automation and Robotics in Production
In today’s environment, automation and robotics have revolutionized lithium battery production processes. They streamline operations, reduce human error, and significantly ramp up efficiency. Automated systems can perform tasks ranging from electrode assembly to cell testing, making it possible to manufacture lithium cells at a pace that manual labor simply cannot match.
A major benefit of using automation is the consistency it brings. Robots equipped with precision tooling ensure that each cell produced meets stringent quality standards. For instance, consider how robotic arms can handle materials in a clean room setting, minimizing contamination risks. This controlled environment is essential, given that even minor impurities can negatively affect battery performance.
Additionally, the integration of advanced software in production lines allows for real-time monitoring and data collection. Manufacturers can immediately identify and rectify production bottlenecks or quality issues.
"Automation stands not just as a solution for better production but as a stepping stone towards the future of energy storage technology."
"Automation stands not just as a solution for better production but as a stepping stone towards the future of energy storage technology."
To further illustrate, many companies are investing in flexible automation systems. These systems adapt easily to changes in production needs, catering to various cell designs without extensive downtime. It's a shift that's proving invaluable in responding to market demand fluctuations.
Materials Innovation
Another pivotal area in advancements in lithium cell manufacturing is materials innovation. The quest for more efficient, safer, and cheaper materials is a driving force behind research and development within the industry. For example, researchers are exploring alternative anode materials such as silicon, which has a theoretical capacity significantly higher than traditional graphite, potentially leading to batteries with longer life and higher energy densities.
Moreover, electrolyte materials are undergoing innovative changes as well. Solid-state electrolytes are an exciting prospect, providing advantages such as increased safety by reducing flammability risks compared to liquid electrolytes. This shift not only promises to enhance battery lifespan but also hints at better overall performance in various applications.
In terms of sourcing materials, companies are increasingly looking to sustainable practices. The push for recyclable and more ethically sourced materials reflects a broader trend within manufacturing as stakeholders become more aware of their environmental footprint.
Here are some key aspects of materials innovation in lithium battery manufacturing:
- Increased Energy Density: New materials enable batteries that can store more energy.
- Enhanced Safety: Innovations reduce the chance of battery malfunctions.
- Cost-Effectiveness: Research aims to lower the costs associated with more advanced materials.
The advancements in materials reflect not only a response to technological demands, but also an evolving understanding of material science, which is critical for addressing the long-term demands of energy storage solutions. Together, automation and materials innovation represent key pillars in the ongoing transformation of lithium cell manufacturing.
Sustainability in Lithium Cell Manufacturing
The importance of sustainability within lithium cell manufacturing cannot be understated, especially in an age where climate change and resource depletion are at the forefront of global conversations. As the dependence on lithium batteries grows, so does the pressing need for manufacturers to embrace eco-friendly practices. Striking a balance between meeting energy storage demands and preserving the planet is more than just a noble aspiration; it is an essential strategy for the future of this industry.
Recycling of Lithium Batteries
One of the cornerstones of sustainability in lithium cell manufacturing is recycling. Lithium batteries, used extensively in everything from smartphones to electric vehicles, do not have to end their lives in landfills. Through effective recycling processes, manufacturers can recover valuable materials such as lithium, cobalt, and nickel, which in turn can be reintroduced into the production cycle. This not only lessens the extraction pressure on natural reserves but also reduces the carbon footprint associated with mining and processing raw materials.
- Closed-Loop Systems: Many companies are adopting closed-loop systems, focusing on recycling spent batteries to create an internal supply of materials.
- Innovative Technologies: New technologies are emerging that enhance the efficiency of battery recycling, including methods that can recover nearly 100% of valuable metals.
- Economic Benefits: Recycling can also be economically advantageous. Less reliance on virgin materials can lead to reduced production costs in the long run, promoting a more sustainable economy.
"Recycling lithium batteries isn't just about saving the planet—it's about resource efficiency that makes business sense."
"Recycling lithium batteries isn't just about saving the planet—it's about resource efficiency that makes business sense."
By recognizing the value of used batteries, the industry can transform waste into a resource, paving the way for a more circular economy.
Environmental Considerations
Environmental matters stand as a crucial pillar in the sustainability narrative of lithium cell manufacturing. The footprint left by lithium extraction and battery production can be significant, impacting both ecosystems and communities. Thus, developing strategies to mitigate these impacts is vital.
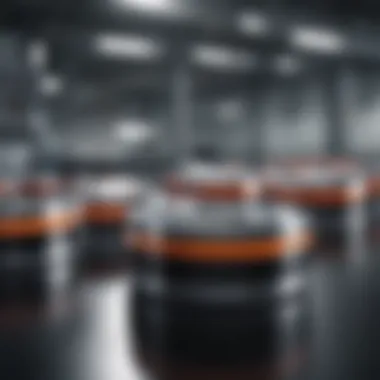
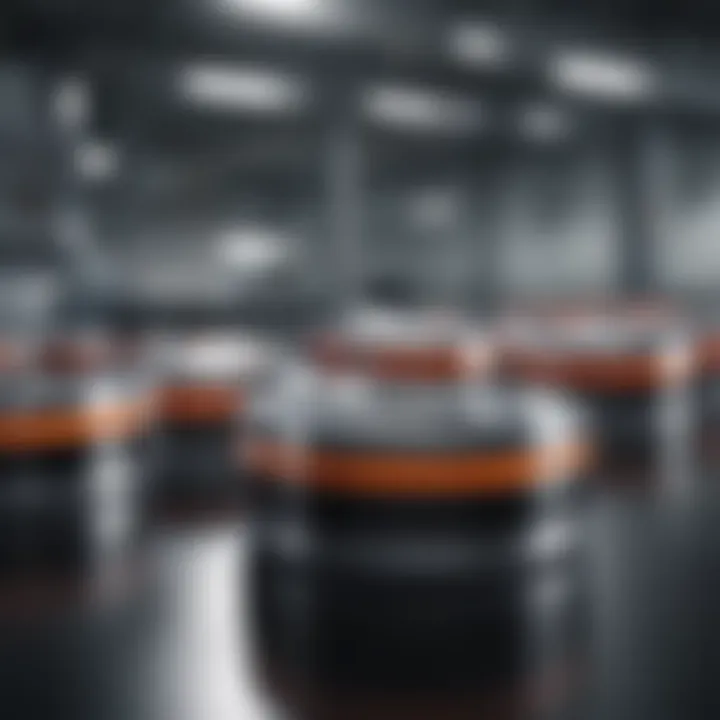
- Water Usage: The extraction of lithium from brine involves considerable water use, particularly in arid regions. Manufacturers are investing in technologies to minimize this usage, such as closed-loop water systems.
- Land Disturbance: Mining activities can result in substantial land degradation, affecting local flora and fauna. Sustainable practices now focus on minimizing land disturbance and rehabilitating mined areas post-extraction.
- Toxic Waste Management: As with any manufacturing process, lithium cell production can generate waste products. Implementing stringent waste management protocols is essential to ensure harmful substances do not leach into the environment or adversely affect worker health.
In summary, the incorporation of sustainable practices in lithium cell manufacturing not only addresses ethical concerns but also leads to thriving economic and operational benefits. As the industry adapts to these complexities, it lays the foundation for a more sustainable energy future.
Future Trends and Challenges
The realm of lithium cell manufacturing is witnessing swift transformations, and comprehending the future trends and challenges within this domain is imperative. As the world leans heavily on energy storage solutions, staying ahead in technology and market dynamics becomes crucial. The following sections will delve into emerging technologies that promise to redefine manufacturing processes and how market dynamics and demand shape the landscape for lithium cells in the forthcoming years.
Emerging Technologies
Innovations in electrical storage are tilting towards more efficient and sustainable practices. Many rapid advancements are being made in materials and production techniques, making it essential to keep an eye on what's brewing in this space. For instance, solid-state batteries are captivating the attention of researchers and manufacturers alike. Unlike traditional lithium-ion cells, these batteries utilize solid electrolytes instead of liquid ones, which can result in higher energy density and improved safety. This could be a significant game-changer in sectors demanding high-performance, such as electric vehicles and aerospace.
Additionally, artificial intelligence and machine learning are being increasingly integrated into lithium cell manufacturing. These technologies enable manufacturers to optimize production processes, predict failures, and reduce waste, thus achieving not just efficiency but also sustainability. Using AI for thorough data analysis can also lead to smarter sourcing of materials and better quality control methods.
- Prospective gains from these technologies:
- Challenges to consider:
- Improved energy density
- Enhanced safety features
- Reduced production costs
- High R&D costs
- Need for thorough testing for market readiness
One risks discussing emerging technologies is falling into the trap of overhyping their potential. While they're promising, many still need considerable development and proving grounds before becoming commercially viable. It's crucial for manufacturers to balance innovation with practical application.
Market Dynamics and Demand
The landscape of lithium cell manufacturing is predominantly shaped by market dynamics, influenced by factors such as energy consumption trends, evolving technological requirements, and global economic conditions. As countries move towards sustainability, the demand for electric vehicles continues to soar, pushing the boundaries for lithium-ion technology.
Given that lithium is a finite resource, its supply chain is under scrutiny. Manufacturers must be agile in sourcing materials, ensuring that they can meet growing demands without compromising quality or sustainability. New entrants to the market mean competition is heating up; hence, leveraging competitive pricing and promoting innovative solutions can differentiate one player from another.
Furthermore, the rise of the second-hand market for electric vehicles is also reshaping demand for lithium cells. As people opt for more environmentally friendly options, looking at battery lifecycle management becomes critical. Reusing and recycling lithium batteries opens new markets and drives the development of innovative recycling technologies.
"The adaptability of manufacturers to shifting demands will determine their longevity in the market."
"The adaptability of manufacturers to shifting demands will determine their longevity in the market."
To encapsulate, the evolving trends in lithium cell manufacturing are both exciting and challenging. As new technologies emerge and market demands reshape the industry, a strategic approach is necessary to navigate the complexities ahead. Companies must engage in forward-thinking to adapt and innovate in response to the ever-shifting landscape of energy storage solutions.
Ending
The conclusion serves as a vital component of any discussion on lithium cell manufacturing, offering a synthesis of the intricate details explored throughout the article. It encapsulates the advancements in technology and materials that are shaping this field, while also emphasizing the significance of ongoing research.
Firstly, the core insights discussed demonstrate not only how pivotal lithium cells are in various applications—from consumer electronics to electric vehicles—but also the necessity for robust manufacturing processes to uphold quality and efficiency. The reader should recognize that the journey from raw materials to finished products is fraught with challenges, yet it is also ripe with opportunities for innovation.
Secondly, the benefits of improved sustainability practices within lithium cell manufacturing cannot be overlooked. It's crucial to weigh the environmental implications of battery production and to consider how recycling initiatives can extend the lifecycle of lithium batteries, thereby reducing waste and resource consumption.
Moreover, understanding the market dynamics and consumer demand further underscores the importance of agility within the manufacturing sector. As the demand for lithium-powered devices skyrockets, the industry must adapt swiftly to meet new pressures and expectations.
In short, this article not only highlights the state of lithium cell manufacturing today, but it also outlines the pathways toward its future. The challenges identified—be they technological, environmental, or economic—will require dedicated research and innovative approaches. Thus, the conclusion serves as both a summary of vital information and a clarion call for ongoing investigation into the complexities and potential of lithium cell technology.
Summary of Key Points
- Lithium cells play a crucial role in energy storage solutions in a breadth of sectors, including electric vehicles and portable electronics.
- Advancements in materials and technologies are enhancing manufacturing efficiency and product quality.
- Sustainability efforts, such as battery recycling, are essential for minimizing environmental impact.
- Market dynamics are shifting, creating new demands for greater efficiency and adaptability in production processes.
Implications for Future Research
The landscape of lithium cell manufacturing is dynamically shifting, and it presents a fertile ground for future exploration. Here are a few areas ripe for further study:
- Alternative Materials: Investigating new anode and cathode materials that could improve battery performance, longevity, and sustainability.
- Recycling Technologies: Developing innovative methods for effectively recycling lithium batteries to reclaim valuable materials without significant energy costs.
- Process Optimization: Identifying ways to streamline the manufacturing process to reduce costs and enhance product quality.
- Regulatory Impacts: Studying how evolving regulations regarding environmental policies might influence production methodologies in the lithium battery market.
In closing, the future of lithium cell manufacturing is poised for transformation, driven by technological, environmental, and regulatory changes. Emphasizing continual research and investigation in this sphere will ensure that advancements not only meet market demands but also contribute positively to environmental sustainability.