Understanding Fiber Reinforced Plastics in Depth
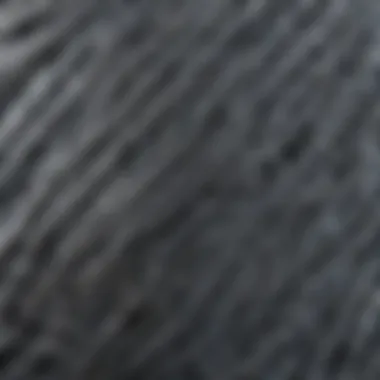
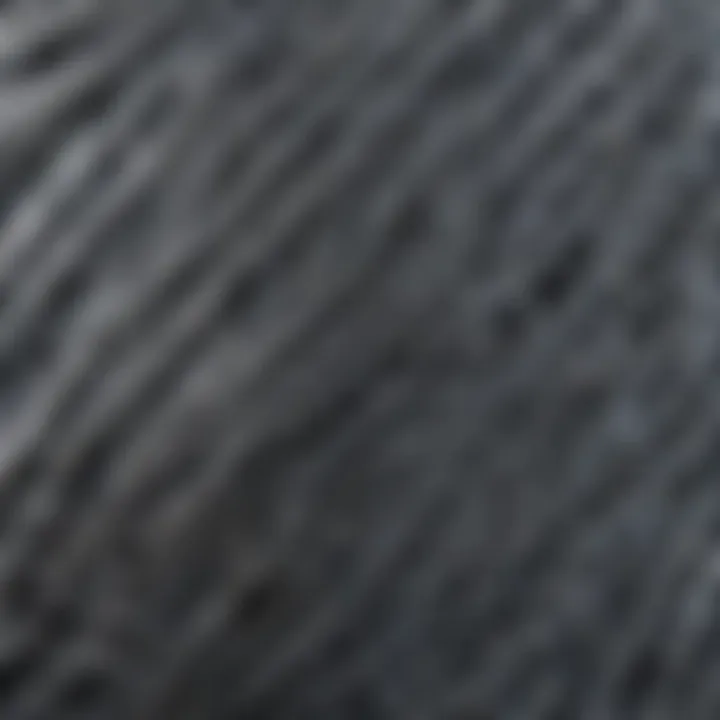
Intro
Fiber reinforced plastics (FRPs) stand at the intersection of material science and engineering innovation. They embody a unique fusion of lightness and robustness, offering solutions to a range of challenges across various industries. Understanding FRPs requires a closer look at their components, production methods, and the diverse applications that harness their strengths.
These materials are not just fancy names in a textbook; they're actively reshaping fields like automotive, aerospace, and construction. This article will unpack numerous facets of FRPs, spotlighting everything from their basic definitions to the intricate manufacturing techniques that yield these versatile materials.
By exploring both the benefits and hurdles of using FRPs, we aim to illuminate their significance in today’s tech-rich landscape.
Key Concepts
Definition of the Main Idea
At its core, fiber reinforced plastics are composite materials created by embedding fibers within a plastic matrix. This structure enhances the mechanical properties of the plastic, resulting in a material that is both lightweight and exceptionally strong. It’s a bit like making a sandwich, where the bread is the plastic and the filling is the fiber—it’s the combo that counts.
Overview of Scientific Principles
The scientific principles behind FRPs hinge on the interactions between the fibers and the plastic. The fibers, often made of materials such as glass, carbon, or aramid, provide tensile strength, while the plastic acts as a binding agent. This bond is crucial; it allows the fibers to distribute external forces over a larger area, effectively improving durability and performance.
Understanding these interactions involves delving into areas such as:
- Mechanical Properties: These include strength, stiffness, and toughness, all vital for determining how the material will perform under stress.
- Manufacturing Processes: Techniques like pultrusion, layup, and resin transfer molding play a significant role in the properties of the final product.
- Applications: Identifying where FRPs are used helps gauge their relevance in real-world contexts, from automotive parts to infrastructure components.
"Fiber reinforced plastics are the backbone of modern engineering solutions, merging innovation with practical application."
"Fiber reinforced plastics are the backbone of modern engineering solutions, merging innovation with practical application."
Current Research Trends
Recent Studies and Findings
Research on FRPs has seen a surge in recent years, with scholars and professionals keen on understanding not only their mechanical properties but also their long-term performance and sustainability. Recent studies have shown that:
- Recycling Methods: There’s a growing technological focus on effective recycling processes for FRPs, which is crucial as sustainability becomes paramount in material production.
- Bio-based Fibers: New studies are looking into integrating natural fibers as reinforcement, which could offer an eco-friendlier alternative to conventional materials.
Significant Breakthroughs in the Field
Several breakthroughs have transformed our outlook on FRPs, highlighting their versatility and expanding their potential applications. Among these advancements are:
- Enhanced Durability: Innovations in resin formulation have resulted in FRPs that can endure extreme environmental conditions, pushing their applications further.
- Smart Composites: Researchers are integrating sensors into FRPs, enabling these materials to provide real-time feedback on their structural integrity.
As we navigate through the complexities of fiber reinforced plastics, it’s imperative to consider both the revolutionary advancements and the challenges that lie ahead. Each step taken in research not only broadens our understanding but also shapes the use of these materials in future applications.
Understanding Fiber Reinforced Plastics
Fiber reinforced plastics (FRPs) are increasingly important in various sectors due to their remarkable mix of durability and lightweight properties. These materials are not just a passing trend; they embody the future of engineering and material science. By understanding FRPs, industries can leverage their strengths for innovation while addressing critical sustainability challenges.
The essence of fiber reinforced plastics lies in their composition. They combine plastic polymers with reinforcing fibers, each of which brings unique benefits. This combination results in materials that are often stronger than steel yet lighter, making them ideal for applications where weight savings are crucial. The relevance of FRPs, particularly in fields like aerospace and automotive, cannot be overstated. These sectors demand materials that enhance performance while reducing fuel consumption and emissions.
Definition and Composition
Fiber reinforced plastics are composite materials made from a polymer matrix and reinforcing fibers. The polymer serves as a matrix, holding the fibers together, which provide added strength and rigidity. The most common types of plastic used in FRPs include epoxy, polyester, and vinyl ester. The choice of polymer affects the overall characteristics of the finished material, such as its flexibility, resistance to chemicals, and thermal properties.
The fibers can be made from various materials, including glass, carbon, and aramid, each contributing distinct characteristics to the composite. This layered structure not only enhances strength but also influences how the material behaves under stress, making FRPs an attractive option for many applications.
Types of Reinforcements Used
Understanding the types of reinforcements used in fiber reinforced plastics is critical for selecting the right material for any application. Each type of fiber brings its own advantages and disadvantages.
Glass Fiber
Glass fiber is one of the most common reinforcements used in FRPs. It’s well-known for its excellent tensile strength and low cost, making it a go-to choice in many industries. The unique feature of glass fibers lies in their ability to resist moisture and chemicals, which is crucial for products exposed to harsh environments. While they may lack the specific lightweight characteristic of carbon fibers, their durability and versatility make them tremendously popular.
However, it’s important to consider the trade-offs. Although glass fiber composites are already strong, their stiffness isn’t comparable to that of carbon fiber composites. Generally, they are viewed as a good starter material, particularly for applications where cost is a concern, and ultra-high performance is not the primary goal.
Carbon Fiber
Carbon fiber is celebrated for its high strength-to-weight ratio, making it a top choice for applications where performance and weight are paramount, such as in high-end sports cars and aircraft components. The key characteristic of carbon fiber is its rigidity and resilience, contributing to improved performance and fuel efficiency when integrated into designs.
One unique feature of carbon fiber is its carbon nanotube structure which greatly enhances its mechanical strength. However, these advantages come with a price; carbon fiber products are often considerably more expensive than their glass fiber counterparts. Additionally, carbon fibers can be less resistant to impact compared to glass fibers, which can be a concern in certain applications.
Aramid Fiber
Aramid fibers, like Kevlar, are known for their exceptional toughness and resistance to abrasion. These fibers are particularly significant in applications that require enhanced impact resistance, such as bulletproof vests or protective gear. The key characteristic of aramid fibers lies in their unique chemical structure that offers both strength and flexibility, making them suitable even in challenging environments.
However, aramid fibers can be more challenging to work with due to their inherent properties. They are more expensive, which might make their use less ideal for some applications. Plus, they have a tendency to degrade when exposed to UV light, posing a limitation for external applications.
In summary, the choice of reinforcing fiber is vital in determining the performance and suitability of fiber reinforced plastics for specific applications. Each type—glass, carbon, and aramid fibers—brings its own set of benefits and drawbacks, influencing design and material decisions in engineering.
In summary, the choice of reinforcing fiber is vital in determining the performance and suitability of fiber reinforced plastics for specific applications. Each type—glass, carbon, and aramid fibers—brings its own set of benefits and drawbacks, influencing design and material decisions in engineering.
These insights into fiber reinforced plastics and their composition are key for professionals and researchers navigating this complex landscape. Each of these fibers plays a crucial role in defining the capabilities of FRPs, shaping the future of materials science.
Manufacturing Processes
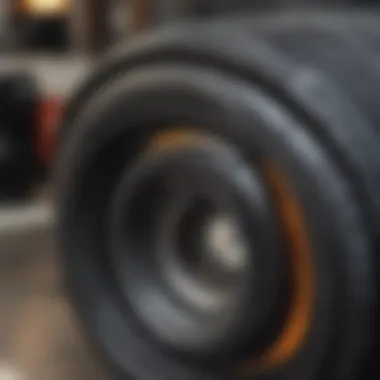
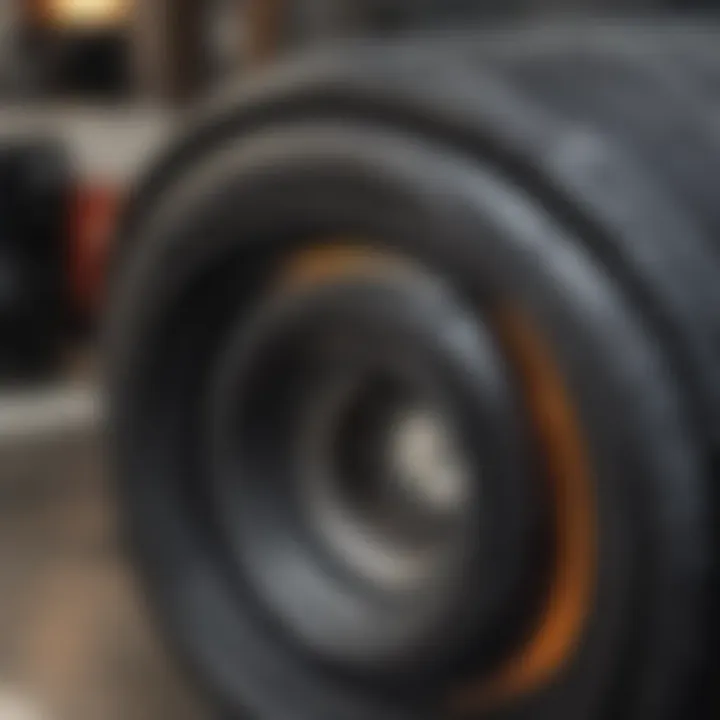
The manufacturing processes of fiber reinforced plastics (FRPs) stand at the heart of their versatility and functionality. With a myriad of techniques available, each method provides distinct advantages tailored to specific applications. Understanding these processes leads to a greater appreciation for the innovations and capabilities of FRPs in various industries. Each method can influence the material’s ultimate performance, cost, and production efficiency, making it vital to grasp the nuances involved.
Lay-Up Methods
Lay-up methods, whether manual or automated, play a significant role in creating FRPs with tailored characteristics. Traditional hand lay-up involves laying layers of resin-soaked fibers onto a mold, which allows for precision in designing complex shapes. This technique is highly scceptible to customization, but it requires a skilled hand to ensure even layering and proper adhesion.
On the other hand, the automated variant, known as automated fiber placement, brings efficiency into play. It uses programmed machines to deposit fibers with exceptional accuracy. This method is essential for high-volume production while maintaining quality standards, especially in aerospace applications where reliability is paramount.
Injection Molding Techniques
Injection molding techniques represent another cornerstone in the fabrication of fiber reinforced plastics. This method allows for rapid production of complex shapes at lower costs compared to traditional techniques. During this process, a thermoplastic resin reinforced with fibers is heated until molten and then injected into a mold where it cools and hardens.
Injection molding is particularly favored for its ability to produce high-strength parts with minimal waste. However, it’s crucial to consider factors like fiber length and orientation, as these can significantly impact the mechanical properties of the finished product. The advantage of this technique shines through in industries such as automotive, where mass production of lightweight yet durable components is key.
Pultrusion and Its Advantages
Pultrusion stands out as a continuous process for producing composite profiles with exceptional consistency and quality. Unlike other methods, pultrusion pulls raw materials through a resin bath and into a heated die to create a final shape—thus the name "pultrusion"—which indicates a reversal of extrusion.
One of the standout benefits of pultrusion is its high fiber-to-resin ratio, ensuring that the finished product boasts remarkable strength while maintaining its lightweight properties. Additionally, the continuous nature of the process allows for long lengths of the product, making it ideal for applications in civil engineering, such as bridge construction. Its efficiency in production further solidifies its place in high-demand manufacturing sectors where both durability and cost-effectiveness matter.
In summary, the production methods of fiber reinforced plastics not only define the end product but also drive innovation in design and application across multiple industries.
In summary, the production methods of fiber reinforced plastics not only define the end product but also drive innovation in design and application across multiple industries.
By understanding these processes and their respective benefits, professionals can better harness the power of FRPs in their work, ultimately leading to advancements in technology and engineering.
Mechanical Properties of FRPs
Understanding the mechanical properties of fiber reinforced plastics (FRPs) is crucial for several reasons. These properties dictate how these materials behave under various loads and conditions. When designed properly, FRPs exhibit a balance of strength, stiffness, and resilience, making them suitable for an array of applications. Their mechanical characteristics directly impact performance, safety, and durability in real-world scenarios. In this section, we'll focus on three major attributes that highlight the essence of FRPs: tensile strength and stiffness, impact resistance, and thermal properties. Each attribute plays a pivotal role in determining the suitability of FRPs in engineering applications.
Tensile Strength and Stiffness
Tensile strength refers to the maximum amount of tensile (pulling) stress that a material can withstand before failure. For FRPs, this property is amplified due to the embedded fibers, which transmit the load through the matrix. When we delve into specifics, carbon fiber reinforced plastics often stand out for their impressive strength-to-weight ratio. This means they can take on significant stress without adding unnecessary bulk to a structure.
Moreover, stiffness, or the ability of a material to resist deformation under load, is equally essential. Stiffness in FRPs is typically measured by their modulus of elasticity. The higher the modulus, the stiffer the material. In applications like aerospace and automotive, where weight savings are paramount, selecting an FRP with the right balance of tensile strength and stiffness can yield structures that are both lightweight and robust.
Key takeaway: The integration of fibers enhances not only the tensile strength but also the stiffness, creating materials that perform exceptionally under stress.
Key takeaway: The integration of fibers enhances not only the tensile strength but also the stiffness, creating materials that perform exceptionally under stress.
Impact Resistance
Impact resistance is another critical mechanical property. It gauges how well a material can withstand forces that act suddenly, like a drop or collision. In real-world applications, FRPs are subjected to harsh conditions, and their response to such impact loads is vital for safety and structural integrity. Various factors play into impact resistance, including the type of fibers used. For instance, aramid fibers, known for their toughness, can significantly improve the impact resistance of FRPs, making them suitable for protective gear and military applications.
Additionally, the resin matrix also contributes to this property; a toughened resin can absorb energy, preventing catastrophic failure. In fields like automotive engineering, where crash resistance is necessary, understanding and optimizing impact resistance in FRPs is indispensable.
Thermal Properties
Thermal properties represent how materials respond to heat. Knowing how FRPs react when exposed to varying temperatures is essential. For instance, many FRPs exhibit excellent dimensional stability under heat, which is crucial in applications like engine components or high-temperature envelopes in aerospace settings.
Another aspect of thermal properties includes thermal conductivity. Most fiber reinforced plastics have low thermal conductivity, making them good insulators. This characteristic not only protects components from excessive heat but also plays a role in energy efficiency in built structures. As industries push for more sustainable practices, understanding thermal properties can also assist in designing materials that maintain performance while minimizing energy loss.
Applications in Various Industries
The role of fiber reinforced plastics (FRPs) is indispensable across a wide array of industries. Their unique properties position them as materials of choice for applications that demand high strength while remaining lightweight. This section dwells into the significant applications of FRPs, elaborating on the benefits and considerations within different sectors, highlighting how these materials continue to innovate and enhance performance.
Aerospace Applications
In the aerospace sector, FRPs are becoming the beating heart for modern aircraft design. The combination of high tensile strength and low weight means that these materials can help manufacturers produce more fuel-efficient and less polluting aircraft.
- Structural Components: Components like wings, fuselage, and even interiors are often made from FRPs, leading to stronger but lighter structures.
- Fuel Efficiency: Using these materials can lower the overall weight of the aircraft, which translates to significantly improved fuel efficiency.
- Corrosion Resistance: Unlike metals, fiber reinforced plastics do not corrode easily, making them ideal for the various environments encountered in flight.
A study done by the National Aeronautics and Space Administration emphasizes that the use of composite materials like FRPs can result in aircraft that use up to 15% less fuel compared to their metal counterparts. This is a critical driver for aerospace companies looking to meet sustainability standards.
Automotive Industry Impact
When it comes to the automotive industry, FRPs have revolutionized vehicle engineering. Cars are not only getting sleeker but also safer due to these advanced materials. The shift from traditional materials to fiber reinforced plastics holds significant implications.
- Weight Reduction: Cars made with FRPs can achieve substantial weight reduction, resulting in better fuel efficiency and lower emissions.
- Crash Safety: FRPs can absorb energy on impact, helping to enhance passenger safety without adding extra weight.
- Versatile Design: The ability to mold FRPs into complex shapes allows for increased flexibility in design, paving the way for more aerodynamic forms and stylish exteriors.
A prime example is the use of glass fiber-reinforced plastic in sports cars, which combine speed with safety at aerodynamic levels. Therefore, capitalizing on FRPs not only boosts performance but also contributes to competitive advantage.
Civil Engineering Uses
In civil engineering, the adoption of FRPs is on the rise. They offer a robust solution to many challenges related to the construction and maintenance of infrastructures such as bridges, buildings, and tunnels.
- Reinforcement of Structures: FRPs are commonly used as an internal reinforcement in concrete, elevating the overall durability of structures.
- Seismic Resistance: In earthquake-prone regions, fiber reinforced polymer can be a game changer. Its lightweight nature and high strength provide enhanced performance during seismic events.
- Longer Lifespan: Utilizing FRPs helps control issues related to corrosion, leading to extended lifespan of the infrastructures while minimizing maintenance costs.
These properties lead to decreased overall lifecycle costs, an increasingly critical consideration for today’s civil engineers.
Marine Industry Utilization
The marine industry also sees a considerable benefit from FRPs, particularly in boat and ship manufacturing. This sector demands materials that are resistant to water, salt, and other harsh environmental factors.
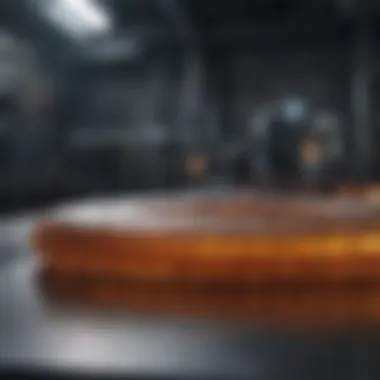
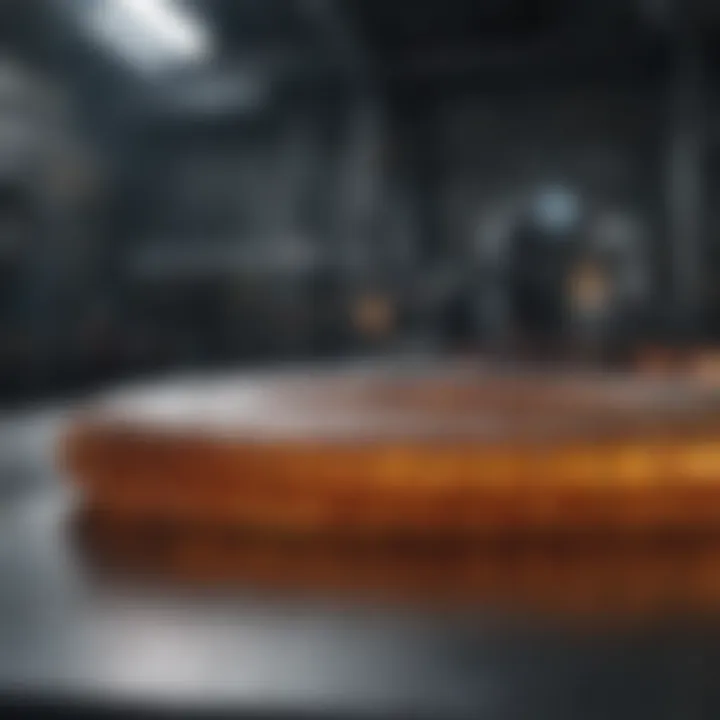
- Hull Construction: Many manufacturers are now employing FRPs in hull construction due to their exceptional strength-to-weight ratio and corrosion resistance.
- Reduced Maintenance: The longevity of these materials reduces the need for frequent repairs and maintenance, saving both time and money.
- Design Flexibility: Just like in automotive applications, the adaptability of FRPs enables naval architects to push the boundaries of design.
With advancements in composite technology, even larger vessels are beginning to use FRPs, creating possibilities that were previously unattainable.
"The versatility and advantageous properties of fiber reinforced plastics unlock new horizons across industries, revealing not only how engineers tackle existing challenges but also how they pave the way for innovative solutions."
"The versatility and advantageous properties of fiber reinforced plastics unlock new horizons across industries, revealing not only how engineers tackle existing challenges but also how they pave the way for innovative solutions."
In summary, as various industries embrace fiber reinforced plastics, they unlock a multitude of benefits that include enhanced durability, weight savings, and broader design options. It is evident that FRPs are more than just materials; they are catalysts for change, driving efficiency and performance to new heights.
Advantages of Fiber Reinforced Plastics
Fiber reinforced plastics (FRPs) bring to the table a set of distinctive advantages that boost their applicability across various domains. In a world where efficiency, strength, and lightweight materials are paramount, the advantages of FRPs give them a cutting edge in modern engineering. This section dissects three key advantages: their lightweight nature, corrosion resistance, and design flexibility, showcasing why these materials are now essential in multiple industries.
Lightweight Nature
One of the hallmarks of fiber reinforced plastics is their lightweight nature. To put it simply, FRPs weigh significantly less than traditional materials like metals or ceramics, a quality that simplifies both transport and installation processes. This property allows manufacturers to design products that do not compromise strength for weight, promoting efficiency.
For example, in the automotive industry, using lighter materials means better fuel economy. When you cut down on weight, you ease the burden on the engine, allowing vehicles to go farther with less gas. As a result, several manufacturers have incorporated FRPs into car structures, from body panels to internal components. The reduction in weight can be as much as 30% compared to similar metal structures.
- Economic Benefits: Less weight in vehicles also translates to lower shipping costs, making FRPs not just a technical advantage but an economic one, too.
- Environmental Impact: Furthermore, lighter vehicles tend to produce fewer emissions, aligning well with sustainability goals.
This relative lightness offers tremendous latitude for engineers and designers. Because it is easier to handle, FRPs can be crafted into increasingly complex shapes without the fear of excessive weight, thus enhancing creative possibilities.
Corrosion Resistance
In addition to being lightweight, fiber reinforced plastics boast high corrosion resistance. Unlike metals, which may succumb to rust or erosive processes over time, FRPs maintain their integrity even in the harshest conditions. This property is particularly valued in industries that operate in environments where exposure to moisture, chemicals, or other damaging elements is a constant.
Take the marine industry as an example. Boats and other sea vessels made from fiber reinforced plastics can withstand salty water better than their metal counterparts. They resist the corrosion that typically plagues metal parts, allowing for prolonged service life and reduced maintenance costs.
Moreover, construction applications benefit from this property as well. For bridges subjected to constant exposure to various elements or roads made from FRPs, their longevity is significantly enhanced, decreasing long-term repair and replacement expenditures.
"Corrosion resistance is key in extending the lifespan of structures and vehicles, leading to considerable savings over time."
"Corrosion resistance is key in extending the lifespan of structures and vehicles, leading to considerable savings over time."
Design Flexibility
Design flexibility is the third ace up the sleeve of fiber reinforced plastics. Because of their composite nature, FRPs can be molded into almost any shape. This characteristic opens a world of possibilities for engineers and designers looking to create innovative solutions.
In particular, complex geometries that would be difficult to achieve with metals can easily be realized with FRPs. Whether it’s intricate designs for aerospace components or customized parts for medical devices, the ability to manipulate these materials is a game-changer.
Additionally, the aesthetic versatility of fiber reinforced plastics allows for more freedom in design aspects. Manufacturers are not strictly bound to utilitarian forms—they can craft visually appealing products, combining functionality with style. This adaptability aligns well with evolving consumer demands, which often require that products are not only efficient but also pleasing to the eye.
In summary, the advantages of fiber reinforced plastics—lightweight nature, corrosion resistance, and design flexibility—are seminal in facilitating modern engineering challenges. They stand as a testament to how engineering can innovate for functional efficiency and sustainable practices.
Challenges and Limitations
When discussing fiber reinforced plastics (FRPs), it's crucial to not only look at their numerous advantages but also to address the challenges and limitations that come hand-in-hand with these materials. Being aware of these factors helps in making informed decisions and can influence future developments in both research and industrial applications.
Cost Implications
One significant hurdle facing the widespread adoption of fiber reinforced plastics is the cost. Generally, these materials can be quite pricey relative to traditional plastic options, primarily due to the specialized fibers and resins required in their composition.
- Material Costs: Fibers such as carbon and aramid can be more expensive than common reinforcements like glass fiber. A lot of the price difference stems from the advanced manufacturing processes involved, which often require high-tech factories and equipment.
- Processing Expenses: Beyond raw materials, the processes needed to shape and cure FRPs are also costly. For instance, techniques like autoclave curing used in aerospace applications demand significant investment in technology and energy.
- Economic Viability: For smaller companies or start-ups, these high costs can be a stumbling block, making it difficult to compete against more established players who might have economies of scale on their side. This economic barrier can slow down innovation and limit market entry for novel applications of FRPs.
Investment in research to develop cost-effective alternatives is ongoing, but as it stands, the expense can limit the practicality of using FRPs in projects where budget constraints are a factor.
Durability Concerns
Another point of contention regarding fiber reinforced plastics lies in their durability and lifespan. While FRPs are generally praised for their robustness, they also come with certain limitations that can’t be ignored.
- Environmental Degradation: Exposure to UV light and harsh weather can degrade the matrix material in many FRP composites over time. This can lead to performance issues, especially in applications such as outdoor construction or marine environments.
- Impact Vulnerability: certain types of fiber reinforced plastics may exhibit less resistance to impact forces compared to metals. If FRPs are used in applications requiring high impact resistance, such as automotive or aerospace, the selection of fiber type and matrix become paramount to overall durability.
- Fatigue: Repeated loading and unloading cycles can cause micro-cracks, which could lead to catastrophic failures if not monitored properly. Unlike metals, which might visibly deform before cracking, FRPs tend to fail suddenly without much warning.
Addressing these durability concerns is essential in enhancing the reliability of FRPs, especially as technology progresses and these materials find new uses.
Recycling Difficulties
Finally, the issue of recycling is a dominant challenge when it comes to fiber reinforced plastics. While they're heralded for their performance advantages, the end-of-life implications of FRPs raise red flags.
- Material Complexity: The composite nature of FRPs makes them more challenging to recycle than single-material plastics. The process of separating the fibers from the resin requires specialized techniques and does not always yield high-quality recycled materials.
- Environmental Footprint: Disposing of FRPs in landfills is common, yet this practice poses environmental concerns given that many FRPs do not decompose easily. This builds up plastic waste and contributes to broader ecological issues.
- Innovation Lag: Efforts to improve recycling processes for FRPs are underway, but the technology and infrastructure needed for effective recycling of these materials is still lagging. This could hold back their adoption in sustainability-driven sectors where recycling is increasingly prioritized.
Environmental Impact of Fiber Reinforced Plastics
Understanding the environmental ramifications of fiber reinforced plastics (FRPs) is indispensable in today’s context of heightened ecological awareness. As these materials have garnered popularity across various industries due to their beneficial properties, it's equally crucial to address their ramifications on the environment. A comprehensive overview of their impact encompasses sustainability issues and end-of-life management, which are pivotal in shaping their future adoption in the market.
Sustainability Issues
One of the primary concerns surrounding fiber reinforced plastics revolves around sustainability. While FRPs offer remarkable durability and improved performance in comparison to traditional materials, their production often involves energy-intensive processes and contributes to environmental degradation. Factors like raw material extraction, manufacturing emissions, and waste generation can add to their ecological footprint.
- Resource Usage: The extraction of raw materials, such as fibers and plastics, inherently contributes to environmental destruction, particularly when these materials are sourced from non-renewable resources.
- Energy Consumption: Manufacturing processes, including the polymerization of plastics and the integration of fibers, require substantial energy, often derived from fossil fuels. This exacerbates carbon emissions and elevates global warming concerns.
- Pollution: Waste products and pollutants released during the production phase can contaminate local ecosystems, affecting biodiversity and human health.
To mitigate these sustainability issues, researchers are exploring bio-based alternatives, such as natural fibers and biodegradable resins. Utilizing sustainable practices and promoting circular economy ideals can help reduce the overall environmental costs associated with FRPs.
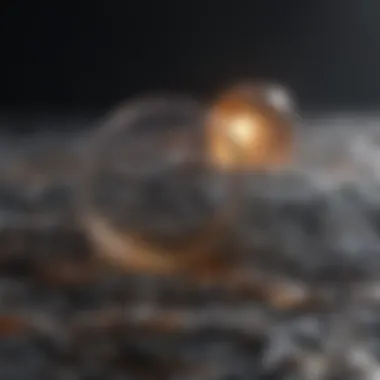
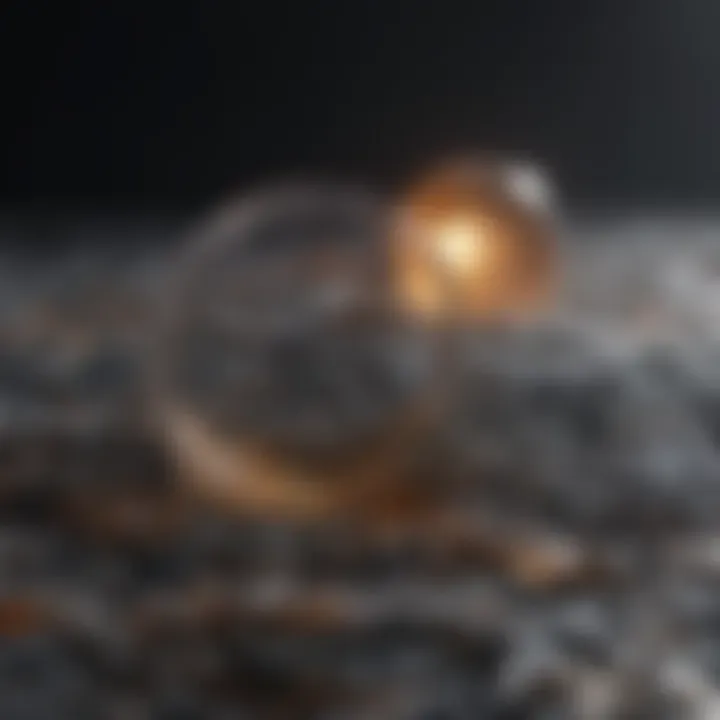
End-of-Life Management
Another crucial aspect of the environmental impact of fiber reinforced plastics is their end-of-life management. Unlike metals and certain other materials that can be easily recycled, the high-performance nature of FRPs presents unique challenges for disposal and recycling.
- Recycling Difficulties: Many existing recycling technologies are not designed specifically for FRPs, limiting their recyclability. Traditional separation techniques struggle to differentiate between the organic and inorganic components, resulting in materials often ending up in landfills rather than being repurposed. This leads to significant waste, raising questions about resource efficiency.
- Landfill Concerns: The durability that makes FRPs appealing also means they can persist in the environment for extensive periods once discarded. This longevity can contribute to landfill overflow and ultimately affects natural habitats.
- Innovative Solutions: Innovative technological advancements, such as chemical recycling, are being explored to address these end-of-life issues. Research into methods that can break down FRPs into reusable feedstock shows promise in enhancing the lifecycle management of these materials.
"Developing systems for the effective recycling and upcycling of FRPs is essential to minimizing their ecological footprint and promoting sustainable practices."
"Developing systems for the effective recycling and upcycling of FRPs is essential to minimizing their ecological footprint and promoting sustainable practices."
Future Prospects of FRPs
The future of fiber reinforced plastics (FRPs) is shaping up to be as dynamic as the material itself. As industries strive for improved performance and sustainability, FRPs stand at the forefront of this transformation. The unique properties of FRPs lend themselves to numerous innovative applications, pushing the boundaries of what’s currently possible in engineering and design. With increased focus on materials that offer both strength and reduced weight, the development of FRPs has become crucial in meeting the evolving demands of modern technology.
Innovations in Materials
The innovation landscape in fiber reinforced plastics is quite expansive. Researchers are diving into enhanced matrix materials, such as epoxy resin formulations that offer greater durability and resistance to wear. New reinforcement methods are surfacing too. For example, researchers have begun exploring bio-based fibers from agricultural waste, tapping into sustainable resources. These materials not only meet mechanical expectations but also help reduce reliance on fossil-fuel-based products.
Through the introduction of nanomaterials, like graphene, in combination with traditional fibers, it's possible to achieve improved electrical conductivity and thermal properties. These advancements mean FRPs can cater to high-tech sectors like electronics and aerospace even more effectively than before. As manufacturers experiment with hybrid composites—which combine various types of fibers for improved performance—opportunities for customization and optimization of material properties abound.
"The leap towards hybrid materials marks a significant turning point in the functionality and adaptability of FRPs in specialized applications."
"The leap towards hybrid materials marks a significant turning point in the functionality and adaptability of FRPs in specialized applications."
Expanding Applications
As the material science realm continues to explore the capabilities of fiber reinforced plastics, the array of applications is set to diversify. Industries such as aerospace, automotive, and construction have already carved out significant niches for FRPs. However, new horizons are emerging. In the medical field, for instance, FRPs are being utilized for prosthetics and implants, offering a lightweight alternative that doesn't compromise strength.
Moreover, the renewable energy sector is also seeing a boost from FRP technologies. Wind turbine blades, designed with advanced composites, not only withstand harsh environmental conditions but also maximize energy efficiency.
- Automotive Engineering: With the push for electric vehicles, car manufacturers are increasingly adopting FRPs to reduce vehicle weight, thereby improving battery efficiency and mileage.
- Infrastructure: Bridges and other structures made from FRPs promise enhanced longevity due to their corrosion resistance and lightweight nature. This could mean fewer resources spent on maintenance over time.
- Sports Equipment: Companies are opting for FRP gear in sports, offering high-performance, lightweight options for athletes.
In looking toward the future, one should expect the concept of 'smart materials' to play a role in fiber reinforced plastics. By integrating sensors within the FRPs, applications can be monitored in real-time, providing data that can inform design and functionality improvements.
The possibilities for fiber reinforced plastics seem boundless. As their applications spread across various sectors, driven by advancements in materials and environmental considerations, it’s clear that FRPs will remain pivotal in the engineering solutions of tomorrow.
Research Trends in Fiber Reinforced Plastics
The field of fiber reinforced plastics (FRPs) is constantly evolving, driven by a host of factors like technological advancements, environmental concerns, and the demand for enhanced performance in various applications. These trends are not just changing the way we understand and use FRPs, but also underline their importance in modern engineering practices. As industries continue to seek materials that blend strength with lightweight features, the spotlight is firmly on FRP research to answer these growing needs.
A significant element of current research focuses on improving the properties of FRPs through the exploration of new composite materials. Researchers are investigating how alternative fibers—such as natural fibers or hybrid combinations—can create stronger, more durable materials, while also offering better sustainability metrics compared to traditional options. This approach not only reduces the environmental footprint but also opens up exciting avenues for industries eager to adopt green technologies.
Moreover, studies are digging into advanced manufacturing techniques that could optimize the production process for FRPs. For instance, 3D printing is being examined as a viable method for fabricating FRP components, offering improved design flexibility and reduction in waste. This is a game changer for industries looking to enhance efficiency and innovate their product lines. The implications of such developments are profound, as they could lead to entirely new applications for FRPs, challenging conventional manufacturing paradigms.
In addition to material advancements and production innovations, the area of biocompatibility and health applications of FRPs is gaining traction. Increasingly, researchers are exploring the potential use of these materials in medical devices, prosthetics, and implant technologies. This not only marks a technological shift but also demonstrates the versatility of FRPs across diverse sectors. The ability to customize materials for specific health applications might usher in a new era of personalized medicine and improve patient outcomes.
"Research into fiber reinforced plastics is not only about enhancing materials for traditional boundaries; it's about rethinking how these materials can transform industries from the ground up."
"Research into fiber reinforced plastics is not only about enhancing materials for traditional boundaries; it's about rethinking how these materials can transform industries from the ground up."
Emerging Studies
Recent studies on FRPs are focusing on various facets of material properties and usability, trying to push the envelope further. One promising area of investigation is the integration of smart materials into FRPs. Researchers are exploring the combination of sensors and actuators within fiber reinforced matrices, thereby making it possible for these composites to respond to external stimuli. This could lead to self-healing capabilities or adaptive structures that change shape according to environmental conditions—offering tremendous potential especially in aerospace and civil engineering.
Moreover, there is a concerted effort to investigate weather and temperature resistance in FRPs. Understanding how these materials behave under extreme conditions is crucial for applications where safety and reliability cannot be compromised. By analyzing these factors, researchers hope to establish a new benchmark for durability standards in the industry.
Collaboration Between Disciplines
The future of FRPs does not rest solely within materials science; it thrives on the collaboration between diverse fields. Chemists, engineers, biologists, and environmental scientists are increasingly working together in pursuits that can integrate knowledge from various realms. For instance, the role of nanotechnology in enhancing FRP composites is an emerging theme. Collaborative efforts are yielding results that harness nanoscale materials to improve the mechanical strength or other performance metrics of FRPs while maintaining or even reducing their weight.
Additionally, partnerships between private companies and academic institutions are becoming commonplace. These alliances foster innovation and promote the transfer of knowledge between theory and application. For example, educational institutions often have the latest research capabilities, which can provide companies with a competitive edge in product development.
Key Takeaways
Understanding fiber reinforced plastics (FRPs) sheds light on their vital role in modern engineering. These materials not only combine the best attributes of plastics and fibers but also address real-world needs across diverse industries. Here are some key takeaways:
- Strength-to-Weight Ratio: FRPs are known for their excellent strength-to-weight ratio. This feature makes them invaluable in sectors like aerospace and automotive, where minimizing weight without sacrificing performance is crucial.
- Versatility in Applications: The potential applications of FRPs are virtually limitless, spanning from automotive parts to complex structural components in buildings. Their adaptability makes them suitable for both consumer products and industrial-grade materials.
- Sustainability Considerations: With growing concerns about environmental impact, FRPs present challenges as well as opportunities. The push for recyclable materials in engineering has sparked innovations in FRP technology, leading to more sustainable practices.
- Innovation in Manufacturing: Continuous advancements in manufacturing methods contribute to the evolution and performance enhancement of FRPs. This ongoing technical evolution keeps engineers engaged and often leads to new applications that weren't previously possible.
"The breakthrough in FRP technology has changed the horizon of material science, paving the way for innovations that meet both performance and environmental demands."
"The breakthrough in FRP technology has changed the horizon of material science, paving the way for innovations that meet both performance and environmental demands."
- Collaboration Across Disciplines: The study and application of FRPs involve multiple fields—material science, engineering, and sustainable design, to mention a few. Such interdisciplinary collaboration fosters innovation and adaption to new engineering challenges.
Importance in Modern Engineering
Fiber reinforced plastics are not just materials; they are pivotal in determining how products are designed, manufactured, and utilized. Their lightweight nature brings significant advantages when building vehicles and aircraft, leading to improved fuel efficiency. Moreover, with their resistance to corrosion, FRPs significantly decrease maintenance needs and prolong service life for structures and components in harsh environments. This resilience not only translates to economic savings over time but also supports longevity in sustainable practices.
Additionally, the flexibility in design and processing allows engineers to create shapes and structures that were once considered too complex for conventional materials. Tailored mechanical properties can be achieved by adjusting the type and amount of reinforcement, further enriching the material's utility.
In essence, the role of FRPs in modern engineering cannot be overstated; they are tools for innovation and drivers of efficiency across various industries.
Adapting to New Challenges
As industries evolve, so too do the challenges that engineers and material scientists face. With the urge for higher performance in more demanding environments, fiber reinforced plastics must adapt and overcome obstacles. One significant challenge is the growing emphasis on sustainability. The transition toward greener alternatives has highlighted the need for FRPs to not only be efficient in use but also in their lifecycle management.
Moreover, the recycling of FRPs presents a conundrum. As the materials often consist of composite structures, recycling them effectively without compromising material integrity is a topic of ongoing research. Addressing this issue not only involves technological advancements but also requires collaboration with regulatory bodies and industry leaders to establish viable recycling methods.
The integration of advanced materials, such as bio-based fibers or recyclable resins, reflects an attempt to keep pace with environmental demands. Engineers are increasingly challenged to innovate and modify processes to meet stricter environmental regulations while maintaining the properties that make FRPs desirable.
In summary, adapting to new challenges is crucial for the future of fiber reinforced plastics. It reflects a commitment to progressive material development that meets both performance and ecological standards.